Organisation et compétences dans l’usine du futur
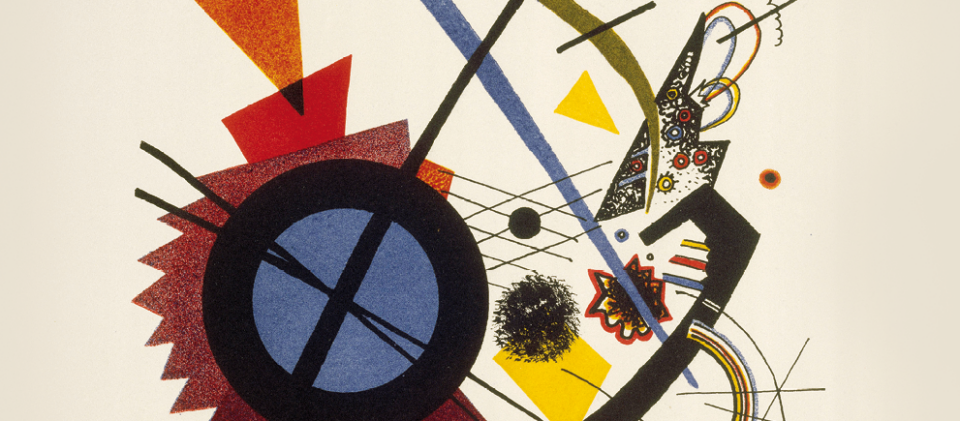
Violett, 1923 Kandinsky Vassily (1866-1944) Paris, Centre Pompidou – Musée national d’art moderne – Centre de création industrielle Photo © Centre Pompidou, MNAM-CCI, Dist. RMN-Grand Palais / image Centre Pompidou, MNAM-CCI
Préface de Bruno Grandjean, président de l’Alliance Industrie du Futur
Les entreprises industrielles, soumises à une pression concurrentielle permanente, vivent et survivent en réalisant chaque année des gains de productivité : soit en répondant à des demandes nouvelles, soit en réduisant leurs coûts directs et leurs besoins en consommations intermédiaires, soit les deux à la fois. C’est dans ce but qu’elles redoublent d’efforts pour imaginer des produits et des services innovants ou de nouvelles manières de les réaliser, qu’elles renouvellent les compétences de leurs équipes, qu’elles cherchent à réduire leurs coûts… En somme, l’industrie ne cesse jamais d’être tendue vers une vision de l’avenir, qu’elle préfigure et participe à faire advenir.
Depuis 2011, en Allemagne puis dans tous les pays du monde, des groupes d’experts tentent d’imaginer ce que sera le futur de l’industrie. À quoi ressemblera la production du fait de l’irruption des technologies de l’information, non plus seulement dans les bureaux d’étude mais à présent aussi dans les ateliers ? À quoi ressemblera le travail aussi ? Pourra-t-on s’appuyer sur des machines autonomes et communicantes ? Quels savoir-faire faudra-t-il maîtriser ? Comment les équipes seront-elles organisées et les responsabilités réparties ?
Nous n’avons pas réponse à toutes ces questions. Mais nous savons que nous ne pouvons pas attendre d’y avoir totalement répondu avant d’enclencher un mouvement ambitieux de modernisation de notre parc productif ; nous le pouvons d’autant moins que tous les industriels de la planète sont de cet avis. C’est cette grande mobilisation, ce grand dessein, que nous appelons en France « industrie du futur » et que d’autres nomment Industrie 4.0 ou Advanced Manufacturing.
Cette mise en mouvement se nourrit de deux courants : technique et humain. D’une part en
effet, les entreprises doivent s’approprier les nouvelles technologies numériques, sources de nombreuses opportunités (intelligence artificielle, modélisation numérique des produits et process, interfaces avec les clients et fournisseurs, machines connectées et autonomes, robotique…). D’autre part et dans le même temps, elles doivent donner à leurs équipes la possibilité de maîtriser ces techniques et d’en tirer le meilleur parti, et faire monter en compétence leurs salariés.
La rencontre de ces deux transformations fait couler beaucoup d’encre, parce qu’elle suscite autant d’espérances que d’appréhensions. Le robot va-t-il détruire nos emplois ou rendre le travail à l’usine ergonomique pour toutes et tous ? L’intelligence artificielle offre-t-elle des gisements de productivité insoupçonnés ou va-t-elle faire de chaque opérateur un pur exécutant de consignes logicielles ? Peut-on espérer une montée en compétence de tous les travailleurs de l’industrie ou le numérique va-t-il accentuer jusqu’au déchirement la polarisation des actifs et des emplois ?
Aucune de ces réponses n’est valable dans l’absolu. Tout dépend, à chaque fois et sur chaque site, des conditions techniques et humaines dans lesquelles les innovations sont déployées et au service de quelle stratégie d’entreprise elles sont convoquées. Mais c’est bien là qu’il faut regarder, à n’en pas douter : à l’interface entre le bouillonnement de la novation technique et la vitalité des équipes en mouvement.
C’est tout le mérite de cet ouvrage, dont l’analyse est méticuleusement adossée à une quinzaine d’études de cas (dont quatre entreprises labellisées « vitrine Industrie du futur » par l’AIF). Il montre, avec son modèle CALT (confiance, autonomie, lean, technologie), combien
la technique, l’organisation de la production et la culture d’entreprise avancent de concert. Forts de ces observations, les auteurs avancent la proposition d’un « design du travail », c’est-à-dire d’une conception des activités de production qui prendrait en compte les attentes et les besoins de l’opérateur en activité et dont celui-ci serait acteur. Je m’associe pleinement à cette proposition et souhaite qu’elle obtienne rapidement une audience étendue, car elle esquisse de toute évidence le principal défi organisationnel que nos entreprises ont devant elles et représente une réponse au problème d’attractivité des métiers de l’industrie.
L’Alliance Industrie du futur (AIF) a placé au cœur de sa stratégie la prise en compte du salarié avec son savoir-faire, ses compétences et son savoir-être, comme élément majeur de la réussite de la transformation de l’industrie française. Cette thématique constitue l’un des six leviers de compétitivité figurant dans son référentiel de l’industrie du futur. Ses travaux, Agora Industrie, Osons l’Industrie…, menés avec ses membres, en témoignent. C’est pourquoi je suis particulièrement heureux de m’associer à la publication de cet ouvrage de la Fabrique de l’industrie.
Synthèse
L’objectif de cette Note est d’identifier des pratiques émergentes d’organisation du travail et de gestion des compétences dans les usines qui modernisent avec succès leur outil de production, à partir d’une vingtaine de témoignages d’experts et de dirigeants d’entreprises manufacturières de taille variée. Ces entreprises sont plutôt à l’avant-garde et ne sont donc pas représentatives de l’ensemble des usines françaises, mais ces pionnières peuvent inspirer les autres. Leur transformation est globale et culturelle, avant même d’être technologique.
Besoins des entreprises et transformation
La transformation vise à augmenter la compétitivité et l’agilité de l’entreprise.
Cette transformation passe non seulement par l’introduction de technologies, mais surtout par une évolution vers un modèle d’organisation plus apprenante, permettant de réduire les temps de contrôle et de décision de la chaîne managériale (autonomie), d’encourager les salariés à s’exprimer sur leur tâche et leur poste (amélioration continue), et de libérer les énergies et la créativité (innovation).
L’organisation apprenante reste cependant – même dans ces entreprises pionnières – plutôt un objectif à atteindre qu’une réalité avérée. On constate une recherche encore tâtonnante d’équilibre entre la rationalisation des procédures là où il y en avait peu et l’augmentation des marges de manœuvre des salariés. Il n’y a pas un modèle unique abouti, mais des circulations, des hybridations entre différents modèles d’organisation, qui tentent de résoudre diverses tensions, par exemple entre l’enrichissement des tâches sur chaque poste et la polyvalence des opérateurs susceptibles d’occuper plusieurs postes, ou entre la diminution de la pénibilité physique et l’alourdissement de la charge cognitive et psychologique. Dix de ces tensions sont commentées en annexe du document.
Gestion des compétences
Pour faire face aux difficultés de recrutement dans les métiers de production, les entreprises sont amenées à embaucher et gérer les carrières en s’appuyant davantage sur le potentiel des personnes (capacités, savoir-être, appétences) que sur les compétences visibles sur leur CV, et en accompagnant les talents dans la durée (soutien aux projets personnels, intrapreneuriat).
Les entreprises de l’échantillon investissent de façon importante dans la formation pour adapter les compétences de leurs salariés.
Les compétences métiers ne représentent qu’une partie de cet effort de formation ; le reste est consacré au développement des savoir-être, des capacités relationnelles et d’une culture numérique. À côté de la formation traditionnelle, les entreprises encouragent les apprentissages informels qui visent à stimuler la curiosité, l’initiative et les collaborations transversales entre salariés, afin de renforcer l’agilité de l’organisation.
Trois composantes structurant l’organisation du travail
Quasiment toutes les entreprises de l’échantillon combinent, à des niveaux de maturité variables, lean (rationalisation des processus), autonomie des salariés et introduction de nouvelles technologies.
Le lean est un outil structurant mais insuffisant lorsque les opérateurs ne sont pas au cœur de la démarche. Les gains de productivité sont alors souvent de courte durée et les contraintes induites, mal vécues.
Le développement de leur autonomie permet aux salariés de se réapproprier l’organisation de leur travail, de réfléchir sur son sens et son intérêt et sur ce qui les empêche parfois de faire du bon travail.
Cette autonomisation des salariés conduit souvent à un aplatissement de la ligne hiérarchique et à un déplacement progressif des frontières entre exécution et décision. Cet accroissement du pouvoir d’agir et de la responsabilité se révèle toutefois un chemin escarpé pour certains salariés et pour certains managers.
Quand les technologies sont introduites dans l’usine, elles peuvent permettre au lean de déployer tout son potentiel, par la synchronisation des flux physiques et des flux d’informations (lean connecté). Mais leur impact sur la qualité du travail est ambivalent : enrichissement des tâches ou réduction des marges de manœuvre d’un opérateur guidé et « piloté » par les technologies ?
Vers un design du travail ?
Là où l’autonomie précède le lean et où les opérateurs sont associés à l’introduction des technologies, l’appropriation de celles-ci est plus aisée et efficace. L’acronyme CALT (confiance, autonomie, lean, technologie) dessine un chemin de progrès permettant de combiner valorisation du travail humain, modernisation de l’outil de production et performance pour l’entreprise. La confiance, condition du bon déroulement de la démarche, se renforce au cours de son déploiement.
Cette approche illustre ce que pourrait être, d’une manière plus générale, le design du travail, une approche qui consiste à appliquer la pensée design non plus seulement à la construction du produit ou du service avec le client final mais aussi à celle du processus de définition du travail avec le salarié. Certaines entreprises ont commencé à explorer cette voie. Cet effort est nécessaire pour redonner de l’attractivité aux métiers de la production, et in fine à l’industrie.
INTRODUCTION
À quoi ressemblera l’usine du futur ? En première instance, cette question semble faire appel à un imaginaire techno-futuriste, idéalisé ou critiqué selon les points de vue. Cécile Roche, Lean and Agile
qui laisse penser que nous avons du temps pour nous adapter et éloigne le caractère d’urgence des transformations ». Disons-le tout net, l’usine du futur dont il sera ici question n’est pas celle que vous imaginez.
Usine du futur, futur de l’usine
Les pouvoirs publics et les fédérations industrielles mobilisent aujourd’hui les entreprises autour d’une vision de l’industrie qui se modernise par l’incorporation de technologies numériques sophistiquées. Pourtant, l’usine du futur ne se résume pas à l’introduction de technologies « 4.0 ». L’usine dont nous allons parler est celle qui se transforme ici et maintenant, sur nos territoires et avec les communautés humaines qui la composent, pour assurer son existence et sa prospérité dans le futur. Contrairement à l’industrie, concept abstrait et ensemble d’activités débordant largement la seule production d’objets, l’usine est un lieu fait de métal, de machines, de chair, de vie et de neurones. L’usine est un lieu tangible, le lieu d’une transformation permanente où se combinent le travail humain et l’innovation technologique et organisationnelle. Aujourd’hui, il est question de robots, d’objets connectés, de jumeaux virtuels, d’analyse de données massives, d’intelligence artificielle et de nouveaux procédés de fabrication. Mais aujourd’hui comme hier, il faut aussi organiser le travail et les flux, capitaliser les connaissances, développer les compétences de chacun, promouvoir des relations de travail permettant de construire des capacités collectives et l’engagement de tous, bref… il faut s’intéresser à l’humain.
Est-ce à dire que rien n’a changé ? Tout au contraire. Comme le dit Anne Leitzgen, présidente de Schmidt Groupe, « plus de digital nous conduit à développer toujours plus d’humain ». Ce qui pourrait ressembler à un slogan marketing semble confirmé par l’analyse de chercheurs. Pierre Veltz1 souligne ainsi : « Soient deux usines de yoghourts, absolument identiques, mêmes qualifications, niveaux de salaires très proches. Surprise : le coût de la tonne produite varie de 50 % entre les deux sites. Pourquoi ? […] Celle-ci dépend directement de la densité et de la qualité des communications au sein des collectifs humains gravitant autour de la machinerie, de leur capacité à apprendre collectivement, à interpréter et à gérer les flux d’événements qui constituent désormais le véritable substrat du travail.» C’est donc le levier managérial et humain qui ferait la différence entre les entreprises, de façon au moins aussi importante que la technologie.
Mutation technologique, mutation organisationnelle
Pourtant, beaucoup de dirigeants semblent encore focaliser leur réflexion sur les mutations technologiques, la rentabilité et le financement des investissements. Dans un récent livre blanc2, EY distingue la maturité opérationnelle des entreprises, i.e. la transformation de l’outil de production ; la maturité organisationnelle, i.e. l’adaptation de l’organisation ; et la maturité de la relation client. Le cabinet constate que seulement 15 % des grandes entreprises industrielles ont une transformation de leur organisation à la hauteur de la maturité de leur transformation opérationnelle et de leur prise en compte du client. L’étude indique que la transformation organisationnelle n’est souvent abordée que lorsqu’un plafond de performance est atteint, mais qu’a posteriori certains dirigeants regrettent de ne pas avoir suffisamment anticipé les transformations du processus de production, l’impact sur les personnels, les besoins de formation aux nouvelles compétences requises. Le niveau de performance de la mutation opérationnelle dépend crucialement de la bonne prise en compte des questions d’organisation et de compétences.
L’objectif de cet ouvrage est d’examiner si et comment certaines organisations industrielles, en prise avec des transformations de leur outil de production, développent des pratiques plus efficientes que d’autres en matière de gestion et d’acceptation du changement par les équipes, et de développement des compétences visant à tirer tout le parti possible des technologies.
Un échantillon de 14 entreprises révélatrices de tendances
Nous avons souhaité présenter un panel diversifié d’entreprises (PME, ETI, grandes entreprises – voir tableau synoptique, p. 18). Certaines d’entre elles ont, à un titre ou un autre, bénéficié d’une certaine médiatisation en lien avec l’industrie du futur et sont considérées comme des « modèles » en pointe, labellisés ou en voie de labellisation comme « vitrines de l’industrie du futur » par l’AIF (Alliance Industrie du Futur). Elles ne sont donc pas représentatives de la population des entreprises françaises, mais elles sont en revanche révélatrices de tendances émergentes.
On notera que les grands groupes industriels sont sous-représentés par rapport à la part d’emplois qu’ils représentent. Les petites et moyennes entreprises sont plus aisées à rencontrer et observer. Les changements peuvent y être rapides du fait de décisions en boucles courtes. On peut donc les considérer comme d’excellents « laboratoires » d’observation des changements en cours, mais leurs pratiques inspirantes ne sont pas toujours transposables aux structures de très grande taille.
D’une façon générale, c’est moins l’usine du futur que nous avons rencontrée que le futur de l’usine. Certaines des entreprises auditionnées sont effectivement engagées dans l’introduction des technologies de l’industrie 4.0 dans les ateliers, mais même celles qui le sont moins sont conscientes de la nécessité d’une transformation culturelle dictée par l’exigence renforcée d’agilité et d’orientation client. Cette transformation culturelle passe par le développement des capacités d’apprentissage des personnels, leur engagement et leur réactivité. Parallèlement, nombreuses sont celles qui sont confrontées à des difficultés de recrutement au moment où leurs carnets de commande commencent à se remplir, et ce en raison du déficit d’image des emplois de production. Cette double contrainte – transformation culturelle, difficulté de recrutement – est très présente dans l’esprit des dirigeants, même lorsque la technologie n’est pas leur priorité. Le point d’entrée des transformations à l’œuvre est donc loin d’être seulement technologique, même s’il y contribue. Les chiffres le confirment : 63% des PME-ETI sont entrées dans un cycle de transformation, aussi modeste soit son degré d’avancement3.
Cette Note s’appuie sur la parole des dirigeants et rend compte de leurs discours par rapprochements et croisements pour en dégager des tendances. D’où la place importante qu’elle accorde aux verbatim4. Le discours du dirigeant présente un intérêt particulier en raison de sa fonction performative, puisqu’il est en capacité d’orienter l’organisation selon les convictions qu’il énonce. Analyser son discours, c’est aussi prendre en compte les lacunes ou les approximations de cette parole : nous nous intéressons donc aussi bien à ce qui est dit qu’à ce qui est tu. Quels sont les sujets que le dirigeant aborde préférentiellement ? Et a contrario, quels sont ceux qu’il n’aborde qu’en mode assisté ou ceux qu’il évite ? Nous nous attachons aussi à replacer autant que possible cette parole dans le contexte plus large des discours institutionnels ou médiatiques qui peuvent l’influencer. Nous mentionnons, chaque fois que cela nous a semblé nécessaire, les principaux éléments de la critique adressée au discours patronal sur ces sujets.
Continuités et variations
On entend fréquemment dire que l’organisation du travail connaîtrait des transformations profondes du fait de l’automatisation-numérisation, mais aussi en raison de paramètres sociétaux liés au niveau d’éducation et d’information des salariés, et à l’évolution de leurs aspirations. Les transformations organisationnelles et managériales que nous avons pu observer sont réelles, mais lentes et assez peu spectaculaires dans l’ensemble.
Parler de « transformation » pourrait aussi laisser entendre qu’on assiste au passage d’un modèle d’organisation général et dominant vers un nouveau modèle. Or, plusieurs types d’organisation du travail ont coexisté à toutes les époques (taylorienne, en lean production, en structure simple, apprenante, libérée, etc.) : il n’y a donc pas d’évolution d’un modèle unique vers un autre modèle unique en voie de constitution, mais des circulations, des évolutions et des hybridations entre différents modèles existants. Tout au plus peut-on constater dans une majorité des entreprises observées une recherche tâtonnante vers un modèle d’organisation combinant rationalisation du travail et participation des salariés ; un modèle plus horizontal et plus « apprenant », susceptible de répondre à la fois aux besoins de la révolution numérique, aux aspirations nouvelles des salariés et à l’exigence accrue de compétitivité et d’agilité. Les méthodes que ces entreprises mettent en œuvre visent à favoriser les capacités d’apprentissage en autonomie, les modes de travail en intelligence collective, à renforcer selon la belle expression de Martin Richer « les terminaisons nerveuses »5 de l’entreprise comme réponses à un environnement instable et fortement concurrentiel. Mais la réalité des organisations, même les plus avancées dans cette voie, véhicule nombre d’ambiguïtés sur des termes tels qu’autonomie, responsabilité, polyvalence, délégation ou subsidiarité, etc.
Bonnes pratiques
Notre objectif était de déceler des pratiques inspirantes et d’avant-garde dans les usines. Nos observations ont fait progressivement apparaître un chemin de progrès capable de favoriser à la fois une bonne appropriation des technologies, une réponse aux besoins psychologiques des salariés et une performance globale de l’entreprise satisfaisante. Nous le présentons sous le nom de « modèle CALT » pour confiance, autonomie, lean et technologie. Ce modèle ouvre la voie à une proposition plus globale et militante que nous désignons par l’expression « design du travail » et qui vise à répondre à la crise de représentation que subit le travail de production, en vue de renforcer l’attractivité du secteur industriel dans son ensemble.
***
Pour prendre la mesure des transformations de l’organisation du travail dans les usines, nous examinerons : les besoins exprimés par les entreprises pour justifier les transformations organisationnelles (chapitre 1), les tendances en matière de gestion des compétences (chapitre 2), trois déterminants structurant l’organisation du travail (lean, autonomie, technologie) et leur articulation dynamique (chapitre 3). Enfin, nous mettrons en discussion une proposition originale : imaginer ce que pourrait être demain le « design du travail » (chapitre 4). Une annexe intitulée « 10 tensions qui questionnent le travail » permet de rattacher les observations de terrain à des problématiques plus générales concernant l’évolution du travail telles qu’elles sont saisies par nombre d’études et enquêtes sur ces sujets. Nous renvoyons dans le corps du texte à ces développements. de neurones. L’usine est un lieu tangible, le lieu d’une transformation permanente où se combinent le travail humain et l’innovation technologique et organisationnelle. Aujourd’hui, il est question de robots, d’objets connectés, de jumeaux virtuels, d’analyse de données massives, d’intelligence artificielle et de nouveaux procédés de fabrication. Mais aujourd’hui comme hier, il faut aussi organiser le travail et les flux, capitaliser les connaissances, développer les compétences de chacun, promouvoir des relations de travail permettant de construire des capacités collectives et l’engagement de tous, bref… il faut s’intéresser à l’humain.
Est-ce à dire que rien n’a changé ? Tout au contraire. Comme le dit Anne Leitzgen, présidente de Schmidt Groupe, « plus de digital nous conduit à développer toujours plus d’humain ». Ce qui pourrait ressembler à un slogan marketing semble confirmé par l’analyse de chercheurs. Pierre Veltz1 souligne ainsi : « Soient deux usines de yoghourts, absolument identiques, mêmes qualifications, niveaux de salaires très proches. Surprise : le coût de la tonne produite varie de 50 % entre les deux sites. Pourquoi ? […] Celle-ci dépend directement de la densité et de la qualité des communications au sein des collectifs humains gravitant autour de la machinerie, de leur capacité à apprendre collectivement, à interpréter et à gérer les flux d’événements qui constituent désormais le véritable substrat du travail. » C’est donc le levier managérial et humain qui ferait la différence entre les entreprises, de façon au moins aussi importante que la technologie.
Mutation technologique, mutation organisationnelle
Pourtant, beaucoup de dirigeants semblent encore focaliser leur réflexion sur les mutations technologiques, la rentabilité et le financement des investissements. Dans un récent livre blanc2, EY distingue la maturité opérationnelle des entreprises, i.e. la transformation de l’outil de production ; la maturité organisationnelle, i.e. l’adaptation de l’organisation ; et la maturité de la relation client. Le cabinet constate que seulement 15 % des grandes entreprises industrielles ont une transformation de leur organisation à la hauteur de la maturité de leur transformation opérationnelle et de leur prise en compte du client. L’étude indique que la transformation organisationnelle n’est souvent abordée que lorsqu’un plafond de performance est atteint, mais qu’a posteriori certains dirigeants regrettent de ne pas avoir suffisamment anticipé les transformations du processus de production, l’impact sur les personnels, les besoins de formation aux nouvelles compétences requises. Le niveau de performance de la mutation opérationnelle dépend crucialement de la bonne prise en compte des questions d’organisation et de compétences.
L’objectif de cet ouvrage est d’examiner si et comment certaines organisations industrielles, en prise avec des transformations de leur outil de production, développent des pratiques plus efficientes que d’autres en matière de gestion et d’acceptation du changement par les équipes, et de développement des compétences visant à tirer tout le parti possible des technologies.
Un échantillon de 14 entreprises révélatrices de tendances
Nous avons souhaité présenter un panel diversifié d’entreprises (PME, ETI, grandes entreprises – voir tableau synoptique, p. 18). Certaines d’entre elles ont, à un titre ou un autre, bénéficié d’une certaine médiatisation en lien avec l’industrie du futur et sont considérées comme des « modèles » en pointe, labellisés ou en voie de labellisation comme « vitrines de l’industrie du futur » par l’AIF (Alliance Industrie du Futur). Elles ne sont donc pas représentatives de la population des entreprises françaises, mais elles sont en revanche révélatrices de tendances émergentes.
On notera que les grands groupes industriels sont sous-représentés par rapport à la part d’emplois qu’ils représentent. Les petites et moyennes entreprises sont plus aisées à rencontrer et observer. Les changements peuvent y être rapides du fait de décisions en boucles courtes. On peut donc les considérer comme d’excellents « laboratoires » d’observation des changements en cours, mais leurs pratiques inspirantes ne sont pas toujours transposables aux structures de très grande taille.
D’une façon générale, c’est moins l’usine du futur que nous avons rencontrée que le futur de l’usine. Certaines des entreprises auditionnées sont effectivement engagées dans l’introduction des technologies de l’industrie 4.0 dans les ateliers, mais même celles qui le sont moins sont conscientes de la nécessité d’une transformation culturelle dictée par l’exigence renforcée d’agilité et d’orientation client. Cette transformation culturelle passe par le développement des capacités d’apprentissage des personnels, leur engagement et leur réactivité. Parallèlement, nombreuses sont celles qui sont confrontées à des difficultés de recrutement au moment où leurs carnets de commande commencent à se remplir, et ce en raison du déficit d’image des emplois de production. Cette double contrainte – transformation culturelle, difficulté de recrutement – est très présente dans l’esprit des dirigeants, même lorsque la technologie n’est pas leur priorité. Le point d’entrée des transformations à l’œuvre est donc loin d’être seulement technologique, même s’il y contribue. Les chiffres le confirment : 63 % des PME-ETI sont entrées dans un cycle de transformation, aussi modeste soit son degré d’avancement3.
Cette Note s’appuie sur la parole des dirigeants et rend compte de leurs discours par rapprochements et croisements pour en dégager des tendances. D’où la place importante qu’elle accorde aux verbatim4. Le discours du dirigeant présente un intérêt particulier en raison de sa fonction performative, puisqu’il est en capacité d’orienter l’organisation selon les convictions qu’il énonce. Analyser son discours, c’est aussi prendre en compte les lacunes ou les approximations de cette parole : nous nous intéressons donc aussi bien à ce qui est dit qu’à ce qui est tu. Quels sont les sujets que le dirigeant aborde préférentiellement ? Et a contrario, quels sont ceux qu’il n’aborde qu’en mode assisté ou ceux qu’il évite ? Nous nous attachons aussi à replacer autant que possible cette parole dans le contexte plus large des discours institutionnels ou médiatiques qui peuvent l’influencer. Nous mentionnons, chaque fois que cela nous a semblé nécessaire, les principaux éléments de la critique adressée au discours patronal sur ces sujets.
Continuités et variations
On entend fréquemment dire que l’organisation du travail connaîtrait des transformations profondes du fait de l’automatisation-numérisation, mais aussi en raison de paramètres sociétaux liés au niveau d’éducation et d’information des salariés, et à l’évolution de leurs aspirations. Les transformations organisationnelles et managériales que nous avons pu observer sont réelles, mais lentes et assez peu spectaculaires dans l’ensemble.
Parler de « transformation » pourrait aussi laisser entendre qu’on assiste au passage d’un modèle d’organisation général et dominant vers un nouveau modèle. Or, plusieurs types d’organisation du travail ont coexisté à toutes les époques (taylorienne, en lean production, en structure simple, apprenante, libérée, etc.) : il n’y a donc pas d’évolution d’un modèle unique vers un autre modèle unique en voie de constitution, mais des circulations, des évolutions et des hybridations entre différents modèles existants. Tout au plus peut-on constater dans une majorité des entreprises observées une recherche tâtonnante vers un modèle d’organisation combinant rationalisation du travail et participation des salariés ; un modèle plus horizontal et plus « apprenant », susceptible de répondre à la fois aux besoins de la révolution numérique, aux aspirations nouvelles des salariés et à l’exigence accrue de compétitivité et d’agilité. Les méthodes que ces entreprises mettent en œuvre visent à favoriser les capacités d’apprentissage en autonomie, les modes de travail en intelligence collective, à renforcer selon la belle expression de Martin Richer « les terminaisons nerveuses »5 de l’entreprise comme réponses à un environnement instable et fortement concurrentiel. Mais la réalité des organisations, même les plus avancées dans cette voie, véhicule nombre d’ambiguïtés sur des termes tels qu’autonomie, responsabilité, polyvalence, délégation ou subsidiarité, etc.
Bonnes pratiques
Notre objectif était de déceler des pratiques inspirantes et d’avant-garde dans les usines. Nos observations ont fait progressivement apparaître un chemin de progrès capable de favoriser à la fois une bonne appropriation des technologies, une réponse aux besoins psychologiques des salariés et une performance globale de l’entreprise satisfaisante. Nous le présentons sous le nom de « modèle CALT » pour confiance, autonomie, lean et technologie. Ce modèle ouvre la voie à une proposition plus globale et militante que nous désignons par l’expression « design du travail » et qui vise à répondre à la crise de représentation que subit le travail de production, en vue de renforcer l’attractivité du secteur industriel dans son ensemble.
***
Pour prendre la mesure des transformations de l’organisation du travail dans les usines, nous examinerons : les besoins exprimés par les entreprises pour justifier les transformations organisationnelles (chapitre 1), les tendances en matière de gestion des compétences (chapitre 2), trois déterminants structurant l’organisation du travail (lean, autonomie, technologie) et leur articulation dynamique (chapitre 3). Enfin, nous mettrons en discussion une proposition originale : imaginer ce que pourrait être demain le « design du travail » (chapitre 4). Une annexe intitulée « 10 tensions qui questionnent le travail » permet de rattacher les observations de terrain à des problématiques plus générales concernant l’évolution du travail telles qu’elles sont saisies par nombre d’études et enquêtes sur ces sujets. Nous renvoyons dans le corps du texte à ces développements.
- 1. Pierre Veltz, La Société hyperindustrielle , Seuil, 2017.
- 2. Ernst&Young Advisory, Croire en l’industrie du futur et au futur de l’industrie , 2017.
- 3. Bpifrance Le Lab, L’avenir de l’industrie : le regard des dirigeants de PME-ETI sur l’industrie du futur et le futur de l’industrie , décembre 2018.
- 4. Tous les verbatim figurent dans le texte en italiques et entre guillemets. Les autres citations sont en romain.
- 5. Voir son Blog Management & RSE http://management-rse.com/
Besoins des entreprises et transformation
Pour comprendre les recompositions de l’organisation du travail, il est nécessaire de les lier aux besoins des entreprises aujourd’hui. Tous ces besoins ne sont pas nouveaux mais ils présentent une nouvelle acuité.
1.1 Compétitivité, agilité
L’organisation que les entreprises interrogées tentent de mettre en place vise essentiellement à répondre à deux exigences : la compétitivité et l’agilité. L’exigence de compétitivité est bien connue et ancienne, l’exigence d’agilité est plus récente.1
La compétitivité (voir figure 1.1), c’est conquérir des parts de marché en affrontant la concurrence : faire les bons produits et services, qui répondent aux besoins du client et de plus en plus à ceux de la société, et les faire bien, en respectant les critères de qualité de chaque marché et de façon rentable. Pour réussir dans la durée, il faut encore les faire mieux que les autres, c’est-à-dire faire appel durablement à toutes les ressources de l’amélioration continue.
L’agilité (voir figure 1.2) permet de s’adapter en permanence à l’imprévu. Elle
est la dimension nouvelle que l’organisation doit développer pour faire face au
monde VICA2. Elle recouvre plusieurs dimensions : la flexibilité se réfère à la capacité de l’entreprise à se reconfigurer pour s’adapter aux besoins changeants du client ou de l’environnement ; l’adaptabilité renvoie spécifiquement à la capacité des salariés à reconnaître et accepter le changement, et à apprendre vite en boucles courtes pour s’adapter et apprendre de leurs erreurs.
Cela suppose d’investir dans le développement des personnes. Enfin, la rapidité se réfère à la fois à la contraction des délais et à la vitesse de réaction et d’apprentissage.
Ces impératifs de compétitivité et d’agilité se traduisent très concrètement pour les dirigeants que nous avons interrogés en : raccourcissement des délais d’approvisionnement, de production et de livraison, production en petites séries, réduction des prix de revient, amélioration de la qualité et de la satisfaction client, innovation dans les produits et services, montée en gamme, pérennisation de l’activité en France, croissance du chiffre d’affaires.
L’adoption des technologies de l’industrie du futur représente un moyen d’atteindre ces objectifs. « L’arrivée du robot, à la fin de 2014, a eu pour effet de diviser le temps de soudure par trois ou par quatre selon les produits, avec une qualité constante. Ceci nous a permis de gagner de nouveaux clients et de diversifier nos secteurs d’activité, ce qui s’est traduit par une augmentation de 43 % de notre chiffre d’affaires en quatre ans. » (CFT Industrie, Cintrage et assemblage de fils, tubes et tôles)
Julien Chomat, DG de WorldCast, fait état d’une véritable « amazonisation » de la demande client, même sur un marché de niche BtoB comme les systèmes broadcast pour les entreprises de radiodiffusion. « La réduction des délais fait partie des arguments qui nous ont permis de gagner certains marchés et de faire la différence par rapport à nos concurrents. »
1.2 Une appétence pour l’organisation apprenante
Dès lors, développer l’agilité ou l’adaptabilité des équipes devient un impératif pour répondre à ces besoins. Ce cheminement suit plusieurs étapes : il faut d’abord convaincre les équipes du fait que le changement n’est pas l’ennemi mais une composante du travail. Il faut ensuite inciter les salariés à « avoir envie d’apprendre » par eux-mêmes et à avancer vers l’autonomie, ce qui permet de réduire les temps de contrôle et de décision induits par la chaîne managériale. Deming3 disait déjà qu’étant donné le niveau de complexité des systèmes modernes, les dirigeants et les cadres ne peuvent absolument pas comprendre ce qui se passe réellement sans une totale coopération des employés de terrain.
L’amélioration continue suppose aussi d’encourager les salariés à s’exprimer au sujet de leur tâche et de leur poste (décrire, diagnostiquer, résoudre les problèmes) et représente une étape vers cette autonomie désirée, apte à réduire les délais mais aussi pourvoyeuse de la créativité nécessaire à l’innovation.
De là découle pour les entreprises la nécessité de promouvoir la confiance bilatérale, les méthodes participatives, l’esprit de collaboration et la transversalité, ainsi que le bien-être au travail qui visent, tous, à favoriser la « libération » des énergies et l’engagement subjectif de chacun dans le travail, au service des objectifs posés par l’entreprise.
À l’évidence, il existe une appétence « apprenante », avec un recours plus ou moins important aux outils numériques pour appuyer la transformation.
Pour autant, le modèle reste plutôt un objectif à atteindre qu’une réalité avérée, et se combine avec des modèles anciens tels que les structures simples et les organisations en lean production, parfois encore imprégnées de taylorisme4. Il n’y a pas d’évolution vers un modèle unique en voie de constitution, mais des circulations, des porosités et des hybridations entre différents modèles d’organisation existants (voir figure 1.3).On constate une recherche d’équilibre encore tâtonnante entre rationalisation des procédures plus ou moins inspirées du lean et libération des énergies.
Qu’est-ce qu’une organisation apprenante ?
Une organisation apprenante regroupe des salariés qui disposent d’une forte autonomie dans le travail, autocontrôlent la qualité de leur travail et rencontrent fréquemment des situations d’apprentissage et de résolution de problèmes imprévus. Ils sont relativement nombreux à travailler en équipe, exercent le plus souvent des tâches complexes, non monotones et non répétitives et subissent peu de contraintes de rythme5.
Par exemple, Bosch, entreprise puissamment « lean », vise à devenir une « Learning company », c’est-à-dire à adapter en profondeur les modes de travail entre les collaborateurs et les méthodes d’apprentissage6, alors que simultanément des organisations en structure simple qui avaient peu de procédures tendent à introduire à leur manière le lean (voir chapitre 3). Le passage vers l’entreprise apprenante semble parfois plus aisé et plus rapide pour les structures simples, dès lors que le dirigeant est convaincu de la démarche.
Quelques chefs d’entreprise ont également fait référence à des catégories en devenir, telles que les entreprises libérées7, les organisations du travail participatives (OTP)8 ou encore les organisations opales9, mais souvent pour s’en distancer ou introduire des réserves ou des nuances (à l’exception d’AE&T qui se revendique du modèle de l’entreprise libérée).
1.3 Des transformations qui se déploient sur un fond de tensions
Comme l’indique de titre de l’ouvrage de Michel Lallement (Le Travail sous tensions, Sciences humaines, 2010), l’organisation du travail et la gestion des compétences à l’ère de l’automatisation/numérisation sont, dans cette époque de transition, des champs traversés de tensions. Les tendances d’évolution sont complexes et parfois difficiles à saisir. Sans prétendre à l’exhaustivité, nous avons recensé 10 tensions structurantes que l’on retrouve à des niveaux divers dans les entreprises observées (voir figure 1.4). Ces tensions représentent la toile de fond sur laquelle se déploient les transformations. Pour une compréhension plus détaillée de ces tensions et paradoxes, nous renvoyons à l’annexe (p. 104) qui développe chacune d’entre elles.
1.4 Des projets d’entreprise témoignant d’une approche globale de la transformation
La transformation à l’œuvre est généralement présentée par les dirigeants que nous avons rencontrés comme un vaste plan d’ensemble, portant sur tous les paramètres de l’organisation et pas seulement sur les technologies. Les patrons parlent au fond davantage du futur de l’industrie – de leur industrie – que de l’industrie du futur. Cette impression de vision architecturée pourrait cependant résulter d’un biais de notre approche, centrée sur la parole des chefs d’entreprise. Par souci de dégager le sens de l’action menée, ceux-ci ont naturellement tendance à présenter une narration (story-telling) organisée et ordonnée chronologiquement, là où les démarches ont souvent été juxtaposées de façon plus erratique et pourraient avoir été jalonnées d’erreurs et de corrections.
Ces plans de transformation, lorsqu’ils existent, ne sont pas nés par hasard. Ils ont pour origine des circonstances particulières auxquelles l’entreprise a été confrontée : une crise économique profonde ayant mis en jeu la survie de l’entreprise (Adam, AE&T, CFT Industrie, Lippi, SORI, Vision Systems, WorldCast), associée ou non à un changement de direction suite à une reprise ou à une transmission (Adam, Alliansys, CFT Industrie, SORI, Vision Systems, WorldCast). Dans quelques cas, le changement a été plus progressif et s’est inscrit dans une stratégie continue de progression et d’adaptation, marquée par la volonté de saisir toutes les opportunités ouvertes par les technologies (Bosch, SEW USOCOME, Schmidt Groupe).
Les plus petites entreprises ont été aidées par des programmes d’accompagnement liant un audit de l’organisation à l’introduction de nouvelles technologies : par exemple, le programme Robot Start PME piloté par le Cetim, ou les programmes régionaux pour l’industrie du futur.
C’est, par exemple, le cas de CFT Industrie : « Nous pensions que cet accompagnement porterait surtout sur les aspects techniques et, de fait, l’intervenant du Cetim nous a beaucoup aidés à rédiger le cahier des charges du robot, ou encore à établir un prévisionnel de productivité. Mais il nous a également fait réfléchir aux changements qu’allait induire ce nouvel équipement dans notre façon de travailler, à la nécessité de communiquer en interne et en externe sur cette robotisation et, surtout, il nous a donné des pistes pour transformer notre management et l’orienter vers le développement des talents. »
Lorsque Jean-Charles Rinn reprend Adam en 2009 en pleine crise, il redéfinit le projet stratégique : remettre le client au cœur du dispositif ; monter en gamme et sortir du marché de masse ; valoriser le volet social car il s’agit d’une industrie de main-d’œuvre sur un matériau vivant (le bois) ; produire uniquement en France. Le projet va déterminer une série d’actions dans les domaines du marketing (connaissance des marchés et montée en gamme), de la communication structurée et du management visuel (issus du lean), de la modernisation de l’outil industriel (nouvelle usine éco-conçue) et de l’articulation de la performance sociale avec la performance économique. Jean-Charles Rinn est l’un des rares dirigeants à faire état avec humilité des difficultés rencontrées : « On fait plein d’erreurs, c’est une perpétuelle remise en cause. Parfois le retour de terrain est un peu frustrant, mais malgré tout, la volonté stratégique du partage, de la transmission et de la pérennité de l’entreprise est inébranlable.
Point intéressant, quasiment toutes ces entreprises donnent une dimension environnementale à leur transformation, associée aux dimensions technologique, organisationnelle et sociale (Adam, Alliansys, Bosch, CFT Industrie, SEW USOCOME, SORI, WorldCast). Cela peut concerner les économies d’énergie, la réduction des rejets et des déchets, l’éco-conception des produits ou encore les actions sociétales à vocation environnementale (planter des arbres, installer des ruches).
En moyenne, selon les dirigeants que nous avons entendus, la transformation de l’organisation nécessite une dizaine d’années pour produire tous ses effets.
1.5 Un exemple : SORI, révélateur de tendances
Le cas de SORI présente un concentré d’approches intéressantes qui nous permettent de visualiser les briques constitutives d’une transformation à l’échelle d’une PME. Ce cas ne saurait cependant constituer un « modèle », car certaines dimensions de la transformation sont ignorées (le lean, par exemple).
Histoire
SORI est une entreprise familiale fondée en 1973, située à Tullins (Isère). Elle compte aujourd’hui 38 salariés (dont environ une dizaine d’emplois administratifs et commerciaux, le reste en production) pour un chiffre d’affaires de 6,2 millions d’euros (progression de 50 % en 3 ans).
Jusqu’en 1985, il s’agissait d’une société d’outillage, spécialisée en mécanique (tournage, fraisage, ajustage), qui travaillait essentiellement pour des donneurs d’ordres fabricants d’outillage, tels qu’Allibert, Merlin Gerin ou Black&Decker. C’est pour ce dernier qu’elle imaginera des coffrets permettant de ranger les perceuses et les meuleuses.
Suite à une baisse d’activité de Black&Decker, SORI connaît de grandes difficultés et dépose le bilan en 1986, à peine quelques mois après qu’Hervé Valliet, fils du fondateur, est entré dans l’entreprise. Hervé Valliet a fait un DUT de micro-électronique, et s’intéresse dès cette époque aux circuits numériques et à l’informatique industrielle. Il propose un plan de poursuite de l’activité, et un concordat d’apurement du passif est conclu qui s’étalera jusqu’en 2004.
Hervé Valliet décide alors d’arrêter la mécanique générale, et de s’orienter uniquement vers la tôlerie fine appliquée aux solutions de rangement pour les professionnels : coffrets, casiers, servantes d’ateliers, armoires de rangement d’outillage. L’entreprise s’organise autour de deux lignes de produits : des produits propres génériques sur catalogue (environ 300 références), et des produits labellisés pour le compte des grands fabricants d’outillage électroportatif. Les produits catalogue servent essentiellement les marchés des artisans du bâtiment et travaux publics, l’aménagement des véhicules utilitaires et les ateliers industriels. En complément, SORI distribue également des éléments de rangement en plastique de son fournisseur allemand de composants plastiques, puisque l’entreprise ne fait pas de plasturgie. SORI conçoit en interne tous les produits qu’elle fabrique : « conçu chez SORI, fabriqué chez SORI », telle est la devise maison.
Une réponse à la concurrence chinoise : le voyage des servantes d’atelier
À partir des années 2000, Hervé Valliet constate qu’il lui faut impérativement baisser les prix de revient pour rester dans la course face à la concurrence chinoise. Le renchérissement de l’euro par rapport au dollar (entre 2004 et 2014) a considérablement impacté la compétitivité de ses produits. 80 % du marché européen a été pris par des produits chinois. D’ailleurs, la totalité des fabricants français de solutions de rangement ont disparu (ils étaient une trentaine en France en 1987). S’il parvient à baisser les prix de revient même en restant marginalement plus cher, il pourra alors invoquer d’autres arguments auprès des acheteurs : la flexibilité, l’agilité et la rapidité, permettant aux acheteurs de moduler les commandes en fonction de la demande, la personnalisation des produits sur petites séries et le Made in France.
Le gros de la vente des accessoires d’outillage se fait sous la forme de promotions saisonnières, essentiellement à Noël. Pour une grande surface d’outillage en Europe, le cycle standard consiste à passer commande en mars à un fabricant chinois. Il faut donc définir à ce moment-là le type de servantes d’atelier (5, 6, ou 7 tiroirs) et les couleurs qui seront commandées. En juillet, la commande a été fabriquée. Elle est préparée, mise en container et expédiée pour une livraison en septembre en Europe chez le grossiste. Celui-ci répartit les produits pour une mise en place de la promotion dans les magasins autour du 15 novembre. Bien entendu, la prévision du nombre de servantes par type se révèle souvent fausse : par exemple, il ne se vend cette année-là que des servantes 7 tiroirs. Les autres produits doivent donc être soldés au 1 er trimestre de l’année suivante pour reconstituer la trésorerie et repartir pour un nouveau cycle en mars.
En réponse à cette situation, l’argument de SORI consiste à dire : certes, je suis 3 % plus cher que la concurrence chinoise, mais grâce à mon système de production ultra-flexible à base de cellules de production automatisées et une conception des servantes qui permet de les assembler en 5, 6 ou 7 tiroirs à la fin du cycle de fabrication, je peux vous livrer des servantes customisés en une semaine ! Les fonctions les plus sensibles à ces arguments ne sont pas les acheteurs qui ont essentiellement des objectifs de prix, mais les directeurs logistique, financier et commercial de ses clients qu’Hervé Valliet va rencontrer pour valoriser cet atout.
Organisation de la production
Pour atteindre son objectif de baisse des prix et de production flexible, Hervé Valliet va engager un plan d’investissement massif (de l’ordre de 3,5 millions d’euros sur 3 ans) visant à introduire des systèmes numériques intelligents : automatisation et robotisation de la production, simulation et jumeau numérique. Si l’entreprise avait déjà mis en place un ERP performant et customisé (basé sur 4D) et des machines à commande numérique « classiques », le virage vers l’industrie du futur a été pris en 2016 avec l’installation de nouvelles machines à commande numérique complexes et de 5 robots à bras articulé (4 sur 5 sont des robots encagés, 1 est un cobot) en 3 ans, au sein d’une organisation en 5 cellules : découpe laser de la tôle fine, pliage, soudage, peinture, assemblage.
Les cellules robotisées conçues par SORI sont très flexibles, et permettent de faire des séries extrêmement courtes (40 pièces). Cependant, de nombreuses opérations restent encore manuelles (assemblage). Une réflexion a été menée sur les flux et les stocks intermédiaires, sans pour autant qu’on puisse affirmer qu’il s’agisse de « lean manufacturing » (dixit Hervé Valliet lui-même).
Les machines sont choisies en fonction de leur performance énergétique, ce qui a permis de faire baisser les consommations, et donc les coûts, en passant d’un système tout hydraulique à un système hybride hydrau lique/actionneurs électriques avec récu pération d’énergie, qui consomme jusqu’à 5 fois moins.
La prochaine étape est le remplacement des anciennes machines de pliage, ce qui permettra de réduire nettement le niveau so nore de l’atelier, et surtout la robotisation de l’ensemble de la chaîne de peinture. « Robotiser la peinture sur des petites pièces mo biles comme les nôtres est assez compliqué, mais nous sommes en train de résoudre le problème avec notre fournisseur de robot » explique Hervé Valliet.
Les nouvelles cellules de production sont conçues par un intégrateur sur la base d’un cahier des charges mis au point en collaboration entre le bureau d’études, la maintenance et les opérateurs. Il arrive assez souvent que ce soit le personnel lui-même qui propose des adaptations du robot ou de ses mouvements, qui seront pris en compte par le fournisseur (par exemple, un robot de micro-soudure capable de changer d’outillage sans intervention humaine).
Les cellules robotisées10 ont été entièrement numérisées pour créer un modèle 3D per mettant de programmer les opérations à réa liser directement sur ce jumeau numérique de l’installation11 . Le programme ainsi réalisé est alors transféré sur le robot et testé en conditions réelles. L’ensemble de ce processus est ce que SORI appelle sa FAO
Selon Hervé Valliet, la transformation numérique de la production a permis de renforcer la compétitivité (avec des baisses de prix de 5 à 20 % selon les produits) et la flexibilité de la production (petites et moyennes séries), d’améliorer les conditions de travail avec réduction des troubles musculo-squelettiques (TMS) et d’élever les compétences des salariés qui voient en conséquence leur rémunération s’améliorer.
Une histoire bien française : l’arrogance du bureau d’études
En 2010, le bureau d’études (BE) de SORI est encore composé de quatre personnes qui représentent les plus gros salaires de l’entreprise. Il est devenu un véritable bunker, un État dans l’État. Ses délais de développement sont de plus en plus longs, des problèmes de qualité sont constatés, et les différends avec la production se multiplient, dégradant l’ambiance et le fonctionnement général. Le BE refuse de se considérer comme un service support de la production : « Qu’est-ce que vous voulez qu’on fasse avec les bourricots que vous avez embauchés dans l’atelier ? » ; « C’est tout marqué sur les plans. Si tu sais pas lire les plans, c’est pas de ma faute ». Après avoir mis en place une démarche d’accompagnement pour faire évoluer les personnes au sein du bureau d’études, Hervé Valliet, ne constatant aucune amélioration au bout d’un an, prend la décision de licencier l’intégralité de l’équipe, et de reprendre en main le BE en 2012, avec un jeune de niveau licence formé en alternance. Stupéfaction des personnes du BE qui se croyaient intouchables et irremplaçables !
Cette expérience a été fondatrice pour Hervé Valliet : « Ce n’est plus le savoir-faire qui compte, mais le savoir-être ». En conséquence et comme nous le verrons plus loin, les embauches sont faites sur les capacités : capacité à travailler en équipe, ouverture, mais aussi capacité à apprendre.
Une certaine conception de l’homme au travail
Chez SORI, la conception de l’entreprise s’inscrit dans une philosophie du collectif. Dès le milieu des années 2000, l’entreprise a supprimé la ligne hiérarchique (chef d’atelier), et favorisé l’autonomie et la responsabilisation des personnes. « Responsabiliser, c’est expliquer les problèmes. » Tous les salariés sont en râteau. Hervé Valliet décrit le fonctionnement de son entreprise comme tendant vers un « groupement d’artisans ». Tout le monde a accès à l’ERP, et les résultats de l’entreprise sont complètements transparents. La communication entre les personnes se fait de façon très informelle, les gens s’accordent spontanément et vont chercher l’information dont ils ont besoin, y compris dans le bureau du patron dont la porte est toujours ouverte et qui vit quasiment sur place. Tout le monde s’appelle par son prénom. Les salariés n’hésitent pas à poster sur les réseaux sociaux des petites vidéos de leurs réalisations. En principe, le personnel signe une charte informatique pour encadrer les usages, mais ce point n’a pas vraiment l’air de préoccuper le dirigeant : clairement, ici, la culture du secret n’est pas de mise.
L’investissement personnel du dirigeant dans l’entreprise vécue comme une famille (« c’est notre entreprise ») semble être une caractéristique marquante de SORI. Quasiment tous les bénéfices sont réinvestis dans le développement.
« Le CV, je m’en fiche complètement »
La majorité du personnel de production est composée de gens sans diplômes ou avec des diplômes sans rapport avec leur travail. La blague dans l’atelier, c’est « T’as quoi comme diplôme ? » « J’ai un C.RA.P (c’est râpé) ! ». Ils et elles (6 femmes) ont entre 30 et 40 ans, avec une ancienneté moyenne de 10 à 20 ans. La logique de recrutement est basée essentiellement sur le potentiel et le talent. « De toute façon, il n’y a quasiment personne qui soit formé en tôlerie fine ni en peinture. Je recrute donc essentiellement sur les savoir-être. Chez eux, les gens savent faire plein de choses et c’est ça qui m’intéresse. Je regarde s’ils sont curieux, débrouillards, malins. Le CV, je m’en fiche complètement. » C’est ainsi qu’Hervé Valliet a recruté ces dernières années un ancien boulanger et un CAP boucherie. Pas de recours à l’intérim par principe, mais une grande ouverture à l’alternance.
La transformation numérique a cependant créé de l’angoisse chez le personnel de production. Hervé Valliet a promis qu’ils allaient tous progresser ensemble. Aucun d’entre eux ne savait, par exemple, programmer des machines. La formation est devenue l’une des priorités de l’entreprise qui y a investi jusqu’à 100 000 euros, sur les trois dernières années, essentiellement en programmation machines pour une vingtaine d’opérateurs. Il s’agit de formations courtes (5 jours) menées chez les fournisseurs de solutions. Quand Hervé Valliet a commencé à parler de formation, les opérateurs « qui secouaient de la tôle » étaient très réticents ! Aujourd’hui, 6 à 8 personnes de la production ont vraiment changé de job et maîtrisent la FAO. « Les mêmes bourricots que dénonçait le bureau d’études » fait remarquer Hervé Valliet. On peut ici observer ce que représente réellement la « montée en compétences ». Ces opérateurs naviguent entre la salle des ordinateurs où ils programment les machines et robots selon le type de production, et la cellule de production où ils surveillent le déroulement des opérations. À voir Jonathan ou Jean-Philippe penchés sur des images en 2D ou 3D des robots, on pourrait croire qu’ils jouent à un jeu vidéo. Ni l’un ni l’autre ne souhaiterait revenir en arrière, et ils affirment que le travail est devenu plus intéressant et nettement moins pénible.
Le télétravail est également devenu possible grâce à de nouveaux outils de « domotique industrielle » : l’opérateur peut se connecter à distance, de chez lui, et reprogrammer la cellule. Récemment, des caméras ont été installées dans l’atelier, de façon à ce que l’opérateur-programmeur puisse non seulement visualiser à distance l’écran de la commande numérique, mais également le comportement réel du robot pour interrompre les opérations et les reprogrammer si nécessaire.
Et l’emploi ?
Pour Hervé Valliet, le robot ne tue pas l’emploi. Il permet de retrouver de la compétitivité, ce qui engendre une augmentation du chiffre d’affaires, et permet la création de nouveaux emplois. SORI a créé cinq nouveaux emplois en deux ans, uniquement à la production, et prévoit d’en créer au moins cinq autres dans les deux ans qui viennent grâce à l’augmentation des volumes. À la question « jusqu’où voudriez-vous croître ? », Hervé Valliet répond que 50 personnes lui semblent être un palier, et ce point de vue semble partagé par le personnel. Au-delà, cela deviendrait un autre type d’entreprise.
- 1. Nous empruntons à Cécile Roche, Lean and Agile Director chez Thales, les développements qui suivent, en les adaptant à notre sujet.
- 2. VICA pour Volatile, Incertain, Complexe et Ambigu.
- 3. William Edwards Deming (1900-1993), professeur et consultant américain en management, auteur des 14 points de Deming. Il a eu une grande influence au Japon. Ses principes sont orientés sur le développement de la connaissance dans un climat de coopération au service de la productivité et de la qualité.
- 4. Cette typologie des formes d’organisation du travail des salariés de l’Union européenne a été élaborée en 2005 par Lorenz et Valeyre sur la base des données de la troisième enquête européenne sur les conditions de travail. Voir Lorenz E., Valeyre A. (2005), « Les formes d’organisation du travail dans les pays de l’Union européenne », Travail et Emploi, no 102, avril, pp. 91-105.
- 5. Les organisations apprenantes sont les héritières des expériences d’élargissement et d’enrichissement des tâches et des groupes semi-autonomes de production, inspirés du modèle sociotechnique du Tavistock Institute of Human Relations .
- 6. Pour une vision plus détaillée des méthodes employées par Bosch, voir Planet Labor , Article n. 11053 du 21.03.2019, « Bosch continue à déployer son concept de “Learning company” ».
- 7. Isaac Getz et Bernard Carney, Liberté et compagnie ; Quand la liberté des salariés fait le bonheur des entreprises , Fayard, février 2012.
- 8. Martin Richer, « Les organisations du travail participatives : les 5 piliers de la compétitivité », Blog Management & RSE, 12 sep-
tembre 2013. - 9. Frédéric Laloux, Reinventing organizations : Vers des communautés de travail inspirées , Diateino, 2015.
- 10. Vidéo disponible sur https://youtu.be/NXtl2dd14NA
- 11. Vidéos disponibles sur https://youtu.be/pVhssI390_g et https://youtu.be/Xa0Eo5OSDk0
Gestion des compétences
L’exemple de SORI nous a permis de faire ressortir quelques pratiques émergentes dans la gestion des compétences, afin d’accompagner les transformations de l’organisation.
Le premier souci des entreprises concerne l’adaptation des compétences existantes : compétences métiers liées à la maîtrise des technologies certes, mais aussi savoir-être et état d’esprit permettant la transition vers une entreprise plus agile et plus apprenante. Cette adaptation passe par la formation mais aussi et surtout par des incitations aux apprentissages informels.
Le deuxième point de vigilance concerne le recrutement et la gestion des carrières. Face à une pénurie de compétences venant spontanément s’orienter vers l’industrie et les métiers de la production, les entreprises misent de plus en plus sur le potentiel et les talents des futurs salariés, quitte à les former en interne. Elles veillent ensuite à l’adéquation des talents et des postes pour fidéliser celles et ceux qu’elles ont eu tant de mal à attirer.
2.1 Adapter les compétences
Dans les entreprises interrogées, l’introduction de nouvelles technologies dans les ateliers ne s’est pas traduite par des licenciements. Ni d’ailleurs par des recrutements massifs. « Il faut faire avec les gens qu’on a » déclare Frédéric Lippi. En revanche, elle s’est accompagnée d’un important effort pour adapter les compétences. « C’est un enjeu pour nous d’accompagner les collaborateurs présents depuis longtemps dans l’entreprise afin de leur permettre de progresser et de conserver leur emploi » (Anne Leitzgen, Schmidt Groupe).
2.1.1 La formation continue
L’investissement dans la formation est largement mis en avant par les chefs d’entreprise. Ces formations ne relèvent pas seulement des techniques « métier », elles incluent des formations comportementales (savoir-être) et des formations destinées à élever la culture numérique des salariés.
Chez CFT Industrie, Elisabeth Klein indique avoir investi plus de 200 000 euros en formation pour 12 personnes depuis 2014. « Les apprentissages techniques représentent la moitié du budget formation. Parmi les formations techniques, certaines ne sont pas directement liées à nos métiers (par exemple, tous les salariés sont formés à Excel), mais nous considérons qu’elles pourraient être utiles un jour et, en attendant, elles peuvent intéresser les salariés pour leurs activités personnelles. Le reste est consacré aux formations […] qui développent une façon différente d’appréhender l’humain. »
Chez Alliansys, la transformation a demandé un gros effort de formation, « car certains n’avaient pas forcément toutes les connaissances nécessaires. Aujourd’hui, même les magasiniers doivent maîtriser Excel et savoir faire des tableaux croisés dynamiques. »
Au siège allemand de Bosch, le porte-parole RH a indiqué qu’en vue de déployer le concept de « Learning company», le groupe a investi en 2018 pour la formation « environ 250 millions d’euros. Soit environ 600 000 jours de séminaires et 600 000 jours de formation personnelle pour 400 000 salariés. […] Mais cela ne suffit plus par rapport aux cycles de vie des savoirs qui sont de plus en plus courts. Aujourd’hui on estime que ce qui a été appris à l’école et à l’université est dépassé dès l’âge de 35 ans. Et dans certains domaines, on a parfois du mal à savoir de quelles nouvelles connaissances on aura besoin dans 6 mois. »1 Concernant les personnels de production qui constituent la moitié des salariés de Bosch, le groupe a mis au point avec la Fédération allemande des chambres de commerce et d’industrie, 200 modules de formation sur toutes les briques de l’industrie 4.0.
2.1.2 Des formations pas toujours bien accueillies
La majorité des chefs d’entreprise insistent cependant sur un point : pour les personnels de production, la formation n’a rien de facile ni de naturel.
Cela résulte d’une très longue période durant laquelle la formation continue a été systématiquement proposée aux personnels les plus diplômés au détriment des autres. Dans l’édition 2018 de « Formations et emploi », l’Insee traite notamment de l’accès et de la place de la formation selon les parcours professionnels des salariés2 : si 59 % d’entre eux (45 % dans le secteur privé) ont suivi une formation en 2016, les cadres ont quasiment deux fois plus de chance que les ouvriers d’avoir accès à une formation professionnelle (66 % contre 35 %). Les peu ou pas diplômés se forment moins que les autres. C’est pourquoi, comme le résume Michel de Nonancourt, président d’Alliansys, il faut commencer par « dérouiller les cerveaux ».
« J’ai proposé des formations à des salariés qui n’en avaient pas fait depuis dix ans et qui me répondaient : “Pourquoi moi ? Qu’est-ce que vous avez à me reprocher ? Envoyez plutôt ma collègue !”. Même lorsqu’ils consentent à suivre une formation, il faut les accompagner, sinon cela ne sert à rien. » (Alliansys) ; « [La formation] a été précédée par un important travail de persuasion, sachant qu’à l’époque, la formation était considérée comme une punition plutôt que comme un investissement. » (Lippi)
Ces réticences ont conduit une entreprise comme Alliansys à mettre en place une autre approche de la formation : « Nous avons dû faire tout un travail auprès des formateurs, qui avaient l’habitude de délivrer un savoir magistral et se sont trouvés déstabilisés par certaines personnes à qui il manquait une partie des bases, mais qui, par exemple, savaient parfaitement braser, même si elles ignoraient pourquoi elles le faisaient de telle ou telle manière. En conséquence, elles refusaient qu’on leur explique comment elles devaient travailler. Désormais, nous employons une personne à plein temps pour préparer les formations, expliquer pourquoi tel groupe va devoir suivre tel programme, ce que l’on en attend, comment cela va se passer, etc. »
2.1.3 L’incitation aux apprentissages informels
La formation classique n’est que la pointe émergée de l’iceberg. Ce que les dirigeants essaient d’obtenir par des méthodes variées, ce ne sont pas seulement des compétences spécifiques, mais une orientation des personnels vers la curiosité, l’ouverture au changement, le décloisonnement, l’interaction, la collaboration et la densité relationnelle. Ils encouragent donc les apprentissages informels et collaboratifs (voir figure 2.1), tous ces « petits » apprentissages ancrés dans le quotidien, produits par des échanges libres ou dirigés entre collègues, mais aussi l’auto-apprentissage où l’individu définit lui-même ce qu’il désire apprendre et le cherche de manière autonome.
Visites d’entreprises
Elisabeth Klein chez CFT encourage le développement de la curiosité : « Nous avons proposé [aux salariés] d’aller découvrir d’autres entreprises, une fois par mois et sur le temps de travail. Dernièrement, par exemple, nous avons visité une entreprise de Blois qui fabrique des étiquettes. A priori, cela n’a rien à voir avec notre activité, mais cette société pratique le lean management et le 5S depuis huit ans déjà, et c’était intéressant de pouvoir profiter de son expérience en la matière. » Ces visites d’entreprises ne sont pas obligatoires, mais tout le monde joue le jeu. Certains salariés prennent même l’initiative d’aller découvrir d’autres sociétés sur leur temps de congés, le soir en sortant de leur travail ou à l’occasion de salons. Ce sont eux qui informent l’entreprise de l’existence de tel ou tel robot ou dispositif qui leur paraît intéressant, ce qui témoigne de leur implication dans la vie de l’entreprise. Les visites d’entreprises sont également une méthode employée chez WorldCast.
Vis mon job
La pratique du « Vis mon job » a été citée sous différentes formes par plusieurs entreprises et tend à se répandre dans le but de familiariser les salariés aux interdépendances des fonctions. « Récemment, nous avons créé un dispositif baptisé “Vis mon job” : une fois par an, chaque opérateur est invité à passer trois heures dans un service support de son choix (commercial, finance…). Il est accueilli par un membre du service qui lui explique quelles sont ses tâches quotidiennes. Inversement, chaque collaborateur des services support passe une journée complète en production. Autre initiative, tous les ans au mois d’octobre, chacun d’entre nous, PDG en tête, prend un balai, une pelle ou un chiffon à poussière et nous passons toute une journée à nettoyer l’usine. C’est très efficace pour créer des liens entre nous » (Jérôme Monvaillier, Vision Systems).
Rituels
Des rituels sont en place chez AE&T. Régulièrement, une équipe collecte les idées avant ou pendant un projet (Démo), ou encore fait un retour d’expérience sur un projet ou un événement une fois que celui-ci est terminé (Rétro). L’objectif est toujours de capitaliser sur l’expérience.
Working out loud
Comme d’autres entreprises allemandes et américaines, le groupe Bosch utilise en Allemagne la méthode « working out loud »3 mise au point par le coach John Stepper, basée sur l’accroissement des relations humaines pour atteindre un objectif, acquérir une capacité ou découvrir un nouveau champ de connaissances. Concrètement, des groupes de cinq personnes ayant des intérêts communs décident de se réunir sur une base volontaire, de se fixer un objectif et d’échanger des savoirs pendant douze semaines, en ligne ou en personne. Chaque semaine, la progression est ponctuée par des petits devoirs et des « défis » à réaliser. Les personnes apprennent ainsi à présenter leur travail, formuler des demandes, comprendre les intérêts et les savoirs des autres, et bâtir des relations professionnelles. Cette méthode vise à transformer les méthodes de travail et d’apprentissage.
Scrum à tous les étages
Chez AE&T, le scrum ou « méthode agile » a d’abord été adopté au bureau d’études, puis de fil en aiguille dans toute l’entreprise. Par effet de contagion, tous les secteurs de l’entreprise ont commencé à se prendre en charge et à se référer à la mêlée de rugby (scrum). De son côté, WorldCast a créé en son sein une start-up, Connect, qui développe des logiciels pour les objets connectés. Si cette création correspond à un objectif stratégique de diversification, le fait qu’elle soit hébergée dans les locaux a aussi pour objectif de familiariser les personnels avec les méthodes agiles de développement, de façon à ouvrir l’horizon des salariés affectés aux fabrications plus traditionnelles. Une hybridation qui, aux dires des dirigeants, se révèle cependant moins facile que prévue. Chez Bosch à Mondeville, un plateau de développeurs de solutions 4.0 a été intégré dans l’usine.
L’art de la conversation numérique
C’est sans doute chez Lippi que les apprentissages informels ont pris la forme la plus originale, quand les dirigeants ont fait le pari de promouvoir au début des années 2000 les usages personnels de l’Internet, des outils collaboratifs et des réseaux sociaux au sein de la vie professionnelle. « Concrètement, nous avons installé une sorte de Web School dans une salle de réunion. Des ordinateurs étaient mis à disposition toute la journée et chacun était invité à venir se familiariser avec les technologies du Web . » Untel créera un blog, l’autre montera des vidéos, le troisième créera des avatars sur Second Life.
Sur cette base, l’entreprise a alors introduit l’usage des réseaux sociaux, puis d’autres outils collaboratifs. « Un outil nous a paru particulièrement intéressant, Twitter. Nous avons créé un compte Twitter fermé auquel tous les salariés se sont abonnés. Ils se sont ensuite inscrits à leurs comptes respectifs afin que chacun puisse communiquer avec tout le monde. Nous avons, en quelque sorte, détourné Twitter pour en faire un quasi-réseau social d’entreprise. Un jour, un salarié a envoyé un tweet pour signaler un problème de production4 . Cinq minutes plus tard, quelqu’un lui a répondu qu’il s’agissait d’une question de nomenclature5 et non de production. Une demi-heure après, le problème était résolu. Ce jour-là, nous avons compris que nous disposions désormais d’un outil très puissant qui allait modifier le rapport au temps dans l’entreprise. Nous avons ensuite adopté des outils collaboratifs proprement dits, notamment Google+. Ce réseau social est très adapté au fonctionnement d’une entreprise . » Tous ces outils collabora tifs ont permis de passer d’une conversation dite discrète (c’est-à-dire menée à quelques-uns dans un bureau ou autour de la machine à café) à une conversation indiscrète , à laquelle peuvent être associés, en fonction des besoins, 30, 40, 60 ou 80 % de l’effectif de l’entreprise. Grâce à ce basculement, le système hiérarchique et pyramidal s’est trouvé progressivement ébranlé, et l’entreprise s’est mise à apprendre collectivement de façon beaucoup plus rapide. L’utilisation des outils collaboratifs a produit de nombreux effets positifs. Elle a poussé chacun à prendre conscience, de façon très concrète, du fait que l’entreprise recouvre bien d’autres choses que son propre champ d’action et qu’une part de son efficacité repose sur des acteurs situés au-delà même du périmètre de l’entreprise. Elle a permis aussi de mesurer les conséquences négatives de certains actes et d’accroître le sens des responsabilités. Quand l’atelier envoie chez un client des produits qui ne sont pas totalement finis et que le commercial relaie le mécontentement du client et joint des photos à son post, la récrimination porte bien plus que lorsqu’elle passe par la voie normale.
Frédéric Lippi a un stock inépuisable d’histoires très convaincantes sur les effets positifs de cette communication non structurée : « Il y a quelques jours, quelqu’un signale le montant des commandes enregistrées au cours de la jour née, et l’accompagne d’un compliment : “Bravo au commerce !”. Ce mail a été jugé intéressant par vingt personnes et plusieurs ont pris la peine d’écrire des commentaires : “Super !”, “On lâche rien et on est les meilleurs”, “Good job !”. Ce qui me paraît intéressant est que ce sont les équipes qui se congratulent elles-mêmes. Ce type de message fabrique de la reconnaissance et de l’automotivation .» La conversation s’étend également à l’extérieur de l’entreprise : « Il y a quelque temps, par exemple, des concessionnaires ont formulé des critiques à propos de la présence trop visible de notre logo sur un nouveau produit. Le marketing a posté les photos d’une proposition alternative et les concessionnaires l’ont rapidement validée. Nous avons gagné un temps considérable par rapport au processus qui aurait consisté à leur adresser un questionnaire ou à les appeler un par un . »
À l’objection qu’il entend souvent, selon laquelle cette approche doit générer une belle pagaille, Frédéric Lippi répond, imperturbable, que la « conversation » fait partie du travail : « C’est en se confrontant à des visions du monde différentes que l’on développe sa capacité à changer. En général, les conversations sont menées au sein de groupes homogènes de dix à quinze personnes : celles qui sont concernées par le problème. »
2.2 Miser sur les potentiels
Compte tenu de la pénurie de compétences ou de l’inadéquation des compétences, les entreprises industrielles ont désormais tendance à recruter non plus sur la base d’un profil mais d’un potentiel, puis à former la jeune ou moins jeune recrue pour atteindre le niveau de compétences requis.
2.2.1 Recruter sur les potentiels
Pour recruter les nouveaux profils, l’alternance reste une voie plébiscitée, parce qu’elle permet de « tester » les candidats dans la durée. Chez Bosch à Mondeville, la majorité des développeurs de solutions pour l’industrie 4.0 sont des alternants qui proviennent de différentes écoles d’informatique de la région de Caen. Du niveau BTS jusqu’au doctorant, ils travaillent sur des projets réels, comme par exemple la programmation de futurs AGV, ou la réalisation d’un POC (proof of concept) de réapprovisionnement de ligne gravitaire, pendant une durée de 7 à 18 mois.
Pour des postes faiblement à moyennement qualifiés, les dirigeants affirment s’intéresser de moins en moins au CV, et de plus en plus aux traits de caractère, à la personnalité et aux activités dont témoigne le « hors CV ». Il s’agit de repérer le potentiel, les aptitudes et les capacités, davantage que les savoirs et savoir-faire à un instant donné. Directeur RSE de l’Olympique Lyonnais, Laurent Arnaud a mis en place avec le Campus Veolia et Pôle Emploi, un audacieux programme de gestion des emplois à l’échelle du territoire (ODAS6), il explique ainsi cette nouvelle philosophie de recrutement : « L’idée, c’est d’accompagner les entreprises à regarder les potentiels des personnes différemment. Plutôt que de chercher des gens qui savent faire le boulot, regarder ce que réclame le boulot précisément, et regarder plutôt ce qu’il faut leur apprendre pour être en parfaite maîtrise. Chacun a des capacités individuelles qui peuvent l’amener en théorie à faire plein de choses différentes tout au long de sa vie, avec un effort d’adaptation à fournir qui est plus ou moins important. » Ou formulé à peine différemment par Vision Systems : « Chacun de nous possède de multiples compétences en plus de ses compétences professionnelles. Quand vous bricolez le dimanche matin, vous faites de la gestion de projet sans le savoir, et quand vous rangez votre garage, vous mettez en œuvre la méthode 5S. »
Face aux difficultés de recrutement dans l’usinage, Landry Maillet, le PDG d’ABCM, a carrément décidé d’ouvrir une formation partagée avec d’autres entreprises. « On forme des gens de l’extérieur pour rentrer dans nos métiers. On s’est mis à plusieurs confrères de la profession et on a demandé à l’AFPI7 de nous créer une formation. On s’est dit : on ne trouve personne, alors on identifie des personnes qui ont un savoir-être, qu’on a vues en intérim, ou des gens qu’on a côtoyés, qui sont venus chez nous, qui ont l’air bien. On leur propose cette formation et on les met à l’AFPI. Quand ils sortent, on les embauche en CDI. » Et il poursuit : « Les CV, on ne les regarde plus. Plus exactement, on regarde les premières lignes du CV. Par exemple, “je suis allé castrer du maïs quand j’avais 13 ans, j’ai bossé avec mes parents, j’ai configuré des logiciels, j’ai assemblé des PC”. On voit les gens qui sont bosseurs au fond d’eux dans les premières lignes de leur CV. »
2.2.2 Accompagner les potentiels et les talents
Au-delà du recrutement, certaines entreprises veillent, dans la durée, à l’adéquation des postes et des talents. Dans des sociétés qui grandissent ou se transforment, des personnes révèlent leurs talents, quand d’autres ont du mal à s’adapter aux évolutions. Au point que Brice Goguet du Groupe Voltaire s’entend parfois dire en interne qu’« on est trop dans le Secours catholique à chercher en permanence le bon poste pour la personne. »
Chez Lippi, jusqu’à 15 % des effectifs peuvent changer de poste chaque année en raison des talents que révèle leur utilisation du numérique.
Toujours dans l’esprit de faire émerger les talents ou de les fidéliser, les entreprises encouragent les passionnés, et les soutiennent dans leurs idées de développement personnel ou d’intrapreneuriat. Ce qui permet, au passage, d’appuyer les capacités d’apprentissage de l’organisation elle-même. Adam, par exemple, soutient les projets personnels de ses jeunes salariés à travers un incubateur interne de design, relayé en externe à Bordeaux par l’atelier Zelium8 qui est à la fois un lieu de co-working et un espace de fabrication pour des projets originaux en ébénisterie. WorldCast a longtemps hébergé dans ses locaux une entreprise de consulting achats, créée par l’un de ses salariés et incubée chez eux.
Autre exemple : à l’usine Bosch de Mondeville, la fabrication additive a été introduite de manière originale. Un technicien s’y intéressait à titre personnel et disposait d’un certain nombre de compétences de base (informatique, codage…) ; la direction lui a donc acheté une imprimante 3D pour expérimenter. Son projet a ensuite gagné un concours inter-usines de Bosch. Le prix de 200 000 euros a permis d’acheter d’autres équipements. Aujourd’hui, ils sont trois à animer ce département, installé dans un espace dédié au milieu des lignes de production. La trentaine d’imprimantes 3D utilisent toutes du matériau plastique de plusieurs types (fil, résine, poudre) et servent à la fabrication de petites pièces de réparation machines, de nacelles de convoyage adaptées à chaque produit, mais également au prototypage, à des simulations de fonctionnement de nouvelles lignes et à la réalisation d’éléments ergonomiques pour les postes de travail.
- 1. Planet Labor , Article n. 11053 du 21.03.2019, « Bosch continue à déployer son concept de “Learning company” ».
- 2. https://www.insee.fr/fr/statistiques/3526086
- 3. John Stepper, Working Out Loud: For a better career and life , Ikigai Press, 2015.
- 4. Un composant nécessaire à la production prévue n’était pas disponible en quantité suffisante.
- 5. Le même composant était enregistré dans le système d’inventaire sous deux « noms » différents, donc il en existait suffisamment (sous l’autre nom) pour démarrer la production.
- 6. https://www.odas-rh.com/
- 7. Association formation professionnelle pour l’industrie.
- 8. http://www.atelierzelium.fr/
Trois composantes structurant l’organisation du travail
Dans quasiment toutes les entreprises observées, trois composantes structurent l’organisation du travail : le lean, l’autonomie et la responsabilité des personnes, la technologie. Et pas forcément dans cet ordre ! Ces trois composantes entretiennent entre elles des relations dynamiques (voir figure 3.1 ci-après), et c’est leur conjonction qui doit contribuer à un changement culturel1, c’està-dire à une transformation de l’état d’esprit général des salariés, susceptible de favoriser l’atteinte des objectifs poursuivis (compétitivité, agilité). Comme le résume Alexandre Ricard, le PDG du groupe Pernod-Ricard : « L’entreprise qui gagnera sera celle dont les équipes embrasseront le plus vite le changement et adopteront le plus vite les nouvelles façons de travailler et de penser. Donc, pour le dire autrement, les champions du change management. D’où la nécessité de distiller le bon “mindset”, qui vaut à lui seul toutes les recommandations stratégiques. »2
3.1 Lean
Le lean constitue quasi systématiquement l’une des briques de la transformation des organisations, y compris dans la période récente pour les PME en phase de modernisation. Ce modèle industriel a émergé dans les années 1950 chez Toyota, il a été théorisé au MIT à la fin des années 1980 et s’est diffusé graduellement à partir des années 1990. Cette diffusion est d’abord due à la puissance du modèle, qui a permis à Toyota de passer du statut de petit constructeur local à celui de géant mondial. Elle est ensuite le résultat d’une intense promotion menée depuis trente ans par les acteurs privés du conseil, mais aussi par les organisations patronales ou publiques de soutien à la compétitivité, et qui semble se renouveler aujourd’hui sous le vocable d’« excellence opérationnelle » en lien avec le discours sur l’industrie du futur3. Cette réappropriation par des acteurs multiples a rendu le concept assez polysémique. Le lean prêt à l’emploi proposé par tel ou tel cabinet de conseil et imposé aux personnels de l’entreprise cliente peut n’avoir que quelques outils en commun avec le système mis en place chez Toyota dans les années 1960.
La large diffusion de ce modèle organisationnel incite à revenir sur les critiques qui lui sont adressées et sur les bénéfices qu’on peut en attendre.
3.1.1 Critiques adressées au lean
De nombreuses critiques ont été adressées au lean. D’une part, il a été maintes fois souligné qu’il peut avoir des effets néfastes ou non désirés sur la santé des travailleurs4. En privilégiant la traque des temps morts (les gaspillages), en encadrant le travail par la fixation de normes de productivité, en réduisant les marges de manœuvre, le lean serait non seulement porteur d’un risque d’intensification du travail, mais plus encore destructeur de la façon dont le « travail réel » crée de la valeur, via les ajustements et les libertés que les travailleurs se donnent par rapport à la prescription et par la mobilisation de leurs ressources inventives. À la pointe de cette critique, on trouve les ergonomes et les psychologues du travail, souvent sollicités pour accompagner le déploiement de la méthode5. On notera toutefois qu’après avoir fortement augmenté dans les années 1990 et 2000, l’exposition des salariés aux contraintes de rythme de travail tend, depuis 2013, à se stabiliser6. Serait-ce le signe que les organisations ont su métaboliser ou adapter les standards du lean ? Il sera intéressant de suivre cette tendance à l’avenir.
D’autre part, les résultats du lean en termes de gains de productivité durables sont également contestés. S’il produit souvent des gains rapides à court terme, il a aussi fréquemment engendré une démobilisation et un désengagement progressif des salariés – du fait de la contraction des marges de manœuvre – qui viennent réduire la portée des résultats engrangés. Dans les grandes organisations, cette critique, portée par les CHSCT et les syndicats, a été à l’origine de nombreuses tensions sociales si bien que les directions générales ont fini par la prendre en considération. Au-delà même de la dégradation du climat social, des résultats de productivité souvent décevants sur le moyen terme ont incité les directions à desserrer l’emprise de la doctrine lean et à rendre aux travailleurs des marges de manœuvre. En témoignent les expériences menées chez Michelin7 ou à l’usine Renault de Flins8 qui, sur des bases différentes, visent à redonner du « pouvoir d’agir » aux opérateurs.
Il serait donc tentant de penser que, si les résultats n’ont pas été au rendez-vous, c’est que le lean aurait été mal compris, dévoyé, n’aurait pas impliqué les personnels de production dans les processus de rationalisation et qu’il conviendrait de revenir à ses sources (le Toyotisme) ou de le faire évoluer.
3.1.2 Le lean, système vertueux ?
Le lean peut être conçu comme un système global en rupture avec le taylorisme, avec son vocabulaire, ses rituels, ses « maîtres » (Sensei) et qui doit être appréhendé dans toutes ses dimensions pour pouvoir produire réellement tous les effets attendus. Cette approche serait par nature vertueuse puisqu’elle ne promet rien de moins que de combiner gains de productivité, amélioration des conditions de travail et renforcement de l’autonomie des personnes : elle pourrait donc « changer le monde » selon la promesse de ses promoteurs américains Womack, Jones et Roos9.
Michel Sailly, dans son essai Démocratiser le travail10, met en lumière la nature profondément anti-taylorienne du lean tel qu’il est décrit dans les ouvrages fondateurs. D’abord, tout se passe sur le terrain. Ensuite, l’amélioration continue (Kaizen) est centrale. Troisièmement, l’autonomie et même la subsidiarité y sont fondamentales, les standards étant construits par les équipes. Quatrièmement, l’ensemble des parties prenantes sont prises en compte, même si le client est premier. Enfin, le lean est fondé sur une culture du respect des hommes, de leur intelligence et de leurs compétences. Selon la littérature, le lean fait donc une large place à l’opérateur et à sa participation active.
Cécile Roche est membre du conseil d’administration de l’Institut Lean France, Sensei11 et auteure de plusieurs ouvrages sur le lean12. Elle s’inscrit pleinement dans la logique de ce lean originel, considéré comme authentique. Selon elle, il s’agit « d’un système de développement continu des personnes » ou, pour le dire autrement, d’un système d’apprentissage en boucles courtes. « Le lean doit être compris comme un système qui ne sert pas à pressuriser les gens comme dans les années 1980-1990, mais comme une “machine” à donner de l’autonomie dans la résolution des problèmes. » Cécile Roche reconnaît cependant que ces outils sont assez faciles à dévoyer et que leur application nécessite une grande vigilance. Par exemple, on demande aux opérateurs de faire des commentaires sur les problèmes rencontrés. Certains managers oublient cette phase pour demander directement un plan d’action, ce qui est contreproductif car le problème n’a pas été explicitement analysé et qu’on n’a pas demandé aux personnes de prendre le temps de réfléchir avant de passer au plan d’action.
Qu’en est-il dans les entreprises rencontrées pour cette étude ? Quel lean appliquentelles ?
Plusieurs conceptions du lean
Pour résumer, le lean peut être conçu comme : (1) un ensemble d’outils dans lequel on peut piocher ; (2) un système d’apprentissage visant le développement continu des personnes et permettant de faire la chasse aux non-valeurs ajoutées pour le client ; (3) un système permettant de construire une stratégie à partir du terrain13.
3.1.3 Observations : un lean « boîte à outils » dans les PME, un système structuré dans les grands groupes
Des pratiques lean sont généralement à l’œuvre dans toutes les entreprises observées, même les plus petites (CFT Industrie, 12 personnes). Les niveaux de maturité peuvent cependant être très différents : Bosch pratique le lean depuis vingt ans à l’usine de Mondeville, quand CFT Industrie l’expérimente depuis seulement trois ans.
Le flux tiré est loin d’être la norme, et selon les secteurs d’activité, les stocks de produits finis demeurent encore importants pour faire face aux exigences de contraction des délais des clients. La consolidation des diagnostics effectués de 2014 à 2017 sur 300 PME du programme Usine du futur en Nouvelle-Aquitaine a fait apparaître que 10 % seulement des entreprises étaient en flux tiré.
Dans les grandes entreprises observées, le lean est un système global adapté à la culture de l’entreprise. Il porte souvent un nom maison, est documenté, et en général soutenu par des spécialistes internes. Il se rapproche de la définition n°2 donnée ci-dessus, même s’il n’est pas toujours décrit comme un système d’apprentissage visant le développement des personnes.
Dans les PME, le lean s’utilise le plus souvent comme une boîte à outils dans laquelle on pioche (5S, management visuel, rituels de communication structurée). Curieusement, l’amélioration continue (le Kaizen) est assez peu citée par les dirigeants ; c’est pourtant la pierre angulaire du système.
Management visuel et rituels de communication
Dans le cadre du programme Usine du futur de la Région Nouvelle-Aquitaine, WorldCast a été accompagné par un cabinet spécialisé pour la mise en place d’un « Lean durable® »14. Des méthodes simples et jugées efficaces, comme le management visuel ou les points 5 minutes tous les matins, ont été introduites. Selon Julien Chomat, son directeur général, « depuis, il n’y a quasiment plus d’e-mails internes, les gens se voient, parlent et résolvent les problèmes. » Le management visuel et les rituels de communication structurés (points 5 mn, 15 mn, 60 mn) font partie des outils du lean les plus souvent cités : on les retrouve chez Adam, AE&T, Alliansys, Lippi, Groupe Voltaire, etc.
Cependant, ce qu’on entend par « management visuel » dans des structures petites ou moyennes – le plus souvent via des post-it® magnétiques sur tableaux – n’a pas grand-chose en commun avec le « global monitoring » de Bosch à l’usine de Mondeville, ou encore avec le TRSP (temps réel de suivi de production) à l’œuvre chez SEW USOCOME. À Bosch Mondeville, le management visuel prend la forme d’écrans surplombant les lignes ou les cellules, qui indiquent aux opérateurs le plan de production, les objectifs, le réalisé et le reste-à-faire en temps réel, ainsi que les incidents de production. Des smileys (rouges en cas de retard, verts quand tout est OK) donnent la tonalité de l’avancement. Il ne s’agit pas tout à fait du même « lean » que dans les PME. Les dirigeants de Bosch Mondeville reconnaissent d’ailleurs que l’outil de management visuel a nécessité beaucoup de pédagogie et de dialogue avec les représentants du personnel pour qu’il soit pris « pour ce qu’il est » : un outil de mesure pour l’amélioration collective de la performance de l’équipe et non un outil destiné à juger la performance individuelle de chacun. Preuve que « l’acceptabilité » du dispositif n’était guère spontanée et a nécessité un accompagnement.
Sur ce sujet, les termes employés par JeanClaude Reverdell, DG de SEW USOCOME, sont quasiment les mêmes que chez Bosch : « Avant d’instaurer ce dispositif, nous en avons discuté avec les représentants du personnel. Il a été jugé acceptable à la fois parce qu’il ne s’agit pas de “flicage” individuel et parce que la mesure de la perfor mance est ainsi transparente pour tout le monde. Si la production est interrompue, les opérateurs doivent en indiquer la raison : aléa technique, manque de pièces, problème de qualité, etc. ».
Dans les deux cas, on notera que cette application rigoureuse du lean est le fait de deux entreprises de taille importante et dont la maison mère est allemande. Aux dires de leurs dirigeants, il faut toutefois rester extrêmement vigilant dans l’utilisation quotidienne de ces outils de mesure pour qu’il n’y ait pas de dérive.
Un outil jugé efficace et structurant…
Les dirigeants interrogés se montrent dans l’ensemble très satisfaits de leur expérience du lean qu’ils considèrent comme un outil d’organisation particulièrement structurant et efficace : « C’est un outil très utile, et humain si on sait bien s’en servir» (Jean-Charles Rinn, Adam).
Chez WorldCast, par exemple, la cartographie des flux de valeur ou VSM (Value Stream Mapping15) effectuée au cours de l’audit Usine du futur a permis de faire apparaître que les flux de l’entreprise étaient extrêmement compliqués et peu efficients, avec en particulier des circulations multiples de pièces entre différents sous-traitants. Ce diagnostic a conduit, à partir de 2015, à faire le choix d’un sous-traitant unique pour assembler l’ensemble des produits, afin de simplifier les flux. Ce sous-traitant français, situé à proximité, est devenu « l’usine » de WorldCast qui lui achète désormais directement des produits finis. Les ERP des deux entreprises sont connectés. WorldCast garde la maîtrise des achats, de la conception, des méthodes, du réglage et des tests de produits, ainsi que de la logistique d’expédition. C’est un exemple d’entreprise étendue, modèle de relations clients-fournisseurs soutenu par les nouvelles technologies ou Manufacturing as a Service.
… Mais un outil parmi d’autres
Plusieurs dirigeants complètent spontanément le lean par d’autres approches managériales. Pour Frédéric Lippi, par exemple, le lean doit être adossé à « un désir commun » pour produire des effets.
Il distingue la communication structurée par les méthodes lean et la communication non structurée produite par les outils collaboratifs utilisés de manière informelle : « Nous avons mis en place un système de communication structurée inspiré du SIM (Short Interval Management), qui fait partie du TPS (Toyota Production System). Le SIM consiste à organiser des réunions courtes et régulières au cours desquelles sont passés en revue des indicateurs permettant d’identifier les écarts par rapport aux standards et de discuter des corrections à apporter. Les équipes sont formées pour prendre leurs propres décisions au vu de ces indicateurs, sans avoir à faire appel à la hiérarchie. » Et il ajoute immédiatement : « […] mais ce sont les outils collaboratifs qui contribuent à résoudre une bonne partie des problèmes en temps réel. Les mails ou les posts offrent un canal de communication et des possibilités de correction supplémentaires. De plus, ils s’accompagnent généralement de photos, dessins, copies d’écran ou graphiques qui rendent la communication beaucoup plus explicite et percutante. »
Ce qui fait dire à Frédéric Lippi qu’« améliorer les problèmes des clients, résoudre tous les points de contention de bout en bout sans en laisser un seul de côté, ce n’est pas que du processus, c’est aussi de la culture ! ». Il considère que c’est bien davantage l’évolution de l’organisation de Lippi dans son ensemble, plutôt que le lean seul, qui a permis d’améliorer les résultats de sa société : un cocktail subtil, détonnant, et pas totalement anticipé, entre lean, outils numériques et autonomie des personnes. C’est ce qui a permis de casser la culture traditionnelle du « attends » (le client peut attendre) et de basculer vers le « à temps » (produire à temps), jusqu’à devenir une culture propre à l’entreprise. « Il faut aussi être patient, dit-il, ce résultat est arrivé près de 12 ans après l’avoir voulu. » Mais ce travail n’est jamais terminé.
3.2 Autonomie, responsabilité, participation
Des dizaines d’articles sont consacrés chaque mois par la presse professionnelle et les blogs d’experts à l’intelligence collective et à la coopération en entreprise, aux façons d’y favoriser l’autonomie et la densité des relations ou encore de développer des démarches participatives.
Une intense promotion est faite de ces concepts et méthodes pour l’amélioration de la performance, en lien avec la modernisation des entreprises. Dans Le Guide des technologies de l’industrie du futur16, qui expose la vision portée par l’Alliance pour l’Industrie du Futur, le mot « collaboration » est cité 29 fois ; « autonomie », 11 fois ; « responsabilisation », 5 fois ; « coopération », 5 fois ; et « intelligence collective », 4 fois.
3.2.1 Autonomie-responsabilité : une tentative de définition
Ces deux termes indissociables exercent aujourd’hui une grande attraction sur les salariés ; ils sont aussi revendiqués comme des objectifs par les entreprises pour plusieurs raisons : les décisions prises au niveau du terrain sont souvent plus pertinentes (« c’est celui qui fait qui sait ») et mieux appliquées (« une personne qui prend une décision devient plus investie dans son résultat »17).
Le terme « autonomie » vient du grec auton (soi-même) et nomos (la loi, la règle, l’organisation) : il s’agit de déterminer soi-même ses propres règles. Martin Richer, associé au think tank Terra Nova, la définit comme « l’incorporation du “décider” dans l’acte de travail »18. Le psychologue du travail Yves Clot parle du « pouvoir d’agir » non seulement sur son travail, mais sur la prescription qui régit ce travail. Au passage, il rappelle que « l’autonomie, ce n’est pas la liberté, mais la construction de la prescription »19.
Synthétisant plusieurs approches, La Fabrique de l’industrie, l’Anact et Terra Nova ont proposé un modèle d’autonomie en trois niveaux20.
Le niveau 1 est centré sur la tâche. L’autonomie consiste dans la latitude existant pour le salarié de pouvoir définir sa propre tâche : séquencement, méthode d’exécution, rythme de travail, outils à utiliser, etc. L’amélioration continue avec la participation des opérateurs intervient à ce niveau.
Le niveau 2 définit le pouvoir pour le salarié ou pour le collectif de travail d’exercer une influence sur l’environnement organisationnel, en participant à l’amélioration de l’organisation du travail, en influençant les décisions qui concernent le travail ou les modes de coopération nécessaires à la bonne exécution du travail. C’est ici qu’entrent en jeu les méthodes de management participatives.
Le niveau 3, enfin, mesure l’implication des salariés dans la gouvernance de l’entreprise à travers le dialogue social ou la négociation sur les conditions de travail, le partage de la valeur créée, etc. Ce niveau ne sera pas abordé dans le cadre de cette étude21.
La responsabilité est l’autre face de l’autonomie. C’est un terme ambigu qui doit être manipulé avec précaution. La responsabilité recouvre certes la capacité à agir de son propre chef, mais aussi le devoir de répondre de ses actes. L’anglais nous éclaire sur ce point, en distinguant ce que la langue française tend à regrouper: empowerment et accountability. Empowerment indique le processus par lequel on acquiert du pouvoir d’agir sur son travail. Accountability désigne le lien par lequel un résultat peut être porté au compte de la personne qui en est à l’origine (la reddition des comptes).
Cette polysémie révèle l’importance de rechercher à tout moment un équilibre entre ces deux composantes de la responsabilité. On considère généralement que le management « à la française » tend à mettre davantage l’accent sur l’imputabilité des actes, c’est-à-dire les manquements et les erreurs, plutôt que sur l’empowerment.
3.2.2 Observations : les chemins de l’autonomie
Dans toutes les entreprises observées, la tendance des dirigeants consiste à mettre en avant leur volonté de développer l’autonomie des équipes et l’existence de démarches participatives à différents niveaux de l’organisation. Néanmoins, il faut « creuser » le discours pour recueillir des indications sur la manière dont cette autonomie est conçue et mise en œuvre dans l’organisation.
Volonté et exemplarité du chef d’entreprise
L’autonomisation des équipes provient le plus souvent d’une impulsion venue d’en haut. Les dirigeants qui s’orientent vers ce type d’organisation affirment ne pas aimer contrôler : « Je n’aime pas contrôler les autres et, par conséquent, j’essaie de faire en sorte qu’ils se contrôlent eux-mêmes » (Frédéric Lippi) ; « Je suis allergique aux organigrammes » (Brice Goguet, Groupe Voltaire). Ou encore ils se disent attachés à limiter les marques et privilèges hiérarchiques pour favoriser l’esprit d’équipe : « La place de parking de la direction, c’est fini. C’est dans l’ordre d’arrivée, premier arrivé, premier garé. C’est juste logique, si j’arrive le dernier, je me gare où il reste de la place. Au foot, ce n’est pas parce que c’est le meilleur buteur de la saison que c’est lui qu’on doit remercier tous les jours. Non, il a marqué des buts parce que ses collègues lui on fait des passes. C’est toute l’équipe. On essaye de limiter cette hiérarchie pour avoir cette agilité et ce dynamisme » (Landry Maillet, ABCM). Ce point est largement confirmé par les déclarations des dirigeants interviewés dans le cadre d’une autre étude concomitante22 qui s’intéresse particulièrement aux entreprises sensibles aux questions d’autonomie et de responsabilité.
Mais, pour maintenir ce cap, le dirigeant doit être passé par un travail sur soi et sur le traitement de ses peurs : « Que faire en effet de ses craintes, de cette peur de ne pas réussir, de cet argent qu’il faut investir pour un résultat incertain, du regard des autres et de sa réputation en cas d’échec… Finalement, le mieux pour surmonter ses peurs, c’est d’en parler sans honte… » indique Frédéric Lippi.
Pour Elisabeth Klein chez CFT Industrie, le travail sur soi a consisté à apprendre à dire « je ne sais pas ». « Au fil des ans, j’ai appris à dire “je ne sais pas” à un collaborateur, ce que je n’aurais jamais fait il y a quinze ans. Je lui aurais répondu : “Je vais réfléchir et je reviens vers toi”, puis je me serais débrouillée pour trouver une solution. Aujourd’hui, je lui dis : “C’est toi le spécialiste. Toi, qu’est-ce que tu ferais ?”. Les formations que j’ai suivies m’ont appris que la vulnérabilité n’est pas une faiblesse
Bertrand Ballarin, qui a initié la démarche de responsabilisation chez Michelin, évoque le fait que « des dirigeants suffisamment ignorants, mais qui voudront bien donner l’impulsion […] et faire confiance à ceux qui savent, sont une condition de la responsabilisation ».
Diminution ou suppression de la hiérarchie : évacuer le territoire de la décision
On peut formuler l’hypothèse que l’autonomie et la responsabilité se développent plus facilement sur le territoire que les ma-nagers évacuent. Un dessaisissement d’une partie des prérogatives qui étaient auparavant exercées par le management serait donc nécessaire pour y parvenir. Sans être généralisable, cette tendance s’observe dans les organisations et se traduit par deux phénomènes : d’une part, la diminution du nombre de strates hiérarchiques, cette tendance pouvant aller jusqu’à la suppression de la hiérarchie intermédiaire ; d’autre part, la transformation du rôle du manager qui passe du contrôle à l’animation et au coaching (« comment puis-je t’aider ? »).
Chez SEW USOCOME, l’organisation de l’entreprise est devenue très plate depuis plusieurs années déjà. Les usines du groupe en France sont découpées en mini-usines et il n’existe plus que trois niveaux hiérarchiques : les collaborateurs, les managers des mini-usines, le directeur de l’usine (en fait, quatre si l’on inclut la direction générale du groupe). La logique décrite par Jean-Claude Reverdell, le DG, est la suivante : « Les collaborateurs sont chargés du court terme, à savoir livrer les produits commandés par les clients. Les managers s’occupent du moyen terme, en s’appuyant sur les services support. Enfin, le comité de direction traite le long terme. »
Chaque manager de mini-usine doit gérer entre 40 et 60 personnes. Ces managers sont dits « de terrain » : ils ont, bien sûr, des tâches administratives, mais ne doivent pas passer trop de temps dans leur bureau. Ils sont notamment chargés d’animer les réunions quotidiennes qui ont lieu sur chaque ligne, pour faire le point sur ce qui s’est passé la veille et sur le programme de la journée, discuter des problèmes rencon-trés et aussi transmettre les messages de la direction.
Ce point a été également souligné chez Michelin comme l’un des facteurs structurants du processus de responsabilisation mis en place. « Les horaires de travail des agents de maîtrise ont été modifiés. Ces managers ont pris leur poste dans les horaires normaux de jour (matin et après-midi). Les équipes de fabrication se sont ainsi trouvées sans manager toutes les nuits et pendant les week-ends. »23
Il faut cependant souligner que chez SEW USOCOME, l’aplatissement de la ligne hiérarchique est propre à l’organisation française du groupe et que le modèle a échoué dans sa tentative d’exportation en Allemagne comme au Brésil. « Par exemple, en Allemagne, on aime bien la hiérarchie et, dans la maison mère, il doit exister cinq ou six niveaux hiérarchiques. L’entreprise fonctionne très bien ainsi: pourquoi changerait-elle d’organisation ? » précise Jean-Claude Reverdell. Le nombre de niveaux hiérarchiques aurait-il, en définitive, moins d’impact sur l’autonomie des travailleurs que le comportement des managers ? On peut faire l’hypothèse que ce n’est pas seulement le nombre de strates hiérarchiques qui empêcherait l’autonomisation, mais aussi la distance hiérarchique, définie comme « la perception du degré d’inégalité du pouvoir entre celui qui détient le pouvoir hiérarchique et celui qui y est soumis »24. Or l’indice de distance hiérarchique (IDH) calculé pour la France (68) est largement supérieur à la moyenne mondiale25.
Pour favoriser l’autonomie, il paraîtrait donc souhaitable d’agir directement sur l’attitude et les comportements des managers. Chez SEW USOCOME, ces derniers suivent régulièrement des demi-journées de formation au sein d’un dispositif baptisé « Les Ateliers du management ». En début d’année, la direction définit les thèmes les plus pertinents et chacun s’inscrit aux ateliers qui l’intéressent : par exemple, gérer des conflits, faire grandir ses collaborateurs, piloter la génération Z, ré-impliquer des collaborateurs désimpliqués, etc. Le choix des sujets cités indique clairement que le modèle de management promu par la direction est celui de « manager coach ».
Chez Lippi, l’encadrement n’a pas été supprimé mais il est désormais coopté par les salariés. Selon Frédéric Lippi, des leaders émergent naturellement : ce sont ceux qui sont le plus à l’aise avec la nouvelle organisation, ceux qui prennent le plus d’initiatives ; ils sont rapidement identifiables et identifiés par leurs pairs. Dès lors, l’entreprise les soutient par une formation au développement personnel. « Il est clair qu’un cadre dont l’essentiel du travail consistait à établir le planning des congés, à valider des notes de frais, à décider de la formation et à résoudre des problèmes à la place des autres n’a pas sa place dans notre entreprise. Le profil de nos cadres est quelque part entre le leader, le coach et le manager. C’est un changement radical de posture, de compétences et de comportement que nous avons accompagné par un effort massif de formation entre 2014 et 2015, avec treize mille heures de formation dont huit mille cinq cents heures de développement personnel. »
Chez SORI, AE&T ou encore Groupe Voltaire, il n’y a plus du tout de hiérarchie, et parfois depuis près de vingt ans (SORI). Tous les salariés sont positionnés« en râteau ». Une telle organisation semble fonctionner dans les petites structures, mais nécessite une forte implication et disponibilité du chef d’entreprise. Chez SORI, Hervé Valliet, selon ses propres termes, vit quasiment sur place et sa porte est ouverte en permanence.
Délégation – Subsidiarité26
Délégation et subsidiarité sont deux manières de procéder à des réaménagements de responsabilité, rapprochant pouvoir de décision et de réalisation. Mais le principe de la délégation est construit sur un postulat : la décision appartient au sommet, qui la concède par exception à la base. Alors qu’avec le principe de subsidiarité, au contraire, la décision appartient à la base qui ne fait appel au niveau supérieur que par exception.
Déplacer les frontières entre exécution et décision
Évacuer le territoire de la décision est cependant insuffisant, et pourrait même se traduire chez les salariés par un sentiment d’abandon contraire à la construction de l’autonomie au travail. Pour donner de l’autonomie, il est aussi nécessaire de dessiner les contours d’une nouvelle répartition des responsabilités basée sur la délégation ou sur la subsidiarité. Les dirigeants auditionnés se sont montrés spontanément assez peu diserts sur cette question pourtant essentielle.
Pour redistribuer les responsabilités, il faut comprendre ce que les gens se sentent capables d’assumer sans en référer à leur chef, en évitant de procéder d’en haut par une décision hétéronome qui serait par nature contraire à l’objectif poursuivi. C’est ainsi qu’a procédé le groupe Michelin en transformant, pendant un an, 38 îlots de fabrication (soit à peu près 1 500 personnes dans plusieurs pays) en « laboratoires de l’autonomie ». Cela a conduit à remettre en cause la séparation stricte entre l’exécution et la résolution de problème, qui caractérise encore bien souvent les organisations, et à accorder aux agents de fabrication « l’aptitude et le droit d’agir sur la régulation de leur propre travail à mesure qu’ils résolvaient par eux-mêmes les problèmes qu’ils rencontraient »27. Ce qui a signifié concrètement opérer un transfert de compétences techniques des fonctions support vers les opérateurs de fabrication, par exemple la maintenance de premier niveau ou le contrôle qualité.
Plusieurs organisations procèdent en élargissant, dans des proportions variables, le périmètre des missions des opérateurs. Ainsi, chez Vision Systems : « Nous avons élargi les missions. Les facilitateurs sont des opérateurs et ils conservent les mêmes tâches de base mais, lorsqu’un problème apparaît, ils doivent, en plus, prendre l’initiative de le signaler. […] Cette responsabilité supplémentaire est prise en compte dans leur rémunération et elle fait l’objet d’une formation qui est elle-même rétribuée. Le facilitateur n’est pas un “chef”, mais simplement un interlocuteur privilégié pour les services support. Au début, nous avons rencontré quelques résistances : “Moi, je sais monter un sous-ensemble, mais la qualité, je n’y connais rien. C’est le travail des bureaux d’études”. Peu à peu, nous avons pu montrer par l’exemple qu’exercer cette fonction était possible et utile. »
C’est dans ce contexte de déplacement des frontières des postes que la polyvalence a parfois été évoquée et présentée sous un angle positif comme un corollaire de l’autonomie : « Les salariés deviennent plus autonomes, se montrent capables de gérer les problèmes qu’ils rencontrent et sont polyvalents au sein d’une même cellule » (Michel de Nonancourt, Alliansys). « La formation, mais aussi le partage informel des savoir-faire nous ont permis de rendre tous les salariés extrêmement polyvalents. L’un des soudeurs est également peintre et c’est lui qui règle la machine à commande numérique. Un autre soudeur est régleur presse. Dans mon tableau de compétences, personne ne figure sur une seule case » (Elisabeth Klein, CFT Industrie).
Cependant, les rapports entre polyvalence et autonomie peuvent être assez ambigus. Toutes les polyvalences ne correspondent pas à un enrichissement des tâches, ni à un accroissement de l’autonomie, comme nous le rapportons dans l’annexe (Tension n°9 : polyvalence versus enrichissement des tâches p. 116).
Confiance, droit à l’erreur, transparence
Parmi les autres ingrédients que les dirigeants interrogés affirment insuffler pour favoriser l’autonomie des équipes, les plus souvent cités sont : la confiance, le droit à l’erreur et la transparence.
Confiance. Vue par les dirigeants, la confiance ne suffit pas à créer l’autonomie mais elle en représente le socle. On pourrait dire de la confiance comme de la politesse qu’elle n’est pas en elle-même une vertu mais qu’elle est celle qui permet toutes les autres28 « Le plus important, c’est la confiance a priori, et c’est le rôle du leader que de montrer qu’il a confiance dans ses équipes. L’autonomie, c’est autre chose, ça dépend des capacités de chacun, mais aussi des circonstances. » (Frédéric Lippi). Vue du côté des salariés en revanche, la confiance se construit au fur et à mesure de la démarche d’autonomie, et renforce alors celle des dirigeants. Plusieurs dirigeants ont souligné le fait qu’avoir passé une crise importante sans recourir à des licenciements avait contribué à construire un socle de confiance sur lequel capitaliser par la suite.
Droit à l’erreur. « En cas de ratage, nous constituons un bêtisier qui nous permet de revenir sur ce qui s’est passé. Une de nos formules consiste à dire que “personne n’a jamais quitté la société avec la tête sous le bras”. Nous comptons beaucoup sur l’im plication et les suggestions du personnel, mais si les gens se sentent en danger, ils ne suggèreront rien du tout. Cela nous oblige à la cohérence. » L’entreprise a une tradition du droit à l’erreur (et du devoir de se corriger). Débloquer la parole par le droit à l’erreur permet de construire un vrai retour d’expérience, qui n’est plus biaisé par la peur de la sanction « On favorise la prise de décision. Si la décision est mauvaise, ce n’est pas grave, on apprend ! Ce qui est grave, c’est de ne pas prendre de décision. » (Landry Maillet, ABCM)
Transparence.
La transparence porte le plus souvent sur la vision et la stratégie de l’entreprise. « Pour qu’ils puissent s’approprier le projet global et la nouvelle vision de l’entreprise, toutes les informations doivent être entièrement accessibles à tous » (Alliansys). « Tous les membres de Vision Systems, depuis le PDG jusqu’aux opérateurs, connaissent la stratégie qui a été adoptée. »
La transparence peut aussi porter sur les résultats d’activité, qui sont partagés avec l’ensemble des équipes sur une base régulière pour servir d’outils de pilotage et d’aiguillons pour l’action, voire de référence objective pour le dialogue social. « […] Tous les mois, nous affichons dans toutes les usines les données du mois précédent : chiffre d’affaires, évolution des effectifs et des quantités produites, taux de service, résultats de l’entreprise. Cela permet d’éviter les bonnes ou mauvaises surprises à la fin de l’année et, lors des rencontres avec les délégués syndicaux, de discuter de choses “vraies”… » (Jean-Claude Reverdell).
En revanche, l’accès ouvert aux systèmes d’information est moins souvent évoqué, à l’exception de SORI : « Tout le monde a accès à l’ERP, et les résultats de l’entreprise sont complètements transparents indique Hervé Valliet, le PDG, qui conçoit le fonctionnement cible de son entreprise comme celui d’un «groupement d’artisans ». L’asymétrie informationnelle reste la règle dans une majorité d’entreprises.
De même, seul CFT Industrie mentionne la transparence sur les salaires : « Les salaires sont entièrement transparents. Ils vont de 1 900 euros bruts pour un opérateur à 4 300 euros pour les commerciaux. Le mien est de 3 900 euros. J’ai souhaité que la prime d’intéressement soit la même pour tous, quels que soient le poste, le salaire, l’ancienneté, etc. Par exemple, s’il y a 10 000 euros d’excédent, nous divisons cette somme par 12 (i.e. le nombre total de salariés). » (Elisabeth Klein).
Démarches participatives
Les démarches qui visent à faire participer les salariés à la vie de l’entreprise (autonomie de niveau 2) sont extrêmement populaires parmi les dirigeants qui, tous, aiment les évoquer longuement. Néanmoins, les objets et les modalités de mise en œuvre de ces démarches sont assez différentes d’une entreprise à l’autre, et n’ont de ce fait ni le même sens, ni la même portée (information, consultation, concertation, délibération, codécision). Des démarches participatives peuvent poursuivre d’autres finalités que la construction de l’autonomie : créer une culture commune, renforcer la cohésion du groupe, obtenir un consensus, donner une bonne image, améliorer un processus, etc.
Consultation.
La consultation constitue un premier niveau de participation. Entre 2011 et 2018, Adam Pack a lancé trois enquêtes de climat social, en collaboration avec la chaire Capital humain de l’université de Bordeaux, ce qui est assez exceptionnel pour une entreprise de 70 personnes. Ces enquêtes étaient cohérentes avec l’activité d’Adam, qui est une industrie de main-d’œuvre reposant sur un savoir-faire artisanal (travail du bois). Elles ont fourni à la direction des indicateurs sur les problèmes prioritaires à résoudre en fonction du niveau d’insatisfaction des salariés. Elles ont porté successivement sur des sujets tels que les conditions de travail, les salaires et l’évolution des carrières, le développement des compétences anciennes et nouvelles, la politique de fidélisation. Elles ont été conduites selon les règles de l’art : transparence de la mesure utilisée, confidentialité, restitution des résultats, mise en place de plans d’actions concrets et mesurables dans les différents domaines. C’est suite à ces enquêtes qu’ont, par exemple, été mis en place des contrats d’intéressement et un plan d’amélioration des conditions de travail. Dans ce type de démarche, les décisions appartiennent par nature à la direction.
Participation à l’amélioration continue: les « boîtes à idées ». Nous avons déjà évoqué la participation des salariés à la résolution de problème via la communication structurée que représentent les points quotidiens, hebdomadaires et mensuels (voir 3.1 lean). Dans le cadre des pratiques lean, certaines entreprises mettent aussi en place des systèmes de suggestion organisés: un nouveau nom donné aux anciennes « boîtes à idées ».
Chez SEW USOCOME, on l’appelle le SMI (système de management des idées). Il permet aux opérateurs de suggérer des améliorations sur les outils existants, qu’il s’agisse de productivité ou d’ergonomie. Les propositions sont formulées sur des cartes jaunes, bleues ou rouges : jaunes lorsqu’il s’agit de défaillances qui nécessitent l’intervention des méthodes ou de la qualité, bleues pour les améliorations pouvant être réalisées au sein de la mini-usine ou via l’intervention de la maintenance, et enfin rouge pour tous les aspects liés à la sécurité. Le manager commence par sélectionner les idées qui lui paraissent pertinentes et se charge de les mettre en œuvre. Tous les trois mois, un comité composé des managers, des directeurs d’usine et des responsables des ressources humaines, sélectionne les deux meilleures idées de chacune des trois usines du groupe en France.
Chez Bosch France, à l’usine de Mondeville, on les appelle les « idées étincelles ». Elles sont recueillies via une fonctionnalité de la plateforme de communication de Bosch, l’Active Cockpit. Il s’agit d’une application software via des écrans tactiles répartis dans toutes les unités de l’usine, de la taille d’un grand écran LED, qui permettent de traiter et de visualiser en temps réel les données de production, et de mettre en réseau des applications, la messagerie électronique et toutes sortes de fichiers. L’opérateur peut à tout moment poster dans le système une « idée étincelle ». Toutes les idées étincelles donnent lieu à des récompenses, même lorsqu’elles ne sont pas retenues. L’Active cockpit, qui fait partie de l’offre de Bosch Rexroth en solutions intelligentes pour l’usine 4.0, permet également d’animer les points journaliers de l’équipe de management de l’atelier qui ont lieu tous les matins pendant une vingtaine de minutes pour discuter du déroulement des opérations de la veille ; les opérateurs n’y sont pas systématiquement conviés.
Méthodes participatives portant sur la vision, les valeurs, la stratégie.
Chez WorldCast, les dirigeants se sont livrés en 2014 à un exercice stratégique. Il s’agissait de définir des valeurs, une stratégie et de les partager. La stratégie, affirment les deux dirigeants, n’a pas vocation à être construite par les salariés ; en revanche, elle doit être partagée, appropriée et enrichie au niveau de responsabilité de chacun. « Nous devions vraiment y aller avec tout le monde, car la période précédente avait été extrêmement douloureuse. » C’est ainsi que se met en place un dispositif participatif de partage et d’appropriation avec les deux strates que sont les cadres intermédiaires et les autres salariés. Dans les deux cas, c’est la direction générale qui communique. Deux questions sont posées : aux cadres, « qu’est-ce qu’il faut changer dans l’entreprise pour réussir la stratégie ? » ; aux autres salariés, réunis en groupes de 8 à 10 personnes, « qu’est-ce que tu penses devoir changer sur ton poste pour réussir la stratégie ? ». Les ateliers sont organisés et pas moins de cinquante idées remontent. « Contrairement à une boîte à idées, ce n’était pas n’importe quelle idée, mais des idées “dirigées” par la stratégie ». Après regroupement en grappes d’idées, les dirigeants en conservent une trentaine, avec la promesse de les financer, de les mettre en œuvre et de les évaluer. Et surtout, au-delà des idées récoltées, l’entreprise a gagné une véritable adhésion à la stratégie globale, et une adhésion individuelle aux propositions d’idées créées en groupe. Par exemple, raconte Julien Chomat, les salariés avaient majoritairement insisté pour la mise en place d’un ERP : « Du coup, même quand il y a eu des moments difficiles à la mise en route [de l’ERP], tout le monde a adhéré et mis tout en œuvre pour rechercher des solutions. » L’exercice participatif a été jugé si satisfaisant par la direction qu’il a été réédité en 2018, lors de l’actualisation du plan stratégique.
Intelligence collective.
À l’occasion d’un séminaire annuel, le groupe
Nous avons organisé pour cela une petite place de marché avec un stand pour chacun des 12 thèmes. Chaque équipe devait présenter son thème, mais aussi rendre visite aux 11 autres stands » raconte Elisabeth Klein.
Chez Adam, le déménagement qui a eu lieu en 2015 dans une usine éco-conçue de 10 000 m2 au cœur du Médoc a donné lieu à une démarche d’intelligence collective de grande ampleur. Des groupes de travail thématiques et par atelier ont poursuivi une réflexion pendant plusieurs mois. Ils ont été déterminants pour décider de l’implantation des machines. Le responsable de l’activité finition (peinture des coffrets, vernis, ponçage…), 52 ans et « trente ans de boîte », a ainsi bousculé les propositions du cabinet d’ingénierie. Il a suggéré que l’espace finition ne soit pas installé en bout de chaîne, mais soit accessible à la fin de l’usinage, du marquage ou du montage. « Nous avons retenu cette modification profonde du projet », confirme le patron JeanCharles Rinn. Le responsable de l’activité usinage, ٥١ ans, a eu carte blanche pour implanter les machines. « J’ai réuni les quatre personnes de mon équipe et leur ai demandé d’y réfléchir, en tenant compte des machines les plus utilisées, de la facilité d’accès aux stocks. C’est aux mecs que ça doit plaire ! » Les groupes de salariés ont aussi étudié la gestion des déchets, les équipements du réfectoire et des vestiaires, les horaires de travail. Ils ont, par exemple, choisi de raccourcir la pause déjeuner d’un quart d’heure pour pouvoir partir plus tôt le soir29.
Chez AE&T, depuis 2015, les règles qui gouvernent l’intelligence collective sont affichées sur tous les murs (voir photos ci-dessous) ; les salariés en ont fait leur miel et les appliquent désormais au quotidien. Parler avec intention signifie « c’est moi qui parle » et non pas « on pense que… », cela consiste aussi à éviter de porter des jugements. « Respecter le cadre », c’est respecter les quatre règles énoncées, ainsi que les règles de l’équipe locale, la loi, les règles de qualité, de sécurité et le règlement intérieur. Deux fois par an, l’entreprise organise aussi un forum ouvert pour permettre à tous de s’exprimer. Le DG, Eric Greven, s’engage à mettre en place les décisions prises.
3.2.3 Les limites de l’autonomie vues par les dirigeants
La majorité des dirigeants qui ont mis en place des démarches d’autonomisation, sollicitant la participation des salariés, constatent qu’elles ne suscitent pas toujours l’enthousiasme général et nécessitent un temps d’apprentissage.
« Quand j’ai lancé la réflexion sur notre vision, je voulais que tout le monde soit partie prenante. Je me suis vite rendu compte que, sur un terrain de jeu, il y en a toujours qui préfèrent rester sur le banc de touche. Mais parfois, au bout d’un moment à regarder ceux qui jouent, ils se disent : “Cela se passe bien, j’y vais aussi” » explique Elisabeth Klein chez CFT.
Pour Landry Maillet chez ABCM, « Le plus dur a été d’accompagner les collaborateurs qui n’y croyaient pas. Il y en a qui ont foncé tête baissée. Il y en a qui y sont allés vraiment avec le frein. Il y a des gens qui ont eu des déclics et qui ont basculé. Mais globalement, au départ, on a eu 2-3 ans avec des gens vraiment sur la défensive. On a eu aussi des gens qui ont dit : “je quitte l’entreprise”. Ce qu’il est important de souligner, c’est que dans le cadre du développement d’une entreprise vers un nouvel univers, il y a des gens qui vont y aller rapidement, il y a des gens qui ont des difficultés et qu’il faut vraiment accompagner, et il y a ceux avec lesquels on n’y arrivera pas. L’enjeu est d’accompagner chacun quel que soit son niveau de maturité, et peu importe l’orientation finale, l’idée est de respecter les valeurs de tous et sortir grandi de l’expérience ».
Selon Frédéric Lippi, « Cela ne va pas de soi pour tout le monde de devoir prendre des décisions sans en référer à quelqu’un d’autre. Pour certains, c’est douloureux, et cela se passe plus ou moins bien. »
La construction de l’autonomie au travail est un chemin escarpé.
3.3 Technologie
Si les termes « transformation numérique », « industrie du futur » ou « usine 4.0 » sont sur toutes les lèvres, il n’en demeure pas moins que les technologies présentes dans les organisations sont assez différentes les unes des autres, tout comme l’est leur degré d’appropriation. Rappelons que l’objet de cette étude n’est pas de dresser un panorama exhaustif des technologies 4.0 mais de s’interroger sur les modalités de leur implémentation favorisant une bonne appropriation de celles-ci.
3.3.1 Trois blocs de technologies qui interagissent
Systèmes d’information
Bien avant qu’on ne parle d’industrie du futur, la plupart des grands groupes et ETI disposaient déjà de systèmes d’information comme les ERP (années 1990-2000). Les PME se sont équipées plus tardivement.
D’autres progiciels ont également fait leur entrée dans les entreprises : GPAO, GMAO, CRM, PLM, MES30, etc. La difficulté consiste à interconnecter ces systèmes pour les rendre réellement efficients en interne comme en externe (par exemple via les échanges de données informatisées avec les fournisseurs pour s’assurer de la disponibilité des composants). Le vrai défi est de parvenir à synchroniser les flux physiques et les flux d’information, à l’image de ce qu’a réussi SEW USOCOME : « Nous sommes parvenus à synchroniser les flux physiques et les flux d’informations depuis l’enregistrement de la commande jusqu’à la livraison. Par exemple, une filiale suédoise nous adresse une commande émanant d’un de ses clients. Après avoir vérifié si nous avons la capacité de monter le produit souhaité dans le délai imparti, la commande du client se transforme en ordre de montage, puis traverse les différents services : réception, magasin, montage, emballage et livraison. Le suivi se fait de façon entièrement numérique, sans aucun papier. »
Ces systèmes s’appuient sur des bases de données intégrées qui nécessitent centralisation et verticalité, comme l’évoque Anne Leitzgen, la présidente de Schmidt Groupe : « Pour permettre cette collecte globale [des données], il est nécessaire de disposer d’une architecture technique conçue pour cela, qui est centralisée, intégrée. C’est notre colonne vertébrale qui nous apporte des contraintes assez fortes en matière de pilotage et de gestion des données. C’est contraignant et c’est très cher, mais on ne pourrait pas faire tout le reste si on n’avait pas cette colonne vertébrale. »31 Le paradoxe est que cette intégration centralisée et verticale passe d’abord par un « dé-silotage » de l’organisation pour permettre la collecte de l’ensemble des données des secteurs de l’entreprise.
Technologies collaboratives
Orthogonales aux premières, les technologies du web et des réseaux sociaux se caractérisent au contraire par la mise en relation des individus sans aucune prescription préalable, favorisant ainsi l’horizontalité et la transparence. La coexistence de ces deux philosophies n’est pas toujours évidente dans les entreprises. En témoigne, par exemple, Jacques Aschenbroich, le patron de Valeo : « Les technologies digitales recouvrent deux sujets différents […]. Ici à Valeo, on a un ERP exceptionnel. […] C’est un outil fabuleux en termes de contrôle et de gestion, un outil absolument indispensable aujourd’hui. Ensuite, il y a tous les outils de communication. On a été la première entreprise française à quitter les outils bureautiques classiques de type Microsoft pour utiliser les outils Google (gmail, docs…). Ce sont des outils de communication interne et de mise en place de réseaux fabuleux, mais je suis en revanche très réticent sur l’utilisation des réseaux sociaux comme outils parce que nous développons des produits très en avance de phase pour tous nos clients et le contrôle du secret industriel est absolument clé et ne supporte aucun écart. »32
Que ce soit dans le champ de la relation client ou pour promouvoir leur marque employeur ou encore pour flexibiliser l’organisation interne, ces technologies plus récentes occupent aujourd’hui une grande place dans les entreprises. L’entreprise Lippi est une adepte des outils Google du fait de leur facilité à partager les informations tout en laissant les clés à la discrétion de l’utilisateur : « Ce qui nous a principalement intéressés chez Google, c’est le cloud, le drive. Que la donnée soit à un endroit mais que par un jeu de permissions, à la main de l’utilisateur, on puisse ou non travailler à plusieurs, ouvrir à l’extérieur, c’est vraiment très puissant.»33
Automatisation et robotisation
C’est l’étape la plus récente du mouvement de numérisation et celle qui fait l’objet du « bruit médiatique » : robots, cobots, exosquelettes, internet des objets, fabrication additive, réalité augmentée, etc. Sans céder inconsidérément aux projections futuristes, force est de constater que certaines de ces solutions entrent dans les ateliers, y compris les plus petits, même si ce n’est pas encore de façon massive.
Si de nombreuses entreprises industrielles possédaient depuis longtemps des machines à commande numérique, elles tendent aujourd’hui à renouveler en profondeur leurs équipements. La justification en est parfaitement résumée par Michel de Nonancourt, président d’Alliansys, un sous-traitant électronique : « Plus que le coût de la main-d’œuvre, c’est clairement le caractère obsolète des machines qui pose problème. L’automatisation et le remplacement des machines existantes sont d’autant plus indispensables que nous assistons à la multiplication des composants de très petite taille, dont certains sont presque invisibles à l’œil nu et ne peuvent pas être posés à la main. Enfin, pour être compétitifs, nous devons également automatiser le plus grand nombre possible de tâches en amont et en aval de la production. » Une tendance très forte pour des secteurs déjà fortement automatisés tels que l’électronique ou l’automobile, et qui se diffuse progressivement aux autres secteurs.
3.3.2 Observations : organisation du travail de production dans l’usine digitalisée
Comment s’organise le travail dans les établissements où ces trois types de technologies se combinent et font « système » ?
Lean et technologies
La couche de technologies 4.0 vient se greffer sur une organisation existante. Dans une petite entreprise comme CFT Industrie qui n’avait quasiment pas de procédures, l’arrivée du premier robot de soudure a produit une révolution copernicienne, et c’est l’ensemble de l’organisation de l’entreprise qui s’en est trouvé modifié : le lean a été introduit, puis la norme de qualité ISO et tous les progiciels de gestion.
Dans l’autre sens, dans une entreprise très mature comme Bosch, la transformation digitale s’est articulée sur le système Lean de Bosch, le Bosch Production System. Aux dires des dirigeants, l’industrie 4.0 est ce qui permet de mieux faire fonctionner le Bosch Production System, le digital permettant au lean de déployer tout son potentiel : la synchronisation des flux, le zéro papier, l’approvisionnement en juste à temps, la réduction des risques de rupture de charge, sont ainsi « augmentés » par les technologies, là où les points d’articulation du système demeuraient auparavant fragiles.
À l’usine de Mondeville de Bosch, l’automatisation de l’approvisionnement des lignes a constitué la pierre fondatrice du système. Tous les produits qui entrent dans l’usine portent aujourd’hui une étiquette normalisée par Bosch (MAT LABEL), partie intégrante du cahier des charges transmis aux fournisseurs. Le produit entrant est scanné et « entré » dans l’ERP. L’étiquette permet ensuite de suivre la pièce, le lot et sa provenance tout au long de la chaîne de fabrication. Le magasin de stockage est entièrement automatisé, les pièces sont placées dans des paniers métalliques qui naviguent par des colonnes d’ascenseurs (MAT LIFTS) montant jusqu’au plafond. Quand une pièce est appelée, grâce au Pocket PC du magasinier (demain, ce sera une tablette), elle se présente automatiquement devant lui, et le même Pocket PC la reconnaît avec une certitude absolue. Suite à cette automatisation, l’effectif des magasiniers a été fortement réduit. Ils ne sont plus que six aujourd’hui à alimenter les lignes et sont « polyvalents » : magasiniers et distributeurs.
Pour prendre la mesure des changements induits par la numérisation de l’organisation industrielle, il faut aussi écouter Jean-Claude Reverdell chez SEW USOCOME décrire le fonctionnement de la nouvelle usine 4.0 de Brumath. Ce site effectue le montage des commandes dont les composants sont fournis par les autres usines du groupe : « Auparavant, les collaborateurs chargés de la préparation de commande, ou picking, se rendaient au magasin, cherchaient les pièces qu’ils devaient transporter, les scannaient pour les déduire du stock, les plaçaient sur les plateaux de montage, puis chargeaient les différents plateaux sur un chariot et conduisaient celui-ci à la ligne de montage. Aujourd’hui, des convoyeurs déplacent les composants depuis le magasin automatisé jusqu’aux stations de picking. Lorsque la personne chargée du picking prélève les pièces dans les bacs pour les poser sur les plateaux, elle effectue une partie de l’assemblage en temps masqué, ce qui accélère les opérations ultérieures de montage. Ceci n’est possible que parce que les pièces arrivent dans un ordre précis, piloté par un séquenceur. L’usine est équipée de sept stations de picking, qui permettent de prélever 40 000 composants par jour, soit un prélèvement toutes les vingt secondes environ. Le transport des pièces vers les lignes de montage est assuré par 37 AGV, qui effectuent 1 100 trajets quotidiens, soit 440 kilomètres par jour, ce qui permet de réduire fortement la pénibilité pour les collaborateurs. Tous ces équipements ont été développés en interne et avec notre maison mère. Les plateaux sont identifiés par des codes-barres. Lorsqu’ils arrivent devant le monteur, celui-ci voit s’afficher sur son écran toutes les informations dont il a besoin pour réaliser la commande. »
Critique.
Un récent article de L’Usine nouvelle décrivait ainsi une usine de Panasonic au Japon : « [L’usine] est munie au plafond de 40 balises Beacon34 pour la géolocalisation des opérateurs, et de 20 caméras. Il devient ainsi possible de voir en temps réel tout ce qui se passe dans l’atelier : les déplacements des opérateurs, les actions qu’ils ont sur les machines, le fonctionnement des équipements, etc. Les données sont analysées pour déterminer les mouvements à faible valeur ajoutée, les pertes de temps ou encore les difficultés d’exécution. Autant d’enseignements utilisés pour optimiser la configuration des machines, l’ordonnancement des opérations, les instructions de fabrications, etc. »35 Le système semble entièrement fondé sur l’exploitation des données digitales recueillies. Le Gemba, qui signifie en japonais « le vrai lieu où se passent les choses » et qui consiste pour les managers à aller sur le terrain voir ce qui s’y passe réellement, semble ainsi détourné au profit d’un Gemba numérique à distance. Il en est de même du Kaizen – l’amélioration continue – qui passe traditionnellement par le dialogue avec les personnes ; dans cet exemple, il semble avoir sombré corps et biens. Ces pratiques se rapprochent du voice picking d’Amazon36, continue l’article : « Les opérateurs reçoivent leurs instructions de fabrication de façon vocale, et ils rendent comptent de l’état des machines de façon vocale. […] Lors de la vérification de l’état des équipements, des réglages ou de reconfiguration des lignes, ils se contentent de cocher des cases ou répondre par oui ou non à des questions sur l’écran de la tablette. »37
Au moment même où l’autonomie des personnes est mise en valeur comme facteur d’agilité des entreprises, elle pourrait se voir complètement évacuée par un nouvel usage des technologies en vue de la détermination et du contrôle du travail. Que restera-t-il alors du lean « apprentissage » ? Quelles marges de manœuvre restera-t-il aux opérateurs ?
Valeur sociale des technologies : un travail moins pénible et plus intéressant ?
Les dirigeants mettent en avant la valeur sociale de ces technologies, c’est-à-dire l’amélioration des conditions de travail des salariés, la réduction de la pénibilité et la pré vention des TMS . « Avant l’arrivée du robot, toutes les soudures étaient effectuées à la main, ce qui pouvait être pénible, par exemple lorsqu’un opérateur devait réaliser au cours de sa journée 60 chariots de 7 kilos chacun. La robotisation a eu un impact immédiat sur la réduction des TMS et, plus généralement, sur l’amélioration des conditions de travail. Nous avons également apporté d’autres améliorations, par exemple en installant une ventouse derrière le robot pour ne plus avoir à soulever les objets lors de leur mise en place. Nous demandons régulièrement à la médecine du travail de réa liser des diagnostics sur le bruit, les TMS ainsi que les fumées, et nous travaillons en partenariat avec la caisse régionale d’assurance maladie sur de très nombreuses petites actions qui ne coûtent pas cher et peuvent vraiment améliorer la vie quotidienne. Petit à petit, les mesures prises en faveur de la santé et de la sécurité ont changé l’état d’esprit dans l’entreprise » (Elisabeth Klein, CFT Industrie).
Critique. Cette diminution de la pénibilité qui découlerait « par principe » de l’automatisation est fortement contestée par le s ergonomes. Ceux-ci considèrent que la pénibilité et les TMS ont des causes multifactorielles et que leur prévention ne saurait se réduire au soulagement des contraintes biomécaniques, condition nécessaire mais non suffisante. «
; les dimensions psychosociales, les possibilités pour les opérateurs d’avoir des marges de manœuvre individuelles et collectives, l’usage que l’organisation fera de la technologie, ou encore les modalités de conduite du changement sont des éléments tout aussi nécessaires que la technologie pour préserver la santé au travail. »38
Les dirigeants insistent également sur le fait que le travail des opérateurs, « libérés » des tâches les plus ingrates et répétitives, est devenu plus riche et plus intéressant, ce qui semble être parfois le cas, comme nous l’avons vu avec l’exemple de SORI et de ses opérateurs-programmeurs (chapitre ١). Cependant, il paraît hasardeux de généraliser trop vite : il est en effet permis de s’interroger sur cette augmentation de « l’intérêt du travail » pour ceux dont la tâche à l’assemblage ou au montage est entièrement cadrée par des instructions fournies sur des écrans
Associer les personnels à l’introduction des technologies devient alors un garde-fou pour faciliter leur appropriation par les équipes, mais aussi pour s’assurer de leur valeur sociale.
Associer les personnels à l’introduction des technologies
Des changements d’une telle ampleur en gendrent beaucoup d’angoisse au sein des équipes, et en particulier dans les équipes de production directement concernées. Il y a bien entendu la crainte de perdre son emploi et d’être remplacé par un robot, mais aussi l’inquiétude face au changement et la peur de devenir « incompétent ».
Pour répondre à ces inquiétudes et réussir les transformations, certaines entreprises développent des méthodes associant étroitement les opérateurs aux choix technologiques qui les concernent.
Comme le dit Frédéric Lippi avec bon sens, « dès l’instant où ce sont les employés qui ont décidé d’entrer une nouvelle technologie, il n’y a pas de problème. C’est choisi par le corps social. » Plus encore, il s’agit là d’une manière d’agir directement sur la qualité du travail.
Cette démarche de bon sens, Elisabeth Klein l’a appliquée pour l’installation de son premier robot soudeur : « Je me suis occupée du montage financier de l’opération, mais je ne suis pas du tout intervenue dans le choix de l’équipement. Ce sont deux des soudeurs qui ont été désignés comme porteurs du projet. Ils sont allés rencontrer les fournisseurs et ont travaillé sur le cahier des charges, en se faisant aider par [un expert]. Cette implication des opérateurs eux-mêmes a grandement facilité l’intégration du robot. Aujourd’hui, c’est l’un des deux soudeurs qui s’occupe de son réglage
L’association des personnels peut intervenir à plusieurs étapes : dans la mise au point du cahier des charges, dans le choix de l’équipement, dans l’adaptation et le réglage des machines, ou dans la révision du processus de production, en collaboration avec les autres spécialistes des processus. Chez SORI (voir chapitre 1) ou chez SEW USOCOME (voir chapitre 4), les personnels de production sont systématiquement associés à la conception des cellules ou des lignes à l’occasion de leur modernisation.
Reste un point aveugle : l’ingénierie de conception des produits demeure, elle, largement coupée du travail de production ; elle n’intègre que peu le paramètre du travail « réel » de ceux qui seront chargés de monter les produits. C’est un peu comme si Ikea créait ses meubles sans prendre en compte l’expérience de montage réelle de ses clients (parfois, on peut se le demander !). Chez Thales, Cécile Roche, qui est aussi en charge d’appliquer le lean à l’ingénierie de conception, indique qu’effectivement, sa prochaine étape sera d’accentuer l’articulation entre ingénierie et production. Elle évoque une approche intéressante sur ce point : le slow build qui consiste à filmer un opérateur en train de monter un prototype, afin d’en tirer des enseignements pour la définition de la gamme. À une toute autre échelle bien sûr, la PME SORI témoigne que de telles collaborations sont possibles : ici, le bureau d’études est placé au cœur de l’atelier ; il est situé à côté de la salle des ordinateurs où les opérateurs programment à distance les machines et les robots de fabrication. Le bureau d’études prend en compte dès la conception la façon dont le produit sera fabriqué en FAO : « Il vient nous voir, et nous consulte pour voir ce qui est vraiment réalisable ». À quand une approche « design » appliquée au travail de l’opérateur ? Cette proposition, que nous appelons « le design du travail », fait l’objet de la dernière partie de cette étude.
3.4 Articulation entre autonomie, lean et technologie : le modèle CALT
En partant de l’observation de trois entreprises de taille différente qui ont articulé lean, autonomie et technologie, nous pouvons dessiner un chemin de progrès permettant de combiner valorisation du travail humain, modernisation de l’outil de production et performance pour l’entreprise : une PME, Lippi ; un grand groupe, Michelin ; une ETI, SEW USOCOME.
3.4.1 Lippi
Chez Lippi, la transition entre la génération précédente et celle de Frédéric et Julien s’effectue progressivement à partir de 2003. Dès 2003, l’entreprise développe une démarche lean avec un objectif à moyen terme de flux tiré-tendu mais, après une phase d’amélioration, la performance industrielle retombe. Des formations massives au lean sont alors déployées dans l’entreprise, puis un système de pilotage visuel est mis en place. En 2008, coup d’arrêt brutal du marché. Il est alors décidé de former l’ensemble des salariés aux usages et codes culturels de l’Internet et des réseaux sociaux. Ces outils et leurs pratiques induites contribuent à décloisonner l’entreprise à tous les niveaux, et à donner une place nouvelle et centrale au client. La démarche d’autonomie s’est accélérée à ce moment-là. Enfin en 2011, l’entreprise constate que la performance s’est améliorée au niveau local, mais que de gros progrès restent à faire au niveau global. Un processus de vision partagée est alors lancé. Un « désir commun » et une stratégie sont co-construits avec les salariés. En outre, une nouvelle organisation émerge de ce processus, avec la constitution de petites équipes autonomes. Aujourd’hui, les technologies de fabrication sont choisies par les équipes. L’appropriation est bonne et le déploiement efficace39. Chez Lippi, le lean a précédé la démarche d’autonomie, et le couplage des deux assure désormais une assise solide à l’appropriation du changement technologique.
3.4.2 Michelin
Michelin a une tradition ancienne de respect des personnes et d’« idées de progrès », visant à associer les exécutants à la résolution de problèmes, deux notions fortes dans la culture « patronat chrétien » de la famille Michelin. Une des maximes favorites d’Édouard Michelin, l’aîné, était que « ceux qui font savent précisément ce qu’ils font. »
Pourtant lorsque le lean est déployé dans l’entreprise dans les années 2000, ce substrat culturel ne se traduit pas par une autonomie réelle sur le terrain. Comme beaucoup d’entreprises, Michelin adapte le système Toyota, ce qui aboutit au Michelin Manufacturing Way (MMW). La productivité augmente fortement, mais assez rapidement la démotivation apparaît. Les ouvriers et la maîtrise se sentent pris dans un étau de contraintes, et le font savoir. Le groupe décide alors de lancer un projet pour responsabiliser les acteurs de l’entreprise, en partant du bas vers le haut de la hiérarchie. Bertrand Ballarin, chargé du projet, propose de tester l’idée avec trente-huit îlots de production volontaires dans dix-huit usines (sur 68 dans 17 pays). La première étape consiste à consulter les ouvriers de ces îlots démonstrateurs, en leur demandant de répondre à une question : « De quoi seriez-vous capables, en termes de décision, sans intervention des agents de maîtrise, en termes de résolution de problèmes, sans dépendre des maintenanciers ni des régleurs, techniciens et autres organisateurs industriels? Et à quelles conditions ? ». Mille cinq cents personnes s’investissent dans cette démarche. Le but n’est pas de dresser un catalogue de « bonnes pratiques », mais d’évaluer le niveau d’autonomie auquel peut parvenir un îlot de fabrication ordinaire. Cette phase produit des résultats convaincants. Au bout de douze mois, cinq sites reçoivent pour mission de voir comment il est possible de généraliser les expériences des îlots démonstrateurs, de faire évoluer le fonctionnement des structures d’appui (méthodes, relations entre les niveaux hiérarchiques, etc.) et d’imaginer de nouveaux principes de direction, mais en veillant à ne pas en faire un projet avec un déploiement jalonné et piloté par un sentiment d’urgence. L’idée est plutôt qu’il avancera par propagation naturelle. L’articulation entre le MMW et la démarche d’autonomie a été formalisée dans un nouveau système de management : le Management Autonome de la Performance et du Progrès (MAPP)40
Chez Michelin, la démarche d’autonomie a été perçue comme nécessaire pour contrebalancer la rigidification des procédures résultant d’une stricte application du lean. Selon Bertrand Ballarin, la première vague de digitalisation avait mis en place un instrument de surveillance de tous et de chacun. L’enjeu de la nouvelle vague de numérisation est précisément d’en faire ce qu’elle peut être : un instrument qui met ensemble les intelligences, les « maille », et en libère les flux. La suite de l’histoire reste à écrire.
3.4.3 SEW USOCOME
SEW USOCOME est une entreprise familiale allemande d’envergure internationale, disposant de trois usines en France. La démarche organisationnelle de SEW est une fusée à trois étages.
Premier étage de la fusée, la démarche d’autonomie des salariés et des équipes, initiée par Michel Munzenhuter41, l’ancien dirigeant, sous le nom de Perfambiance, contraction des deux mots performance et ambiance. Celui-ci a importé et adapté le modèle développé par Jean-François Zobrist chez FAVI, fait de mini-usines travaillant en autonomie. L’entreprise dispose d’une vraie tradition visant l’implication, l’autonomie des collaborateurs et la construction d’une bonne ambiance au travail.
Ensuite, l’introduction du toyotisme en 1998 avec un Sensei japonais a permis d’adopter une philosophie du lean orientée dès le départ vers la participation des opérateurs. Cette orientation anti-taylorienne et le fait qu’elle ait été adoptée facilement s’expliquent par l’existence préalable de la démarche d’autonomie, qui présupposait dès l’origine une vision respectueuse du savoir des opérateurs.
Enfin, en 2008, la crise frappe de plein fouet SEW USOCOME et conduit à une baisse d’activité de 20 %. Plutôt que de licencier, l’entreprise décide de réorienter certains salariés vers la mise en place d’une équipe interne dédiée à la conception des lignes de production, dirigée par Philippe Klein, qui était déjà en charge du déploiement du lean dans l’entreprise. Nous reviendrons en détail dans le chapitre suivant sur cette démarche originale qui nous paraît être un exemple abouti de ce que pourrait être le design du travail en production. Elle a permis d’articuler efficacement le lean et l’introduction des technologies de l’industrie 4.0, tout en impliquant fortement les opérateurs. Cette démarche s’est révélée déterminante lors du projet de construction de la nouvelle usine 4.0 de Brumath qui assure le montage des produits. Le projet poursuivait l’objectif d’améliorer la compétitivité des usines françaises en mettant en œuvre les concepts de l’industrie 4.0 (synchroniser les flux physiques et les flux d’informations, développer des solutions de robotique et de « transitique » propres, impliquer toutes les équipes, des opérateurs aux ingénieurs, pour repenser la collaboration homme-machine).
SEW USOCOME a donc commencé par une démarche d’autonomie, puis déployé le lean, et enfin développé une capacité de conception des lignes de fabrication en interne permettant ainsi une appropriation efficace des technologies. Chacun des trois étages, construits sur 10 ans, assure des fondations solides pour l’étage suivant. Ils se complètent pour former un tout homogène.
3.4.4 Le modèle CALT (Confiance-Autonomie-Lean-Technologie)
La juxtaposition des parcours de ces trois entreprises est révélatrice. Lippi et Michelin ont commencé par le déploiement du lean, mais après des gains de performance rapides, un essoufflement de la démarche et une démotivation sont apparus dans les deux entreprises. Une démarche d’autonomie a alors été initiée pour contrer les effets négatifs du lean, ce qui a permis de rendre durables les gains de performance. Dans le cas de SEW USOCOME, la séquence autonomie-lean adoptée dès le départ a assuré une base solide pour la performance. Il nous semble donc que le bon ordre serait de commencer par le déploiement de l’autonomie qui donne une assise solide au lean. Pour les trois entreprises, le couple autonomie-lean a permis ensuite une bonne appropriation des technologies.
Cette articulation renvoie aux leçons de Takehiko Harada, ancien président de Toyota Taïwan, qui a passé quarante ans à mettre en œuvre le système de production Toyota (TPS) sous la direction de Taiichi Ohno42. Harada demandait toujours à ses managers de retirer leur casquette de contrôle (control hat) pour mettre à la place leur casquette de : « Je rends le travail facile à mes équipes […]. Et il concluait ainsi : « J’en suis venu à comprendre que le TPS ne fonctionne pas très bien avec le mode de management traditionnel dans lequel on reçoit des ordres de personnes placées plus haut dans la hiérarchie. »43
La place de la confiance est essentielle dans ce modèle. Elle irrigue l’interaction dynamique entre les éléments du triptyque autonomie-lean-technologie. Si le démarrage d’une démarche d’autonomie est souvent un pari sur la confiance que prennent les dirigeants de l’entreprise, cette confiance (des dirigeants, des salariés et entre dirigeants et salariés) se construit tout au long du déploiement de la démarche.
Le modèle CALT synthétise cette approche et dessine un chemin de performance, respectueux des hommes et de leur travail (voir figure 3.4). Travailler sur l’autonomie des personnes constitue le socle qui permet de fonder, dès le départ, un lean authentique faisant place à la participation active des opérateurs. Ces deux strates permettent une acceptation et une appropriation plus efficaces des nouvelles technologies par ceux qui vont les mettre en œuvre. Cette dé marche construit de la confiance à toutes les étapes et celle-ci vient, à son tour, renforcer chacune des briques ainsi mises en place. Ce type de démarche est à la base d’un concept plus global que nous appelons le design du travail.
- 1. « La culture est la manière dont on travaille chez nous. » John Kotter, Conduire le changement, feuille de route en 8 étapes , chapitre 1, Pearson, 2015.
- 2. Cité in Deshayes Christophe, La transformation numérique et les patrons , Les Docs de La Fabrique, Presses des Mines, 2019, p. 124.
- 3. « Lean » est cité 33 fois et « excellence opérationnelle », 6 fois, dans le récent Guide des technologies de l’industrie du futur , Alliance Industrie du futur, mars 2018.
- 4. L’enquête du CEE (Valeyre, 2006) comparant les conditions de travail dans l’Union Européenne montre que les salariés travaillant dans des configurations lean ont déclaré des troubles musculo-squelletiques et psychosociaux, un accroissement de la durée et amplitude de travail, une plus grande flexibilité des horaires et des cadences plus élevées, beaucoup plus souvent que ceux encore exposés aux modalités tayloriennes du travail.
- 5. Bourgeois Fabrice, « Que fait l’ergonomie que le lean ne sait / ne veut pas voir ? », Activités , octobre 2012.
- 6. Dares, « Quelles sont les évolutions récentes des conditions de travail et des risques psychosociaux ? », Dares Analyses , décembre 2017
- 7. Bertrand Ballarin, « La responsabilisation appliquée à Michelin », in Bourdu et al., Le travail en mouvement , Presses des Mines, 2019.
- 8. Dispositif DQT – Dialogue sur la qualité du travail, développé par l’équipe d’Yves Clot du Cnam.
- 9. James Womack, Daniel Jones, Daniel Roos, The Machine that Changed the World, Harper, 1991.
- 10. Michel Sailly, Démocratiser le travail, Un nouveau regard sur le lean management , Editions de l’Atelier, 2017
- 11. « Maître » au sens des arts martiaux. Dans le monde du lean, le Sensei est celui qui emmène un cadre dirigeant sur le terrain et lui « apprend à voir ». Comme un maître spirituel, le Sensei montre la voie plus qu’il n’explique.
- 12. Dont Petit guide Lean , L’Harmattan, 2016, Le Lean en question s, L’Harmattan, 2016 et Lean en Ingénierie, Guide de Voyage , L’Harmattan 201
- 13. Michaël Ballé, La stratégie Lean , Eyrolles, 2018.
- 14. Marque déposée par le cabinet conseil POP.
- 15. Le VSM est un outil fondamental dans une démarche Lean. Il permet de visualiser les différents flux au sein d’une production (matière et information), de mettre en avant les tâches à valeur ajoutée et d’identifier les sources de gaspillages, afin d’améliorer l’état existant. Il est bon d’y incorporer l’approvisionnement en amont et la livraison client en aval.
- 16. Le Guide des technologies de l’industrie du futur , Alliance Industrie du futur, mars 2018, 186 pages.
- 17. Team of Teams , Général McChrystal, Portfolio Penguin, 2015.
- 18. Martin Richer, « Autonomie au travail, la France a tout faux ! », Blog Management & RSE, 15 juin 2016.
- 19. Colloque de Cerisy, Bourdu et al., Le travail en mouvement , Presses des Mines, 2019.
- 20. E. Boudu, M.-M. Péretié, M. Richer, La qualité de vie au travail : un levier de compétitivité , La Fabrique de l’industrie, Anact-Aract, Terra Nova, Presses des Mines, 2016, pp. 136-138.
- 21. Ce niveau « politique » n’est pas abordé pour la bonne raison qu’aucun dirigeant ne l’a évoqué.
- 22. Voir l’étude « Autonomie et responsabilité dans les organisations » de la Chaire FIT2 , à paraître en 2020.
- 23. Bertrand Ballarin, op. cit.
- 24. Cf. les travaux de Geert Hofstede, cité in Bourdu et al., op cit., pp. 140-142.
- 25. Ibid.
- 26. Ce développement est emprunté à Gilles Verrier, « Le principe de subsidiarité : une clé », RH Info , 17/08/2017. Consulté le 21 février 2019.
- 27. Betrand Ballarin, op. cit.
- 28. La politesse in André Comte-Sponville, Petit traité des grandes vertus , PUF, 1995.
- 29. Ce développement sur le déménagement d’Adam est issu de L’Usine nouvelle , janvier 2016.
- 30. Gestion de la production assistée par ordinateur ; Gestion de maintenance assistée par ordinateur ; Customer relationship management ; Product lifecycle management ; Manufacturing execution system.
- 31. Cité in Christophe Deshayes, La transformation numérique et les patrons , Les Docs de La Fabrique, Presses des Mines, avril 2019.
- 32. Cité in Christophe Deshayes, ibid .
- 33. Ibid.
- 34. Boîtier physique qui utilise la connexion Bluetooth.
- 35. https://www.usinenouvelle.com/article/comment-panasonic-reinvente-le-kaizen-pour-creer-son-usine-modele-de-l-industrie-du-
futur.N764389 - 36. http://www.wk-rh.fr/actualites/detail/83302/voice-picking-mon-chef-est-dans-le-casque.html et aussi « Chaque nuit, le pickeur courra son semi-marathon, conscient de la nécessité de faire une belle performance, voire de battre son record, sous le contrôle vigilant et constant des leads (contremaîtres), planqués derrière des écrans : ils calculent en temps réel la cadence de chacun des mouvements des ouvriers, produisent du ratio et admonestent dès qu’un fléchissement est enregistré… », Jean-Baptiste Malet, En Amazonie, Infiltré dans le « meilleur des mondes », Fayard, 2013.
- 37. Usine nouvelle, op. cit.
- 38. Barcellini Flore, « Industrie du futur : quelle place pour le travail et ses transformations ? » in Bourdu et al., Le travail en mouvement , Presses des Mines, 2019.
- 39. Frédéric Lippi dans les 2 comptes-rendus cités en référence et Julien Lippi, interview RCF, https://rcf.fr/culture/lippi-faire-confiance-et-organiser-la-decision-au-plus-pres-du-terrain
- 40. Bertrand Ballarin, compte-rendu du séminaire Vie des Affaires de l’Ecole de Paris du Management, 3 février 2017, et Bourdu et al., Le travail en mouvement , Presses des Mines, 2019.
- 41. Ancien directeur technique, puis directeur général de SEW USOCOME France, et inspirateur du concept de Perfambiance. Il est l’auteur avec Eric Lemaire de L’Entreprise qui libère les énergies : le management Perfambiance , Editions du Signe, 2016.
- 42. Takehiko Harada, Management Lessons from Taiichi Ohno : What Every Leader Can Learn from the Man Who Invented the Toyota Production System , McGraw-Hill, 2015, cité in https://thehypertextual.com/2016/04/26/15-lecons-de-management-de-taiichi-ohnolessons/
- 43. Ibid.
Le design du travail
Le modèle CALT articule des ingrédients permettant d’assurer à la fois une réponse aux besoins psychologiques des salariés, une bonne appropriation des technologies et une performance globale de l’entreprise satisfaisante. Sur cette base, nous souhaitons mettre en débat la notion de « design du travail »1, concept plus global qui renverse la perspective en plaçant le travailleur comme client de l’organisation du travail.
4.1 La « pensée design » pour changer de regard sur le travail
« Le sujet n’est pas l’objet, c’est l’Homme » disait Charlotte Perriand, collaboratrice et amie de Le Corbusier2. De même, la fonction de production ne consiste pas qu’à fabriquer des objets ou à rendre des services, mais avant tout à satisfaire les besoins des hommes en tant que consommateurs et producteurs (travailleurs). En partant de ce postulat, la « pensée design » nous permet de regarder autrement le travail et son organisation.
Les définitions du design sont nombreuses, mais on y retrouve toujours le client, les usages, la conception, l’ergonomie, les interfaces, l’aspect visuel. Généralement associée à la conception de produits ou de services, la « pensée design » est un état d’esprit qui peut, sous certaines conditions, être aussi utilisé pour produire une réflexion sur le travail.
Il est important ici de distinguer le design et le design thinking. Le design thinking est une méthode pour résoudre des problèmes de manière itérative, par la collecte de données et la progression par essais et erreurs. Le design est une attitude orientée sur les usages, avant même d’être un métier. Sollicité par une grande organisation pyramidale pour former son top management au design thinking, Dominique Sciamma, directeur de l’école de design Strate, indiquait d’ailleurs : « Nous avons formé des centaines de senior managers au design tout court, de manière à remettre l’utilisateur, autrement dit les collaborateurs, les clients et les partenaires, au centre des préoccupations. »3
Avant même de parler de telle ou telle méthode agile, la pensée design est une posture mentale qui permet de revisiter l’ensemble de l’organisation sous l’angle de « l’expérience utilisateur » au sens large. Elle engage un processus qui repose sur l’observation, le dialogue avec les différentes parties prenantes et sur la capacité à reformuler plusieurs fois le problème à résoudre tel qu’il a été initialement posé. « De par sa nature intrinsèquement centrée sur l’homme, la pensée design […] nous invite à nous servir de notre empathie et de notre compréhension des autres pour concevoir des expériences créatrices d’implication et de participation actives » précise Tim Brown, créateur de l’agence IDEO et auteur de L’Esprit Design4.
Appliquer la pensée design au travail conduit à un déplacement, voire à un renversement de la notion de client. Le client du travail, de sa conception et de son organisation, ce n’est pas que le client final, mais aussi celui qui réalise le travail. Cela implique que l’objet de l’organisation ne peut pas être la seule satisfaction du client final (usages, coût, qualité, délai), mais que ceux qui réalisent le produit doivent aussi être considérés comme clients du processus de conception du travail de production. Il ne s’agit pas de choisir entre « customer-centric » ou « employee first »5, mais bien de tenir les deux en même temps dans une tension dynamique.
En considérant l’homme au travail comme un client (celui qui subvient à nos besoins, qui nous fait vivre), on change de regard sur la contribution du travailleur qui cesse d’être une simple utilité concourant au processus productif. Fini le travailleur invisible, caché dans les ateliers de l’usine, dans les cuisines du restaurant, sur un plateau de centre d’appel, dans un entrepôt logistique ou dans une « ferme à clic ». Si le travailleur est considéré comme client du processus de conception du travail, alors le processus doit être pensé dans son intérêt aussi et co-conçu avec sa participation, au même titre qu’un produit ou service est co-conçu avec le client final (ou a minima en le prenant en compte). Sa part dans le processus est ainsi valorisée et « dévoilée » (au sens des sociologues) comme l’un des vecteurs de la valeur créée pour le client final. Le travail invisible6 est ainsi rendu visible.
En rendant visible à tous ce qui se déroule habituellement dans les coulisses de l’entreprise, un tel changement peut participer de façon très puissante à résoudre la crise des représentations du travail7.
Si l’expression « design du travail » est peu utilisée en France, elle peut être rapprochée de notions plus usitées dans le monde anglo-saxon, particulièrement aux États-Unis, telles que le job design ou work design8. Couvrant un domaine très vaste, elles se réfèrent à la fois aux caractéristiques d’un poste, à la structure des tâches et activités, à leur organisation et à leur articulation par rapport aux autres activités au sein d’une équipe. Dans cette approche, l’accent est mis sur la motivation, l’engagement et la satisfaction des salariés, ainsi que sur la réduction de l’absentéisme, la productivité et les capacités d’apprentissage. Le job design tient compte des caractéristiques personnelles du salarié. Notre approche du design du travail est davantage centrée sur la conception du contenu du travail (définition du poste de travail, du standard, de la gamme, choix et implémentations des technologies et des façons d’interagir avec elles, etc.). Dans les deux cas, l’emploi du mot « design » est justifié par l’orientation mise sur la satisfaction des besoins du salarié.
4.2 Le design du travail, pourquoi ?
Pourquoi considérer le travailleur comme un usager, comme un client ? Pourquoi le mettre au cœur du processus de conception du travail ? Des raisons locales liées à l’efficacité du processus de production, et des raisons globales ou sociétales, militent pour une telle approche.
Les raisons locales « L’intérêt de faire participer les opérateurs à l’élaboration d’un nouvel outil est non seulement d’optimiser ce dernier, mais aussi de faciliter son acceptation » (JC Reverdell, SEW USOCOME). Impliquer les opérateurs dans la définition de leur propre travail permet de réduire la fracture entre travail prescrit et travail réel. C’est la meilleure manière de faire entrer l’expérience terrain de l’opérateur dans la prescription. Participer aux modalités d’implémentation d’une nouvelle technologie, voire à la décision de son introduction, assure une bonne appropriation de celle-ci. C’est aussi une occasion d’orienter réellement le lean vers une méthode d’apprentissage pour développer les personnes.
Pour ce qui concerne les raisons sociétales, Pierre-Marie Gaillot, pilote du plateau Industrie du futur du Cetim, constate qu’avec la montée du niveau d’éducation des salariés et les possibilités qu’ils ont d’accéder à une grande variété d’informations dans leur vie sociale, les grandes tendances qui impactent la société entrent de plein fouet dans l’entreprise. Celle-ci ne peut pas demeurer un monde clos dans lequel les règles du jeu de la relation de travail seraient affranchies de ce qui se produit dans l’environnement social, à savoir le passage d’un contrat vertical à un contrat plus horizontal9.
Crise de l’autorité et du lien de subordination, revendication de participation aux décisions collectives et de respect de la capacité de chacun à penser et à agir, individualisme centré sur la réalisation de soi et tendance au zapping professionnel, organisation communautaire et par affinité au sein des réseaux sociaux, consommation responsable, recherche d’un équilibre entre vie personnelle et vie professionnelle, quête du sens social ou éthique de l’action dépassant la simple satisfaction des besoins individuels,… toutes ces tendances traversent l’identité de l’individu au travail, et l’entreprise se voit contrainte de les prendre en compte. La rapidité avec laquelle certains dirigeants de grands groupes ont pris la défense de la « raison d’être », lors des débats qui ont précédé l’adoption de la loi PACTE, témoigne d’une compréhension assez fine du fait que, pour continuer à opérer dans la société contemporaine, les entreprises doivent changer de logiciel. Le design du travail propose un cadre pouvant permettre de prendre en compte les aspirations des travailleurs-citoyens.
Pour l’industrie, la réflexion à mener sur la réhabilitation du travail de production est encore plus prégnante, même si le volume d’emplois décroît en nombre.
En premier lieu, l’industrie a, par son histoire, une mauvaise réputation qui lui colle à la peau. Ne fut-elle pas le lieu de l’aliénation des masses laborieuses, soumises à un travail contraint, répétitif, souvent peu respectueux de la santé et des conditions de travail ? En 1912, Taylor écrivait ainsi : « Toute forme de travail cérébral devrait être éliminée de l’atelier et recentrée au sein du département conception et planification. »10 Il s’ensuit que l’Organisation scientifique du travail (OST) s’organisera autour d’une verticalité descendante entre le bureau d’études, le bureau des méthodes, et les ateliers de production limités aux tâches d’exécution. Le travail sera conçu par des personnes qui ne le réaliseront pas. Cependant, petit à petit, une expertise individuelle du « métier » émerge dans l’atelier, par la montée progressive en compétences. La critique du modèle taylorien se diffuse et l’étau de l’OST va progressivement se déserrer : de multiples innovations (cercles de qualité, chantiers Kaizen, systèmes de suggestions, groupes semi-autonomes) seront intégrées à la production, visant à tirer parti de l’intelligence des opérateurs, de leur connaissance du terrain, mais toujours dans le cadre d’une autonomie très contrôlée. En parallèle, l’entreprise gestionnaire11 fait son apparition, avec ses tableaux de bord, son reporting et l’obsession du court terme. Le profil de l’encadrant de terrain change. Il est choisi pour ses qualités de manager, plus que pour ses connaissances techniques. Il connaît de moins en moins le métier. Il est de moins en moins dans l’atelier. Il s’intéresse de moins en moins au travail. Les solidarités traditionnelles au travail se délitent, les fermetures d’usines se multiplient, donnant une vision peu engageante du travail dans l’industrie.
Dans la dernière décennie postérieure à la crise de 2008-2009, le discours change progressivement ; le secteur industriel retrouve des couleurs, son utilité économique et sociale est à nouveau reconnue, mais le mal est fait, et depuis longtemps12. La faible attractivité des métiers de production handicape fortement les possibilités de recrutement des entreprises françaises. Si l’on veut attirer les jeunes générations vers ces métiers, il est impératif de montrer que le travail n’a plus grand-chose à voir avec la représentation taylorienne de l’usine, qui demeure très vivace dans les esprits.
D’autant qu’au même moment, une autre tension apparaît, qui vient, à son tour, peser sur la représentation du travail de production ; les technologies 4.0 entrent dans l’usine et se présentent tel un Janus à double face : vecteur d’amélioration des conditions de travail et de l’intérêt du travail, ou facteur progressif d’élimination des emplois de production, dont la qualité cesserait dès lors d’être un enjeu ? Si l’usine est destinée à être entièrement robotisée et numérisée, pourquoi se former à des métiers en voie de disparition ? L’alignement supposé des planètes entre sortie du taylorisme et usine 4.0 peine dès lors à convaincre les jeunes d’embrasser ces métiers, et on peut les comprendre. De fait, les usines françaises connaissent de grandes difficultés de recrutement, alors que leur carnet de commande commence à se remplir et que l’automatisation rend enfin possible le maintien de l’activité en France.
C’est donc à un double mouvement concernant le travail que doivent s’atteler les industriels : convaincre de l’enrichissement des tâches qu’ils proposent et de l’existence d’importantes marges d’autonomie dans le travail, tout en dénonçant l’usine sans hommes comme un fantasme. Moins d’emplois certes, mais un travail de meilleure qualité, avec de réelles marges de manœuvre et des responsabilités, un contact avec des technologies en pointe, une rémunération supérieure aux métiers hors industrie pour un même niveau de qualification, considération et respect pour l’intelligence des hommes, perspectives de progression et de carrière, dans de belles usines et dans une bonne ambiance.
Pour convaincre que cette réalité est bel et bien en voie de constitution, les paroles ne suffiront pas. Il va falloir s’intéresser de près à la qualité du travail « réel » le long d’un continuum d’organisation qui s’étend de la conception à la production des produits et services. C’est précisément à cette exigence que s’intéresse le concept de « design du travail ».
4.3 Du design de service au design du travail
La notion de « design de service » nous permet de mieux comprendre comment le design peut s’appliquer au travail13.
Dans les années 1920, avec la naissance du design industriel (Bauhaus), les concepteurs étaient centrés sur l’objet. À compter des années 1950, progressivement, l’environnement du produit a été davantage pris en compte dans tous ses aspects (fonctionnel, esthétique, sécuritaire…). Les théories ont alors commencé à s’orienter vers l’idée que le design devait intégrer l’ensemble des dimensions d’un processus centré sur l’usage. C’est aussi le moment où se développent des disciplines telles que la psychologie cognitive, la sémiotique, l’ergonomie… Si le marketing des services commence à apparaître dès les années 1970 dans les pays anglo-saxons, le concept de service design est véritablement né au début des années 1990 en Allemagne, à l’École internationale de design de Cologne (KISD). Son développement est allé de pair avec la place grandissante d’une réflexion centrée sur l’utilisateur et ses besoins. Ainsi, le design de service introduit une évolution par rapport aux théories orientées vers l’objet, tout en intégrant l’importance du design de produit.
Dans nos économies où les industries de services ont une importance croissante, le design de service participe à redessiner les parcours utilisateurs et les interfaces. La multiplication des interfaces logicielles et web accélère par ailleurs la montée en puissance de la « user experience » (UX) virtuelle.
De manière générale, le design de service s’appuie sur des bases à respecter. Il faut notamment avoir une certaine ouverture d’esprit, observer, accepter la mise en cause des objectifs initialement définis, et le principe de la co-conception. Bien entendu, le design de service ne s’applique pas uniquement aux entreprises de services ; il peut être utilisé comme méthode pour améliorer les processus internes et externes de tout type d’entreprise, et pas uniquement ceux qui concernent les interactions avec le client final. Le design du travail peut ainsi être appréhendé comme un design de service dont le premier client est le travailleur, mais qui bénéficie aussi au client du client (le client final).
La façon dont on passe du design de service au design du travail peut être illustré par un exemple14 : en 2005, le cabinet IDEO est sollicité par le groupe hospitalier américain Kaiser Permanente pour améliorer les échanges d’information entre les infirmières. L’hôpital avait en effet identifié des discontinuités de soins et des risques pour la sécurité des patients lors des rotations d’équipes. La direction avait relevé que chaque infirmière possède sa propre manière de communiquer les informations, ce qui peut occasionner de nombreux mal entendus. Bien que la finalité du programme soit l’amélioration du service au patient, ce sont bien les infirmières qui sont les « clientes » de cette intervention. Après une phase d’observation, un programme en quatre étapes a été développé pour optimiser les rotations d’équipes. Deux étapes concernent la préparation de la rotation : l’affectation des patients puis la transmission d’informations aux infirmières « arrivantes ». Les deux autres étapes interviennent pendant la rotation en commençant par une tournée des infirmières arrivantes et sortantes puis par l’installation d’un tableau blanc dans chaque chambre. Cette tournée permet de co-organiser avec le patient les objectifs à accomplir jusqu’à la prochaine rotation. Un travail de co-création, auquel ont participé des infirmières, des médecins et des directeurs d’établissements, a donné naissance à des prototypes de calendriers, logiciels et tableaux blancs, testés directement par les infirmières.
On voit émerger dans cet exemple l’idée que c’est l’action co-construite sur par
En production industrielle, à quoi pourrait alors ressembler un design du travail ?
4.4 Le design du travail en production industrielle
Dans un univers procédural et normé comme la production, le design du travail peut sembler un idéal hors de portée. Pourtant, de nombreux exemples d’équipes transversales chargées de définir l’organisation du travail et incluant des opérateurs existent déjà, comme nous l’avons vu dans le corps de cette étude, même si ces démarches ne sont pas systématiques.
Ce qui reste difficile à réaliser, c’est que la conception du produit prenne pleinement en compte la façon dont il sera fabriqué dans la totalité de la chaîne : dès la définition du produit, puis dans la gamme, la mise au point des standards, et enfin sur le poste de travail. Il reste beaucoup à faire pour prendre en compte les besoins des opérateurs dans la conception des processus de production. Une telle approche met évidemment en cause la hiérarchie entre ingénierie de conception, méthodes et exécution, de même qu’elle induit entre ces trois entités des processus non linéaires, fait d’itérations et de boucles de rétroaction.
Les méthodes à l’œuvre dans une entreprise comme SEW USOCOME indiquent qu’aller dans cette direction est possible.
SEW USOCOME : une démarche originale de conception
des lignes de fabrication
Certes, chez SEW USOCOME comme ailleurs, le travail de conception des produits reste localisé au bureau d’études (en Allemagne dans son cas), mais c’est localement et avec la collaboration des opérateurs que les cellules d’usinage ou les lignes de montage sont conçues et développées.
Philippe Klein, qui animait jusqu’à une période récente le pôle consulting (les experts centraux du lean, 5 personnes) et le pôle innovation process (30 personnes) pour SEW USOCOME, témoigne : « En ce qui concerne les plans de progrès, nous proposons d’entrée de jeu de faire une VSM15 pour essayer de mettre tout le monde d’accord sur la situation qui pose problème. On élabore donc une VSM initiale, une VSM cible et une feuille de route pour aller de l’une à l’autre. Ensuite nous commençons les chantiers d’amélioration avec les équipes terrain et l’opérateur. »
Qu’il s’agisse de la conception des lignes ou des chantiers d’amélioration, le manager de la mini-usine dégage du temps aux opérateurs pour participer aux groupes de travail sur les processus. « Soit les équipes produisent, soit elles réfléchissent à leur futur, mais elles ne peuvent pas faire les deux en même temps. En règle générale, en fonction de la complexité des sujets, l’équipe travaille 3 ou 5 jours non-stop. Elle est constituée d’opérateurs, des gens qui touchent au quotidien les étapes de ce processus, ainsi que des représentants de la qualité, des méthodes, de la maintenance. La composition du groupe est variable en fonction de la thématique, mais il y a toujours l’opérateur car c’est celui qui sait parce qu’il fait. Même si un objectif cible a été fixé avec le management, c’est bien l’équipe qui définit l’objectif final retenu. On va discuter de ce qui ne va pas, donc on va mettre les lunettes du gaspillage. Puis, chaque membre de l’équipe exprime des propositions d’objectifs. Nous gardons tous ces objectifs. Pas de filtre. En fait, on réalise un catalogue des attentes des opérateurs. En résumé, la 1ère journée, c’est observation du processus, attentes des opérateurs, identification des gaspillages, explication de la VSM cible et de la feuille de route, formation. La valeur de cette première journée, c’est un consensus sur la situation, les objectifs fixés par le groupe, et les attentes définies par chaque membre du groupe. »
Suit une deuxième journée pour analyser en détail les processus. « Le consultant interne partage le travail entre les membres du groupe. On a alors des séances d’observation de parties de processus, et en général l’après-midi, on consolide la totalité du processus. Qu’est-ce que ça veut dire “observer” ? ça veut dire écrire les activités élémentaires, les quantifier (temps, mètres, surfaces, kilos) pour rendre les choses factuelles. Il s’agit de mesures terrain, et pas des chiffres issus du Système d’Information (SI). Les temps opératoires sont fixés par les membres du groupe entre eux et sur base de l’expérimentation. En fin de journée, restitution au directeur d’usine. La restitution est faite sous forme de prise de parole de chacun des participants au groupe de travail, y compris les opérateurs bien entendu. Fin de la 2ème journée. On a tout sur la table. Il faut maintenant réfléchir et devenir créatif pour le nouveau processus.
3 ème journée : comment pourrait être le nouveau processus ? Dans tous les cas de figure, un consensus sur le nouveau processus doit être arrêté rapidement (fixer l’idée). On réalise une maquette carton 2D dès le matin pour rendre l’idée concrète. L’après-midi, on réalise une maquette 3D sur cette base et cette maquette 3D deviendra le cahier des charges pour la ligne future. La séquence de 3 jours se termine. Présentation par l’équipe à l’ensemble du management. S’il s’agit d’un processus avec beaucoup d’innovations, on s’arrête là. Un travail est à faire ensuite pour travailler le projet avant de l’implémenter. Si les modifications sont limitées, on peut passer en quatrième et cinquième journée à la réalisation effective. Au bout de 5 jours, on a donc réalisé un nouveau processus. Après, on repart en amélioration continue pour, par exemple, maîtriser la variabilité induite par le nouveau processus. Mais s’il s’agit d’un nouveau processus complet, sa réalisation peut prendre bien entendu plusieurs mois.
La technologie de la réalité virtuelle permet aujourd’hui de sophistiquer cette manière de faire. « L’idée est d’immerger les collaborateurs dans le nouveau processus à travers la réalité virtuelle. Un premier pilote prometteur a été réalisé. La difficulté n’est pas d’imaginer le processus, mais de faire interagir 3-4 opérateurs dans un environnement virtuel. Et si, en plus, il y a de l’interaction avec un robot, c’est assez compliqué.
Et puis on rajoute encore une partie : l’ergonomie avant que la ligne n’existe. Aujourd’hui, la cotation finale est réalisée quand la ligne existe. Et il arrive d’avoir encore des problèmes sur la nouvelle ligne. Il faut donc re-démonter/corriger. [L’usage de la réalité virtuelle] aura donc un autre effet : au-delà de la ligne carton, on met les opérateurs en scène tout de suite dans ce nouveau processus. Ça a un effet rassurant et les gens se prêtent au jeu du nouveau processus avec les casques de réalité virtuelle. De plus à travers des capteurs posés sur les différents membres du corps, nous pourrons évaluer l’ergonomie en temps réel. L’expérimentation est en cours sur un premier projet.
On voit ici un exemple de ce que peut être le design du travail : la conception en équipe transverse d’une nouvelle ligne de fabrication, en prenant en compte l’expérience des opérateurs de fabrication et leurs attentes.
On peut évidemment imaginer aller encore beaucoup plus loin. Le design du travail, en tant que mode de pensée visant la co-conception du travail, inclut toutes les formes de dialogue et de délibération pouvant exister sur et autour du travail, telles que le dialogue sur la qualité du travail (DQT) développé par les équipes du Cnam et expérimenté à l’usine Renault de Flins, l’ergonomie de l’activité et les groupes d’amélioration continue (groupes Kaizen).
4.5 Design du travail et numérique
Aujourd’hui cependant, une nouvelle menace apparaît, pouvant venir peser sur la coconception du travail : que les outils numériques de plus en plus nombreux qui cadrent et prescrivent le travail soient conçus, réalisés, standardisés et déployés par des « sachants » numériques sans tenir compte du savoir-faire des salariés, de leurs conditions réelles de travail, ou sans les adapter aux usages qu’ils en feront.
Ainsi que l’indique Maryse Salles16, enseignante en informatique à l’université de Toulouse, le système d’information est un langage et, comme tout langage, il structure le monde dans lequel l’organisation agit. Les indicateurs choisis peuvent, par exemple, imposer aux salariés une vision modifiée de leur mission, l’amélioration de l’indicateur devenant un objectif en soi au détriment d’autres objectifs. Elle donne l’exemple du reporting des infirmières : si l’item « parler avec les proches d’un patient » ne figure pas dans le « menu » de suivi du temps de travail des infirmières, cette activité finira par être assimilée progressivement à une « perte de temps » et par disparaître de leur agenda, en dépit de son utilité sociale.
L’association des personnels à la conception des systèmes d’information, au choix des indicateurs retenus, semble être un angle mort de la réflexion sur le travail. Le design du travail a vocation à s’intéresser aussi à cette question. De ce point de vue, un exemple intéressant est la mission réalisée par l’équipe du cabinet conseil Fabernovel auprès d’un grand groupe industriel. Le point de départ de la mission est le constat fait par l’industriel que les outils numériques de suivi de la performance des équipes de fabrication, préparés et mis à disposition par la Direction administrative et financière, sont inadaptés à la fois en termes de choix des indicateurs de suivi, mais aussi en termes d’ergonomie de l’interface utilisateur. Un travail de recueil des besoins auprès des équipes qui suivent cette performance a donc été réalisé par un designer afin de servir de base au cahier des charges du nouveau logiciel à développer.
Enjeu de motivation des salariés, d’attractivité de l’industrie, comme d’efficacité et de productivité à long terme, le design du travail a un champ d’applications très large. La tâche qui l’attend est immense.
- 1. Ce chapitre est un développement de l’article paru dans Le Monde du 10 janvier 2019 https://www.la-fabrique.fr/wp-content/uploads/2018/06/article_le-design-du-travail.pdf
- 2. Charlotte Perriand, Une vie de création , Odile Jacob, 1998.
- 3. https://www.lesechos.fr/thema/transformation-entreprise/un-management-reinvente-levier-indispensable-a-la-transformation-994008
- 4. L’Esprit Design , Pearson, 2014.
- 5. Vineet Nayar, Employees first, Customers second , Harvard Business Review Press, 2010.
- 6. Pierre-Yves Gomez, Le travail invisible , François Bourin Editeur, 2013.
- 7. Laurence Decréau, Tempête sur les représentations du travail, Paris, Presses des Mines, 2018.
- 8. Anja Van den Broeck and Sharon K. Parker, Job and Work Design , Oxford Research Encyclopedia.
- 9. Voir aussi sur ce sujet Gilles-Laurent Rayssac, Danielle Kaiserguber, Martin Richer, Délibérer en politique, participer au travail : répondre à la crise démocratique , Terra Nova, 26 février 2019.
- 10. Shop management , 1912, p. 98-99.
- 11. Vincent de Gaulejac, La Société malade de la gestion. Idéologie gestionnaire, pouvoir managérial et harcèlement social , Seuil, 2005.
- 12. Laurence Decréau, op. cit.
- 13. https://www.usabilis.com/design-de-service/
- 14. Cet exemple est tiré du site de ressources sur le design de services http://www.designdeservices.org/exemples/15/
- 15. Value Stream Mapping ou cartographie des flux de valeur.
- 16. Maryse Salles, « Langages au travail : enjeux de pouvoir et d’émancipation » in Bourdu et al., Le travail en mouvement, Presses des Mines, 2019.
CONCLUSION
Les transformations dont ont témoigné les dirigeants interrogés dans cette étude ont pour objectif de donner plus de compétitivité et d’agilité à l’organisation, pour mieux répondre à la demande d’un client exigeant : raccourcissement des délais, personnalisation des séries, apprentissage en boucles courtes… Dans les petites organisations, la finalité poursuivie semble être moins la croissance « à l’infini » que la pérennité de l’entreprise, permettant de maintenir un bon niveau d’investissement et de construire une communauté de travail et d’emplois, dans une ambiance qui soit la plus agréable possible. Aux yeux de certains dirigeants, croître au-delà de cinquante salariés impliquerait une remise en question de l’organisation jugée trop profonde par rapport à leur modèle de référence. Ce « syndrome de Peter Pan », qui va bien au-delà des effets psychologiques des seuils sociaux, doit pouvoir être dépassé à nos yeux : des structures plus grandes témoignent de leur capacité à combiner performance, autonomie et qualité du travail.
Nous avons constaté que trois briques principales structurent l’organisation du travail dans les entreprises en mutation : le lean, l’autonomisation des personnes et l’introduction de technologies, qu’elles relèvent ou non de l’industrie du futur (SI, technologies du web collaboratif, robots…). L’aspect technologique est perceptible, sans être encore massif, et s’intègre dans les entreprises de notre échantillon au sein d’une vision globale de la transformation à accomplir (organisation, relation client, culture). Dans les PME, le lean est utilisé comme une boîte à outils, sans référence à une doctrine d’organisation qui aurait une vocation universelle. C’est un lean pragmatique, adapté aux besoins de chaque organisation, source d’amélioration là où n’existaient auparavant que très peu de démarches structurées. En complément ou en « correction » du lean, l’autonomie des personnes est promue par les chefs d’entreprise, souvent en lien avec un aplatissement de la ligne hiérarchique, mais elle est vue comme un chemin parfois escarpé, nécessitant un apprentissage et la construction progressive d’une confiance réciproque. L’autonomie est vécue comme un véritable changement culturel que tout le monde ne veut ni ne peut suivre, chez les opérateurs comme chez les managers, en dépit d’investissements souvent lourds en formation et accompagnement. Le renouvellement générationnel des équipes devrait progressivement atténuer les difficultés, tout en générant dans l’intervalle des tensions et parfois un management à deux vitesses. Au-delà de l’autonomie, l’accent est mis sur les incitations aux collaborations transverses, sans passer par la hiérarchie, de façon à accroître la densité relationnelle et les capacités d’apprentissage informel des équipes. Les démarches participatives s’inscrivent dans ce contexte, répondent à une demande sociale des salariés et visent à établir au sein de l’organisation un meilleur niveau de confiance.
En revanche, les dirigeants interrogés ont rarement abordé le rôle des institutions représentatives du personnel (IRP) dans le processus de transformation : soit que les organisations soient petites et familiales, soit que le sujet soit source de tensions inavouées. Ce point mériterait d’être creusé.
Quand l’autonomie et le lean sont mis en œuvre conjointement, ils préparent et facilitent l’acceptabilité et l’appropriation des technologies qui contribuent, à leur tour, à l’autonomisation et à la montée en compétences, ce qui construit de la confiance à toutes les étapes. Dans le cas contraire, mais non représenté au sein de notre échantillon, le lean augmenté par les technologies pourrait réduire puissamment les marges de manœuvre des travailleurs peu qualifiés et ouvrir la voie à une « aliénation 4.0 », telle qu’on peut déjà la voir à l’œuvre dans certaines entreprises de la logistique.
Le modèle CALT, articulation de la confiance, du lean, de l’autonomie et de la technologie, permet de donner une assise à notre proposition sur le design du travail, impliquant un dialogue et une délibération avec les personnels de production sur la définition de leur propre travail, le long d’un continuum allant de la conception du produit (bureau d’études) jusqu’à l’amélioration continue des processus (chantiers Kaizen), en passant par les méthodes (conception des lignes et des postes).
Sur le plan des compétences, une tendance semble émerger. Du fait de la rareté ou de l’inadéquation des compétences, y compris pour des compétences « métiers » classiques, les entreprises manufacturières s’intéressent désormais aux potentiels et aux talents des futurs salariés : savoir-être de base (ponctualité, rigueur, politesse, capacité de travail, capacité à apprendre), compétences relationnelles, mais aussi savoir-faire cachés dans les replis de la vie personnelle. Il s’agit d’élargir à l’ensemble des postes la « gestion des talents », autrefois réservée aux hauts potentiels de l’encadrement ou aux métiers d’expert. Détecter ces potentiels, les accompagner pour les développer, pourrait représenter à l’avenir une compétence distinctive pour les entreprises, encore plus appréciable lorsqu’il s’agira de redéployer les effectifs vers des métiers « qui n’existent pas encore », sans référentiel ni formation adaptée. Notons au passage que la promotion de leur marque employeur a été l’une des principales raisons poussant les chefs d’entreprise à témoigner dans le cadre de cette étude, ce qui confirme que les difficultés de recrutement dans les métiers de production restent une préoccupation majeure des dirigeants.
L’irruption de l’industrie 4.0 et la digitalisation qu’elle implique rendent plus que jamais nécessaire l’instauration de la délibération sur le travail dans l’entreprise1, car le risque est réel que la prescription technologique vienne encore réduire les marges de manœuvre des salariés si une grande vigilance n’est pas portée à ces questions. Il s’agit de mettre les salariés en position de se réapproprier leur travail et de participer à la recherche d’un équilibre entre la performance de court terme et la réalisation personnelle et collective qui garantit la performance sur le long terme. Il s’agit aussi de transformer l’image de l’industrie auprès de la population et particulièrement des jeunes, non seulement en donnant à voir un espace de développement technologique avancé, mais aussi et surtout en construisant l’image d’une communauté qui développe le potentiel des personnes et des équipes. L’attractivité de l’industrie en dépend.
- 1. Mathieu Detchessahar, L’entreprise délibérée, op. cit.
Annexe : 10 tensions qui questionnent le travail
Ce que nous disent les enquêtes et les études
De nombreuses études1 parues ces dernières années sur les questions d’évolution du travail et de compétences font apparaître des contradictions ou des paradoxes, montrant que les évolutions sont complexes et difficiles à saisir, et rendent inopérantes les recettes simples et les solutions monolithiques. Nous les synthétisons autour d’un panorama en dix tensions.
Tension n°1 : Disparition des emplois versus mutation des métiers
C’est une tension en toile de fond. La question de l’impact du numérique, de la robotisation et de l’intelligence artificielle sur l’emploi a fait couler ces dernières années beaucoup d’encre2. Les travaux les plus récents font état pour la France d’environ 10 % d’emplois risquant de disparaître3, tandis que les projections de créations d’emplois liées aux nouveaux produits et services restent hasardeuses. Cette question macro-économique et ses conséquences sociales relèvent de la sphère publique ; elle n’est pas du ressort direct des dirigeants d’entreprises manufacturières qui, au mieux, se livrent à des exercices de gestion prévisionnelle des emplois et des compétences (GPEC), et dont certains ne peuvent que constater l’érosion des emplois de production par unité productive : « Il est vrai que, sur un plan global, l’automatisation détruit des emplois [de production]. Par chance, notre entreprise connaît une croissance qui lui permet de continuer à en créer, alors qu’elle recourt de plus en plus aux robots. En 2009, nous avons inauguré une usine de 23 000 mètres carrés qui employait 200 personnes, dont 70 dans les ateliers et le reste en support. Celle que nous sommes en train de construire actuellement emploiera 120 salariés seulement, pour un volume de production comparable. Dans les entreprises qui n’ont pas la chance de connaître la même croissance, les machines ont tendance à remplacer les hommes » (Anne Leitzgen, Schmidt Groupe).
La mutation des métiers est, elle, une préoccupation beaucoup plus directe pour les patrons. Elle est susceptible d’entraîner au niveau de chaque entreprise un constat d’inadéquation des compétences nécessaires au développement de l’industrie du futur. L’étude de McKinsey, Skill Shift, pour les États-Unis et l’Europe (2018) indique qu’entre 2016 et 2030, la demande des entreprises manufacturières pour les capacités physiques, les compétences manuelles et les compétences cognitives de base, va continuer à décroître à un rythme deux fois supérieur aux autres secteurs d’activités, tandis qu’elle augmentera pour les compétences cognitives supérieures, les savoir-être et les compétences technologiques (de base et avancées).
Face à ce mismatch les entreprises déploieront de plus en plus une combinaison de cinq types d’action pour (re)composer la main-d’œuvre dont elles ont besoin : former, redéployer, embaucher, externaliser, licencier.
Quel sera le rythme de ces évolutions ? Ce diagnostic porté sur la demande de compétences ne correspond pas, à ce jour, à ce qui est constaté par une majorité d’entreprises manufacturières françaises qui sont au contraire confrontées à des difficultés de recrutement sur des compétences « métiers » classiques : chaudronniers, soudeurs, tourneursfraiseurs, opérateurs sur machines à commande numériques, etc. ce qui les mobilise dans l’immédiat bien davantage que le recrutement de data scientists, en particulier dans les PME. Olivier Bouba-Olga, spécialiste des dynamiques territoriales, constate que, lors de tous ses travaux de terrain, ce problème est évoqué par les entreprises4. On manque cependant de données pour mesurer précisément l’ampleur du problème. L’enquête « Besoins en main-d’œuvre » (BMO) de Pôle Emploi montre que la part des projets de recrutement jugés difficiles par les entreprises est importante : elle se monterait à 44,4 % en 2018, tous métiers et secteurs confondus. La métallurgie est le secteur où la part des recrutements difficiles est la plus importante (67 %), les autres industries manufacturières se situant à 61 %. Parmi les 100 métiers en tension recensés par Pôle Emploi en 2018, un grand nombre sont des métiers avec une forte composante manuelle.
Tension n°2 : Mutation technologique versus mutation organisationnelle
Cette tension constituait l’hypothèse de départ de cette étude. Selon un livre blanc d’EY (2017), la transformation de l’outil de production par l’introduction de technologies précède généralement la mutation de l’organisation : 45 % des entreprises de leur échantillon étaient en avance sur la transformation opérationnelle par rapport à celles de l’organisation et de la relation client. L’étude formule l’hypothèse que la transformation de l’organisation n’apparaît nécessaire que lorsque l’entreprise se heurte à un plafond de performance; ce n’est qu’à ce stade que la culture, le degré d’ouverture et l’organisation proprement dite sont remis en question. EY ajoute qu’« a posteriori, les témoignages suggèrent qu’il aurait été préférable de commencer avec la transformation de l’organisation »5 pour obtenir de meilleurs résultats. L’étude avance également l’idée que la transformation de l’organisation est, pour les grandes entreprises, un sujet plus délicat et anxiogène que les autres dimensions, en raison des enjeux de compétences, d’emplois et de culture d’entreprise qui s’y rattachent. On peut entendre en arrière-plan des craintes de tensions ou de conflit social.
Les conclusions de Bpifrance Le Lab dans son étude de fin 20186, ainsi que nos propres observations, ne corroborent cependant pas totalement ce diagnostic. Nous avons plutôt été frappés par le fait que les entreprises interrogées envisagent les technologies sous l’angle de la performance globale de leur entreprise, et analysent en même temps l’ensemble des dimensions, même si les transformations peuvent être mises en œuvre successivement. La transformation organisationnelle est d’ailleurs parfois déclenchée par une crise économique qui secoue l’entreprise dans ses fondements. Ce décalage pourrait provenir du fait que notre échantillon comporte davantage de petites structures qui ont été menacées de disparition que celui d’EY centré sur de grandes organisations.
Tension n°3 : Individu versus collectif
Les trois besoins psychologiques fondamentaux de l’individu, moteurs de la motivation intrinsèque7 au travail, sont désormais assez bien connus. Il s’agit de l’autonomie, ou désir de diriger sa propre vie, de la maîtrise, associée au besoin de développer ses compétences, et de la finalité ou du sens, c’est-à-dire le fait de travailler pour un objectif plus grand que soi. Ces trois besoins au travail sont particulièrement perceptibles chez les jeunes générations : pour 56 % des jeunes actifs entre 20 et 30 ans interrogés par la Cegos8, l’épanouissement et la réalisation de soi, d’une part, le développement des compétences, d’autre part, sont les principaux objectifs qu’ils fixent au travail (la rémunération restant le 1er critère d’attractivité d’un poste selon la même étude). Ce qui conduit les entreprises à devoir agir, à des degrés divers, sur ces trois leviers de motivation.
Susan Fowler9 garde les deux premiers ingrédients de la motivation (autonomie et compétences) et reformule le troisième. Le sens s’étendrait au lien à autrui (relatedness10). L’Homme comme animal social fait ici son entrée. La motivation intrinsèque aurait une dimension sociale importante, incluant la qualité des relations dans le groupe et le respect mutuel. Ce qui fait dire au sociologue Pierre Veltz qu’« au niveau d’un site productif, la performance repose moins sur la qualité et le coût des diverses ressources que sur l’intelligence de leur combinaison, autrement dit l’efficacité de l’organisation et du tissu relationnel »11.
Or les techniques de management individualisées (par objectifs) diffusées depuis trente ans, en matière de recrutement, évaluation, gestion des carrières et rémunération, et répondant pour partie à une demande des salariés eux-mêmes, ont contribué à « casser » les collectifs de travail, générant des comportements compétitifs, non coopératifs et protectionnistes qui vont aujourd’hui à l’encontre des besoins des entreprises. D’où un mouvement de balancier inverse visant à promouvoir les collaborations intra et interéquipes au sein de l’organisation. Mais simultanément, si l’efficacité relationnelle est revalorisée, elle reste souvent abordée par les entreprises comme un savoir-être subjectif de l’individu (un savoir-être à détecter, à renforcer, à évaluer) plutôt que comme la résultante d’une organisation du travail (et donc de méthodes de management) incitant à un fonctionnement réellement collectif.
Cet équilibre difficile à trouver entre la motivation de l’individu et l’efficience collective est au cœur de la réflexion de nombreux chefs d’entreprise.
Tension n°4 : Travail prescrit versus autonomie des salariés
Les salariés, et en particulier les Millenials12, réclament plus d’autonomie dans le travail. Cette montée en autonomie des collaborateurs est également affichée par les dirigeants d’entreprises comme une demande forte pour le bon fonctionnement des nouvelles organisations.
Selon les enquêtes Dares « Conditions de travail », l’autonomie est pourtant en recul continu depuis 1998 pour toutes les catégories de salariés13 sur des critères tels que la façon d’atteindre les objectifs, les délais, les consignes, la latitude pour régler les incidents14. Un indice positif cependant : entre 2013 et 2016, ils sont de plus en plus nombreux à déclarer que leur travail leur permet d’apprendre des choses nouvelles.
Une autre étude IFOP/IGS (juin 2018) indique que l’évolution des modes de management perçue par les salariés va vers plus de hiérarchie, de bureaucratie, de court terme et d’opacité.
Un peu moins de 4 salariés sur 10 perçoivent cependant l’émergence de nouveaux modes de management autonomisants et responsabilisants. Ceux qui les identifient indiquent que le management encourage l’expression de points de vue divers, permet un soutien aux collaborateurs même s’ils font parfois des erreurs, manifeste de la confiance pour prendre des décisions sur des sujets importants, offre des possibilités de développer leurs compétences.
On est ici au cœur du paradoxe actuel entre les discours et les actes : dans les discours, on présente les transformations comme déjà opérées, alors que l’évolution des modes de management est certes présente, mais ne concerne encore qu’une grosse minorité de salariés. Pour la majorité d’entre eux, une tendance inverse est à l’œuvre avec des organisations qui se rigidifient et des marges de manœuvre qui diminuent, en dépit de toutes les déclarations. Une hypothèse expliquant cette dernière tendance est qu’elle serait due à la crispation de managers désorientés15, déstabilisés par le changement culturel à l’œuvre (voir aussi Tension n°6). D’autre part, ce sont souvent les dirigeants de grandes entreprises qui s’expriment sur ces sujets, mais ils ne représentent qu’une fraction infinitésimale des entreprises françaises.
Tension n°5 : Diminution de la pénibilité versus surcharge cognitive
D’une part, la diminution de la pénibilité physique des tâches est au cœur des argumentaires des fournisseurs de solutions d’automatisation et de robotique. Les ergonomes, de leur côté, tendent à s’insurger contre cette vision simplificatrice de la technologie comme « remède », la santé au travail résultant de multiples facteurs, entre autres des modalités d’insertion de la technologie et des marges de manœuvre accordées au salarié.
D’autre part, il est souvent affirmé que les nouvelles technologies joueraient un rôle dans la perception de l’intensification des rythmes de travail (contrôle et suivi informatisé de la production, cadences et délais, sollicitations constantes, etc.), augmentant le risque de surcharge cognitive et donc d’atteinte psychique à la santé.
Qu’en dit la Dares ? Dans sa dernière étude « Conditions de travail » (2016), les contraintes physiques sont en légère diminution par rapport à 2013, mais demeurent à un niveau élevé pour la population ouvrière : plus de 60 % des ouvriers restent exposés à au moins trois contraintes physiques parmi cinq16.
Après une période de très forte augmentation jusqu’en 1998, les contraintes de rythme de travail tendent à se stabiliser pour toutes les catégories socioprofessionnelles, à l’exception des ouvriers non qualifiés qui sont aussi souvent des intérimaires jouant le rôle de variable d’ajustement. Seule la contrainte « normes de production à satisfaire en une journée ou plus » continue de croître. L’exposition au contrôle et suivi informatisé du travail a fait un bond entre 2005 (première date du suivi de ce critère) et 2013, passant de 25 à 35 % pour l’ensemble des catégories, et de 26 à 37 % pour les ouvriers qualifiés, mais se stabilise entre 2013 et 2016. La charge mentale est en réduction pour toutes les catégories mais particulièrement pour les ouvriers qualifiés. L’enquête « Parlons travail » de la CFDT (2017) fait entendre un autre son de cloche concernant la charge de travail : selon celleci, moins de 30 % des salariés seraient dans une situation de charge de travail pouvant être considérée comme « normale ».
Globalement, l’enquête Dares 2016 donne à voir des évolutions légèrement positives, mais on sait que les moyennes agrégées peuvent dissimuler une grande disparité de situations. Il sera intéressant d’observer si ces tendances récentes se confirment dans la prochaine étude qui paraîtra en 2020.
Tension n°6 : Aplatissement des niveaux hiérarchiques versus transformation du management
Tendanciellement, les entreprises suppriment l’empilement des niveaux d’encadrement pour favoriser une meilleure agilité de l’organisation et restreignent les fonctions support17. Cette tendance se présente comme la contrepartie de la montée en autonomie souhaitée, voire comme l’une des manières de la favoriser. Le rôle du management de proximité en ressort considérablement transformé : l’animation des relations et le soutien aux salariés doivent venir remplacer l’encadrement, le contrôle et le reporting. « L’entreprise aura bien plus besoin d’animateurs que de chefs dans le futur »18 indique l’AIF.
Cette transformation est difficile, compte tenu d’une tradition française de distance hiérarchique19 et de stratégies descendantes. Lorsqu’elle a lieu, elle est vécue souvent douloureusement par les managers qui ressentent un décalage croissant entre la formation au management vertical qu’ils ont reçue en école, et les nouvelles injonctions à collaborer et à se faire « passeurs de sens » promues par les directions RH. D’autant que les directions ne sont pas à l’abri de contradictions et d’hypocrisie organisationnelle, mêlant les nouvelles injonctions à d’anciennes pratiques, de même que les aspirations des salariés ne sont pas toujours homogènes concernant l’autonomie et la responsabilité. Le malaise dans le management, souligné par Brigitte Nivet dans un récent article20, est perceptible partout. Un symptôme : les cadres se sentent souvent plus proches de leurs collaborateurs que de leur direction21. Parmi les dirigeants auditionnés, plusieurs ont indiqué que c’est avec le management intermédiaire qu’ils ont rencontré le plus de difficultés au cours de leur transformation (« En matière d’évolution de l’organisation, c’est, de façon classique, avec le management intermédiaire que nous avons rencontré le plus de problèmes. Les petits chefs d’hier sont désormais confrontés à des jeunes qui ont étudié Excel en première langue et à qui il ne faut pas raconter d’histoires… », Alliansys).
Tension n°7 : Qualité de l’environnement de travail versus qualité du travail
La qualité de l’environnement de travail (bâtiment, restaurant d’entreprise, salle de repos et de sport, crèche, conciergerie, massages, etc.) fait l’objet d’une grande attention dans les entreprises les plus en pointe, afin de renforcer l’attractivité de leur marque employeur sur un marché des compétences tendu. Cette tendance est stigmatisée par certains observateurs : la philosophe Julia de Funès22 parle d’une « certaine infantilisation des salariés », par exemple via la nomination de Chief Happiness Officers. Installer des baby-foot et des salles de détente ne compensera pas une ambiance de travail délétère. La qualité de l’environnement de travail n’est qu’une des composantes de la qualité de vie au travail (QVT), concept multifactoriel23.
Selon le psychologue du travail Yves Clot, c’est bien davantage la qualité du travail qui produit bien-être et santé au travail. La qualité du travail est ici entendue comme la capacité de l’individu à réaliser les buts qu’on lui a fixés24. Il s’agit pour les individus non seulement d’atteindre les objectifs qui ont été fixés par d’autres, mais aussi d’avoir la possibilité de discuter et comprendre ces objectifs, voire de les remettre en cause pour donner naissance à d’autres objectifs plus appropriés. C’est ce travail sur le travail qui permettrait d’en finir avec les risques psychosociaux. Toujours selon Yves Clot, l’efficacité au travail et la fierté du travail bien fait sont des buts que l’individu cherche naturellement à atteindre, et l’organisation peut en tirer parti ou au contraire les entraver. Lorsqu’une personne se sent « empêchée » de bien faire en raison des contraintes et injonctions de l’organisation, la démotivation, puis les pathologies apparaissent. La qualité du travail représenterait donc le lien entre santé au travail des salariés et performance de l’organisation. C’est par la discussion sur les critères du travail (« qu’est-ce qu’un travail bien fait ? ») au sein d’espaces de délibération qu’on peut découvrir de vrais gisements de productivité et de qualité à travers la parole des salariés. C’est pourquoi Yves Clot comme Mathieu Detchessahar parlent de la quête d’une entreprise « délibérée » 25 plutôt que « libérée ».
On pourrait même aller jusqu’à penser que l’accent mis sur la qualité de l’environnement de travail est le masque qui vient souvent dissimuler le fait que la qualité du travail (autonomie, intérêt, sens) n’est pas au rendez-vous.
Tension n°8 : IRP freins ou partenaires ?
Les Institutions représentatives du personnel (IRP) sont bien souvent perçues par les chefs d’entreprise comme des freins ou tout du moins comme alourdissant les processus de décision. Les informations et consultations sur les modifications d’organisation ou sur l’introduction d’une nouvelle technologie sont souvent plus formelles que réelles. Beaucoup d’entreprises hésitent même à employer l’expression « transformation de l’organisation » car elles estiment que l’amalgame est trop souvent fait entre transformation, recherche de gains de productivité et plans de restructuration.
Une démarche pour structurer le dialogue social dans un contexte de transformation technologique et organisationnelle a été présentée par la fédération de la métallurgie de la CFDT (FGMM-CFDT), à l’occasion des travaux de l’Agora Industrie du futur26. Elle est issue d’un projet financé par le Fonds social européen et porté par la FGMM-CFDT, avec les concours du Cnam, de l’Alliance pour l’Industrie du Futur et de l’UIMM. L’objectif est d’accompagner les branches et les filières dans la réussite de la transition numérique de leurs entreprises et de leurs salariés, à travers la méthode du « design social » et en mettant des outils à la disposition des entreprises.
Tension n°9 : Polyvalence versus enrichissement des tâches
L’AIF décrit « l’opérateur 4.0 » dans les termes suivants : « La technologie et l’organisation permettent de décharger [l’opérateur] des tâches pénibles, répétitives, pour qu’il se concentre sur les tâches à forte valeur ajoutée27 » et, plus loin, « l’opérateur pourra se former en continu et renforcer sa polyvalence. »
L’enrichissement des tâches et la polyvalence sont l’une des promesses de l’industrie du futur, mais les rapports qu’entretiennent travail industriel et technologies semblent en réalité plus ambivalents que ne le laisse entrevoir cette description.
Premièrement, que deviennent dans ce contexte les compétences « métiers » (soudure, usinage, peinture, etc.) ? Si le travail passe de plus en plus par la médiation de machines ou de robots, le travailleur aura-t-il encore besoin de maîtriser les gestes du métier ? Le travail ressort-il « enrichi » de cette disparition du geste manuel ? Dans les CFA de la métallurgie, le choix a été fait de former les jeunes à la fois sur des machines traditionnelles et sur des machines à commande numérique. Beaucoup d’observateurs, dont les syndicats de salariés, pointent un risque de perte de compétences extrêmement dommageable à moyen terme, si l’on renonçait à transmettre l’expertise du métier telle qu’elle passe par l’intelligence de la main. D’ailleurs, dans des cas où l’on a « dérobotisé » certaines tâches dans l’industrie automobile, il a fallu aller chercher des retraités, car plus personne ne disposait de la compétence en interne28. Néanmoins, la question du contenu des formations et de l’équilibre à trouver entre compétences manuelles et compétences numériques se pose avec acuité.
Deuxièmement, tous les postes nécessiteront-ils une montée en compétences ? Les technologies numériques peuvent permettre de faire entrer ou de maintenir dans l’emploi des personnes à faible niveau de qualification. C’est le cas par exemple lorsque les tâches sont complètement assistées par des consignes (de montage, d’assemblage, ou par des scripts et protocoles transactionnels dans les services) affichées sur des écrans29. Le groupe Bosch, dans son catalogue de solutions pour l’industrie du futur, propose un poste d’assemblage disposant d’une aide intuitive30. Cette solution assiste l’opérateur étape par étape lors du montage grâce à un système de projection lumineuse, surveille les erreurs avec des caméras et propose des mesures correctives en cas de besoin. Un tel dispositif peut être utilisé pour la formation et assister l’opérateur qui doit réaliser des séries courtes de produits variés. Il permet aussi de recruter des opérateurs très peu qualifiés, mais il peut difficilement passer pour un vecteur d’enrichissement des tâches.
Enfin, qu’en est-il de la polyvalence, terme souvent présenté positivement ? Dans la vision promue par l’industrie du futur, l’opérateur devient un conducteur ou un pilote de processus, supervisant, le long d’une ligne ou dans un îlot, plusieurs machines connectées. Il doit comprendre son rôle dans le processus, signaler les problèmes et, de plus en plus souvent, les résoudre, intégrant une partie des compétences de maintenance et de contrôle qualité. Cette polyvalence correspond bien à l’idée que chacun peut se faire d’un enrichissement des tâches par rapport à l’ancienne organisation taylorienne. Mais le terme de polyvalence n’est pas dénué d’ambiguïté31. Pendant longtemps, la polyvalence inter-postes ou inter-fonctions était le signe d’une mobilité et d’une interchangeabilité résultant d’une faible qualification : une alternance de tâches faiblement qualifiées ou une traditionnelle rotation des postes visant à réduire la monotonie du travail. Ce n’est que plus récemment que la polyvalence a commencé à traduire une recomposition des tâches qui étaient autrefois éclatées sur plusieurs postes et qui sont maintenant regroupées sur un seul. Le même terme peut indiquer une poly-compétence sur un même poste (soudeur et régleur machine) ou sur des postes différents (soudeur et peintre). Le terme de polyvalence peut encore indiquer un élargissement des missions, comme par exemple l’adjonction d’un rôle de correspondant ou de facilitateur au sein d’une équipe de production. Bref, il existe toutes sortes de polyvalence. Dans tous les cas, il conviendra d’en cerner précisément la nature avant de conclure à un enrichissement des tâches. Par ailleurs, la polyvalence étant aussi un outil de flexibilité pour l’entreprise, il importe de regarder si celle-ci est documentée et rémunérée.
Tension n°10 : Compétences versus potentiels, talents ou appétences
On parle aujourd’hui beaucoup de savoir-être (soft skills) et de compétences (ou capacités) métiers (hard skills) difficiles à trouver sur un marché de l’emploi tendu. Parallèlement, une proportion significative de salariés ne trouve pas d’emploi en accord avec leur formation ou sont sur des postes qui ne correspondent ni à leurs capacités ni à leurs appétences, les deux situations résultant d’une orientation défaillante.
Dans les deux cas, les entreprises auraient tout à gagner à refonder leurs recrutements, gestion des compétences et des carrières sur de nouvelles bases : la détection et l’accompagnement des potentiels, des talents et des appétences. Le mot « talents » n’est pas ici employé en référence aux jeunes surdiplômés dont la rareté sur le marché suscite tous les appétits et qui avait fait l’objet d’un livre il y a déjà vingt ans32. Il fait référence au potentiel que chacun d’entre nous porte en lui et qu’il peut révéler, pour peu qu’il soit invité à le déployer ou qu’il soit accompagné pour le faire. Méconnaître le potentiel des individus est une des racines du désengagement au travail et du désir de reconversion professionnelle. Pour une entreprise, cette méconnaissance revient aussi à se priver d’un réservoir de recrutement en contexte de pénurie, à ignorer les ressources cachées pouvant ouvrir la voie à la création de nouvelles activités (intrapreneuriat), et à renoncer à un levier lors des réaffectations de personnel, pouvant permettre d’éviter les licenciements. Jacques Lebeau33, ancien cadre de La Poste, a développé une méthodologie pour révéler les talents enfouis en chacun à travers l’« entretien Talents ». Il a poussé très loin la démarche, allant jusqu’à créer des postes sur-mesure pour la quasi-totalité du personnel de son équipe. C’est l’organisation qui s’est adaptée aux salariés et non l’inverse.
- 1. Cette section est basée notamment sur les études et rapports suivants : Académie des technologies, Industrie du futur : du système technique 4.0 au système social , Rapport, décembre 2017 ; AIF, Le Guide des technologies de l’industrie du futur , mars 2018 ; Agora Industrie, Révolution humaine ? Un nouveau rôle pour les hommes et les femmes de l’industrie du futur , Livre blanc 2018 ; Anact, Aract, Associer les salariés à un projet de changement ; Bpifrance Le Lab, L’avenir de l’industrie : Le regard des dirigeants de PME-ETI sur l’industrie du futur et le futur de l’industrie , décembre 2018 ; Bpifrance Le Lab, Les Dirigeants de PME et ETI face au digital , septembre 2017 ; CFDT, Parlons travail, 2017 ; Dares, « Quelles sont les évolutions récentes des conditions de travail et des risques psychosociaux ? », Dares Analyses , décembre 2017 ; EMC2, Altran, L’Humain au cœur de l’industrie du futur ; EY, Croire en l’industrie du futur et au futur de l’industrie , Livre blanc, 2017 ; IGS-RH/Lispe/IFOP, « Les salariés et la transformation managériale », 2018 ; McKinsey Global Institute, Skill Shift. Automation and the Future of the Workforce , Discussion paper, May 2018.
- 2. Pour une vision synthétique des différentes études en la matière, voir « Numérique et emploi : quel bilan ? », Les Synthèses de La Fabrique, n°12, avril 2017.
- 3. Conseil d’Orientation pour l’emploi, « Automatisation, numérisation et emploi », janvier 2017.
- 4. « Sortir de la CAME pour mieux penser et mieux accompagner les territoires » in Bourdu et al., Le travail en mouvement, Presses des Mines, 2019.
- 5. EY, op. cit ., p. 54.
- 6. Bpifrance Le Lab, L’avenir de l’industrie, op. cit.
- 7. Daniel Pink, La vérité sur ce qui nous motive , Clés des champs, 2016.
- 8. « Les Millennials et le travail : l’entreprise au défi », Enquête Cegos, 2017.
- 9. Susan Fowler, Pourquoi motiver est-il si compliqué… et comment y arriver ! , Pearson, 2017.
- 10. « Relatedness is our need to care about and be cared about by others. It is our need to feel connected to others without concerns about ulterior motives. It is our need to feel that we are contributing to something greater than ourselves. », S. Fowler.
- 11. https://www.uodc.fr/les-amphis-debats/detail/a/cooperer-dans-lentreprise-entre-entreprises-sur-un-territoire-1789.html
- 12. 6e Baromètre Deloitte OpinionWay sur l’humeur des jeunes diplômés, 2017.
- 13. Sources : Dares, DGAFP, Drees, Insee, enquête Conditions de travail et risques psychosociaux (1991, 1998, 2005, 2013, 2016).
- 14. Critères pris en compte par la Dares : choisir soi-même la façon d’atteindre les objectifs fixés ; ne pas toujours appliquer les consignes ou ne pas en recevoir ; régler soi-même les incidents au moins dans certains cas précis ; ne pas avoir de délais ou pouvoir faire varier les délais fixés ; apprendre des choses nouvelles ou a contrario répéter continuellement une même série de gestes ou d’opérations.
- 15. Laetitia Vitaud, https://www.youtube.com/watch?v=fMA7Xk0L40c
- 16. Rester longtemps debout, rester longtemps dans une posture pénible, effectuer des déplacements à pied longs ou fréquents, devoir porter ou déplacer des charges lourdes, subir des secousses ou des vibrations.
- 17. L’étude « Autonomie et responsabilisation dans les organisations » (à paraître en 2020) de la chaire FIT2 montre cependant des cas où un choix inverse a été opéré : accroître les fonctions supports pour mieux accompagner la montée en autonomie.
- 18. Le Guide des technologies de l’industrie du futur, Alliance Industrie du futur, mars 2018, p. 46.
- 19. Le Power Distance Index ou indice de Hofstede classe la France en 42ème position dans les pays de l’OCDE avec une note de 68/100 quand les États-Unis avec 40/100 et l’Allemagne et le Royaume-Uni avec 35/100 sont nettement mieux placés.
- 20. « Malaise dans le management » in Bourdu et al., Le travail en mouvement , Presses des Mines, 2019.
- 21. « Paradoxalement, alors que les organisations sont plus plates, [les cadres] se sentent souvent plus proches de leurs collaborateurs – employés, ouvriers – que de leurs dirigeants. » in « Entreprises et salariés : une entente impossible » , Etudes , 2006/2, p. 189-199, et aussi « Depuis les années 2000, les cadres se sentent plus proches de l’ensemble des salariés que de leur direction. C’est un véritable retournement par rapport à ce que nous analysons depuis 80 ans », Philippe Dabi, directeur général adjoint d’Ifop France cité in Lemonde.fr 19 juillet 2018.
- 22. Socrate au pays des process , Flammarion, 2017.
- 23.« [La QVT] peut se concevoir comme un sentiment de bien-être au travail perçu collectivement et individuellement qui englobe l’ambiance, la culture de l’entreprise, l’intérêt du travail, les conditions de travail, le sentiment d’implication, le degré d’autonomie et de responsabilisation, l’égalité, un droit à l’erreur accordé à chacun, une reconnaissance et une valorisation du travail effectué. » Article 1, Accord national interprofessionnel du 19 juin 2013.
- 24. Voir Le travail à cœur , Pour en finir avec les risques psychosociaux , La Découverte, 2015.
- 25. Mathieu Detchessahar (coord.), L’Entreprise délibérée , Nouvelle Cité, 2019.
- 26. Livre blanc 2018 de l’Agora Industrie , p. 18.
- 27. Le Guide des technologies de l’industrie du futur , Alliance Industrie du futur, mars 2018, p. 8.
- 28. Témoignage d’un dirigeant de l’automobile recueilli par les auteurs.
- 29. Voir sur ce point, le cas d’Alstom Ferroviaria en Italie décrit in A. Magone, T. Mazali, Voyage dans l’industrie du futur italienne , Les Notes de La Fabrique, Presses des Mines, 2018.
- 30. https://www.designworldonline.com/activeassist-software-increases-process-reliability-and-quality-through-industry-4-0/
- 31. Christophe Everaere, « La polyvalence et ses contradictions », Revue française de Gestion Industrielle , vol. 27, n°4, 2008.
- 32. Ed Michaels, Helen Handfield-Jones, Beth Axelrod, The War for Talent , HBR Press, 2001.
- 33. Jacques Lebeau, Révéler les talents enfouis , AFNOR, 2016.
Bibliographie
Académie des technologies, « Industrie du futur : du système technique 4.0 au système social », Rapport, décembre 2017.
AIF, « Le Guide des technologies de l’industrie du futur », mars 2018.
Agora Industrie, « Révolution humaine ? Un nouveau rôle pour les hommes et les femmes de l’industrie du futur », Livre blanc 2018.
Anact, Aract, « Associer les salariés à un projet de changement », 2018.
Bpifrance Le Lab, « L’avenir de l’industrie : Le regard des dirigeants de PME-ETI sur l’industrie du futur et le futur de l’industrie », décembre 2018.
Bpifrance Le Lab, « Les Dirigeants de PME et ETI face au digital », septembre 2017.
Cegos, « Les Millennials et le travail : l’entreprise au défi », 2017.
CFDT, Enquête « Parlons travail », 2017.
DARES, « Quelles sont les évolutions récentes des conditions de travail et des risques psychosociaux ? », Dares Analyses , décembre 2017.
Deloitte/OpinionWay, 6 e Baromètre sur l’humeur des jeunes diplômés, 2017.
EMC2, Altran, « L’Humain au cœur de l’industrie du futur ».
Ernst&Young Advisory, « Croire en l’industrie du futur et au futur de l’industrie », Livre blanc, 2017.
IGS-RH/Lispe/IFOP, « Les salariés et la transformation managériale », 2018.
INSEE, « Formations et emploi », édition 2018.
La Fabrique de l’industrie, « Numérique et emploi : quel bilan ? », Les Synthèses de La Fabrique, n°12, avril 2017.
McKinsey Global Institute, « Skill Shift. Automation and the Future of the Workforce », Discussion paper, May 2018.
Pôle Emploi, Enquête « Besoins en main-d’œuvre » (BMO), 2018.
Terra Nova (Rayssac G.-L., Kaiserguber D., Richer M.), Délibérer en politique, participer au travail : répondre à la crise démocratique , 26 février 2019.
Articles
Ballarin B., « La responsabilisation appliquée à Michelin », in Bourdu E., Lallement M., Veltz P., Weil T., Le travail en mouvement , colloque de Cerisy, Presses des Mines, 2019, p. 126.
Barcellini F., « Industrie du futur : quelle place pour le travail et ses transformations ? » in Bourdu E., Lallement M., Veltz P., Weil T., Le travail en mouvement , colloque de Cerisy, Presses des Mines, 2019, p. 136.
Bonnefond J.-Y., « Instituer le dialogue sur la qualité du travail : un enjeu de performance et de santé » in Bourdu E., Lallement M., Veltz P., Weil T., Le travail en mouvement , colloque de Cerisy, Presses des Mines, 2019, p. 122.
Bouba-Olga O., « Sortir de la CAME pour mieux penser et mieux accompagner les territoires » in Bourdu E., Lallement M., Veltz P., Weil T., Le travail en mouvement , colloque de Cerisy, Presses des Mines, 2019, p. 308.
Bourgeois F., « Que fait l’ergonomie que le lean ne sait / ne veut pas voir ? », Activités , octobre 2012.
Clot Y., « Les conflits de la responsabilité », in Bourdu E., Lallement M., Veltz P., Weil T., Le travail en mouvement , colloque de Cerisy, Presses des Mines, 2019, p. 112.
Everaere C., « La polyvalence et ses contradictions », Revue française de Gestion Industrielle , vol. 27, n°4, 2008.
Lorenz E., Valeyre A., « Les formes d’organisation du travail dans les pays de l’Union européenne », Travail et Emploi, n °١٠٢, avril ٢٠٠٥, pp. ٩١-١٠٥.
Nivet B., « Malaise dans le management » in Bourdu E., Lallement M., Veltz P., Weil T., Le travail en mouvement , colloque de Cerisy, Presses des Mines, 2019, p. 160.
Richer M., « Autonomie au travail, la France a tout faux ! », Blog Management & RSE , 15 juin 2016.
Richer M., « Les organisations du travail participatives : les 5 piliers de la compétitivité », Blog Management & RSE , 12 septembre 2013.
Salles M., « Langages au travail : enjeux de pouvoir et d’émancipation » in Bourdu E., Lallement M., Veltz P., Weil T., Le travail en mouvement , colloque de Cerisy, Presses des Mines, 2019, p. 30.
Schnee T., « Bosch continue à déployer son concept de “Learning company” », Planet Labor , Article n. 11053 du 21.03.2019.
Ouvrages
Ballé M., La Stratégie Lean , Eyrolles, 2018.
Bourdu E., Péretié M.-M., Richer M., La Qualité de vie au travail : un levier de compétitivité , Les Notes de La Fabrique, Presses des Mines, 2016.
Brown T., L’Esprit Design – Comment le design thinking change l’entreprise et la stratégie , Pearson, 2014.
Clot Y., Le Travail à cœur, Pour en finir avec les risques psychosociaux , La Découverte, 2015.
Comte-Sponville A., Petit traité des grandes vertus , PUF, 1995.
Decréau L., Tempête sur les représentations du travail , Les Notes de La Fabrique, Presses des Mines, 2018.
Deshayes C., La Transformation numérique et les patrons , Les Docs de La Fabrique, Presses des Mines, 2019
Detchessahar M. (coord.), L’Entreprise délibérée, Nouvelle Cité, 2019.
Fowler S., Pourquoi motiver est-il si compliqué… et comment y arriver ! , Pearson, 2017.
Funès J. (de), Socrate au pays des process , Flammarion, 2017.
Gaulejac V. (de), La Société malade de la gestion. Idéologie gestionnaire, pouvoir managérial et harcèlement social , Seuil, 2005.
Getz I. et Carney B., Liberté et compagnie ; Quand la liberté des salariés fait le bonheur des entreprises , Fayard, 2012.
Gomez P.-Y., Le Travail invisible , François Bourin Editeur, 2013.
Lallement M., Le Travail sous tensions , Sciences humaines, 2010
Laloux F., Reinventing organizations : vers des communautés de travails inspirées , Diateino, 2015.
Lebeau J., Révéler les talents enfouis , AFNOR, 2016.
Magone A., Mazali T. (dir.), Voyage dans l’industrie du futur italienne , Les Notes de La Fabrique, Presses des Mines, 2018.
Michaels E., Handfield-Jones H., Axelrod B., The War for Talent , Harvard Business Review Press, 2001.
Munzenhuter M., Lemaire E., L’Entreprise qui libère les énergies : le management Perfambiance, Editions du Signe, 2016.
Nayar V., Employees first, Customers second , Harvard Business Review Press, 2010.
Pink D., La Vérité sur ce qui nous motive , Clés des champs, 2016.
Roche C., Le Lean en questions , L’Harmattan, 2016.
Rost B., La Quête de l’entreprise rayonnante , (auto-édité) 2019.
Sailly M., Démocratiser le travail. Un nouveau regard sur le lean management , Editions de l’Atelier, 2017.
Stepper J., Working Out Loud: For a better career and life , Ikigai Press, 2015.
Veltz P., La Société hyperindustrielle , Seuil, 2017.
Womack J., Jones D., Roos D., The Machine that Changed the World , Harper, 1991 .
François Pellerin, Marie-Laure Cahier, Organisation et compétences dans l’usine du futur. Vers un design du travail ?, Paris, Presses des Mines, 2019.
ISBN : 978-2-35671-583-8
ISSN : 2495-1706
© Presses des Mines – Transvalor, 2019
60, boulevard Saint-Michel – 75272 Paris Cedex 06 – France
© La Fabrique de l’industrie
81, boulevard Saint-Michel -75005 Paris – France