Voyage dans l’industrie du futur italienne
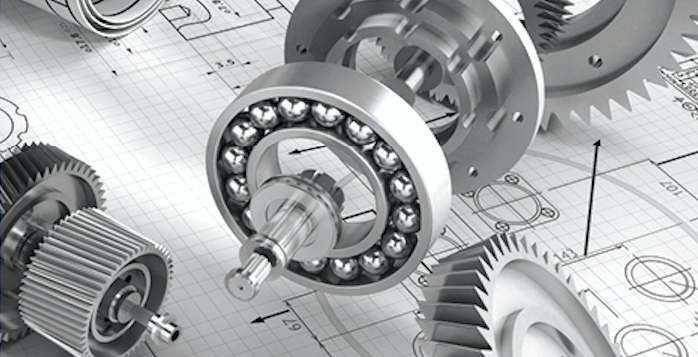
© Istock Photo/adventtr
Avant-propos
Ce voyage dans l’industrie 4.0 italienne, réalisé en 2014-2016 par des chercheurs de Torino Nord Ovest, un think tank basé à Turin, s’inscrit à plusieurs titres dans la droite ligne des travaux de La Fabrique de l’industrie. Nous sommes donc heureux d’en proposer aujourd’hui la traduction au public francophone.
En premier lieu, la publication de cette traduction correspond à notre volonté de faire connaître la réalité industrielle dans d’autres pays, afin d’alimenter la réflexion nationale et européenne. Nous avons déjà présenté des études sur l’Allemagne1, la Suède2, les États-Unis3 et le Royaume-Uni4. L’Italie vient aujourd’hui compléter ce panorama d’expériences étrangères.
L’industrie du futur est également un fil rouge de nos travaux, auquel nous avons déjà consacré plusieurs publications5. L’approche proposée ici par les auteurs est centrée sur l’impact qu’a ou aura la modernisation technologique des usines sur l’organisation et sur la nature du travail. Elle prolonge ainsi la Note que nous avions consacrée en 2016 à Travail industriel à l’ère du numérique, et plus généralement l’intérêt que nous portons aux transformations du travail6.
Nous tenons à remercier tout particulièrement Fiamma Ferrero de la société Inwibe, qui a porté la publication d’origine à notre connaissance, et s’est chargée avec efficacité du dialogue avec les auteurs et l’éditeur italiens.
La présente étude est structurée en deux grandes parties : la première (chapitre 1) raconte le voyage au sein des usines italiennes et rend compte des observations opérées sur le terrain ; la seconde (chapitre 2 à 4) présente les éléments de synthèse et les tendances prospectives, élaborés par les chercheurs de Torino Nord Ovest.
Bonne lecture !
- 1. Jacqueline Hénard, L’Allemagne, un modèle mais pour qui ? , Les Notes de La Fabrique, 2012. Dorothée Kohler, Jean-Daniel Weisz,
Industrie 4.0, Les défis de la transformation numérique du modèle industriel allemand , La documentation française, 2016. - 2. Émilie Bourdu, Les transformations du modèle économique suédois , Les Notes de La Fabrique, 2013.
- 3. Thibaut Bidet-Mayer, Philippe Frocrain, L’industrie américaine : simple rebond ou renaissance ? , Les Notes de La Fabrique, 2015.
- 4. Louisa Toubal, L’investissement étranger, moteur de la réindustrialisation au Royaune-Uni ? , Les Notes de La Fabrique, 2017.
- 5. Thibaut Bidet-Mayer, L’industrie du futur : une compétition mondiale , Les Notes de La Fabrique, 2016. Thibaut Bidet-Mayer et Louisa Toubal, Travail industriel à l’heure du numérique. Se former aux compétences de demain , Les Notes de La Fabrique, 2016. Charles-Pierre Astolfi, Emmanuel Constantin, Antoine Moulet, Fabrication additive. Mobiliser les forces françaises , Les Docs de La Fabrique, 2016. Charlet V., Dehnert S., Germain T. (sous la dir. de), Industrie du futur : progrès technique, progrès social ? Regards franco-allemands , La Fabrique de l’industrie, Fondation Jean Jaurès, Friedrich Ebert Stiftung, 2017.
- 6. Voir Colloque de Cerisy, « Le travail en mouvement », septembre 2018.
Préface
Pour les médias et l’opinion publique, la vision de l’industrie du futur, appelée 4.0, est dominée par la nouveauté technologique : robots, intelligence dite artificielle, internet des objets. Il faut remercier la Fabrique de l’industrie de n’avoir jamais cédé à cette focalisation exclusive, en mettant le projecteur sur les dimensions économiques, sociologiques et même culturelles des mutations en cours, en réalité tout aussi fascinantes.
La publication de ce livre en est une nouvelle illustration. Le voyage, passionnant, que nous proposent ses auteurs nous emmène dans des usines italiennes (grandes unités du Nord, surtout) en pleine mutation technique. Mais son vrai sujet est le devenir des organisations et surtout du travail, qui fait l’objet d’une deuxième partie riche de faits mais aussi d’idées, de concepts. Or, du travail dans le nouveau monde numérique, on en parle bien peu ! Une mini-industrie de rapports prospectifs a émergé à propos du futur de l’emploi, abordé de manière souvent bien mécaniste, comme si la technologie agissait directement sur le volume et la nature de l’emploi sans passer par la médiation des choix d’organisation, ni par les boucles macro de la redistribution. Mais les rapports sur le travail sont bien moins fréquents. Et ceci pour une raison simple : on ne sait pas grand-chose ! Certes le discours 4.0 s’accompagne rituellement d’une rhétorique sur l’importance cruciale du capital humain, la nécessité d’aller vers un travail plus collaboratif, un management moins hiérarchique. Ce mot « rhétorique » n’est pas péjoratif sous ma plume, car une mutation aussi polymorphe a besoin d’un récit, et le récit dominant est plutôt positif, même s’il tend à oublier que le conflit est une dimension inévitable et saine du progrès.
Mais il a impérativement besoin d’être challengé par l’observation du terrain, la prise en compte du réel dans sa complexité. C’est le paradoxe de notre société dite de transparence. Le cœur de la mutation est la prolifération sans précédent de données, sur les machines, les procédés, les usages, les comportements eux-mêmes. Mais ces masses de données ne nous disent rien ou presque rien sur la réalité subjective du travail, ou du fonctionnement des collectifs. Le rêve caressé par certains d’une sociologie panoptique, d’une sorte de « sociologie du drone » en quelque sorte, suivant les humains à la trace par la donnée est au pire inquiétant, au mieux utopiste ou naïf. Plus que jamais, il faut aller <voir, sortir des bibliothèques et oublier un moment les écrans, pour le « plein air » de l’observation. C’est pourquoi un voyage comme celui de ce livre est précieux, et devrait en appeler beaucoup d’autres.
Que nous apprend-il ? Je retiens trois mots-clés. Primo, la diversité. La numérisation, mais aussi d’autres changements (matériaux, production additive) sont génériques, et créent des effets de transversalité qui dessinent un paysage de plus en plus complexe, irréductible notamment aux notions anciennes de filières. La diversité concerne aussi les choix d’organisation, dont le répertoire semble s’élargir sans cesse. Le taylorisme ou le toyotisme étaient évidemment des fictions simplificatrices, mais ces fictions correspondaient quand même à des structures fortes, dont il semble aujourd’hui très difficile de trouver l’équivalent. Le livre pose la question : est-ce transitoire ? est-ce un effet de myopie ? Pour ma part, je ne le crois pas.
Deuxième mot-clé : l’ambivalence. Depuis au moins un demi-siècle, une des disputes centrales de la sociologie du travail, en France comme en Italie, tourne autour du transfert des connaissances humaines vers les machines, et de l’aliénation qui en résulterait pour le travailleur dépossédé. Cette idée d’une sorte de jeu à somme nulle où l’intelligence incorporée dans les machines serait une perte pour les humains m’a toujours semblé absurde, même si, bien sûr, ce jeu redistribue profondément les compétences et les qualifications. Le livre aborde ces sujets avec des lunettes dépoussiérées, montrant que, plus que jamais, la technologie produit des effets ambivalents. Elle ouvre aussi bien la possibilité de tâches considérablement enrichies que celle d’un ultra-taylorisme, où l’opérateur peut accomplir sa tâche en ayant littéralement la tête ailleurs, y compris lorsque son travail est dit « augmenté », par une tablette par exemple.
Autre mot-clé : culture. On oublie trop souvent que l’informatisation a signifié d’abord l’irruption massive de la culture de l’écrit dans l’univers oral des ateliers. Et la question de savoir quelle sera la place respective des cultures technologiques spécialisées, des compétences génériques (abstraites, langagières), sans parler de cette troisième dimension du « talent », est une des plus cruciales du moment. C’est aussi l’une de celles qui est la plus subtilement discutée dans le livre.
Un dernier mot : l’enquête porte ici sur les sites de grandes firmes multinationales, essentiellement dans le Piémont et en Lombardie. On attend avec impatience l’analyse du tissu de PME, de cette « troisième Italie » qui a tant fasciné les chercheurs et les industriels dans les années 1990. Comment ces deux mondes s’articulent-ils ? Comment s’opère la modernisation et comment évolue le travail dans ces entreprises de niche orientées vers la qualité et la différenciation ? Ces questions sont majeures pour l’Italie, mais aussi pour l’Europe en général.
Pierre Veltz
Académie des technologies
Introduction à l’édition française
Après un démarrage à vitesse variable, l’industrie 4.0, et plus généralement la transformation numérique, occupe désormais un espace de choix dans le débat public de tous les grands pays européens. Les raisons de cet intérêt sont multiples : d’une part, l’urgence qui a saisi les gouvernements appelés à fournir des outils concrets aux industries nationales pour affronter un changement de paradigme qu’il devenait difficile d’ignorer ; d’autre part, le rôle joué par les partenaires sociaux, les universités, les organisations de soutien au développement des entreprises et les think tanks, qui ont alerté sur le changement en cours, changement qui était de toute manière en train d’advenir avec ou sans politiques publiques de soutien.
Ce débat, parfois un peu trop théorique, parfois un peu trop prospectif, a cependant eu plusieurs mérites, parmi lesquels : ramener le projecteur sur le secteur manufacturier européen en tant que moteur central de nos économies ; signaler la lenteur avec laquelle nos entreprises s’adaptaient à l’innovation technologique ; souligner le besoin urgent de réfléchir sérieusement à l’avenir du travail et de la protection sociale.
Au sein du débat européen, le discours sur l’industrie du futur présente en France des particularités. Il se réfère à l’open innovation, désormais considérée comme un mécanisme puissant pour amener l’innovation numérique au cœur de l’entreprise, la faire pénétrer dans la structure même du système industriel national pour le modifier en profondeur. C’est cette vision particulière, voire de parti pris, qui a suscité l’intérêt d’Inwibe (voir infra p. 57) pour le sujet que nous traitons ici.
À la différence de ce qui se passe dans les grandes entreprises, dotées de puissantes capacités financières et industrielles, les PME ne peuvent pas faire face à l’innovation numérique avec des perspectives de retour sur investissements conventionnelles. Cela ne signifie évidemment pas que les technologies disruptives ou les méthodes telles que l’innovation ouverte soient réservées aux grands opérateurs ; tout au contraire, le système industriel ne sera réellement transformé que lorsque les équipements numériques seront introduits et adoptés par les petites entreprises et lorsque l’innovation ouverte deviendra une pratique banalisée et commune.
Un modèle adapté à la petite échelle consiste à travailler sur des projets très concrets, des chantiers de dimension limitée, avec un souci d’une approche par la preuve. Il s’agit de privilégier les actions concrètes, permettant de générer rapidement une performance économique à la hauteur des investissements consentis. Des chantiers qui trouvent un terrain d’application idéal dans l’usine, car c’est en son sein que se joue le mécanisme délicat consistant à faire travailler ensemble des équipements physiques, de la haute technologie, des solutions numériques et, last but not least, l’homme – le tout en synchronie pour aboutir à une transformation réussie.
Quelle que soit la voie nationale choisie, au regard de la diversité des politiques industrielles et fiscales de soutien aux entreprises, il n’en reste pas moins que l’industrie du futur ne saurait être considérée comme une question locale. Il suffit de jeter un œil à la carte publiée sur le portail de la Commission européenne dédié au Marché unique du numérique, où sont signalés les différents programmes actifs, pour se convaincre de l’importance d’une approche transnationale de la question.
Notre recherche, qui part d’un échantillon d’usines situées en Italie, adopte cette perspective : les entreprises, que nous avons approchées par la méthode de l’enquête de terrain, font partie de groupes multinationaux, représentant des secteurs d’activités variés et des matrices culturelles diverses – française, allemande, américaine ou autre. Chaque usine, au sein de la transformation 4.0 en cours, présente des caractéristiques particulières mais aussi beaucoup de traits communs, justement parce que l’innovation technologique et organisationnelle, la rationalité des affaires et le sens du travail humain ne connaissent en réalité pas de frontières.
Les entreprises dont nous parlons dans ce volume sont grandes, voire très grandes, et en ce sens, elles ne représentent pas le modèle-type de l’entreprise italienne. Au moment où l’édition française de ce travail est publiée, Torino Nord Ovest est en train de finaliser une nouvelle phase de cette recherche qui cible, cette fois, les PME du Made in Italy. Car celles-ci, aux dires de beaucoup d’observateurs, représentent la véritable colonne vertébrale du tissu productif italien : des PME internationalisées sur des positionnements de niche à valeur ajoutée. La vague de la transformation numérique les touche désormais aussi. Cependant, déjà dans la présente étude, on peut lire certaines caractéristiques de l’industrie du futur à l’italienne : importance du concept de filière ; adaptation numérique des instruments de gestion de l’entreprise ; choix de l’automatisation et de la robotisation qui tendent non vers la production de plus forts volumes mais vers l’amélioration de la qualité du produit.
***
Ce livre est le résultat d’un voyage au sein d’un échantillon d’entreprises italiennes qui a commencé en 2014 et s’est achevé au printemps 2016. Bien avant le lancement du plan Impresa 4.0, dit aussi Plan Calenda du nom du ministre qui l’a conçu, ces entreprises étaient déjà entrées dans le changement de paradigme impulsé par l’industrie 4.0 en matière d’adaptation technologique et culturelle. Elles avaient sous les yeux les implications d’un changement qui concerne la façon de concevoir les biens industriels et de travailler dans les usines et les bureaux. Un changement qui concerne aussi le rapport entre l’homme et le robot, ou encore la conception d’usines toujours plus flexibles, durables, ergonomiques et intelligentes, en un mot smart. Un changement qui concerne enfin les relations des entreprises entre elles, car cette transformation qui touche d’abord les grandes entreprises se diffuse progressivement vers les petites et moyennes, modifie les chaînes de valeur et d’approvisionnement, ainsi que les compétences professionnelles qui sont demandées pour y travailler.
Face à ce scénario de transformation rapide et profonde, soutenu par d’importants financements européens, comment l’industrie italienne, compte tenu de ses caractéristiques propres au sein de la division internationale du travail et des chaînes de valeur mondialisées, intègre-t-elle la révolution numérique ? Pour répondre à cette question, nous avons retenu un angle de vue particulier : pas seulement le potentiel technologique, ni les résultats économiques, mais le changement des processus de travail au sein des usines – quelles transformations déjà observables ? Quelles adaptations ? Quelles anticipations pour l’avenir ? En résumé, ce livre raconte l’industrie 4.0 à travers ceux qui la font et ceux qui en gèrent les effets.
Pour aborder ce thème, la littérature académique est d’un appui limité. La question du travail au sein des usines intelligentes n’y est souvent abordée que de façon extrêmement générale et théorique. Il y a un écart entre l’abondance des considérations portant sur la production intelligente et celles relatives aux conditions de travail qui s’y rapportent. En conséquence, nous avons fait le choix d’une prise de vue à contre-jour : interroger les silences, questionner ce que ni la littérature, ni même les interviews réalisées ne disent ou ce qu’elles ne disent qu’en partie, en allant au-delà de la parole de nos témoins et de ceux qui se situent du côté du management de l’entreprise.
En effet, les signes de la révolution technologique et organisationnelle des usines, dont il est tant question dans la littérature économique, académique et les médias, ne sont en réalité perceptibles que dans quelques-unes des entreprises que nous avons visitées ou dans certains départements de celles-ci, même si une orientation vers la « production intelligente » existe de façon transverse et diffuse. Des différences d’intensité notables existent dans l’évolution en cours selon les secteurs et les établissements. Ce constat renvoie à la nécessité d’aller au-delà du caractère unique de chaque usine pour s’intéresser aux filières de production, elles-mêmes fort différentes les unes des autres.
Parmi les cas examinés, il y a une grande variété de produits et de marchés. On trouvera plutôt ici de grands établissements de l’industrie automobile, mécanique, navale, de la chimie, de l’énergie, de l’électronique, de la robotique ou des composants avancés, ou encore des services à l’industrie (logistique ou recherche). Ces établissements ont des statuts très différents selon le type d’entreprises auxquelles ils appartiennent : établissements uniques et indépendants, têtes de filière industrielle, filiales de multinationales, groupes italiens. Ces usines ont des caractéristiques de production propres à leur secteur d’activité : pièces uniques, à la commande, séries limitées ou plus larges, services à l’industrie ; cependant, aucun des établissements visités n’est vraiment représentatif de la production de masse. Enfin, ces usines se situent à différents niveaux de maturité concernant l’intégration des nouvelles technologies.
Cet échantillon n’a donc pas la prétention de représenter l’intégralité du paysage productif italien. De par sa diversité, il permet cependant d’évaluer où et comment le paradigme de « l’usine intelligente » pénètre au sein du système industriel italien, et s’il représente une tendance lourde pour le devenir industriel du pays. Du fait de leur caractère exploratoire, les réflexions qui suivent ce « voyage au pays des usines » n’ont pas l’ambition d’apporter des conclusions, mais de fournir quelques pistes utiles pour poursuivre les recherches sur l’usine et le travail 4.0.
Annalisa Magone, Fiamma Ferrero
Juin 2018
Méthode de l’étude et remerciements
Ce livre est basé sur une recherche réalisée par Torino Nord Ovest, commandée par IAL Nazionale, FIM CISL Piemonte, Istituto Superiore Mario Boella et financée aussi avec le soutien du Fondo Fapi.
Torino Nord Ovest est une entreprise sociale qui effectue des recherches, du conseil et de l’évaluation dans le domaine socio-économique, et formule des propositions originales. C’est un lieu de recherche appliquée et de circulation d’idées sur les principaux thèmes de l’agenda public italien et européen.
IAL Nazionale est le plus grand réseau d’entreprises sociales intervenant en Italie dans le champ de la formation professionnelle et continue. Il a été fondé en ١٩٥٥ par la Confédération italienne des syndicats de travailleurs (CISL).
FIM CISL Piemonte est la section piémontaise de la fédération syndicale des travailleurs de la mécanique, adhérente de la CISL.
L’Istituto Superiore Mario Boella est un centre de recherche appliquée et d’innovation, centré sur les Technologies de l’information et de la communication (TIC). Il a été créé en ٢٠٠٠ par convention entre la Compagnia di San Paolo et l’École polytechnique de Turin.
La présente étude doit beaucoup à la disponibilité de nombreux responsables de production, conception, innovation, ressources humaines, relations industrielles, qui nous ont accueillis et accompagnés dans leurs établissements et auxquels nous adressons nos plus vifs remerciements. Compte tenu du temps écoulé entre la publication italienne et l’édition française, il est possible que les fonctions des personnes citées aient pu évoluer, nous les prions par avance de nous en excuser.
Raffaella Alberi, Claudia Badalì, Manuela Bozzolan, Luca Merlo, Carlo Pellegrini (Alstom) | Mauro Brega, Alessandro De Gioia, Gian Paolo De Poli, Michele Laterza, Antonio Padovani, Davide Schinetti (Avio Aero) | Renato Marabini, Alberto Signori (Brembo) | Cesare Murgia, Antonio Lucci, Dario Venditti (Centro Sviluppo Materiali) | Tullio Tolio (Cluster Fabbrica Intelligente) | Arturo Baroncelli (Comau) | Franco Gallo (Consulman) | Mario Morgese, Pietro Palma, Carlo Serpentino (Ducati Motor) | Manuele Mattucci (EFFRA) | Luigi Galante, Nevio Di Giusto, Edoardo Rabino, Alberto Filippini (FCA) | Guido Giletta (Giletta) | Paolo Baracchi, Claudio Boschetti, Barbara Eleota, Luca Pipino (Kuehne+Nagel) | Fiamma Ferrero, Damien Heiss (Inwibe) | Frediano Checchinato, Paolo Mulassano, Maurizio Spirito (Istituto Superiore Mario Boella) | Valerio De Martino, Roberto Luciano Forresu, Stefano Gadda (Pirelli) | Marco Cusinato, Roberta Giani, Elena Privitera (Santer Reply) | Claudia Filippone, Antonio Pingiori, Gianandrea Pischedda (Rina, Fincantieri) | Paolo Bessone (Solvay) | Marzio Brambilla, Sergio Mariani, Pietro Palella (STMicroelectronics) | Giusi Di Bartolo, Bruno Torresin (TRM).
Tous nous ont aidés à recueillir des informations et à vérifier leur exactitude, quand celles-ci pouvaient leur être explicitement attribuées. Cependant, toutes les analyses, les références à des modèles économiques et sociologiques, et les comparaisons entre les méthodes et les lieux de travail relèvent exclusivement de la responsabilité des auteurs de l’étude.
Le livre est le résultat du travail collectif de plusieurs auteurs. En particulier, Annalisa Magone a écrit Voyage au pays des usines , Salvatore Cominu a écrit Le travail 4.0 et Tatiana Mazali La personne 4.0 . Les contributions de Giampaolo Vitali et Antonio Sansone sont présentes à différents points du livre. En particulier, Giampaolo Vitali a traité les modèles économiques de l’entreprise et l’impact des technologies habilitantes, tandis qu’Antonio Sansone a développé le raisonnement sur la représentation, la participation et la transformation des compétences. Le dernier chapitre, Interprétations et ouverture , a été partagé par les différents auteurs.
Les différentes contributions qui forment cet ouvrage, si elles dérivent d’une matrice commune, portent cependant la trace de la sensibilité de chacun de leurs auteurs et peuvent refléter des interprétations distinctes. Ce livre offre donc des grilles de lecture différentes sur des faits identiques. Il est d’ailleurs communément admis que les premiers effets de la transformation industrielle, dont nous sommes témoins, suscitent des discussions passionnées, alors même que ses conséquences à plus long terme nous restent encore inconnues.
Voyage au pays des usines
« Une usine sans hommes serait une usine qui tiendrait debout toute seule. Tout simplement impossible ! » Celui qui prononce cette phrase est le responsable de production d’un site industriel que nous visitons dans l’arrière-pays turinois, au cours des premières étapes d’un voyage qui durera plus d’un an, à la rencontre des nombreuses usines italiennes de grands opérateurs industriels. Le but de ce voyage est de vérifier dans quelle mesure l’industrie italienne intègre le nouveau modèle européen d’« usine intelligente », en passe de devenir le cadre conceptuel du renouveau industriel européen. Lorsque débute ce voyage, la feuille de route Factory of the future à l’horizon 2020*7, fruit du travail de l’EFFRA (European Factory of the Future Research Association)8, qui représente un espace de discussion entre les principaux acteurs européens, vient d’être publiée. Le débat national italien n’en est alors qu’à ses prémices, bien qu’un cluster9 dédié à ce sujet ait été constitué et qu’un plan gouvernemental soit en phase d’élaboration10.
Quand démarre notre voyage, nous n’avons pas d’idée précise sur ce que nous allons trouver dans les usines, et nous ignorons si les grands sites industriels que nous avons prévu de visiter seront représentatifs d’un système industriel où dominent les petites entreprises et où l’innovation pénètre selon des modalités particulières. C’est l’une des raisons pour lesquelles nous entamons ce voyage en passant par la « porte de service » et demandons à rencontrer Comau, un fabricant de ces systèmes de production automatisés qui forment la base technologique de l’usine intelligente.
L’usine des robots
Comau pour Consorzio Macchine Utensili (Consortium Machines-Outils) est une entreprise de 9 000 personnes dont le cœur et la tête se trouvent à Grugliasco, dans la rusty belt de Turin (Piémont).
Son histoire est assez mythique. Elle fut fondée en 1973 par un ensemble d’entreprises turinoises qui suivirent Fiat dans la construction de l’énorme complexe de Togliatti (AvtoVaz), sur la Volga en Russie, d’où allaient sortir les automobiles VAZ commercialisées sous la marque Lada11. Progressivement, Fiat en acquit la majorité des parts, puis la totalité du capital. Aujourd’hui, Fiat Chrysler (FCA Group) n’en est plus l’unique client : Comau sert l’actionnaire-maison, mais aussi d’autres constructeurs automobiles12 et d’autres secteurs industriels.
L’entreprise repose sur trois divisions : assemblage qui fournit des solutions pour les chaînes de production ; machining qui propose des machines-outils et des systèmes d’automatisation ; enfin, robotique et autres produits d’automatisation industrielle tels que technologies laser, pinces de soudure ou véhicules industriels autonomes. Auxquelles s’ajoutent tous les investissements dans les technologies numériques pour le monde industriel. Les deux premières divisions construisent des systèmes personnalisés pour chaque client.
Les systèmes de production automatisés sont depuis longtemps l’une des pierres angulaires du savoir-faire industriel piémontais : il faut, par exemple, des centaines de robots de grande dimension pour fabriquer la carrosserie d’une voiture, et une ligne de production robotisée fabriquant des moteurs mesure au moins 100 mètres.
La division robotique est en pleine expansion, principalement au service du monde automobile. En 2009, la crise a eu un fort impact sur le chiffre d’affaires de l’ensemble du secteur, mais la reprise a été rapide. Dans les jours où nous visitons l’usine, la polémique fait rage autour d’une annonce faite par Foxconn : le fabricant chinois d’Ipad a déclaré vouloir introduire dans ses usines un million de robots. On pourrait croire à une boutade, mais l’annonce ne doit pas être sous-estimée : la robotique se développe à grande vitesse et d’immenses possibilités s’ouvrent ainsi aux acteurs du secteur, parmi lesquels Comau, l’un des huit producteurs mondiaux capables de réaliser des robots de toutes dimensions – des petits (3 kilos de charge) jusqu’aux grands (800 kilos de charge).
Le défi que doit aujourd’hui relever ce secteur, c’est de réussir à ouvrir les cages pour rapprocher les hommes des robots sur les lignes de montage et d’assemblage. Les huit grands opérateurs y répondent chacun à leur manière. Comau, par exemple, a lancé Aura, une technologie propriétaire de robot collaboratif doté d’un revêtement sensoriel qui permet à l’opérateur de travailler en toute sécurité. Les produits se modifient en même temps que le marché. Parmi les derniers robots de Comau, Racer laisse entrevoir les trois orientations technologiques et commerciales suivies par ce secteur. En premier lieu, le niveau des prestations : il s’agit de développer de nouveaux produits, vite… très vite. Deuxièmement, la compétitivité : contenir les coûts de production grâce à la recherche sur les matériaux et le nombre de composants. Enfin, le style, c’est-à-dire l’intégration du design dans la conception. Comau s’est directement inspiré du corps humain, si bien que le robot achevé ressemble à un bras avec des tendons. Il y a à Turin une formidable tradition du design : on trouve peu d’endroits dans le monde capables de conjuguer de façon aussi exemplaire style et technologie.
Pendant que nous descendons à l’atelier, nos hôtes nous expliquent la différence entre un robot anthropomorphe et un humanoïde ; nous traversons un vaste hangar où les équipes travaillent autour de nacelles jaunes qui se déplacent sur des rails. Monter un robot représente un travail méthodique, fait à la main pour une grande part. La zone de stockage est impressionnante avec ses rangées de robots bossus, d’un rouge flamboyant, qui attendent tranquillement à côté de leur « valise » noire contenant leurs commandes de contrôle. Impressionnante aussi la zone des « cages » où ces géants sont testés avant livraison. Ils sont vraiment beaux et quand ils se retournent vers nous, on ne sait plus trop qui observe qui.
L’usine de l’architecte-star
En entrant chez Pirelli, 5e producteur mondial de pneumatiques, à Settimo Torinese (entre Turin et Milan), ce qui frappe en premier lieu est l’architecture du site. Celui-ci, construit en 2010 à partir de la restructuration de deux usines préexistantes, est la traduction tangible d’une transformation tant physique qu’organisationnelle. Il est traversé, de part en part, par une colonne vertébrale – dont le nom la Spina ou Arête n’est pas choisi par hasard – conçue par Renzo Piano, l’architecte du Centre Pompidou à Paris entre autres. La patte de l’architecte-star est perceptible de l’extérieur, mais encore davantage à l’intérieur lorsque l’on évolue sur les clairs parquets en bambou. « La Spina » n’a rien d’une prouesse décorative, elle est avant tout fonctionnelle : elle héberge les bureaux et les services aux salariés, et sert de point de jonction, via quelques passerelles suspendues, avec quatre mini-usines : car sud, où le process de production demeure traditionnel, c’est-à-dire subdivisé en îlots qui effectuent chacun une fraction du processus ; cell production, construit autour d’une ligne de production « cellulaire » hautement automatisée qui intègre en un seul flux lean l’ensemble de la fabrication d’un pneumatique, depuis la préparation des composants jusqu’à l’emballage, depuis la vulcanisation du caoutchouc jusqu’au contrôle qualité ; next mirs (pour Modular Integrated Robotized System), ligne entièrement robotisée ; et enfin, la salle de mélangeage où sont réalisés les composés caoutchoutés qui alimentent tous les autres processus.
L’établissement de Settimo est le seul de sa catégorie dans le monde Pirelli. Non seulement parce qu’on y expérimente l’innovation organisationnelle qui se diffusera ensuite dans le reste du groupe, mais aussi parce qu’il résulte d’un accord équilibré entre la direction, les représentants des salariés et le territoire. En 2008, en pleine déflagration de la crise, Pirelli décide d’investir dans la modernisation des équipements, met en œuvre un ambitieux plan de formation des salariés et réorganise le personnel des deux usines originelles qui fusionnent en une seule. Plus moderne. Plus complexe. Plus sûre. Plus innovante. Les 1 080 ouvriers qui travaillent aujourd’hui à Settimo avec 120 cols blancs, sont le résultat de l’intégration de deux populations très différentes en matière de compétences et cultures d’entreprise : l’une chargée à l’origine de la fabrication de pneumatiques de moyenne gamme pour véhicules légers, l’autre en charge des pneumatiques pour les poids lourds.
« Il fallait actualiser les compétences techniques, construire un vocabulaire et des comportements communs, réécrire les horaires de travail et les modalités des pauses, harmoniser les conceptions de la qualité… c’était un changement complet de paradigme », nous explique Valerio De Martino, le jeune responsable RH du pôle de Settimo qui a suivi toute la transformation. Ce qui manquait, ce n’était pas tant les compétences sur les produits que sur les process : avec une population d’un âge moyen de 40 ans et d’une ancienneté de 20, il n’y avait pas vraiment de problème de compétence technique. Mais quand une usine effectue une conversion, en passant d’une production de moyenne gamme à des productions haut de gamme qui équiperont des Lamborghini, des Ferrari ou des Maserati, en petites séries et à variation rapide, c’est la flexibilité des opérateurs qui devient centrale, ainsi qu’un état d’esprit axé sur la qualité.
La clé du changement a reposé sur un programme d’innovation sociale portant sur la sécurité, la formation et la responsabilisation individuelle. « Nous devions travailler sur les comportements parce que nos opérateurs disposaient d’une expérience où s’étaient sédimentées des vieilles pratiques et habitudes. Il ne s’agissait pas de bâtir une nouvelle usine, en embauchant un nouveau personnel, mais de saisir l’opportunité de la modernisation pour opérer une transformation profonde. » Au sein du personnel, sont alors identifiés des « agents du changement » qui sont formés en premier, afin de devenir de nouveaux modèles pour l’action. Le système prend forme et s’enracine, le nouveau style produit des résultats concrets, l’absentéisme et les accidents du travail diminuent : « Nous voulions devenir l’usine de pneumatiques la plus sûre et la plus compétitive au monde. En 2010, nous commencions à peine et l’objectif nous paraissait très lointain, mais aujourd’hui nous y sommes presque. »
Quand nous voyons la ligne automatisée, tout s’éclaire. Les ouvriers travaillent autour de grands modules multifonctions ; le pneumatique naît à partir d’une installation qui ressemble à une grande machine typographique : un parallélépipède le long duquel sont placées de grosses bobines (les « cartouches ») d’un composé caoutchouteux ; la machine déroule les couches et les colle les unes sur les autres comme sur une galette – nappe carcasse, nappe pour la ceinture sommet, bande de roulement, renforts dans les flancs. Le pneu « brut », joufflu et encore privé des rainures qui lui confèreront sa caractéristique, est alors convoyé vers les fours de vulcanisation où il acquerra sa forme finale via un moule. De là, il finira sa course le long d’un toboggan hélicoïdal entre les mains d’un contrôleur qui, en quelques regards ciblés, en déterminera la qualité.
Dans d’autres espaces de cet important pôle industriel, l’innovation technologique prédomine : on y expérimente le cyber-pneu, avec des capteurs et des puces dans le pneumatique, on étudie des matériaux qui amélioreront sa composition, on met au point des programmes de réalité virtuelle pour s’entraîner aux futures conditions de production. Le bâtiment lui-même avec ses 400 mètres de panneaux photovoltaïques et ses réservoirs de récupération d’eau de pluie est à haute performance énergétique et environnementale. Mais ici, dans cet atelier, on mesure plus qu’ailleurs le niveau d’équilibre atteint entre artisanat et industrie, tradition et aptitude au changement. « En Italie plus encore qu’ailleurs, il faut veiller à ce que les personnes soient “engagées”. Tu peux avoir les meilleures technologies et les meilleurs processus, mais le plus important, c’est de réduire la distance entre les managers et les opérateurs, en mettant en évidence l’importance de la contribution de chaque individu. »
L’usine qui se renouvelle
Chez Avio Aero, spécialiste des moteurs pour le secteur aéronautique, sur le site de Rivalta dans la grande banlieue de Turin, nous découvrons une usine immense. Mais grâce à la diminution du volume des machines, il devient possible de consacrer ces espaces à de nouvelles productions. Pendant notre visite, des travaux sont en cours pour mettre en place une nouvelle ligne qui produira 8 000 engrenages sur 1 000 m2, en remplacement d’un système qui en produisait 7 500 dans un espace deux fois et demi supérieur. Dans l’usine du futur, ces unités de production plus petites et plus efficientes communiqueront entre elles, permettant une synchronisation optimale entre l’arrivée des composants et les étapes de montage, avec pour résultat une réduction des délais.
Mais la clé pour faire véritablement entrer le futur dans l’usine n’est pas tant la mise à jour technologique que la transformation anthropologique de la figure ouvrière, en commençant par l’âge et la formation des travailleurs, qui débouche sur un changement de culture d’entreprise. À la division « Transmissions », l’âge moyen du personnel diminue, suite à l’intégration de jeunes : 35 % des opérateurs ont moins de 30 ans et une part égale se situe entre 30 et 40 ans. Les premiers sont souvent issus des instituts technologiques avec lesquels Avio Aero a conclu des partenariats, afin de fluidifier le passage de l’école vers le monde professionnel. La sélection des candidats suit une procédure complexe et coûteuse pour l’entreprise : elle commence par un stage de formation, se poursuit par un passage dans les ateliers au cours duquel les candidats sont évalués par des superviseurs, afin de valider si l’investissement consenti par l’entreprise sur les personnes sera rentable… et rentable à court terme.
Les process et les machines se sont considérablement modifiés ; la production est devenue reproductible, traçable et prévisible. L’expérience humaine ne demeure un facteur clé que dans les cas où les systèmes automatisés ne permettent pas de garantir ces trois qualités. Le responsable de la production, Davide Schinetti, nous présente le chef d’un îlot qui vient d’être monté – un simple carré sous la structure métallique du hangar comme une tache blanche ressortant sur un fond noir : il manœuvre simultanément plusieurs machines qui effectuent diverses opérations sur une pièce protégée par une coupole en verre. Autour de lui, il y a l’atelier qui attend d’être transformé, avec ses rangées de machines mono-fonction qui sont là depuis de nombreuses années et sont désormais dépassées. D’un simple coup d’œil, on peut percevoir chez Avio Aero tous les stades de la transformation en cours : l’ouvrier d’autrefois penché sur son tour, aussi bien que l’opérateur d’aujourd’hui qui travaille en se mouvant constamment et qui, changeant de position, change aussi de perspective. « Ce n’est plus un expert, mais il sait un peu de tout. De notre point de vue, c’est une compétence distinctive et nous avons donc choisi de placer uniquement des jeunes sur les nouvelles lignes. »
Dans les procédés thermiques ou de galvanisation, un ouvrier expérimenté pouvait traditionnellement apporter une réponse à une interrogation sur les traitements en une semaine ; aujourd’hui, une nuit suffit, car c’est un logiciel développé à partir de l’expérience des opérateurs qui fait le travail. Grâce à cette translation du cerveau de l’opérateur vers le logiciel, l’expérience cesse d’appartenir à un seul individu, mais se transfère à toute l’équipe et devient, dès lors, accessible à tous. C’est ainsi que se modifie la manière dont l’information est produite et consommée : avant, il y avait le papier que personne ne consultait, puis il y a eu l’intranet d’entreprise, aujourd’hui on a le réseau social au sein d’une entreprise élargie, qui soude un groupe de 300 000 personnes.
En effet, en 2013, Avio a été acquis par General Electric (GE), changeant au passage son nom en Avio Aero. GE en a fait son centre d’excellence mondial pour les transmissions mécaniques ; depuis lors, les deux entités tentent d’apprendre l’une de l’autre, en particulier en matière de R & D.
Gian Paolo De Poli, responsable de l’équipe qui assure la transformation de l’innovation technologique en processus de production avancés – les Allemands parlent de « technologue de production » – nous explique que la recherche chez Avio Aereo est portée par des ingénieurs spécialisés dans les disciplines scientifiques de base, telles que l’aérodynamique, l’échange thermique ou les matériaux. Dans chacune de ces disciplines fondamentales, on trouve « des sages qui connaissent les orientations du futur », des super-experts qui disposent d’un réseau collaboratif d’informateurs dans les centres de recherche et les universités du monde entier. Le secteur aéronautique est, d’une façon générale, extrêmement collaboratif, car personne ne peut maîtriser toute la connaissance nécessaire.
En Europe, les finalités poursuivies par l’innovation sont au nombre de trois : compétitivité, sûreté et préoccupation environnementale, et elles sont interdépendantes. Pour atteindre ces objectifs, on introduit la numérisation et la simulation en conception comme en production. En prenant comme année de référence l’an 2000, le délai de développement d’un nouveau produit chez Avio Aereo a été réduit de moitié : en une nuit, on peut simuler le fonctionnement d’une turbine, là où il fallait auparavant des semaines. En conséquence, les liens entre conception et production se sont grandement resserrés, conduisant à la constitution d’équipes d’ingénieurs multidisciplinaires et plus équilibrées que par le passé. Nous demandons si cela signifie que des non ingénieurs, voire des designers ou des littéraires, figurent aussi au sein de ces équipes. « Si vous voulez me faire dire que dans l’équipe qui conçoit un avion, il y a de la place pour un musicien de jazz, la réponse est clairement non ! nous dit De Poli, en souriant. Ou pour être plus précis, nous en avons bien un, mais il a un diplôme d’ingénieur. »
L’usine additive
Les problèmes d’excès d’espace ne concernent pas l’unité qu’Avio Aero a ouverte depuis quelques années à Cameri, près de Novara (Piémont), et qui est encore en rodage au moment où nous la visitons. Cameri est le fruit d’un effort de détection de start-ups, lancé par Avio Aereo en 2007 afin de répondre à un projet de recherche. C’est ainsi que l’entreprise tombe sur Protocast, une micro-entreprise de 5 salariés dans un appartement de 320 m2, qui se consacrait à la fabrication additive pour le biomédical, l’automobile et l’aéronautique. Aujourd’hui, l’unité de Cameri peut abriter 60 imprimantes 3D et représente l’un des plus grands établissements d’Europe dédié à cette technologie.
Dans la salle de réunion où Alessando De Gioia, le directeur, nous reçoit, il y a une armoire d’où il sort des échantillons de bijoux, certains gris opaque et rugueux, d’autres brillants comme du strass. Le premier type est sorti de ses « imprimantes », même s’il déteste qu’on les nomme ainsi. Les avantages de cette technologie sont évidents : économiser des matériaux et du temps de travail. Il nous met en main une pale de la turbine d’un Boeing 787 construite de manière traditionnelle et son équivalent produit de façon additive ; elles ont le même usage mais la seconde pèse environ la moitié. Dans le procédé traditionnel, il faut recourir à environ 4 kilos de matière brute pour obtenir 1 kilo de produit fini (la pale), alors qu’en fabrication additive, le rapport est de 1,5 pour 1. La fabrication additive permet également de réaliser des formes géométriques compliquées, inconcevables en production traditionnelle. Substituer l’une par l’autre présente un grand intérêt, non pour dupliquer des solutions existantes, mais pour des projets totalement innovants. « Cette unité a été pensée pour des projets conçus dès l’origine pour la fabrication additive et pour oser des solutions de design qui n’auraient jamais pu être expérimentées en production traditionnelle. »
On trouve à Cameri deux types d’imprimantes, à chaud et à froid, situées dans deux grandes pièces au rez-de-chaussée du hangar. Pour les faire fonctionner, peu d’ingrédients sont nécessaires : des poudres, le logiciel, le modèle en 3D et le cerveau des ingénieurs. L’imprimante elle-même ressemble à un grand réfrigérateur ou à un gros lave-linge avec un hublot. L’opérateur doit simplement enclencher la machine et faire la maintenance prévue. Les machines n’ont pas besoin d’être surveillées et fonctionnent 24 heures sur 24, même lorsqu’il n’y a personne dans l’établissement. Il faut seulement veiller à suivre très précisément la check-list au démarrage et à protéger le mélange chimique contre toute contamination extérieure. Au terme de « l’impression », le produit sort « brut », encore emprisonné dans sa gangue de poussière, mais très proche de sa forme finale, comparé à une pièce issue d’une fusion et d’un moule.
Au moment de notre visite, 15 personnes travaillent à Cameri, dont 10 opérateurs. De Gioia en attend prochainement deux nouveaux. Tous sont très jeunes, le plus âgé a 45 ans. De Gioia confie avoir « beaucoup hésité à l’embaucher, mais il avait une compétence en maintenance électromécanique et il était important pour l’entreprise de progresser sur ce point ». Tous les autres ont entre 26 et 28 ans. Peu de personnes sur le marché du travail maîtrisent cette technologie, et en conséquence De Gioia n’embauche que des jeunes diplômés qu’il tente de choisir parmi les meilleurs et les plus créatifs : « Si tu formes un jeune selon tes méthodes, comme il n’a pas de structure mentale préétablie, il apprendra la logique de fonctionnement de ces machines bien mieux qu’un individu plus expérimenté, mais qui a déjà une forme mentale fixée. Paradoxalement, celui qui ne sait rien ou pas grandchose représente pour nous un avantage. » Cameri n’a de toute manière pas vocation à employer de grands effectifs, et il s’agira probablement plus d’ingénieurs que d’opérateurs. Mais il pourrait y avoir des effets positifs sur les emplois indirects.
La figure la plus essentielle de l’établissement est l’expert processus : le seul à savoir régler précisément les plus de 300 paramètres qui permettent à cette technologie de fonctionner. Depuis quelque temps, il est flanqué d’un apprenti. Standardiser au maximum est l’obsession de De Gioia, car « il est trop risqué de faire reposer le sort de toute une entreprise sur les compétences d’une seule personne ». Par « standardisation », il n’entend pas seulement le respect méticuleux de la procédure, mais encore la constitution d’un répertoire de bonnes pratiques capables d’en assurer à tout moment la reproductibilité. « Je dis toujours que, tous les jours, on apprend quelque chose de nouveau et qu’il faut l’écrire : que chacun le fasse pour ses propres activités et puis, nous trouverons un moyen de les formaliser et de les rendre accessibles à tous. »
Cette question de la transmission du savoirfaire individuel est loin d’être simple, et encore moins secondaire. Selon Nevio Di Giusto, longtemps directeur du Centre de recherche de Fiat, « les outils digitaux qui nous assistent dans le travail de production nous permettent de prendre de la hauteur et de nous élever de l’outil au process. Mais en n’opérant plus de manière physique sur les problèmes quand ils se posent, nous risquons de perdre la capacité à reconnaître les erreurs. » Di Giusto fait ici référence à la notion de savoir-faire, qui entrait dans les mains et la tête de l’opérateur à travers l’expérience, les erreurs, et le chef qui corrigeait, ou pour le dire autrement, par le fait de vivre en temps réel les problèmes et leur correction. Aujourd’hui, on tient ce lent processus d’apprentissage pour acquis, puisque la machine est supposée y suppléer : « Mais quand on perd l’expérience, le problème est qu’il n’y a plus personne pour se rendre compte que l’outil se trompe. De mon point de vue, il est en train de se créer un fossé entre ceux qui savent faire, qui ont l’expérience et ceux qui devront appliquer cette expérience dans le futur. » Ce que Di Giusto résume encore de la façon suivante : les personnes dotées d’expérience ne savent souvent pas utiliser les outils numériques aussi efficacement que les plus jeunes, donc elles ont un potentiel élevé, mais une dynamique très faible. En revanche, les jeunes ont une dynamique élevée mais un potentiel bas, donc ils courent le risque de commettre de grosses erreurs dans un environnement très rapide et dénué de connaissance des risques. « Le vrai défi, c’est de parvenir à encapsuler l’expérience et la connaissance à l’intérieur de l’outil, de manière à ce que les futurs utilisateurs, qui sont beaucoup plus rapides, puissent faire plus de choses que nous, mais sans commettre d’erreurs. »
L’usine élastique
Si à Cameri, ils ont pu partir d’une page blanche, chez Alstom, à Savigliano, dans la province de Cuneo (ou Coni) en Piémont, ils ont suivi le chemin inverse.
Cette usine qui produit des trains est née en 1853, en même temps que la ligne de chemin de fer Turin-Cuneo, la deuxième après celle reliant Naples à Portici. Puis ce fut Fiat qui en prit la tête en 1970, avant de la céder à Alstom en 2000, non sans avoir préalablement développé la technologie qui a fait naître le Pendolino (rames reposant sur une technologie pendulaire permettant une grande vitesse), puis les rames ETR 450 en 1988. Après la cession de ses activités Énergie à General Electric, le groupe Alstom compte aujourd’hui dans le monde 32 000 salariés dans plus de 60 pays. En Italie, avec 8 sites et 2 700 employés, il est l’un des principaux opérateurs du secteur ferroviaire italien. Le site de Savigliano est considéré, au sein du groupe, comme le centre d’excellence mondial pour les trains régionaux et les trains à grande vitesse conçus avec la technologie pendulaire, exemple indéniable d’excellence du Made in Italy avec ses 500 trains vendus dans 14 pays.
Construire des trains est un métier difficile qui englobe tous les champs technologiques. La production est faible en volume, mais aussi complexe que celle d’un navire de croisière ou d’une plateforme pétrolière offshore. Un Pendolino est constitué de 50 000 composants différents pour un total de 900 000 pièces ; le système électrique d’un train comporte 100 000 connexions. À cela s’ajoute la pression issue des délais de plus en plus courts imposés par la commande publique : aujourd’hui, Alstom livre une rame en 13 mois à compter de la signature du contrat, puis complète la commande au rythme d’une rame par semaine.
Le secteur ferroviaire était historiquement une industrie artisanale, où la conception se traduisait par peu de dessins et où le développement se faisait essentiellement dans les ateliers, qui disposaient en général d’un personnel exceptionnellement compétent. Mais en quelques années, Alstom a complètement changé ce modèle, en mettant en place un processus strictement industriel. « La charge est extrêmement variable, nous explique-t-on au cours de l’entretien, donc l’usine recourt à du personnel temporaire en grand nombre, avec des niveaux de compétences assez faibles. » Récemment, pour faire face à une commande importante, Alstom a dû intégrer en quelques semaines 400 personnes, ce qui équivaut au nombre de salariés d’une grosse PME. Dans une configuration industrielle de ce type, on comprend aisément que la transmission de l’information doive se faire sous une forme radicalement différente de celle qui prévalait dix ou quinze ans auparavant à destination de travailleurs hyper qualifiés.
À l’époque, l’information passait du bureau d’études à la production sur la base de quelques dessins qui étaient ensuite interprétés par un personnel formidablement compétent. Aujourd’hui, grâce à l’automatisation de la production et aux outils numériques, Alstom transmet une grande quantité d’informations, immédiatement utilisables même par ceux qui n’ont pas de compétences spécifiques en mécanique ferroviaire. Chacun peut comprendre ce qu’il doit faire en consultant la tablette tactile entre ses mains ou l’écran de montage relatif à chaque poste ; la représentation en 3D du train peut être agrandie et tournée en tous sens, et comporte toutes les instructions permettant de passer de la pièce au montage. Le long de la ligne, chaque poste effectue une tâche différente : quand le travail de chacun est terminé, le chef de ligne fait avancer la rame, et le montage reprend à l’étape suivante. Le Pendolino comporte 14 étapes de montage.Touteslesinstructionsdonnéespar les écrans sont en anglais, mais les opérateurs sont capables de les comprendre, car le système est visuel, principalement composé d’icônes et aussi intuitif qu’un jeu vidéo. Des câbles avec capteurs mesurent la consommation des pièces situées dans des caissettes en bord de ligne, qui sont ainsi réapprovisionnées au fur et à mesure des besoins avec un minimum de gaspillage. En conséquence, l’opérateur fait l’objet d’un suivi très précis, qui aurait été tout à fait impossible à peine quelques années auparavant, permettant de mesurer le temps travaillé, le rythme de travail et le matériel utilisé. Au fur et à mesure de l’avancement de la ligne, est généré un rapport qui accumule les informations sur les opérations, permettant une traçabilité qualitative de l’ensemble du processus de fabrication.
Fait également partie intégrante de l’usine l’École des projets spéciaux, qui forme les ouvriers dans six domaines de compétence particulièrement sensibles dans la construction d’un train : soudage, peinture, collage, raccordement électrique, boulonnage, rivetage de la structure. La « scolarité » se compose d’une partie théorique et d’épreuves pratiques. L’un des derniers investissements est un simulateur de soudage à base de réalité virtuelle. Le soudeur enfile son masque et s’essaie à trois types de soudage, qui obtiendront des scores sur des paramètres tels que rapidité d’exécution, inclinaison, distance, etc. Aux dires des soudeurs eux-mêmes, le casque imite plutôt bien la réalité. Le simulateur favorise l’apprentissage pratique du soudeur qui s’améliore grâce aux scores obtenus, sans gâcher des matériaux.
Mais c’est au cœur de l’ingénierie de conception qu’on trouve les technologies les plus avancées, avec la virtual room. Depuis 2012, tous les projets d’Alstom sont développés à partir d’une modélisation 3D qui constitue la matrice commune, utilisée ensuite par tous les services de l’entreprise : le modèle arrive à la production, mais aussi au marketing pour la conception des catalogues, au service après-vente pour l’élaboration des manuels de maintenance, aux achats pour la liste des composants, etc. En bref, les informations sont élaborées une seule fois et émises à partir d’un centre pour venir alimenter toute la chaîne industrielle. Certes la modélisation 3D est très répandue dans l’industrie ferroviaire, mais Alstom va plus loin en intégrant la réalité virtuelle. Quand nous enfilons nos lunettes, c’est comme si nous entrions littéralement dans la cabine d’un train comme dans un nouveau jeu vidéo : « La 3D d’il y a encore quelques années servait essentiellement à visualiser, nous explique Carlo Pellegrini, ingénieur en chef. Mais aujourd’hui, elle permet en outre de concevoir et tester les multiples étapes du processus de production. »
L’usine des palais flottants
Il y a beaucoup d’analogies entre la construction d’un train et celle d’un navire de croisière. Mais pour le profane, la visite du chantier naval de Fincantieri, à Monfalcone au Nord-ouest de Trieste, l’un des plus grands au monde, produit une impression radicalement différente de celle procurée par les processus futuristes mis en œuvre chez Alstom.
Monfalcone est un site considérable de 750 000 m2, sur lequel opèrent 4 500 salariés, chiffre qui passe à 6 000 lorsqu’un paquebot arrive en phase finale et que le personnel des sous-traitants arrive sur le chantier. Fincantieri a modifié son business model dans la construction de bateaux : de constructeur en propre – il n’y a pas si longtemps travaillaient sur le chantier des charpentiers, des menuisiers, des soudeurs et des décorateurs, salariés de l’entreprise – il est devenu intégrateur et il évolue encore vers un rôle de pur maître d’œuvre, pivot de flux complexes opérés majoritairement par d’autres.
Il faut savoir que la conception d’un bateau ne naît pas dans les bureaux d’études, mais avant tout dans les mailles subtiles de la réglementation internationale. Faire respecter les normes et standards est le travail des sociétés de classification, dont les plus importantes ne sont qu’une douzaine dans le monde : elles vérifient la conformité technique des navires afin de garantir la sécurité de l’équipage, des passagers, du chargement mais aussi la protection de l’environnement marin. La prise en charge extérieure de la conformité réglementaire allège en pratique la charge du chantier, explique Antonio Pingiori, longtemps responsable du secteur maritime au Registre Italien Naval et Aéronautique (Rina)13, car celui-ci peut se focaliser sur les aspects opérationnels et commerciaux, tout en sachant que la sécurité et la robustesse dépendent de paramètres définis par la société de classification.
À partir du moment où un contrat est signé, celle-ci joue un rôle de co-conception. Puis durant toute la phase de construction, elle exerce une fonction de surveillance et elle interviendra également lors des essais techniques au moment de la mise à flots. Le troisième acteur est l’armateur, dont la tâche est plutôt commerciale mais qui n’est pas toujours un « facilitateur » de projet. En effet, entre la commande et la livraison, la construction d’un navire de croisière prend environ deux ans, durant lesquels tout peut arriver. Pendant notre visite à Monfalcone, nos accompagnateurs nous racontent comment, en une certaine occasion, alors que le navire était quasiment achevé, le chantier a reçu l’ordre d’ajouter un moteur supplémentaire, ce qui impliquait de trouver un espace où l’installer. Pour des raisons de ce type, la conception d’un paquebot et sa construction ne sont pas toujours des séquences ordonnées et successives comme pour le Pendolino d’Alstom. Il est fréquent que le bureau d’études conçoive pendant que le chantier construit, et il arrive même que les plans soient élaborés après que le chantier ait trouvé les solutions pratiques pour répondre à un imprévu. En d’autres termes, la fabrication va parfois plus vite que la conception.
Si un navire de croisière est une pièce unique, il ne faut cependant pas tomber dans le travers de croire que la construction navale est un « gros artisanat » : au vu de la complexité du processus, il s’agit bel et bien d’une industrie. En témoignent les chantiers sud-coréens qui, dans le domaine des navires marchands, sont parvenus à rationaliser et industrialiser la construction de telle manière que la notion de pièce unique n’est plus qu’un lointain souvenir. Le client achète sur catalogue un navire en série à coût contenu, car privé de toute « personnalisation ». Il n’est pas impossible d’y introduire des modifications, nous explique Pingiori, mais le coût en est si exorbitant, surtout en cours de construction, que l’armateur est dissuadé d’y recourir. Pour ces constructions « en série », les chantiers coréens disposent de bassins multiples. « Ce n’est pas encore tout à fait l’industrie automobile, mais la référence implicite est celle-là, et l’organisation y est vraiment impressionnante » ajoute Pingiori.
La construction navale militaire s’est aussi largement déplacée en Asie. Aujourd’hui, la carte des chantiers nationaux italiens comprend Gênes, Trieste, Monfalcone, Venise, Ancône, Castellamare di Stabia, Palerme, et Riva Trigoso pour les navires militaires, plus quelques chantiers mineurs hautement spécialisés. Mais il n’en a pas toujours été ainsi : autrefois, on construisait des bateaux partout en Italie, y compris des pétroliers, des ferries et des navires-citernes pour produits chimiques. Ne restent plus que les navires de croisière : les Coréens ne se lancent pas sur ce terrain qui ne correspond pas à leur modèle de production, puisque chaque navire est différent d’un autre. « Croire que ce type de construction est un artisanat est une erreur de perspective ; nous devrions être capables d’en faire une industrie. »
Pour contenir les coûts, Fincantieri a depuis longtemps standardisé des parties du navire comme la coque ou les moteurs. Sur le plan managérial, la société s’attache à améliorer la gestion des sous-traitants et la formation de son propre personnel. Les chantiers coréens fabriquent quasiment tout eux-mêmes, mais pour les navires de croisière, c’est tout simplement impossible. Une cabine, par exemple, est un ensemble préfabriqué, livré complet, avec les revêtements, le mobilier, la décoration et tous les câblages. Quand arrive le moment de la monter, on la libère de son emballage plastique et on l’encastre dans la section du navire correspondant à chaque pont, puis la section entière est soulevée par une gigantesque grue et appuyée contre la coque. L’avantage concurrentiel de Fincantieri est de savoir sélectionner les sous-traitants et coordonner ce processus complexe dans les délais impartis par le contrat et dans le respect des normes réglementaires qui définissent absolument tout, de l’épaisseur de la tôle jusqu’à la dernière vis qui fixera un abat-jour.
Tout est impressionnant dans la visite d’un chantier naval comme Monfalcone : les dimensions des lieux, de l’outillage et des productions. Tout est de taille XXL, du département soudage au ballet des composants, en passant par le navire lui-même tel qu’on peut l’observer dans son bassin : un rectangle de 350 mètres par 50, à sec d’abord, puis rempli d’eau lorsque le navire sera en état de flotter. Le processus de construction est difficilement « saisissable » sur un tel chantier, car contrairement à un train, un navire ne se construit pas de façon linéaire. Il n’apparaît qu’à la fin, lorsqu’il est assemblé, section par section, comme dans un jeu de Lego. Ce qui n’apparaît pas à la surface, c’est la complexité technologique de ces « joyaux » des mers. Le chantier, particulièrement dans les zones où s’effectuent toutes les opérations préliminaires, ressemble vraiment à une usine, avec ses espaces immenses et ses cohortes de soudeurs assis sur des cagettes en bois ou accroupis dans des recoins impossibles, pendant que les flammes des chalumeaux scintillent dans la pénombre du hangar. « De combien de pièces se compose un paquebot ?
– Personne ne le sait. »
L’usine qui se joue du relief
Ansaldo Energia est spécialisé dans les grandes commandes de centrales électriques. Lorsqu’on entre par l’entrée principale dans l’établissement de Gênes, d’une surface de 210 000 m2, on voit un édifice en briques datant de la fin du XIXe siècle ; ce n’est que l’une des parties d’un site extrêmement complexe, au sein d’une ville dont le relief très accidenté constitue une des limites avec laquelle l’usine doit compter depuis toujours.
Le travail est organisé autour de quatre lignes de produits : les alternateurs pour les centrales thermoélectriques et hydroélectriques, les turbines à gaz et à vapeur. Ce sont des machines impressionnantes de 12 mètres de long sur 4 de large, qui pèsent 300 tonnes et que l’on monte en tournant autour. Ansaldo produit environ 60 machines par an ; en moyenne, on en livre 4 ou 5 par mois. La quatrième ligne, au service des autres, produit les pales pour les turbines au rythme de 50 000 pièces par an à partir de composants semi-finis.
Ansaldo Energia emploie 3 000 personnes, quasiment toutes à Gênes, et génère environ 2 000 emplois indirects. Au sein de l’usine elle-même, opèrent 600 ouvriers et 380 employés. La culture d’entreprise s’est modifiée ces dernières années sous l’influence de deux phénomènes. Le premier est l’ouverture des marchés : le groupe répond désormais quasiment à 100 % à des commandes étrangères, et les voyages sont devenus la norme avec leurs lots de conséquences sur une entreprise assez traditionnelle dans son organisation. Le second est l’introduction d’un programme de lean production qui, après un faux départ et un réaménagement avec des objectifs plus progressifs, commence à produire les résultats attendus. Marcello Parodi, directeur du site, en est convaincu et milite pour des investissements dédiés à la modernisation des processus. Le programme que Parodi a mis sur pied avec entêtement se nomme Factory Academy : il porte sur tous les aspects de l’usine et a impliqué plus d’un millier de personnes. Les formateurs sont principalement issus du personnel de l’usine : des techniciens, des ingénieurs de production, des logisticiens, formés pour devenir formateurs. Les sujets abordés sont, d’une part, techniques et personnalisés par type de profil professionnel et de machines, d’autre part, globaux dans le sens où ils visent à transmettre une vision à 360° de l’entreprise, de son système qualité et de ses perspectives technologiques.
« Quand je suis arrivé en 2005, c’est moi le premier qui ai dû changer ma manière de travailler, raconte Parodi. J’ai cherché à ouvrir l’usine au-delà de la production, vers d’autres fonctions entrepreneuriales, car je soupçonnais qu’elle avait un potentiel mal connu au sein du groupe.
Le fait de fabriquer est ce qui a fait la différence pour Ansaldo Energia face à des concurrents qui ne produisent plus mais se contentent de gérer un projet sans en contrôler les différentes parties qui sont déléguées à des OEM (Original Equipment Manufacturers) : ces donneurs d’ordres, qui se contentent de réceptionner les systèmes ou ne font que le dernier niveau d’assemblage entre les équipements dans des « usines-tournevis », sont considérés comme les pirates du secteur ; ils sont petits, agiles et capables de proposer des activités de services, même s’ils n’ont pas une maîtrise complète des technologies. Dans ce contexte, nous explique Daniela Gentile, directrice de la branche Développement devenue une société à part entière du groupe, il faut avoir la capacité de proposer quelque chose de plus et de mieux que les autres, c’est-à-dire une maîtrise complète de l’ensemble du processus et un service après-vente de long terme avec des contrats d’une durée de suivi pouvant aller jusqu’à 20 ans ; par ceux-ci, Ansaldo s’engage à garantir le fonctionnement des équipements, ce qui permet également d’assurer une fidélisation du client et la continuité de la relation.
L’usine a dû également changer pour se rendre attractive auprès des jeunes générations qui « perçoivent les ateliers comme quelque chose d’arriéré par rapport au monde contemporain ». En sens inverse, il est nécessaire d’accompagner les jeunes face au travail industriel et à ses exigences. « Les jeunes sont parfois très approximatifs et manquent de rigueur, ce que nous ne pouvons accepter, explique Parodi. Comprendre la signification d’un dixième ou d’un centième de variation sur un ouvrage mécanique est capital, mais ceux qui sortent de l’école n’ont pas forcément cette sensibilité, et donc la rencontre avec le monde du travail réel n’est jamais facile. »
Pour Parodi, le numérique est essentiel, même s’il vient en second après la formation des travailleurs. Il constate cependant qu’il entre plus lentement dans les entreprises qui travaillent à la commande que dans celles qui produisent de gros volumes. Les investissements sont lourds et le taux de retour sur investissement (ROI) est difficile à mesurer de façon directe ; en fait, c’est plutôt les perspectives qu’il ouvre qui doivent être évaluées : « Quand nous avons investi dans SAP, il y a des années, nous avons tenté de faire des prévisions sur les gains de productivité engendrés par l’outil. Mais à mon avis, il faut poser le problème autrement : comment ferions-nous aujourd’hui pour communiquer efficacement avec nos partenaires chinois ou coréens, sans ces équipements ? Ce n’est pas un problème de contrôle des coûts, ce qui est en jeu, c’est la soutenabilité même de notre business. » Et les robots ? Il n’y en a pas chez Ansaldo parce que les volumes ne sont pas suffisants pour justifier de telles dépenses et parce qu’ils ne sont pas adaptés au travail de précision exigé à Gênes : à ce jour, les hommes et les machines-outils évoluées demeurent plus précis pour ce type de production.
L’usine du juste-à-temps
Toujours à Gênes, à quelques encablures d’Ansaldo, se trouvent les bureaux de Kuehne+Nagel, un des leaders mondiaux de la gestion de la chaîne logistique. Juste en face du port, on trouve le quartier général du fret maritime, la division historique de cette multinationale d’origine allemande, qui a ensuite élargi ses activités à l’aérien, au terrestre et à la logistique intégrée. En Italie, le fret maritime de Kuehne+Nagel a une histoire de 50 ans et occupe 120 personnes, en partie à Gênes et dans d’autres bureaux de représentation, d’Udine à Bari. « Parce que la clientèle italienne apprécie encore le contact local » précise la responsable, Barbara Eleota.
L’organisation est découpée par type de produit (produits périssables, pétrole et gaz, vin, vrac, etc.) et par marché de destination, ce qui implique d’en connaître a minima la réglementation et la culture. La partie la plus délicate du métier de transporteur ne consiste pas tant à choisir le bon moyen de transport qu’à garantir que la cargaison sera assortie de toute la documentation, permettant de satisfaire le client quant à son besoin de « déplacer les choses ». C’est là que réside la véritable valeur ajoutée de l’entreprise logistique qui travaille sur la chaîne d’approvisionnement : trouver des solutions inédites qui pousseront à changer les process chez le client.
Une logistique efficiente est aussi nécessaire à l’usine 4.0 que le système nerveux au corps humain. Enfiler une boîte de conserve dans un carton, l’étiqueter et l’expédier au client, c’est de la logistique. Assurer l’arrivée de la juste quantité d’écrous à la ligne de montage, c’est encore de la logistique. L’impératif catégorique réside dans le mot « juste ». Car l’usine contemporaine n’accepte plus d’accumuler pièces et matériaux en bord de ligne : ils occupent de la place, ralentissent la sélection des composants par les opérateurs (qui ne doivent pas penser, ou plutôt ne doivent pas penser à ça), augmentent les surfaces et les coûts de stockage. Une approche qui change aussi considérablement la philosophie des achats : plus question d’acheter en gros pour faire des économies. Enfin, parce que selon les principes du lean, l’encombrement augmente statistiquement les risques d’accidents.
Une des prestations de service habituellement demandée aux entreprises logistiques est la gestion des entrepôts de stockage, comme c’est le cas à Turin pour le compte d’Iveco, le constructeur de véhicules utilitaires et industriels. Dans la division Logistique de Kuehne+Nagel répartie dans toute l’Italie, travaillent environ 2 000 personnes, y compris le personnel des entreprises soustraitantes qui fournissent « les bras ». La logistique de stockage consiste majoritairement, encore aujourd’hui, à déplacer des colis ; le personnel qui y travaille est souvent perçu comme une simple « offre de bras », même si le modèle se transforme rapidement. Aujourd’hui, on recherche des employés capables de gérer les flux et on investit dans les nouvelles technologies pour réduire le nombre d’erreurs.
Kuehne+Nagel a été la première entreprise logistique en Italie à équiper les magasiniers d’écouteurs qui leur indiquent où ils doivent se déplacer, tout en leur laissant les mains libres, ce qui a augmenté la productivité de 25 %. Ce système est principalement utilisé dans la grande distribution où le rythme de travail est extrêmement rapide. « Chez Iveco, explique Claudio Boschetti, responsable de la logistique pour l’Italie, nous traitons 220 colis par heure et par personne et notre taux d’erreur est descendu à 2 pour 10 000. C’était impensable, il y a encore 10 ans. » Mais au bout de quelques mois de travail dans l’entrepôt d’Iveco, qui comprend 200 000 références, un magasinier a parfois l’impression de se souvenir des différents emplacements et sa concentration diminue. Pour diminuer le risque d’erreur, la puce RFID permet d’assurer la traçabilité du produit : quand le produit arrive à la pesée, il est contrôlé par un lecteur, l’étiquette est générée automatiquement, appliquée sur le colis qui est ensuite chargé sur le camion. Ce dernier subit encore un contrôle en passant sous un portail de vérification.
Comment fonctionne un entrepôt de stockage ? Chaque produit est classé en fonction de diverses caractéristiques, comme ses dimensions par exemple. Ce paramètre permet de répartir les produits entre ceux qui seront prélevés à la main et ceux qui nécessiteront des chariots-élévateurs. Ces derniers ont beaucoup évolué en matière de motorisation (chez Iveco, ils sont tous électriques) et de rapidité (pas tant en vitesse de déplacement, car celle-ci est réglementée, qu’en mobilité). Le cariste commande les manœuvres avec un unique joystick, là où il fallait antérieurement jusqu’à sept mannettes. Sur le chariot, on trouve des instruments tels que des lecteurs de codes-barres et, caractéristique frappante pour le visiteur profane, la plateforme d’élévation n’est plus à l’avant (elle obstruait la vision) mais placée latéralement. Le résultat en est une augmentation impressionnante de la productivité.
Enfin, certains produits, de faible dimension mais sortis en très grandes quantités, sont traités de façon entièrement robotisée. À Turin, chez Iveco, sur les 18 000 ordres d’expédition quotidiens, 8 000 sont traités au sein des 3000 m2 de l’entrepôt robotisé où ne travaillent que 15 personnes. Dans le champ logistique, l’automatisation est un fait avéré, mais elle est d’application moins fréquente qu’on ne l’imagine habituellement : il faut que les gains de productivité attendus justifient les investissements considérables à consentir, autrement dit, il faut que l’entrepôt fonctionne 7 jours sur 7 et 24 heures sur 24. Dans cet entrepôt d’Iveco, il y a six « cages » impressionnantes : des murs hauts et compacts au milieu desquels se meuvent à très grande vitesse des élévateurs dotés de pinces qui prélèvent ou déposent. Les magasiniers ont été remplacés par des experts en informatique ou mécanique, qu’on appelle chez Iveco des « producteurs », capables de manipuler le logiciel et de faire de la petite maintenance. Cet entrepôt traite plus d’un tiers des expéditions, mais n’emploie que 3 % de la main-d’œuvre totale du site.
Au premier plan des systèmes d’information des entrepôts se trouvent les logiciels d’optimisation des déplacements, dont la presse se fait l’écho régulièrement au sujet d’Amazon. Il fut un temps où le système d’information d’un entrepôt consistait en une feuille Excel qui listait à la suite les commandes et qu’on imprimait pour le contremaître qui, à son tour, communiquait par talkie-walkie avec les magasiniers. Souvenirs d’un monde disparu. Aujourd’hui, il n’y a plus de papier, le système attribue à chaque magasinier « une mission » via un terminal, mission élaborée par un algorithme qui optimise chaque déplacement en prenant en compte la nature et le poids des produits à rassembler. C’est une invention d’origine française, le « précolisage », qui indique au magasinier les contenants adaptés aux colis qu’il va chercher : « Plus d’inquiétude à avoir, tu reçois ta mission et tu fonces ».
Dans le secteur de la distribution, l’algorithme est encore plus complexe et compose des caddies de réapprovisionnement des rayons qui tiennent compte de la disposition du supermarché. Le magasinier du point de vente prend son caddy et l’amène directement au rayon, sans même vérifier la correspondance entre les deux. Dans la grande distribution, le système franchit encore un palier : il n’y a même plus de zone de stockage mais une zone de transit où la marchandise stationne brièvement. « Auparavant, un magasin passait commande une fois par semaine ; aujourd’hui, le système engendre des commandes toutes les 50 minutes en fonction des sorties de caisse qui viennent décrémenter la base où sont centralisées les données de ce qui se trouve réellement en rayon. Les coûts logistiques d’un tel modèle seraient insoutenables sans la technologie. »
Chez Iveco, les commandes arrivent du monde entier, certaines sont très urgentes (le camion doit être prêt en 5 minutes), d’autres sont des livraisons en cycle continu (même la nuit). Iveco dispose de cinq entrepôts en Europe : si la pièce n’est pas disponible dans l’un, il faut identifier sa localisation et la faire venir en quelques heures d’un autre. Aujourd’hui 15 à 20 % du trafic entre les entrepôts est engendré par ces requêtes : « En réalité, les coûts logistiques sont restés “constants”, analyse Boschetti, mais notre travail, lui, est devenu radicalement différent ». On parle maintenant de drones pour faire les inventaires, l’innovation est partout, mais selon Boschetti, « nous avons franchi la ligne d’arrivée, au sens où nous connaissons désormais le stock chez le client final et nous pouvons calculer ses besoins à sa place. »
En matière de gestion de la chaîne logistique, il reste un objectif presque mythique à atteindre : modéliser un système global de supply chain, permettant d’optimiser les trajets en boucles, car chaque client livré est aussi le fournisseur d’autres clients. C’est le but visé par certains modèles de gestion avancés comme le 4PL (Fourth Party Logistic Service Provider), qui se concrétise chez Kuehne+Nagel par une « tour de contrôle » centrale, basée au Luxembourg, où des spécialistes recensent et optimisent tous les trajets. C’est un système qui fonctionne pour de très gros clients mais qui peine à prendre pied en Italie. Selon Boschetti, les freins sont essentiellement culturels : « Dans le secteur automobile, les clients achètent un produit et le prix comprend la livraison jusqu’à leur site. Si on gère le transport en groupage, il faudrait sortir le coût du transport du prix de vente, et la pilule est difficile à faire passer. En Europe du Nord, il y a beaucoup plus de transparence dans la formation du prix, mais en Italie, il y a encore une grande réticence à parler “marges” de manière explicite, et cela fausse le raisonnement. Vous savez quelle serait la vraie révolution dans notre secteur ? La confiance ! »
La logistique permet-elle de réaliser des économies ? « Cela dépend du point de vue où on se place. Notre vocation, c’est d’être des spécialistes de notre métier pour permettre à nos clients de se concentrer sur leur core business qui est de produire et de vendre, et c’est bien qu’ils puissent se concentrer là-dessus. C’est toujours le même dilemme pour celui qui décide d’externaliser. » Est-ce que la logistique existerait sans l’informatique ? « Évidemment non. Aujourd’hui encore, l’informatisation est souvent perçue comme un coût, mais elle ne l’est pas. Sans informatique, il n’y aurait pas de logistique, et j’irais même jusqu’à dire que c’est la logistique qui a révélé le vrai potentiel de l’informatique. »
Ces principes d’ingénierie organisationnelle capables de faire bouger toute une entreprise, engendrent une multitude d’innovations : les caisses de pièces qui s’ouvrent automatiquement pour diminuer les erreurs chez Alstom, les rayonnages qui utilisent la force de gravité pour charger les caisses, que l’on trouve partout chez Fiat Chrysler et qui sont fabriqués par une petite société turinoise. Ou encore les trolleys qui suivent la ligne de montage des Ferrari et avancent en même temps que la fabrication du véhicule (10 d’entre eux contiennent une Ferrari tout entière) ; sur le bord de ligne ainsi libéré, les visiteurs peuvent suivre, comme au spectacle, la naissance d’un bolide.
L’usine boutique
Chez Ferrari, à Maranello, près de Modène en Émilie-Romagne, la priorité est de garantir la sécurité et la qualité, et non les volumes. Contrairement à la production en série, chaque Ferrari est personnalisée selon les caractéristiques définies par le client. Le processus de production est donc long, car il n’y a pas de caisse générique. L’approvisionnement de la ligne se fait via le full-kitting. L’ensemble des composants à monter sur un véhicule (le kit) est apporté à proximité de l’opérateur au fur et à mesure des opérations. Le kit est la solution idéale lorsque les pièces sont si nombreuses qu’il devient impossible, pour des raisons d’espace, de les avoir toutes sous la main. De plus, les bords de ligne sont ainsi libérés, ce qui est important chez Ferrari, où la ligne de production est également un lieu de visite.
Non loin de Maranello, on trouve aussi l’entrepôt d’approvisionnement en composants des Lamborghini (Volkswagen). Mais Ferrari est bien plus efficace que son concurrent, nous dit non sans fierté Luca Pipino, responsable logistique à Maranello. La reconfiguration du modèle logistique de Ferrari est un projet qu’il a suivi de bout en bout. Jusqu’alors, le personnel connaissait par cœur la place de chacune des pièces dans l’entrepôt, mais il régnait tout de même une certaine confusion. Aujourd’hui, chaque pièce dispose d’un code-barres, il n’y a plus de papier et les magasiniers qui préparent les kits personnalisés pour chaque voiture sont équipés de lecteurs et tablettes. Jusqu’à ces dernières années, on considérait comme normal d’écrire au feutre sur le carton le nom du composant en lettres majuscules : une véritable hérésie pour tout logisticien.
Les articles sont placés dans des trolleys rouges et accrochés à une motrice qui part toutes les 15 minutes, de 5 heures du matin à 19 heures. À partir du démarrage d’une production, il faudra 3 semaines pour finir une Ferrari ; mais les composants ne sont pas forcément tous présents en magasin. Le système logistique mis en place garantit cependant que la chaîne ne soit jamais rompue, alors même que le nombre de pièces est proprement inimaginable. Le modèle est en fait plus proche de celui de la grande distribution que de celui du secteur automobile. Par exemple, au fur et à mesure que la production avance, les composants de l’étape suivante descendent de rayonnage en rayonnage jusqu’à être à portée de main. Les trolleys sont « tagués » selon l’étape de fabrication à laquelle ils sont destinés, comme les caddies d’approvisionnement le sont pour les rayons des supermarchés. En production, le temps de cycle pour un véhicule ordinaire est de l’ordre d’1,5 minute, alors que pour une Ferrari, il est de 17 minutes sur la ligne des 8 cylindres, et de plus d’une heure sur celle des 12 cylindres. L’opérateur en carrosserie, revêtu d’une combinaison rouge comme un pilote de Formule 1, dispose de compétences multidimensionnelles et peut prendre son temps. Chaque bolide est différent et serpente le long d’une ligne courbe, enveloppé d’une couverture la majeure partie du temps. Tout ce qui donne au véhicule de la valeur ajoutée est produit au sein même de l’entreprise ; le reste est sous-traité.
L’usine qui sent le neuf
Toujours à Maranello, une ligne hautement automatisée produit les moteurs pour Maserati, aujourd’hui filiale de Fiat Chrysler, comme Ferrari.
Maserati a ré-ouvert à Turin en 2013 après de nombreuses années de fermeture. Quand on passe le portail de l’usine, la sensation est comparable à celle ressentie quand on monte dans une voiture toute neuve : l’odeur caractéristique du cadeau dont on vient d’ouvrir l’emballage. La visite de l’usine est hyper scénarisée avec des hôtesses très bien formées, des écrans et des tutoriels, comme si l’entreprise, attentive à sa propre image, voulait se distancer autant que possible du stéréotype de l’usine du XIXe siècle ; elle semble avoir compris que la communication est un moyen essentiel pour agir sur la « société » – étant entendu que ce mot-valise désigne aussi bien le client qui entre dans le Motor Village pour vivre une expérience d’achat que le jeune diplômé qui imagine encore l’usine comme dans un film néoréaliste ou encore l’ingénieur qui préfère les bureaux aux ateliers.
Luigi Galante, responsable industriel du groupe FCA pour la zone EMEA (Europe, Middle East and Africa) et directeur de Maserati, considère la technologie comme acquise et s’enthousiasme surtout pour l’innovation organisationnelle. Le World Class Manufacturing est un projet d’envergure mené par Fiat, dès avant la fusion avec Chrysler, qui détermine en grande partie l’innovation dans ses sites industriels. « La numérisation et la simulation virtuelle acquièrent une importance de plus en plus grande, et ça marche. Ce n’est pas qu’une mode. En phase de conception de nouvelles lignes de production, nous sommes capables d’anticiper un grand nombre d’éléments qu’il était impossible d’appréhender par le passé sans commencer à mettre en œuvre physiquement les postes de travail. Nous en faisons d’ailleurs un usage intensif pour l’amélioration continue de l’ergonomie des postes ; nous sommes probablement le constructeur qui investit le plus dans ce domaine. » Notre hôte émet, en revanche, davantage de doutes sur la perspective d’une usine si fortement automatisée qu’elle pourrait se passer des hommes. « Sur notre site, le travail manuel et l’intelligence des hommes ont encore un rôle essentiel ; le fait de pouvoir prendre en photo un défaut et de le partager en temps réel avec les équipes est chose commune. Et tous les opérateurs, même les moins jeunes, participent activement à cet état d’esprit, en utilisant des outils qui auparavant étaient réservés à quelques-uns. »
Marcher à Grugliasco (voir aussi supra Comau p. 26) le long de la ligne de production revient à feuilleter un catalogue de brevets relatifs aux technologies les plus en pointe : l’innovation commence dans un rivet et finit dans l’unité où soudain tous les segments de la carrosserie s’assemblent. Dans les cages où ils opèrent, les différents robots synchronisés de Comau peuvent changer de position selon la longueur du véhicule à assembler ; la danse de leurs bras qui s’entrecroisent dans l’espace et qui changent leurs instruments de soudure pour atteindre les angles les plus reculés du véhicule, produit un sentiment d’émerveillement. Quand jaillissent les étincelles, on peut visualiser dans ce petit périmètre la métaphore de l’évolution de toute une industrie.
L’usine des passionnés
La chaîne de montage de Ducati Motor à Borgo Panigale, à seulement quelques minutes de Bologne, construit une moto comme un oignon, strate après strate, autour du moteur.
Ducati a trois établissements dans le monde : en plus de celui d’Émilie-Romagne qui compte 1 350 salariés et produit 90 % du volume mondial, il y a aussi la Thaïlande qui sert les marchés asiatiques et le Brésil pour l’Amérique du Sud. Une moto Ducati génère un bon nombre d’emplois indirects : en effet, seul 8 % de la moto résulte de processus effectués en interne ; ceux-ci se concentrent sur les passages les plus délicats, c’est-à-dire la mécanique et l’assemblage. De ce fait, le choix des fournisseurs et la définition de leur cahier des charges représentent des compétences stratégiques essentielles pour Ducati. Durant la visite, nous verrons que la ligne de production de l’arbre de transmission est composée de postes de travail disposés en U et que ce sont des robots qui alimentent en pièces les machines-outils, réduisant ainsi pour les opérateurs le nombre de tâches à faible valeur ajoutée. La démarche de robotisation a démarré en 2003 et s’est achevée à peine deux ans plus tard. D’autres transformations comme l’adoption du modèle de fabrication cellulaire, la révision des processus et le changement continu de la disposition des ateliers, témoignent d’une entreprise vivante qui a su s’adapter aux nouvelles exigences de production.
En dépit des robots, l’usine Ducati est l’une des plus bondées qu’il nous ait été donné de voir. À la mécanique, on travaille en 21 cycles, 7 jours sur 7, nous explique Mario Morgese, directeur des relations industrielles. Les team leaders, qu’on appelle chez Ducati les primus inter pares, représentent le pivot du Ducati Production System, le modèle lean en vigueur dans la maison. C’est sur eux que se concentrent les efforts de formation : ils doivent être capables de travailler sur toutes les machines, condition nécessaire pour pouvoir aider les équipes. Mais cela n’a pas toujours été ainsi. Il y a à peine cinq ans l’opérateur de Ducati effectuait un nombre d’opérations beaucoup plus limité ; à partir de la réorganisation, il a élargi son champ d’intervention à la maintenance des équipements, installation des outils, contrôle qualité et gestion du processus. Selon Morgese, la motivation s’est accrue et cette meilleure implication a eu des effets bénéfiques : « L’individu doit faire fructifier l’investissement consenti dans les technologies, et la montée en compétences en est la clé. Travailler sur la motivation est essentiel pour permettre au capital humain d’exprimer tout son potentiel. »
Aux assemblages travaillent 500 personnes. Comme la moto est un produit dont les ventes sont saisonnières, Ducati a fait le choix de la flexibilité avec des cycles de travail de 9 heures en haute saison et des phases de récupération la deuxième moitié de l’année. Les pics de production sont gérés grâce à un recours massif à du personnel en CDD ou à temps partiel ; celui-ci représente aussi un vivier dans lequel puiser pour faire face au turn-over. Le Ducati Production System qui est en œuvre depuis les années 2000 donne lieu à une organisation par les flux et en juste-à-temps, capable de s’adapter finement aux courbes de la demande. Pour augmenter la production, on fait varier les cadences : en agissant sur le nombre d’opérateurs sur la ligne, on peut produire de 10 à 100 motos par jour ; c’est la direction commerciale qui impulse le rythme.
On est frappé par l’âge moyen des équipes, plutôt bas en général, mais qui descend à 28 ans en moyenne à la production. Le travailleur Ducati présente un style particulier. Peut-être est-ce dû au fait que l’on est au mois d’août, mais tous affichent le hâle de ceux qui ont passé du temps au grand air, et ils sont très élégants dans leur uniforme, polo rouge sur bermuda kaki. Est-ce parce qu’il s’agit de motos, mais les anneaux aux oreilles et les tatouages sur les biceps et mollets ne manquent pas. Ou peutêtre est-ce le fait que chevaucher une moto vous a toujours un air de vacances, même lorsque c’est dans l’espace réduit du box d’essais avant que le bolide ne sorte de la ligne. Quoi qu’il en soit, tout ici respire un air différent. « Nous les choisissons sur la base de la passion, bien plus que sur leur expérience des ateliers. Même un autodidacte peut être pour nous une très bonne recrue. Notre mode de sélection tient compte de l’attitude et des intérêts personnels, puis nous leur faisons passer des épreuves pratiques et comportementales. » Globalement, mécanicien est la formation qui prévaut. Ducati fait appel à un système de formation dual à la manière allemande, que l’entreprise partage avec Lamborghini (groupe Volkswagen), et qui permet de passer le diplôme directement dans l’entreprise, en accord avec les syndicats et l’institution scolaire.
L’entreprise investit beaucoup en R & D, y compris sur le plan des processus de production. Ces investissements s’inscrivent dans un plan de croissance ambitieux, surtout depuis que la société a intégré le groupe Volkswagen en 2012. Elle regarde de près l’Internet des Objets (IoT), mais le coût de cette technologie est encore tel que le retour sur investissement n’est pas garanti, surtout pour des volumes de production assez faibles. À plus court terme, les données générées par la production seront collectées et analysées pour améliorer l’intelligence globale du cycle.
Pendant que nous parcourons la ligne serpentine sur laquelle la moto prend progressivement forme, on nous explique la complexité du produit. Une Ducati contient entre 7 et 10 unités de commande électroniques ; en bref, c’est quasiment un ordinateur sur roues. La question du design est également essentielle : pour satisfaire le sens esthétique du client, les vis ne doivent pas être visibles, ce qui complique passablement le montage ; la délicatesse des finitions nécessite un soin extrême, et l’usage de matériaux tels que le titane et le magnésium exige une attention particulière. Enfin, la moto est de plus en plus « communicante », ce qui implique de travailler sur la qualité des interfaces qui doivent s’apparenter à de l’infotainment.
Le dernier modèle présente, par exemple, un dispositif électronique de réglage des soupapes qui garantit à la moto une meilleure performance ; il se connecte directement au téléphone portable du conducteur et se visualise sur le tableau de bord. Bientôt, l’interface intègrera aussi le parcours et fournira des données sur l’itinéraire et la performance de la moto ; elle permet déjà d’écouter de la musique, de lire des SMS sur le tableau de bord et de parler à un correspon dant. La moto suit les tendances de la voiture avec un décalage de trois ou quatre ans : la voiture explore et la moto adopte.
Morgese nous explique que, même au sein d’un grand groupe comme VW, le rapport au territoire demeure très important. Ducati a mis en place avec l’université de Bologne un programme de cours sur l’ingénierie des motocyclettes. Les heures de volontariat que le personnel effectue sont reconnues et rémunérées par l’entreprise, qui réfléchit également à un modèle de mobilité durable pour les trajets domicile-travail avec l’usage des transports en commun.
La fabrique des métaux
Technologie, innovation, recherche fondamentale, recherche appliquée sont les motsclés de l’industrie 4.0. La recherche, qui n’est pas seulement une activité mais aussi un secteur économique, connaît en Italie un nouveau printemps, mais elle ne peut faire l’économie d’une spécialisation de plus en plus poussée, afin de s’adapter aux nouvelles exigences du secteur productif.
On connaît bien cette situation chez CSM, Centre de développement des matériaux (Centro Sviluppo Materiali), qui constitue le cœur de la recherche métallurgique italienne. Il a été fondé en 1963, en lien avec Finsider, dans un vaste campus aux portes de Rome. Au cours de son demi-siècle d’histoire, le Centre a connu plusieurs restructurations, qui ont correspondu aux différentes transformations du secteur italien de la sidérurgie. L’entrée à son capital du groupe Rina qui en deviendra ensuite l’unique actionnaire, a donné le signal d’une réorganisation complète et d’un plan d’internationalisation. Depuis l’origine, le Centre offre aux grands acteurs de la métallurgie, des services de mesure, évaluation, recherche appliquée et transfert de technologie. Il est organisé en huit départements qui incluent toutes les disciplines de la métallurgie : de la corrosion à la recherche de nouveaux aciers, des technologies de fonderie ou de traitement de surface à la valorisation des déchets. À ces départements sont liés 22 laboratoires, subdivisés en quatre secteurs techniques. L’offre business est, elle, structurée autour de trois lignes de services : solutions for metal qui regroupe toutes les activités sur les matériaux métalliques à destination des grands opérateurs et utilisateurs de métaux ; new technology and material innovation qui s’occupe de faire émerger de nouveaux matériaux et de les tester pour la production ; environmental solutions, chargé d’étudier l’impact environnemental des matériaux, leur optimisation énergétique, leur recyclage et le traitement des rebuts.
1 230 chercheurs, dont un tiers de femmes, cumulent une expérience de haut niveau. De fait, l’âge moyen n’est pas des plus bas : 45 ans. La spécialisation prend du temps et quand, enfin, un chercheur maîtrise l’ensemble des connaissances requises, le risque est que ce soit l’industrie qui le recrute. Gérer l’équilibre entre les générations est l’une des missions, et problèmes, auquel doit faire face le directeur général Cesare Murgia : « Les seniors représentent une énorme richesse, non seulement pour leur connaissance théorique mais aussi pour leurs savoir-faire appliqués : travailler sur site, jour après jour, avec les clients, permet de faire un type de recherche qui n’est pas abstrait, mais orienté vers des solutions capables de résoudre vraiment les problèmes industriels. »
Les liens avec les universités italiennes, de Turin à la Calabre, sont nombreux et structurés. Mais l’origine de la connaissance accumulée par le CSM remonte surtout à l’époque où celui-ci était un établissement public. « Notre actuelle capacité de service doit beaucoup aux compétences développées par le passé, en particulier à nos 160 brevets actifs et notre tradition collaborative avec les industriels. Mais en même temps, nous devons nous transformer pour coller aux tendances actuelles que connaissent le monde de la sidérurgie et, plus généralement, tous processus industriels qui utilisent les métaux. Cela représente l’occasion de changer la perception du métal, qui est encore trop souvent vu comme sortant des forges de Vulcain, alors que cette activité utilise aujourd’hui des processus automatisés et numérisés, et de rendre les aciéries et fonderies plus sûres, moins polluantes, aptes à produire des matériaux de qualité. »
Ici entre en jeu l’industrie 4.0 avec ses technologies facilitatrices, dont trois retiennent particulièrement l’attention du CSM.
En premier lieu, l’Internet des Objets ou, pour le dire autrement, toutes les formes de capteurs communicants qui permettent de contrôler les processus, en les appliquant surtout aux laminoirs et au traitement des surfaces afin de réduire les défauts. « Quand nous sommes amenés à analyser un produit qui comporte un défaut, nous devons remonter tout le chemin à l’envers depuis la coulée, afin de “trouver le coupable”. En effet, derrière l’intégrité d’un matériau, il y a tout un monde caché : comment il a été fondu, laminé, traité. C’est vraiment fascinant, mais on peut se demander si l’automatisation ne nous apporterait pas une aide décisive en termes d’efficacité. »
Parmi les autres technologies facilitatrices de l’industrie 4.0, il y a la fabrication additive. Sur ce plan, le CSM veut apporter ses propres compétences sur les matériaux, et plus particulièrement sur les poudres dont on sait encore peu de choses : il ne suffit pas d’avoir l’imprimante, il faut encore savoir quoi mettre dedans et parvenir en outre à prendre ses distances par rapport au fournisseur qui aura tout intérêt à vous rendre dépendant de son produit – un peu comme pour les cartouches d’une imprimante classique. Le CSM s’y intéresse et prend le pari qu’on pourra arriver dans peu d’années à une technologie mature.
Dernier domaine d’intérêt : la réalité augmentée et tous les dispositifs portatifs qui pourraient complètement changer le travail des opérateurs et leur exposition aux risques et à la chaleur. On peut y ajouter encore la photonique qui a de nombreuses applications en soudage, depuis que celui-ci a été révolutionné par l’usage du laser. « Elle peut contribuer à résoudre de façon simple des problèmes complexes, comme le soudage de matériaux hétérogènes, ce qui représenterait une percée pour les secteurs où la performance et la légèreté des matériaux sont stratégiques. La figure du soudeur s’en verrait également transformée : le soudage au laser n’exige pas de l’habileté manuelle mais du contrôle ; ce n’est pas un hasard s’il est utilisé dans un des secteurs les plus précis au monde : l’aérospatial. »
L’usine à spectre large
À Spinetta Marengo, tout près d’Alessandria (Piémont), Solvay aussi s’intéresse aux processus.
Dans une usine chimique, le terme manufacturing ou fabrication paraît peu approprié. L’activité centrale dans un établissement chimique consiste à se retrouver devant un nombre indéterminé de tuyaux et de vannes sur lesquels, sous la houlette de multiples superviseurs, l’opérateur effectuera des tâches de contrôle de la température, d’ouverture et de fermeture des vannes, selon des paramètres définis mais qui peuvent être modifiés en cours de processus. Il y a peu d’actions répétitives dans ce contexte, du moins au sens où on l’entend généralement dans une usine. Pour cette raison, le niveau de compétences est élevé, et même [Dans la chimie,] les opérations les plus simples requièrent une formation technique et des capacités cognitives supérieures à ce qui est généralement demandé dans une usine classique.
Le site de Spinetta Marengo, aujourd’hui leader mondial des polymères avancés, appartient à l’unité des polymères de spécialité (3000 personnes et 14 sites industriels dans le monde) au sein de la division advanced materials du groupe Solvay. Son quartier général est à Bollate, dans la grande banlieue de Milan, où se trouve également son centre de recherche et d’innovation avec 250 chercheurs, l’un des plus importants d’Italie pour la chimie.
Le site de Spinetta a différentes lignes de production. On y produit des élastomères avec des applications dans plusieurs secteurs – « Souvent, même nous, nous ne savons pas quelles seront les applications finales de nos produits », explique Paolo Bessone, DRH de l’établissement. Il y a aussi les plastomères qu’on utilise, par exemple, pour fabriquer des gaines de câbles. Ou encore les fluides pour des applications liées à la lubrification ou au traitement de surfaces. Un exemple parmi d’autres : une huile fabriquée à Spinetta sert à lubrifier tous les disques durs du monde.
À l’origine des activités du groupe depuis 150 ans, on trouve les produits les plus connus du grand public : la soude et le bicarbonate. Les marchés de Solvay sont aujourd’hui si diversifiés qu’il est impossible de mesurer sa part de marché en général, il faudrait l’évaluer produit par produit. Mais globalement, le groupe fait partie des 10 plus grands acteurs mondiaux de la chimie, et pour rester dans ce peloton, il doit investir continuellement. Pour orienter ses investissements, Solvay s’intéresse aux mégatendances qui transforment l’époque: du changement climatique à l’épuisement de certaines ressources naturelles, en passant par le vieillissement et la santé. C’est pourquoi, il lui arrive de participer à des projets à fort potentiel de communication, comme ce fut le cas avec Solar Impulse, un avion né à l’initiative des Suisses Bertrand Piccard et André Borschberg, exclusivement alimenté par l’énergie solaire, capable de voler même de nuit et d’assurer un tour du monde complet. Le 9 mars 2015, Solar Impulse 2 décollait d’Abou Dhabi, entre autres grâce à des matériaux spéciaux sortis de l’usine de Spinetta. En 2014, Solvay a été l’entreprise qui, en Italie, a déposé le plus grand nombre de brevets : soixante-dix.
Non seulement les produits, mais aussi les usines chimiques évoluent. Sur ce point, nous sommes obligés de croire les responsables sur parole, car nous n’avons pas eu le temps de visiter les lieux. Mais le thème est très présent chez les managers qui, tous les deux ans, s’impliquent dans le projet Usines ouvertes, l’occasion pour les familles des salariés et toute personne intéressée de visiter l’usine. En septembre 2015, il y avait eu 2 200 visiteurs. Bessone nous explique que l’effet produit sur les visiteurs est ambigu : « Il y a une forme de barrière psychologique à l’égard de la chimie, supérieure à celle d’autres activités industrielles. Nous devons combattre les préjugés, en montrant notamment que chez nous “l’aliénation au travail” est bien moindre que celle d’une chaîne de montage et qu’au contraire, l’opérateur évolue dans un univers où le niveau de formation est élevé (110 diplômés des écoles et universités, et 450 diplômés de l’enseignement technique), avec un personnel jeune, entièrement tourné vers l’innovation. En outre, le travail dans la chimie est plus créatif. » Le terme « créatif » nous ayant quelque peu surpris, nous lui demandons d’approfondir : « Au niveau supérieur, pour les jeunes diplômés qui font de la recherche, la créativité est infinie et tout le monde a la possibilité d’apporter de la valeur ajoutée au produit. Au niveau intermédiaire, même si les procédures sont codifiées, les opérateurs disposent d’une réelle autonomie. Ils sont incités à avoir une claire conscience de leur rôle dans le processus et à développer leur capacité à comprendre si, dans la section qui leur a été attribuée, tout se passe comme prévu. Même le mouvement est plus “libre” parce qu’il n’y a pas de ligne, donc chacun peut apporter une contribution personnelle. » C’est sur ces traits caractéristiques que s’appuie le programme Manufacturing Excellence que Solvay a mis en place. L’entreprise a pour objectif d’agir sur les comportements et d’augmenter l’autonomie des opérateurs : « Il y a eu les objections habituelles, comme quoi nous cassions les lignes hiérarchiques, mais nous obtenons des résultats tangibles sur l’amélioration technique et sur l’engagement des personnes ».
La figure de référence au sein de l’établissement de Spinetta est l’ingénieur chimiste ou le docteur en chimie, de préférence récemment diplômé : « Nous travaillons sur des technologies propriétaires, en conséquence l’absence d’expérience préalable n’est pas une barrière à l’entrée. Ce que nous recherchons, ce sont avant tout des jeunes talents formés à l’université, surtout italienne, auxquels nous offrons un parcours de formation et de développement professionnel, y compris à l’international ». Chez les chercheurs, il y a une fraîcheur et une curiosité à saisir dans les premières années, qui tendent ensuite à s’émousser avec le temps ; tandis que les compétences augmentent, l’intuition faiblit. « Pour recruter les jeunes diplômés, nous avons initié des collaborations avec les principaux instituts techniques du territoire et mis en place des parcours en alternance. Depuis 2007, nous avons reçu plus de 500 étudiants et embauché 120 jeunes diplômés sur la base d’un contrat de professionnalisation qui a abouti dans 95% des cas à une embauche en CDI. »
Nous demandons à Bessone ce qu’il pense du nouveau paradigme de la smart factory, s’il le trouve approprié pour faire face au rattrapage de compétitivité que doit opérer le pays. La réponse tombe, tranchante : « Dans les conditions actuelles, il ne paraît pas simple de le mettre en œuvre en Italie. C’est un modèle qui nécessite de mobiliser une vision stratégique pour le pays et par le pays tout entier : croire fermement en l’industrie, avoir une politique de long terme, disposer d’infrastructures et d’une énergie à bas coût. Enfin, il faut construire une forte densité de relations entre toutes les parties prenantes des territoires où l’on opère. Chez Solvay, nous nous sommes donné une ligne de conduite appelée Solvay Way. C’est notre politique de responsabilité sociale et nous la traduisons quotidiennement en comportements et en actions. »
L’usine sous vide
La légèreté des politiques industrielles italiennes, surtout si on les compare à la ténacité et aux programmes parfois ambitieux dont font preuve d’autres économies européennes pour soutenir leur industrie, est au centre de la discussion que nous avons avec Pietro Palella, directeur général de STMicroelectronics pour l’Italie, un acteur mondial italo-français (ou franco-italien) du secteur électronique. Sur le site d’Agrate, proche de Monza (Lombardie), il est possible de vivre l’expérience de la salle blanche, ces espaces en milieu stérile où l’on produit les galettes de silicium, sans lesquelles la révolution de la data n’aurait pas lieu. Les salles blanches se succèdent, chacune avec une luminosité différente, plus blanche, plus jaune, plus rose, dans lesquelles s’agitent des hommes et des femmes portant des combinaisons intégrales. Personne ne semble manipuler quoi que ce soit mais seulement taper sur des claviers pour contrôler des processus physiques et chimiques. Difficile d’imaginer quand on observe les salles blanches d’aujourd’hui qu’il fut un temps où, même dans ce secteur, les processus étaient moins technologiques et moins automatisés. Palella nous confirme qu’autrefois, un opérateur simplement doté du brevet des collèges et correctement formé était tout à fait capable d’évaluer l’oxygène déposé sur une galette de silicium, en se rapportant à un code des couleurs CPK14. Aujourd’hui, cette évaluation est faite par une machine et l’opérateur n’a aucun besoin de comprendre ce qui se passe, « mais s’il le sait, c’est mieux ! ». En conséquence, les opérateurs ont changé de profil : moins compétents sur la technique, mais avec une meilleure maîtrise du processus. « Indubitablement, l’usine à venir sera moins intensive en travail. Le coût du produit, chez nous comme ailleurs, sera toujours moins dépendant du coût du travail. C’est ce qui justifie qu’on puisse rapatrier des activités en Italie, grâce à la qualité et à l’innovation qu’on peut atteindre. Si l’on raisonne à “gâteau constant”, c’est sûr qu’on ne s’y retrouvera pas en termes d’emploi, mais si on s’attache à faire grossir le gâteau, et à développer l’industrie comme moteur de la croissance du pays, alors on peut changer la donne. »
L’électronique est partout, dans les produits, les technologies, les services et les modes de production. Il n’existe pas un secteur dont la transformation ne soit pas accélérée par l’électronique. Palella nous rappelle que l’électronique agit comme un coefficient multiplicateur de 1 à 5 pour un marché donné. Si l’on pense à l’automobile, le secteur tel que nous le connaissons n’existerait tout simplement pas sans l’électronique. Ni les smartphones.
Palella n’est pas du genre à croire au miracle d’un marché qui s’autorégulerait ; il faut des politiques publiques pour cela. Selon lui, il manque en Italie une ligne directrice nationale pour s’inventer un nouveau destin. Les initiatives entrepreneuriales qui dessinent l’avenir reposent sur des facteurs individuels, et non sur un modèle systémique. L’exact opposé de l’Allemagne qui en a fait un exercice stratégique, avec une feuille de route précise : « Non que ce soit forcément le modèle à suivre, mais enfin, nous, pendant très longtemps, nous ne nous sommes même pas posé la question de chercher un modèle. Aujourd’hui, le problème est enfin sur la table, mais nous n’avons pas encore identifié les solutions ni les mécanismes pour capitaliser concrètement sur les résultats de la recherche, ni pour créer les organismes qui feront le trait d’union entre recherche et industrie. »
Tout aussi importants sont les sujets des collaborations et synergies entre grands groupes et PME ou la promotion de l’innovation ouverte. « Quand les entreprises collaborent entre elles, l’information passe des unes aux autres et cela favorise une dynamique d’innovation. » Mais en Italie, les mécanismes de rapprochement ne semblent pas encore avoir produit de résultats visibles, tandis que la grande industrie se délite, laissant des places vacantes qui ne sont pas récupérées par les moyennes entreprises en termes de leadership industriel.
Grand potentiel du tissu entrepreneurial mais travaillant en ordre dispersé et « aptitude à la créativité mais reposant uniquement sur le ressort individuel » sont les caractéristiques d’un pays qui ne parvient pas à se solidifier. Manque le point de rencontre qui parviendrait à rassembler et unifier les énergies.
Au-delà de l’usine
Une règle non écrite dit qu’il est plus facile pour une entreprise numérique de devenir un distributeur que pour une entreprise physique de distribution de se numériser en profondeur.
Apple, par exemple, est devenu un distributeur de produits numériques : il est parti de ses logiciels et produits, puis il a bâti des sites de contenu, des magasins brick and mortar, une logistique et une stratégie de relation client. Pour tous les distributeurs, depuis l’électronique grand public jusqu’aux vendeurs de chaussures, le benchmark en matière de gestion logistique est Amazon. Enfin, Google a imaginé la voiture sans conducteur, en la bâtissant in-house, sans chercher initialement à s’associer à des constructeurs automobiles. Les entreprises du numérique s’intéressent de plus en plus aux biens matériels « parce que dans Internet des Objets, il y a le mot objet ».
C’est Fiamma Ferrero qui l’affirme. Après dix ans passés dans des multinationales, cette experte en innovation numérique a cofondé Inwibe, une société de conseil qui crée des liens entre les start-up et les grandes entreprises de façon à enclencher de nouvelles formes de collaboration et d’innovation. Si les services numériques tendent à « manger » les biens15, c’est parce que ceux qui vendent ces services [numériques] ont développé des compétences et des processus dans lesquels il est plus facile d’intégrer des biens que l’inverse. Autrement dit, si l’on dispose des bonnes compétences, on n’a plus qu’à chercher le bon produit ; en revanche, si l’on a un bon produit, mais qu’on ne sait pas comment le valoriser, construire un modèle d’affaires sera plus laborieux. Tesla est un bon exemple pour comprendre ce renversement de modèle : l’entreprise ne construit ses voitures qu’après les avoir vendues, la plupart du temps en ligne ; le design thinking met au centre les exigences de l’utilisateur et construit la voiture autour de celles-ci ; l’open innovation est la règle, c’est-à-dire un système où en échange de la transparence des données, on obtient l’accès à une communauté qui appuie l’innovation, dans une logique de cycle court et d’échange dynamique entre secteurs d’activité.
« À l’ère numérique, la valeur ajoutée ne réside pas forcément dans le fait de détenir une compétence en propre ou de l’inventer, mais de savoir la trouver, au bon endroit et au bon moment. C’est une disposition d’esprit différente : une culture de l’accès et de la fonctionnalité, au lieu de la possession. »
Dans le secteur automobile, les constructeurs externalisent déjà une grande partie de la production à des équipementiers et conservent l’assemblage ; dans le futur, ils pourraient aussi y renoncer et se transformer en centres de conception, de design, de marketing et de service client. Dans quels secteurs cette mutation semble-t-elle la plus probable ? « Il y a des secteurs dans lesquels cette vision se matérialise plus rapidement que dans d’autres, parce qu’il y va de leur survie ou parce qu’il existe des aptitudes naturelles au changement. »
Cet état d’esprit numérique ne se confond cependant pas avec les TIC ou l’IoT. Les TIC transforment les processus, réduisent les gaspillages, permettent d’optimiser ; l’IoT crée des connexions entre des systèmes divers : « Les TIC permettent de tracer une ligne droite, là où il y avait auparavant un chemin sinueux, l’IoT est un réseau de neurones. » Et d’ailleurs, comme on le constate chez les enfants et les personnes âgées qui apprennent souvent très vite à utiliser un smartphone ou une tablette, il n’est pas forcément nécessaire d’avoir franchi le premier palier pour atteindre le second.
Qui sont ceux qui travailleront aisément dans cet univers ? Selon les études les plus récentes, les compétences les plus recherchées sont l’aptitude à l’innovation, le goût de la relation client, la capacité à résister au stress et à travailler en équipe, sachant qu’en Occident les compétences comportementales sont très présentes alors que dans les pays émergents dominent les compétences techniques. D’ailleurs, pour innover, beaucoup d’entreprises n’embauchent plus forcément, elles s’adressent directement à de nouveaux entrepreneurs : il en résulte une augmentation du travail indépendant et de la sous-traitance. Ce recours à l’externe n’est pas particulièrement lié au coût, mais surtout au nouveau modèle d’innovation.
Quels sont les choix que devrait opérer une politique publique qui voudrait prendre des initiatives pour répondre à ces tendances ? « Elle doit principalement mettre à la disposition des entreprises des ressources structurelles : la formation initiale et continue, l’aménagement du territoire, les infrastructures matérielles et immatérielles pour la mobilité et la communication, y compris permettre l’accès au haut débit partout. Donner des aides aux entreprises n’est pas une fin en soi. Si tu réduis ma pression fiscale, mais que tu ne me donnes pas les infrastructures dont j’ai besoin pour me développer, il vaut mieux continuer à payer des impôts. Alternativement, il vaut mieux baisser les impôts qu’attribuer des aides directes : si mon entreprise crée de la valeur, j’aurai les ressources pour investir ou je réussirai à les trouver. »
- * Toutes les notes sont du traducteur.
- 7. http://ec.europa.eu/research/industrial_technologies/factories-of-the-future_en.html
- 8. http://www.effra.eu/
- 9. http://www.fabbricaintelligente.it/
- 10. Économie),
- 11. Depuis 2008, Renault en est devenu progressivement l’actionnaire majoritaire aux côtés de Rostec, l’agence gérant les participations de l’État russe.
- 12. Dont Renault.
- 13. Société de classification maritime fondée à Gênes en 1861.
- 14. En chimie, le code de couleurs CPK est un ensemble de couleurs permettant la distinction des atomes de différents éléments chimiques dans les modèles moléculaires.
- 15. Selon le titre de l’éditorial de Marc Andreessen, fondateur de Netscape, dans le Wall Street Journal , en 2011 « Software’s eating the world ».
Point de vue – Un patchwork de belles mutations qui incite à la transformation
Par David Machenaud et Michaël Valentin, co-fondateurs et directeurs associés d’OPEO
L’industrie n’est pas un simple secteur économique. L’usine, qui en est le cœur et le symbole historique, a toujours été le carrefour de toutes les disciplines : histoire, sociologie, science, technologie, économie ; ce lieu où la matière se transforme est un véritable laboratoire, un monde fascinant qui participe à l’aventure humaine depuis plus de trois siècles.
Néanmoins, ce monde aux allures romantiques est en train de basculer dans un nouveau chapitre de son épopée : l’hybridation du monde des machines avec celui du digital et de la « tech » produit un nouveau paradigme. Ce dernier est à la fois porteur d’espoirs et de craintes pour l’avenir de ce pilier de l’économie de nos pays, qui a beaucoup souffert du phénomène des délocalisations dans la fin du 20e siècle suite à la globalisation des échanges commerciaux. La 4e révolution est en marche, l’industrie est désormais « 4.0 » et se transforme petit à petit.
Le présent ouvrage donne à voir un magnifique patchwork de très belles usines italiennes qui sont entrées dans cette mutation vers l’industrie « du futur ». Peint à la manière des impressionnistes, l’ouvrage est une parfaite illustration des sensations produites par une usine au 21e siècle : modèles économiques en évolution, diversification des produits, complexité apparente des chaînes logistiques, modernité des machines et des lignes de fabrication, nouvelles technologies balbutiantes, évolution de tous les métiers traditionnels…
Pourtant, la question intemporelle qui structure le récit demeure sans surprise : quelle place pour l’homme dans l’industrie de demain ? Autour de cette question centrale, plusieurs interrogations se dessinent petit à petit pour le lecteur averti : la culture industrielle traditionnelle peut-elle supporter une mutation profonde vers un monde où l’automatisation et l’intelligence artificielle ont de plus en plus de place ? Les équipes industrielles peuvent-elles réellement travailler en autonomie dans un monde de plus en plus complexe ? L’usine va-t-elle garder son rôle de régulateur social dans son écosystème naturel ? Les nouvelles technologies peuvent-elles contribuer à accélérer le mouvement d’une industrie de plus en plus verte ? La « servicisation » de l’industrie va-t-elle se faire au bénéfice des équipes industrielles ou uniquement profiter à un client toujours plus exigeant sur les délais et la valeur d’usage de ses produits ? L’emploi industriel a-t-il une chance de redémarrer ou est-il condamné à diminuer inéluctablement ? L’industrie a-t-elle les moyens de recruter les talents qui seront nécessaires pour faire face à la mutation des compétences ?
Quelle que soit la taille de l’entreprise, notre expérience montre qu’une transformation réussie vers l’industrie du futur repose sur la cohérence de cinq mouvements concomitants : faire évoluer la stratégie pour profiter de la « plateformisation » de l’économie, de l’hyper connexion des produits et de l’effet réseau ; se doter d’une politique environnementale et sociale ambitieuse avec une vision inspirationnelle pour la société et s’intégrer ainsi harmonieusement dans son écosystème ; sélectionner les bonnes technologies du futur et adapter les compétences des hommes ainsi que les modes de travail ; adapter les flux et les pratiques opérationnelles aux évolutions technologiques ; faire évoluer les pratiques managériales et les comportements pour que la culture et les états d’esprit s’adaptent au nouveau paradigme.
Ces cinq dimensions constituent un équilibre fragile, comme une ligne de crête sur laquelle chaque dirigeant industriel se meut, en faisant évoluer petit à petit son organisation pour que l’entreprise s’adapte de façon coordonnée et avec un objectif suffisamment porteur de sens pour que les équipes y adhèrent. Dans cet ouvrage, le lecteur est plongé au cœur de ces cinq changements qui se produisent au sein des usines italiennes, avec un choix délibéré des auteurs d’insister plus ou moins sur l’un ou l’autre d’entre eux, en fonction de l’importance relative que chacune des cinq dimensions revêt pour l’usine concernée.
Au-delà de ces aspects, chaque entreprise doit intégrer des changements associés à l’industrie 4.0 qui dépassent de très loin le cadre micro-économique. Les enjeux sont de taille pour l’économie dans son ensemble. C’est pourquoi le mouvement doit être accompagné par la puissance publique. Chaque grand pays industriel a lancé un plan d’accompagnement d’ensemble qui regroupe des initiatives sur le financement, les infrastructures, la formation, la structuration du marché des offreurs de solutions.
En France, un schéma de transformation de l’entreprise vers l’industrie du futur semble se dessiner, avec une réflexion avancée des institutionnels dans leur appui à cette transformation. Première étape, allumer la mèche par des diagnostics « systémiques » permettant aux entreprises de bâtir un plan de transformation où sont travaillées simultanément les cinq di- mensions évoquées ci-dessus : business model, intégration pertinente et harmonieuse dans l’écosystème, agilité de l’organisation, apport des nouvelles technologies mettant le facteur humain au cœur de la dynamique. Lancés par des régions comme Nouvelle-Aquitaine ou Grand Est par exemple, mais aussi par Bpifrance, ces diagnostics donnent à l’entreprise la feuille de route de la transformation, et permettent aux organisations institutionnelles d’obtenir en retour un panorama des atouts et faiblesses du tissu industriel.
La deuxième étape consiste à enclencher la transformation, avec ces approches chères au monde de la tech qui font irruption dans l’industrie, les Proof of Concept (POC), ces tests « live », pragmatiques et immédiats, pour démontrer l’apport ou non d’une technologie. L’enjeu, à ce stade, est de trouver rapidement les offreurs de solutions répondant aux besoins identifiés pendant le diagnostic. Là encore, un mouvement d’accompagnement a été initié avec la cartographie des offreurs de solutions par les CCI, qui gagnera à ne pas rester un simple annuaire mais à devenir bel et bien un réseau vivant, lisible, et qualifié dans la réponse aux besoins des industriels.
Enclencher les POC technologiques ne doit pas occulter les autres dimensions : l’adaptation de l’organisation, les pratiques managériales, la montée en compétences. C’est dans cette troisième étape que résident les vrais défis pour notre industrie. La technologie n’est pas un hobby, c’est un vecteur de compétitivité. L’enjeu est donc plus large : il s’agit, d’une part, de transformer le système de production pour qu’il devienne horizontal, agile, connecté et apprenant ; d’autre part, de surinvestir dans les compétences du futur. Ces ingrédients majeurs sont indispensables pour que la technologie déploie son plein potentiel afin de faire évoluer les modèles d’affaire, de gagner en performance et d’attirer les talents.
Ce voyage dans l’industrie du futur italienne illustre ces trois étapes qui marquent le passage de l’ancien monde industriel au nouveau. Le mouvement est très largement initié dans la plupart des entreprises, de formidables réussites locales sont d’ores et déjà visibles et encourageantes pour l’avenir. Néanmoins, peu ont entamé avec succès la transformation complète de leur système tant au niveau stratégique, technologique qu’organisationnel, afin de profiter pleinement des opportunités de l’industrie 4.0. C’est sur cette dernière étape que repose la clé du succès de notre industrie européenne : prenons ce virage au plus vite pour permettre à nos industries de retrouver une position de leadership dans le monde.
Le travail 4.0
Catastrophistes et militants de l’innovation
Chaque révolution industrielle a eu sa technologie iconique à laquelle cependant elle ne pouvait être réduite : le métier à tisser mécanique, la machine à vapeur, l’électricité, la chaîne de montage, l’électronique, etc. Le storytelling relatif à l’industrie du futur se nourrit d’images et d’hyperboles qui veulent marquer une rupture avec le passé ; pourtant, si l’on regarde les expérimentations concrètes au sein des usines, on constate que cette mutation suit des voies multiples qui ne dérivent pas nécessairement d’une matrice commune.
Voyager dans l’usine du futur, c’est traverser un paysage discontinu, où les diverses technologies ou concepts associés à l’industrie 4.0 sont identifiables de façon très diffuse, parce que les situations, les stades d’évolution ou le management de chaque entreprise sont différents. En Italie, ces changements se greffent sur une transformation structurelle due à la crise de 2008. Pour beaucoup d’entreprises, la crise a représenté l’occasion d’une rénovation en profondeur16, même si celle-ci a globalement provoqué une diminution de la part du manufacturier dans l’économie italienne. Ces dernières années, un certain nombre d’entreprises ont réussi leur transition, en augmentant leurs investissements, en modifiant leur produit ou leur business model, et ce en l’absence de tout dessein stratégique provenant des institutions italiennes. Il en résulte un catalogue de cas de réussite plutôt qu’un mouvement systémique (Cipolletta-De Nardis, 2012).
À ce renouveau de l’intérêt pour les usines dans leur version « smart » ne semble cependant pas correspondre un égal intérêt pour ceux qui les remplissent : les travailleurs. On en parle en termes de « capital humain » ou en employant des termes génériques comme « les salariés », presque comme si ceux-ci étaient des terminaux faits de chair dans un système essentiellement constitué de machines connectées. Pourtant, dans la mesure où l’automatisation et l’homme co-évoluent au sein de l’usine depuis longtemps, il faut tenter de cerner ce qu’impliquent pour le travail et les travailleurs les transformations en cours.
Dans les phases de mutations technologiques, il est habituel de s’interroger sur les effets de celles-ci sur l’emploi. On constate que le débat en cours se polarise sur deux visions : celle des « catastrophistes » et celle des « militants de l’innovation »17.
Ces dernières années, plusieurs analystes ont prédit que l’automatisation des tâches aurait un impact sur l’emploi global dans les fonctions de moyenne qualification, impliquant un certain niveau de routine et de standardisation, alors que, pour des raisons différentes, l’emploi très qualifié et peu qualifié resterait difficilement substituable : le premier parce qu’il repose sur des capacités de conception et d’élaboration qui demeurent, pour le moment du moins, hors de portée des machines ; le second parce qu’il exige des interventions manuelles nécessitant l’homme ou simplement parce que, pour des tâches à faible valeur ajoutée, il reste moins coûteux que les équipements destinés à le remplacer. Dans cette vision, le critère de segmentation traditionnel entre travail manuel et intellectuel devient obsolète ; c’est désormais le rapport entre les capacités humaines et la faculté des machines à les remplacer qui redessine les niveaux d’emploi et les hiérarchies entre les métiers.
Cependant ce scénario évolue à grande vitesse. L’abaissement des coûts et l’augmentation des performances des technologies numériques permettent désormais d’envisager aussi la progressive disparition d’une part non négligeable d’activités dites supérieures. Selon le très discuté rapport de Carl Frey et Michael Osborne (2013), 702 types d’activités courraient le risque d’être remplacées par des algorithmes aux États-Unis dans les dix prochaines années, soit 47 % des emplois. Au-delà de la controverse sur l’exactitude de cette prévision, il est intéressant de regarder de plus près les professions concernées par cette substitution : à côté des nombreux emplois manuels, les deux chercheurs incluent les techniciens de l’industrie et des services, et quelques professions supérieures. Tout se passe comme si les technologies numériques, après avoir favorisé la rationalisation et la productivité des fonctions d’exécution, remontaient l’échelle hiérarchique pour s’attaquer désormais au bastion des professions considérées jusqu’ici comme non automatisables. Dans leur essai Race Against The Machine, deux professeurs du MIT, Erik Brynjolfsson et Andrew McAfee (2011), indiquent que resteraient pour l’heure hors de la portée des machines les professions exigeant des compétences émotionnelles, relationnelles, créatives, ou des capacités cognitives de diagnostic et de résolution de problèmes difficilement dupliquables.
À l’inverse, les militants de l’innovation soutiennent que nous nous trouvons au commencement d’une transition plus ou moins longue vers de nouveaux fondements technologiques, sociaux et de marché qui recréeront des emplois plus riches, plus complexes et plus gratifiants. Là où l’on constate une destruction des emplois, il s’agirait d’une simple phase de « destruction créatrice » schumpetérienne : les emplois futurs seraient déjà contenus en germe dans les innovations en cours, même s’il reste nécessaire d’en accompagner la création par une qualification de la main-d’œuvre orientée vers la connaissance et les services. En se basant sur une recherche menée en Californie, l’économiste Enrico Moretti (2013) affirme que cinq nouveaux emplois sont créés pour chaque emploi lié à la connaissance.
Bien que divisés entre catastrophistes et militants de l’innovation, les deux camps se rejoignent sur un diagnostic : le caractère décisif de l’impact de la digitalisation sur l’emploi, et sur l’emploi industriel en particulier. Dans la vision classique, les révolutions technologiques avaient pour conséquence des redistributions de l’emploi : certains étaient détruits, mais d’autres étaient créés en amont ou en aval du cycle de transformation. Aujourd’hui, il n’apparaît plus aussi certain que ce cycle puisse s’accomplir : le niveau de développement technologique atteint permet effectivement de réduire le travail nécessaire, produisant un excédent de travailleurs, surtout si l’on tient compte du fait que l’emploi industriel au sens strict décroît régulièrement en Italie comme dans d’autres pays industrialisés depuis les années 1970. Mais il est vrai que le taux d’emploi industriel est un indicateur qui présente de moins en moins d’intérêt. Le nombre d’emplois industriels est un indicateur lié à la classification statistique des activités économiques ; or la tendance est à la tertiarisation de nombreuses activités qui sont situées directement en amont et en aval de la production industrielle. L’industrie « intelligente » combinera de plus en plus biens et services au point de rendre inopérante cette division dont on peine, depuis quelque temps déjà, à délimiter la frontière.
De notre voyage à travers les usines italiennes se détachent quelques profils-types de travailleur, en rupture avec les catégories professionnelles habituellement observées.
L’ouvrier « augmenté »
Le scénario d’usines avec une présence humaine très réduite, tel que nous avons pu l’observer à Cameri avec ses soixante imprimantes 3D fonctionnant en continu, n’est pas le plus probable à grande échelle ; les entreprises industrielles continueront à employer une part importante de travailleurs dans les fonctions de production – même si elle décroît (comme depuis 30 ou 40 ans) – à côté d’équipements et de machines dotés d’une certaine « intelligence ». Et c’est dans le cadre de ce système mixte qu’il faut s’interroger sur la transformation qualitative du travail des opérateurs. Au début du XXe siècle, György Lukacs, le philosophe marxiste hongrois, écrivait que le travail dans les grandes usines était réduit à une fonction « contemplative ». Dans l’usine intelligente, c’est en apparence exactement le contraire : on demande aux opérateurs une participation consciente au processus de production, dont ils doivent a minima comprendre la toile de fond.
« Nous avons créé des cellules de production qui rassemblent toutes les compétences techniques. L’opérateur entre dans un processus de gestion du cycle avec le technologue de production et passe d’expert d’une seule machine à expert du flux des composants dans la cellule au sein du process de production. Nous imaginons de mettre une personne par cellule, qui dialogue avec une ligne de machines. L’opérateur n’est pas un contrôleur, mais une personne qui régule les flux. Il ne connaît pas à fond une seule machine mais il a une vision d’ensemble. » (Avio Aero)
Chez Avio Aereo, l’opérateur polyvalent ou « expert en flux » ne sera pas le seul profil de l’usine intelligente, mais il apparaît comme l’une des figures emblématiques de ces nouveaux ateliers qui comprendront aussi des ouvriers, des team leaders, des ingénieurs, des techniciens et des magasiniers. La différence entre l’opérateur Avio Aereo et les premiers « conducteurs systèmes » de l’usine automatisée tient au fait qu’il surveille le processus de production à partir de terminaux (voire de tablettes) qui lui fournissent en temps réel des données sur le cycle. Le nouvel opérateur est un ouvrier – « si on peut encore le définir ainsi », nous avertit-on dans les interviews – qui n’intervient plus ni manuellement ni en relation avec une seule machine, mais avec plusieurs machines, en surveillance de fractions de plus en plus larges du processus productif.
On va retrouver le même principe chez Ducati Motor, où le système de production lean, implanté depuis les années 2000, est organisé en cellules de production, avec des robots qui effectuent les tâches manuelles pendant que l’opérateur coordonne 10 à 15 machines. Ici encore, les opérateurs vivent un élargissement de leurs missions qui, selon les managers de l’établissement, se traduit par une meilleure motivation au travail.
« Il faut cependant tenir compte du contexte et de l’échelle de production des établissemments, certains facteurs pouvant venir relativiser cette représentation. Là où l’on réalise des pièces uniques, les exigences sont différentes : la polyvalence y reflète plutôt la complexité d’opérations qui ne permettent ni une automatisation intégrale ni la codification des savoir-faire ouvriers. Le temps nécessaire pour accomplir un cycle est un bon indicateur de la complexité et du type de compétences requises par les opérateurs : si le temps de cycle est d’une minute et demie à deux minutes pour un véhicule de série, il est de 17 minutes pour une Ferrari de 8 cylindres et de presque une heure pour la catégorie supérieure, « en conséquence, les ouvriers sont pluridimensionnels. » (Maranello).
Sur les lignes de production qui ont introduit des dispositifs intelligents, l’une des difficultés est la gestion de la variabilité liée à la flexibilité de la production, qui introduit de l’incertitude dans le processus. Ce changement de modèle implique de passer d’une ligne en continu à la possibilité d’intervenir pour modifier les paramètres du flux de production. Cette discontinuité a trois conséquences sur les compétences demandées aux opérateurs : un niveau de connaissances de base en moyenne plus élevé ; une plus grande participation et vigilance tout au long du processus ; une capacité d’adaptation.
« La cellule ne fabrique pas des produits standardisés, mais bien des séries de 23 produits différents. L’opérateur n’est pas sur un poste fixe où il effectue la même opération, il a une capacité dynamique et change de perspective. » (Avio Aereo)
L’usine intelligente exige aussi une plus forte intégration entre la production et les fonctions qui donnent de l’intelligence aux machines, c’est-à-dire l’ingénierie des processus qui fournit les informations nécessaires à l’accomplissement du cycle. D’une part, la conception des postes, des espaces et des mouvements vise à impliquer davantage les opérateurs, dont l’expérience directe et la connaissance des problèmes opérationnels doivent pouvoir être codifiées et incorporées à leur tour dans la conception intelligente des processus. D’autre part, les boucles de rétroaction entre les informations fournies à la production et la production elle-même qui fournit aux systèmes des informations, sont au fondement de l’intégration entre machines, processus et personnes requise par l’usine smart. C’est pour cet ensemble de raisons que l’opérateur doit être à la fois polyvalent, plus coopératif et plus « communiquant » avec la hiérarchie.
À la lumière de ces transformations, l’ouvrier « augmenté » semble devenir la figure centrale de l’usine intelligente : chez Alstom, les ouvriers sont équipés de tablettes ; chez Avio Aereo, ils conduisent et surveillent les flux à partir de terminaux ; à l’entrepôt logistique de Ferrari, ils portent sur eux des dispositifs communicants. Cet opérateur devra en outre disposer d’une connaissance de base de l’anglais – au moins dans les groupes internationaux – et d’un niveau d’éducation secondaire, d’ailleurs communément exigé dans beaucoup d’établissements et de secteurs d’activités, qu’ils soient « smart » ou non. Enfin, les soft skills</> semblent prendre le pas sur les compétences techniques, favorisant les « têtes bien faites » plutôt que les « têtes bien pleines ». Reste à comprendre ce qu’on entend exactement par tête bien faite ou, pour le dire autrement, quel est précisément le profil de compétences jugé utile dans les nouvelles usines. Derrière cette question générale s’en profilent d’autres : émergera-t-il un profil type de ce nouvel ouvrier ? Les changements en cours concerneront-ils toute la main-d’œuvre de l’usine du futur ? L’aliénation deviendra-t-elle un simple souvenir de la phase tayloriste ou voit-on déjà naître une aliénation 4.0 ? Notre ouvrier « augmenté » ne pourrait-il pas aussi se révéler diminué ?
L’ingénieur de nouvelle conception
Tous les entretiens que nous avons menés soulignent l’importance des activités d’ingénierie et du travail de conception dans les processus d’innovation et de développement de projets. Autrement dit, ils mettent l’accent sur ceux qui sont les agents du changement technologique et organisationnel.
Les transformations en cours au niveau de la conception sont encore plus radicales que celles qui affectent les ateliers, avec l’introduction de technologies comme la CAO, la simulation et la modélisation 3D. Bien entendu dans les secteurs high tech ou dans ceux dont l’avantage compétitif repose sur le design et le style, il y a toujours eu une présence marquée de ces professions supérieures ; nous porterons ici notre attention sur deux d’entre elles : celles liées à la recherche et développement et celles qui relèvent davantage du développement et de l’innovation des processus.
Qui travaille dans les départements Recherche des entreprises opère souvent au sein de réseaux horizontaux incluant des laboratoires d’entreprises partenaires, concurrentes ou d’institutions universitaires, qui forment des plateformes partagées. Dans certains secteurs, cette tendance est accentuée par la complexité des produits et des processus, comme en aéronautique : ce passage à l’innovation collaborative peut entrer en tension avec les logiques de systèmes en silos.
Mais c’est au niveau des bureaux d’études que la rupture avec le passé est la plus marquée. Désormais ces ingénieurs fonctionnent de manière beaucoup plus intégrée avec les techniciens de l’aval et travaillent souvent directement dans les ateliers. Les activités de conception se structurent de plus en plus sous la forme d’un engineering collaboratif, répondant à l’objectif de raccourcir les délais de conception grâce aux échanges et à la coopération entre différentes disciplines et niveaux.
L’ingénieur de nouvelle conception voit son travail transformé par l’innovation technologique au moins autant que ses collègues opérateurs. Depuis un certain temps déjà, l’introduction des technologies numériques au service du travail intellectuel produit une transformation des compétences, des modes de coordination, mais aussi de l’essence même de l’activité de conception-développement. La CDAO a rendu beaucoup plus rapide l’obtention d’un résultat, auparavant organisé en phases successives qui allongeaient les délais et multipliaient les risques d’erreurs : on livrait les plans, puis on découvrait que l’usine ne parvenait pas à fabriquer une pièce. Comme celui de l’opérateur au sein des ateliers, le profil de l’ingénieur-concepteur devient multitâche, intégrant des compétences auparavant séparées, telles, par exemple, le calcul et le dessin.
« La conception est assistée par des algorithmes créés pour gérer des problèmes complexes. Quand je suis arrivé dans l’entreprise en 2000, il y avait ceux qui avaient des capacités de calcul et ceux qui traduisaient la conception en plans et dessins. Aujourd’hui, les ingénieurs qui sortent des écoles ont une vision beaucoup plus complète : ils savent concevoir et dessiner de façon intégrée, et évaluer dès la conception les aspects d’assemblage et de mécanique. » (Avio Aereo)
On constate de ce fait une volonté du management de rajeunir les bureaux d’études avec des profils moins conservateurs et plus ouverts au changement.
Ceux qui donnent de l’intelligence aux machines
Qu’est-ce qui donne de l’intelligence aux machines ? En premier lieu, des algorithmes et des logiciels qui sont conçus hors de l’entreprise et achetés à des fournisseurs, leaders dans le domaine de l’automatisation des systèmes et de la mécatronique de dernière génération (pour partie italiens).
Donnent aussi de l’intelligence aux machines ceux qui fournissent les instructions aux machines. Ces fonctions relèvent de l’entreprise elle-même, puisqu’elles nécessitent une connaissance fine des processus de fabrication propres : par exemple, les intégrateurs d’informations opérationnelles, les traducteurs de langages. Elles ne correspondent pas forcément à un métier précis ; ce sont des fonctions « abstraites » qui peuvent être exercées par une même personne ou être attribuées à différents profils de compétences. Chez Alstom, à Savigliano, les professionnels-clés dans ce domaine ont une approche systémique de haut niveau, « capables de coordonner toutes les technologies impliquées dans la production, qui recouvrent dans le cas du Pendolino jusqu’à 50 000 composants différents ». Chez Avio Aereo, c’est le « technologue de production » qui fournit les données de process « de manière à ce que l’opérateur intervienne le moins possible, et concentre son attention sur la fluidité du processus défini. » Le technologue est l’expert de la programmation du système qui doit réussir à ce que l’expérience acquise naguère par l’opérateur sur chacune des machines soit désormais incorporée dans le processus lui-même.
Les quelques profils-types ici décrits n’épuisent pas la variété des organigrammes et des fonctions qui figureront dans l’usine de demain. Il y a des profils aussi bien internes qu’externes qui pourraient y occuper une place croissante. L’analyse, la gestion et le traitement des grandes quantités de données produites par l’usine smart pourraient, par exemple, exiger la création de postes de data analystes.
Plus ou moins compétent ?
Tout saut technologique pose deux questions classiques concernant le travail : quelle sera la quantité de travail nécessaire ? (voir supra p. 65) Quels effets produira cette technologie sur l’enrichissement ou l’appauvrissement du contenu du travail ?
On retrouve ici la polarisation entre « catastrophistes » et « militants de l’innovation » déjà identifiée sur la question de l’emploi. Les premiers pointent une « dégradation du travail » (Braverman, 1978) avec une perte de compétences due à l’extension de l’organisation scientifique du travail et de l’automatisation. Les seconds mettent en avant l’accroissement des compétences, le développement professionnel et le caractère de plus en plus central de la connaissance dans les processus de production. S’ajoutent au débat ceux qui redécouvrent, à l’occasion de l’usine intelligente, le vieux concept de « la professionnalisation pour tous » ou du moins l’extension du modèle du « professionnel » (Wilensky, 1964 ; Bell, 1973), c’est-à-dire d’un travail de plus en plus orienté vers le résultat plutôt que centré sur la tâche.
La digitalisation de la production rouvre les termes d’un vieux débat, à savoir si elle produit (ou produira) une augmentation généralisée des compétences ou si elle contribue (contribuera) à un appauvrissement global de l’expérience au travail et à un « arasement » des compétences humaines. On constate que l’introduction de l’automatisation et des technologies numériques a déjà produit une réduction notable de la composante strictement ouvrière au sein des usines, au point que dans certaines d’entre elles cette catégorie de salariés n’est plus majoritaire.
Les causes en sont nombreuses. Certaines entreprises sont passées d’un modèle relativement « artisanal » à un modèle de production en très grandes séries. L’accès aux marchés mondiaux a imposé des changements d’échelle et d’organisation. Beaucoup d’entreprises ont été rachetées par des groupes internationaux et insérées dans une logique de division du travail mondial plus complexe.
Dans le paysage productif italien, ces changements ont eu un impact bien plus profond que la diffusion du modèle de l’entreprise intelligente, qui n’est qu’une conséquence de la transformation des grands groupes. Dans les exemples que nous avons observés, les investissements technologiques et les réorganisations internes ont eu principalement pour objectif de combiner volumes et qualité, flexibilité et production en série, et de réduire les délais.
Ces changements ont également eu des conséquences sur les profils et les compétences des travailleurs. Par exemple, Giletta, une entreprise italienne spécialisée dans le matériel de désenneigement comme les saleuses, a beaucoup embauché ces dernières années, mais selon différents témoignages, les nouveaux embauchés disposent d’une moindre qualification que par le passé. Cette baisse de la qualification a été rendue possible par la modernisation des équipements de production qui, dans ce cas précis, a entraîné le passage d’une organisation en îlots à une ligne d’assemblage.
En témoignent également les déclarations du management d’Avio Aero, qui établissent un lien entre la réduction des délais de production et le type de compétences recherchées chez les nouveaux embauchés. Ce qui est demandé et valorisé, c’est la capacité multitâches et la vitesse d’apprentissage, augmentées par des dispositifs multimédias, mais on comprend aussi que la rapidité d’insertion des nouveaux dans l’entreprise résulte d’une simplification des tâches.
« Nous avons dû travailler sur des images, des procédures restituées en vidéo, parce que la capacité d’attention de ces jeunes est meilleure sur ces vecteurs auxquels ils sont habitués ; ils ont besoin que les messages soient courts et rapides. Tout doit être facile d’accès et rapide à prendre en main parce que les délais de production se sont considérablement réduits. Le scénario a changé et en conséquence la formation doit rendre l’individu opérationnel en trois mois, et non en deux ans comme auparavant. Evidemment, il n’aura pas une connaissance approfondie de la machine, mais il sera polyvalent et il pourra être utilisé sur davantage de machines au sein d’un même cycle de production. » (Avio Aero)
Ici, la polyvalence et le caractère multitâches sembleraient plutôt correspondre à une forme de diminution de la qualification : savoir plus de choses, avoir une vision plus large du processus, mais aussi en savoir moins sur chaque chose. Il s’agirait d’une sorte d’échange entre connaissances génériques et connaissances spécialisées, échange qui n’apparaît pas en lui-même comme porteur d’un enrichissement du travail pour l’individu. Dans les cas où l’introduction de machines intelligentes dans l’usine est plus avancée, on constate en outre un renversement de la relation homme-machine. Selon le témoignage de Josef Nierling, directeur de Porsche Consulting à Milan, pour le magazine online Linkiesta, dans les établissements Porsche à Zuffenhausen (périphérie de Stuttgart), ce sont des AGV (Automatic Guided Vehicle) qui, dès qu’un ordre est passé, « se mettent en mouvement, de façon autonome, passent par l’entrepôt et demandent les pièces aux magasiniers. Donc ce sont eux, les AGV, qui décident où aller dans l’usine et quoi demander aux employés ou aux différentes machines ». Dans cette même usine, des projecteurs montrent à l’opérateur quelle pièce il doit prendre et où précisément il doit la monter, autrement dit il reçoit une aide visuelle, exactement comme chez Alstom à Savigliano : à chaque station de montage, il y a un écran géant qui reproduit le train en 3D, permettant de passer du code à la pièce et à l’instruction de montage. Le montage d’un train est une opération très complexe qui présuppose une grande attention et un grand nombre d’informations ; celles-ci sont ainsi détenues par des « tuteurs » numériques, bien plus que par les opérateurs. Comme nous l’explique le directeur de la conception d’Alstom, une fois que vous disposez de la formation pour décoder les informations proposées par les écrans, vous pouvez participer à l’acte productif sans avoir aucune compétence spécifique. Pour une entreprise de ce type, c’est un atout-clé qui permet d’intégrer rapidement du personnel temporaire sans expérience ni compétences techniques particulières pour faire face aux pics de production.
Pour autant, des situations de ce type ne signifient pas que la transition en cours vers des tâches plus gratifiantes ou enrichies ne soit qu’une rhétorique. Si l’on se remémore les anciennes tâches parcellisées du modèle tayloriste qui en Italie semble vraiment appartenir à un passé révolu, le degré de polyvalence, le niveau de formation initial, le rapport aux nouvelles technologies et la recomposition des missions dessinent un contenu du travail profondément transformé et, sur certains aspects, plus désirable. La qualité du travail n’est cependant pas un concept unidimensionnel : elle est faite d’aspects ergonomiques, environnementaux, mais elle est également liée à l’autonomie, au « pouvoir », à la variété des activités, aux récompenses matérielles, etc.
À la lumière des témoignages recueillis, il serait très exagéré de vouloir faire passer les nouveaux opérateurs pour des quasi-travailleurs de la connaissance. L’image d’une montée générale des compétences traduit davantage une vision et un vœu qu’une réalité empirique.
L’industrie 4.0 en est à ses prémices, et il est donc prématuré de prétendre tirer des bilans. Il semble cependant assez clair que la main-d’œuvre de production dont aura besoin l’usine intelligente disposera de compétences plus génériques que par le passé, tandis que les machines « intelligentes » absorberont une partie des capacités et connaissances autrefois « vivantes » et les transformeront en unités d’information reproductibles, stockées dans des bases de données, afin de les réallouer le long du cycle de production.
« Nous avions des ouvriers qui construisaient des trains pratiquement sans dessins. L’ouvrier connaissait le train, il l’avait construit depuis toujours, il avait quasiment hérité sa connaissance. Il possédait toute l’histoire des trains précédents, donc quand une nouvelle commande arrivait, il complétait l’information manquante par son expérience, son vécu, la somme des erreurs antérieures. Autrement dit, il avait du métier. Mais chaque fois qu’un de ces hommes sortait du cycle productif, nous nous retrouvions avec un gros problème, parce que cette somme de connaissances n’était pas dans une base de données, elle était en chaque homme. » (Alstom)
Les usines semblent avoir plus que jamais besoin d’homogénéiser les langages, ceux des machines comme ceux des hommes. En définitive, de ce passage de la connaissance spécialisée vers la connaissance générique, l’ouvrier ressortira-t-il plus fort ou plus fragile ? Est-ce qu’il sera plus désirable pour l’entreprise ou plus substituable ?
Même le travail cognitif de niveau supérieur, central dans l’usine intelligente, semble toujours plus organisé et structuré en fonction des nouvelles exigences d’intégration et de coopération, et soumis aux technologies et à la réduction des délais. L’activité de conception dépend elle-même des marchés, du time to market, et subit en conséquence une pression à l’organisation de pratiques reproductibles : quand le temps de conceptiondéveloppement d’un produit devient une variable stratégique, il faut l’assortir de technologies capables de « potentialiser » et d’organiser les coopérations entre ingénieurs et entre professions créatives. À tous les niveaux de la hiérarchie, on ressent la perception diffuse que le travail non seulement s’intensifie mais se standardise de plus en plus (Huws, 2010).
Même si, dans la production industrielle du futur, la ressource clé réside dans la génération et l’application systématique du savoir, la connaissance ne peut pas être considérée comme un objet unique : elle dépend de son type, de son usage, du niveau hiérarchique où elle se concentre. C’est pourquoi, il semble difficile de croire à cette image d’une élévation collective des compétences, qui concernerait tous les travailleurs de l’usine intelligente.
Nous l’avons dit, dans l’usine intelligente, la production du savoir et de l’innovation n’est pas concentrée uniquement dans les laboratoires de R & D. Elle prend forme à travers un système d’interrelations. Il y a des systèmes horizontaux qui font coopérer chercheurs et ingénieurs avec leurs collègues dans d’autres divisions de l’entreprise ou dans d’autres entreprises, y compris des fournisseurs, des clients ou des concurrents, et avec des laboratoires universitaires et des centres de recherche publics. Il y a aussi des systèmes verticaux au sein de l’entreprise qui connectent conception, développement et production, diluant les hiérarchies pour favoriser la capacité à engendrer des informations et des apprentissages communs. Il y a enfin les relations avec le marché, c’est-à-dire la capacité à traiter les informations provenant des clients qui est un des points-clés de l’industrie du futur.
Derrière le premier niveau de production de la connaissance, il devient nécessaire d’opérer un travail de traduction de cette connaissance en informations reproductibles qui puissent être intégrées dans des systèmes et machines nécessaires à la coordination des hommes. Enfin, il existe encore un autre niveau qui en volume est le plus important : l’application, transfert, stockage et circulation d’unités de connaissance plus petites, générées de manière automatique et permanente par les machines connectées. À chacun de ces niveaux, s’opère une division cognitive et hiérarchique : même en R & D, il existe beaucoup d’opérations de routine, alors qu’à l’inverse, certaines tâches de production nécessitent de mobiliser des connaissances en s’adaptant à des contextes divers et imprévus qui n’ont pas pu être intégrés dans des programmes standards de pilotage des machines.
Nouvelles hiérarchies
Hybridation, intégration, coopération ou raccourcissement de la boucle « recherche, conception, développement, production » ne signifient pas pour autant que la hiérarchie interne à l’usine se soit aplatie. Il s’agit cependant de formes hiérarchiques différentes, fondées sur un pouvoir qui dérive de la connaissance.
Pour comprendre ces nouvelles stratifications, on peut partir du fait que découper un cycle de conception-production en séquences successives et séparées est aujourd’hui dépassé du fait des exigences du time to market.
« Si l’on faisait encore de la conception avec les outils traditionnels de modélisation, on ne découvrirait vraiment comment articuler les différentes parties qu’après avoir construit le premier train. Ce qui serait bien tard. Comme notre marché exige la livraison clé en mains d’un train en 13 mois, l’ancien procédé ne tient plus la route. Nous devons superposer conception et fabrication. » (Alstom)
« Le marché demande aujourd’hui de s’adapter rapidement, mais par nature, les composants d’une centrale électrique ont un temps de réalisation long. Pour mener à bien un projet d’amélioration d’une turbine, il faut à peu près 18 à 24 mois, de la conception à la production. Pour fabriquer une turbine à gaz, il en faut 15 de plus, depuis le moment où les premiers matériaux entrent dans l’usine jusqu’à la sortie de la turbine finie. Quand le client te demande un nouvel équipement en 10 mois, tu ne peux pas y arriver si les éléments ne sont pas pour une grande part déjà construits. Il faut donc rechercher un équilibre entre le développement, la réalisation et les opportunités de marché. » (Ansaldo Energia)
Dans les configurations les plus évoluées technologiquement, cette exigence de compression des temps a conduit à une véritable imbrication du travail des concepteurs technologues avec les salariés de la production. Il n’est pas rare de voir dans les ateliers un ensemble indifférencié de fonctions de production, contrôle, supervision et développement, mais ces interactions renforcées ne traduisent pas une relation entre égaux ; au contraire, elles soulignent l’existence d’une différence hiérarchique fondée sur le savoir entre ceux qui fournissent les données du processus et ceux qui surveillent qu’il se déroule conformément aux prévisions et sans heurts majeurs.
Cependant, l’un des effets induit par cette intégration est l’exigence de développer un langage commun. D’où la nécessité pour l’ingénieur de maîtriser l’anglais et pour l’opérateur d’en avoir des bases. La deuxième « langue » commune est une sorte « d’alphabet » technologique, composé d’informations numériques et visuelles. La formation du personnel dans les Factory Academies qui tendent à se développer dans les plus grandes entreprises consiste avant tout à créer cette socialisation cognitive et linguistique du « savoir » organisationnel, codifié et rendu accessible à l’ensemble de la communauté que constitue l’établissement. Si le savoir doit être défendu et contrôlé vis-à-vis de l’extérieur, il est en revanche décloisonné et diffusé en interne, afin que les compétences ne soient pas concentrées sur quelques individus qui pourraient représenter des goulets d’étranglement.
« D’habitude quand un jeune arrivait, le senior avait peur de partager ses connaissances. Mais nous avons construit un pacte intergénérationnel, dans lequel les anciens aident les jeunes et les jeunes, les anciens, dans la mesure où les uns ont l’expérience et les autres, l’agilité numérique. C’est un modèle d’échange entre pairs dans lequel tout le monde est gagnant. » (Alstom)
L’usine 4.0 peut aussi être analysée à travers trois grands modèles d’intégration : homme à homme, machine à machine, homme à machine. Nous avons vu comment la smart factory peut renforcer les rapports de coopération à la fois en amont (recherche, conception, design) et en aval (entre opérateurs), mais aussi entre ces deux niveaux. Quant aux machines, elles ont vocation à dialoguer entre elles en autonomie. Mais y a-t-il, dans ce contexte, une reconfiguration de la relation homme-machine ?
On trouve à ce sujet deux types de projection. D’une part, est promue la figure de l’opérateur qui régule et surveille un processus de production rendu quasiment autonome par la puissance et la précision des données contenues dans les machines ; de l’autre, on imagine un opérateur qui dirige en chef d’orchestre un système complexe de robots et de dispositifs numériques. La réalité est probablement plus complexe : à l’heure actuelle, il est clair que les compétences humaines sont indispensables, compte tenu du niveau « d’intelligence » extrêmement limité des machines. Les machines numériques continuent à avoir besoin en continu du travail humain.
Du reste, dans l’histoire industrielle, le rapport homme-machine n’a jamais connu d’harmonie exemplaire ; la chaîne de montage n’a jamais fonctionné exclusivement grâce aux prescriptions rationnelles de l’ingénieur Taylor, mais bien plus souvent malgré ces prescriptions. Ce sont les connaissances tacites et les savoir-faire des opérateurs qui ont donné de la valeur à ce mode d’organisation, en sortant des schémas rigides et des rythmes imposés par l’usine tayloriste. Dans l’usine intelligente, il importe de s’interroger sur quelles seront les capacités humaines que les machines pourront totalement prendre en charge, lesquelles impliqueront une nouvelle combinaison des parts respectives de l’homme et de la machine, et lesquelles ne pourront être exercées que par l’homme.
Dans cet écart entre projection et réalité, il y a ce qu’on appelle la « subjectivité » des travailleurs, c’est-à-dire leurs valeurs, culture, perceptions. Si l’on veut faire de l’expérience et des savoir-faire individuels une base de connaissances partageables, il va falloir négocier avec ceux qui les détiennent. Imaginer la transformation du rapport homme-machine soit comme un grand mouvement sans frictions, qui nous conduira tout droit à l’avènement du « grand automate 4.0 », soit comme le Grand soir de la libération face au travail aliénant, sont deux représentations fantasmatiques et sans aucun fondement réel.
- 16. Voir sur ce sujet, pour la France, Cahier et Charlet, Rebondir et se réinventer : la résilience des ETI industrielles , Les Notes de La Fabrique, La Fabrique de l’industrie, Presses des Mines, 2017.
- 17. Pour une vision complète des thèses en présence, voir « Numérique et emploi : quel bilan ? », Les Synthèses de La Fabrique, n°12, avril 2017.
Point de vue – L’expérience italienne d’Alstom Ferroviaria
Par Pierre-Louis Bertina, ancien président et actuel vice-président des conseillers du commerce extérieur de la France – comité Italie, ancien Presidente Amministratore Delegato de Alstom Ferroviaria, chevalier de la Légion d’honneur.
Le 4.0 s’est imposé de lui-même chez Alstom Ferroviaria à un moment où les unités italiennes vivaient une période de crise aiguë avec tous leurs clients. Alstom décide alors d’investir pour apporter des réponses à un marché ouvert à la concurrence nationale et étrangère. Compétitivité, qualité totale et respect des engagements seront les trois piliers sur lesquels s’appuieront toutes nos propositions et actions. Le digital en sera le ciment.
Cette transformation a permis d’assurer :
• un « time to market de 13 mois » : temps écoulé entre la commande et la première livraison ;
• un rythme de production intensif : 4 trains régionaux et 2 trains grande vitesse par mois ;
• un niveau de qualité proche du zéro défaut. Elle se mesure entre autres, au moment de la mise en service des trains, par les taux de fiabilité et disponibilité de la flotte ;
• la résorption des pics d’activité, d’où le renforcement de l’offre industrielle ;
• un design à la demande, avec des possibilités infinies.
Nous remettions le client au centre de notre action : après tout, c’est par lui et pour lui que nous existons. Ce que les clients de nos clients – les passagers – ne voyaient pas devait être standardisé. Nous devions, en revanche, intégrer leurs desiderata en matière de confort physique, visuel, d’informations voyageurs, de wi-fi… et avoir la possibilité de les faire évoluer.
La modélisation 3D du train est devenue la colonne vertébrale de toutes les activités de l’entreprise, actualisées en temps réel : du marketing, du design, de la production, des essais et de la maintenance mais aussi des achats, de la finance. Auparavant il y avait les équipes, aujourd’hui il y a « l’équipe ». La réalité virtuelle anticipe et permet de vérifier la faisabilité physique, l’ergonomie et les fonctionnalités du produit, afin d’éviter les erreurs du « retour usine » qui coûtent fortune et réputation.
On est loin de l’usine qui sentait la graisse. Les tablettes au bord de la chaîne s’activent pour dicter à l’opérateur les opérations de montage. À son domicile, dans le métro, sur son lieu de travail, l’ouvrier ne quitte plus sa tablette. Ce qui s’affiche sur l’écran est différent mais le mode de communication est le même : je fais mes achats personnels, je joue, je suis les instructions de montage des équipements du train.
Nous avons pu imaginer un tel processus chez Alstom Ferroviaria parce que nous faisions partie d’une multinationale qui, avec ou sans le soutien d’entités publiques, avait déjà développé des outils similaires, aptes à soutenir cette transformation.
La formation
La transmission de l’information ne se fait plus selon le bon vouloir de chacun. Celle-ci est à la disposition de tous. Le nouveau venu est rapidement mis à niveau grâce aux simulateurs. L’expérience des anciens a été intégrée dans les processus industriels gérés par les moyens digitaux. L’expérience Alstom ne s’est pas traduite par des licenciements. L’ancien a la connaissance, le jeune a l’agilité du digital. Les deux, ensemble, font merveille car tout n’est pas encore « en boîte » dans le processus.
Une des clés du succès de la transformation : trouver et former les bons relais à l’intérieur de l’entreprise, en choisissant si possible des passionnés de leur travail. Les profils et le rôle des opérateurs changent progressivement. La polyvalence s’impose, de même que la flexibilité des horaires pour faire face à la variabilité de la demande. L’homme ne doit pas empêcher ce que la technique industrielle 4.0 lui permet d’accomplir. La qualité du dialogue avec les instances syndicales s’avère donc clé.
Enfin, à un moment où la QVT (Qualité de Vie au Travail) devient discriminante dans le choix des jeunes, il faut noter que le 4.0 contribue à rendre l’industrie plus attrayante.
Débat sur le low cost
Considérer que nos implantations industrielles européennes ont atteint leur apogée en matière d’efficacité et que mieux vaut investir dans des pays low cost est une grossière erreur de perspective. Le 4.0 constitue un frein aux délocalisations qui souvent règlent le problème immédiat – rendre l’offre compétitive – mais ne résolvent pas toujours l’affaire in fine, en raison des risques d’augmentation des coûts et d’allongement des délais : ceux-ci ne relèvent d’ailleurs pas de la responsabilité du pays « usine » mais plutôt de la complexité et spécificité du produit inhérent au type d’industrie.
La désindustrialisation est insidieuse et, sauf action énergique, l’industrie continuera à se déplacer lentement hors de nos frontières en même temps que nos brevets. Le 4.0 constitue une arme sûre pour combattre cette érosion, surtout lorsque les séries de production sont limitées et que la proximité client est importante. La flexibilité et la réactivité jouent alors en faveur de l’industrie locale.
Les pays dits industriels sont ceux :
• qui ont réussi à mettre en place un dialogue constructif syndicats/grandes entreprises – comme en Allemagne – et sont capables de se projeter ensemble sur les cinq ans à venir ;
• qui ont inventé un fonctionnement en réseau de petites entreprises – comme l’Italie, deuxième pays manufacturier européen après l’Allemagne. Ce système a aussi ses limites structurelles et c’est ce que souligne l’étude : le 4.0 n’a pas encore trouvé son chemin dans les PME.
Investir dans nos usines européennes, ce n’est pas nier le besoin de mondialisation et de recherche de solution low-cost : tout tient dans le juste équilibre.
Le futur et les clés du succès
« La seule constante c’est le changement. » Il faut rester à l’écoute. L’homme reste central. C’est lui qui peut faire évoluer le modèle et les machines, y greffer les start-up. À un mo- ment où tout bouge et où personne ne peut dire dans quel sens, il est important de détenir des positions dans plusieurs territoires et parties du monde.
L’industrie restera un lieu d’assemblage mais sera toujours plus digitalisée et plus intelligente pour pouvoir aussi assurer le service et le sur-mesure pour les clients qui ont un fort impact sur le produit final.
La qualité du produit et la satisfaction du client incombent aux hommes et aux femmes placés dans ce processus industriel maîtrisé grâce au digital. Une machine n’a pas d’orgueil et de sensibilité. Les personnes, elles, en ont, même si elles ont perdu du savoir individuel.
De façon innée, les entreprises italiennes poursuivent leur action innovante et créative, bien insérées qu’elles sont dans le jeu mondial. Le défi pour les petites entreprises fonctionnant en réseau, vitales pour l’économie, sera de s’appuyer sur des processus 4.0 permettant de maintenir leur niveau de compétitivité.
La personne 4.0
Hommes et numérique
L’Industrie 4.0 recouvre à la fois des innovations technologiques et des innovations organisationnelles ou, pour le dire simplement, elle concerne simultanément les machines et les hommes.
Ce nouveau paradigme repose sur une rhétorique particulière concernant le travail, le travailleur et les lieux de travail dans leur imbrication avec le digital : « Une usine est bien plus qu’une simple combinaison de machines et de processus automatisés pouvant être facilement délocalisés dans n’importe quel endroit du monde. C’est une entité fondée sur la coopération intelligente entre l’homme et la machine, sur une innovation technologique dont la finalité est de stabiliser la production manufacturière localement et globalement, afin de maintenir l’emploi en Europe », indique un document stratégique de l’EFFRA. La réflexion européenne dessine une industrie du futur dans laquelle l’homme est au cœur d’une vision et d’un but. On y trouve pêle-mêle des orientations telles que : la flexibilité du temps de travail ; la diminution de la pénibilité permettant d’alléger les efforts demandés aux travailleurs âgés ; le développement, la gestion et la capitalisation des connaissances ; les interfaces permettant aux travailleurs de visualiser et simuler le processus de production, etc. Cette vision invite à penser l’usine comme lieu d’innovation sociale autant que technologique ou encore comme opportunité de créer une nouvelle culture du travail dans l’intérêt des travailleurs.
En échange, qu’est-il demandé au travailleur de demain pour devenir acteur de cette usine du futur ? Faire plus et mieux en termes de gestion de la complexité, capacité d’abstraction et résolution de problèmes. Savoir agir de sa propre initiative et avec à-propos, avoir des capacités relationnelles et de communication, savoir se coordonner avec autrui au sein d’une équipe. En résumé, il lui est demandé de mettre en œuvre son potentiel propre et ses capacités « subjectives », qui viendront enrichir son travail sur un plan qualitatif, favoriseront son autonomie, tout en contribuant à rendre l’environnement de travail plus intéressant et à améliorer l’expérience professionnelle dans son ensemble.
En d’autres termes, cette vision propose un dépassement de tout ce qui dans le travail est répétitif et monotone, en posant un principe (abstrait) d’autonomie, déjà mobilisé dans le monde des services et des professions libérales. Ce principe qui traverse dès lors tous les champs du travail, est vu comme l’élément capable de produire, par lui-même, l’innovation sociale au sein de l’usine.
Pourtant, la pénétration systématique des technologies numériques dans le travail représente également une menace potentielle pour le maintien et le développement du capital humain. En effet, il est de mieux en mieux établi que certaines franges de la population sont exclues du travail par la « fracture » numérique. Il en résulte que, si les technologies numériques, après avoir occupé une place centrale dans la vie quotidienne, entrent massivement dans les lieux de travail, l’alphabétisation numérique devient une condition sine qua non pour réduire ces inégalités et permettre l’accès au travail.
Le concept de fracture numérique a connu différentes phases d’évolution. Au début de la diffusion d’internet, dans les années 1990, l’attention a été portée sur la fracture entre connectés et non connectés, recouvrant une double acception : global divide entre zones et pays du monde ; social divide entre segments d’une même population, lié à des facteurs d’âge, genre, origine sociale, éducation, localisation, etc. Avec le passage au nouveau millénaire et la généralisation d’internet, le problème s’est déplacé de la question de l’accès aux technologies à celle de la capacité à saisir toutes les opportunités offertes par ces technologies et des compétences nécessaires pour y parvenir.
On parlera donc plutôt aujourd’hui d’« inégalités numériques », dans la mesure où l’usage des technologies et médias numériques n’est plus un choix de consommation culturelle parmi d’autres mais une véritable obligation. Les compétences numériques deviennent un instrument conditionnant la participation à la vie sociale. Selon le sociologue Jan Van Dijk (2005), les inégalités numériques reposent sur trois facteurs : l’accès mental, c’est-à-dire l’attraction qu’exerce une technologie sur une personne donnée ; l’accès matériel, c’est-à-dire la disponibilité de la technologie pour cet individu ; enfin, l’accès à l’usage, c’est-à-dire la capacité à utiliser tout le potentiel de ladite technologie.
Les inégalités numériques se greffent sur les anciennes inégalités sociales, sans pour autant les recouper totalement. Il est important de garder à l’esprit cette question des inégalités, lorsqu’on discute des modèles de travail véhiculés par l’industrie du futur. Car l’objectif est bien de tenir ensemble évolution technologique, maintien et développement des compétences, et organisation du travail. C’est seulement à cette condition que les nouvelles interactions qui viennent innerver la totalité de la chaîne de valeur pourront améliorer la vie et le travail des individus. Ce point de vue place l’homme au centre et non aux marges de la technologie, comme l’ont affirmé avec force les syndicats allemands (Industry-Science Research Alliance et Acatech, 2013) à travers deux slogans : better, not cheaper et good and fair jobs. L’innovation technologique doit ouvrir la possibilité d’une offre de travail meilleure et plus juste, elle doit garantir la continuité de l’usine et de son capital humain et favoriser la codétermination des travailleurs.
Tullio Tolio, professeur à l’École polytechnique de Milan et président du comité scientifique du cluster italien Fabbrica Intelligente (i. e. Usine intelligente), insiste sur cette centralité de l’homme et son rapport à l’automatisation :
Nous avons toujours parlé ici de l’usine de l’homme, parce que l’interaction de l’homme avec l’usine sera toujours plus forte. Pendant longtemps, nous avons pensé que l’homme pouvait faire une chose et la machine, une autre, mais je crois que dans l’avenir, l’homme et la machine travailleront ensemble. Quand je pense à cette usine évolutive, je pense avant tout à l’homme, parce qu’il est le seul à pouvoir produire le changement, les machines, elles, ne savent pas changer.
La culture des médias numériques entre dans l’usine
On peut comparer le passage de l’usine traditionnelle vers l’usine 4.0 avec les transitions advenues dans notre environnement, lorsque nous sommes passés des TIC aux médias numériques. Nous avons vécu un déplacement du hardware (l’équipement, l’outillage) vers le software, c’est-à-dire un environnement « communicationnel » dans lequel la machine se met à parler un langage interpersonnel. Smartphones, tablettes, portabilité, systèmes connectés en permanence à Internet nous ont habitués à une médiation « naturelle » dans nos relations et actions quotidiennes, que nous avons tout naturellement transposée dans nos pratiques de travail.
Utiliser le terme « médias numériques » au lieu de « technologies numériques » a pour but de bien marquer la distance qui existe entre une vision strictement instrumentale de ces technologies et leur rôle social. Si les TIC correspondaient à l’idée d’une technologie-instrument (i. e utile pour exécuter des tâches), les médias numériques nous parachutent dans le monde de la communication, c’est-à-dire dans un système de relations sociales. Les technologies numériques ont ceci de spécial qu’elles permettent d’établir à la fois des relations entre les individus et la réalité matérielle (ce sont des outils pour l’action) et des relations entre les individus et la collectivité (ce sont des environnements sociaux).
Ces outils ont d’abord envahi nos vies quotidiennes, nos habitations et nos villes, nos relations interpersonnelles et affectives, et ce n’est qu’après qu’ils sont devenus des instruments de communication et de contrôle au sein des lieux de travail, dans les bureaux et les usines.
Les compétences et pratiques relatives à ces technologies, lorsqu’elles sont appliquées dans les secteurs productifs, reposent donc essentiellement sur une alphabétisation digitale acquise à travers l’expérience personnelle, plus que par l’expérience professionnelle. Le monde immatériel des services, de la connaissance, de la communication, des réseaux et le monde matériel des « choses » tendent à partager les mêmes instruments, langages, et donc culture.
Les technologies numériques sont principalement des environnements de communication, intermédiation et relations entre personnes, lieux, objets et machines. Il en ressort que pour comprendre les liens entre ces technologies et les formes du travail contemporain, et en particulier le passage de l’automatisation des usines vers la construction d’univers communicants au sein de l’usine digitale, il faut prendre en compte le langage spécifique de ces médias, leurs règles, leur affordance18 agency19.
Le concept d’agency dans la théorie de l’acteur-réseau proposée par le sociologue Bruno Latour (2005) nous offre ici un cadre d’analyse. Par le terme agency, il entend la capacité de la technologie à prédisposer à l’action. Le travailleur qui utilise les technologies numériques dans l’exécution de ses tâches est soumis aux possibilités et aux limites des instruments qu’il utilise (c’est l’affordance, terme forgé par l’ingénieur et psychologue américain Donald Norman) et il est confronté à la manière spécifique dont ces technologies cadrent l’usage qu’il peut en faire. Le rapport entre l’individu et la technologie est donc caractérisé par une distribution des compétences : l’acte final accompli par le travailleur est déterminé par ses capacités mais aussi par les options que lui offre la technologie, dans un mouvement continu entre innovation et routine, entre créativité et répétition.
Le travail et les missions qui utilisent le numérique dépendent donc des caractéristiques propres à l’agency numérique. La première de ces caractéristiques concerne les modalités procédurales : les actions de travail deviennent des parcours à options qui déterminent le résultat final. La deuxième est l’ouverture, c’est-à-dire que les actions sont caractérisées par un degré de flexibilité et de variabilité. La troisième est la logique dite de « versions » : les actions et modalités de travail sont considérées comme toujours imparfaites et inachevées, et sont donc orientées vers l’amélioration continue, exactement comme des logiciels qui sont en permanence actualisés par de nouvelles versions. La quatrième est « l’immanence de l’action dans le processus » : la faculté d’exercer une option est directement encapsulée dans le processus au point que l’action prévaut sur tout autre choix. La cinquième peut être résumée par la formule « embodied gesture, natural interfaces » : les médias numériques développent un rapport naturel avec l’homme et les interfaces suppriment la médiation entre travail et travailleur ; en fait, la médiation homme machine existe encore, mais elle est devenue transparente. La sixième et dernière caractéristique est la connexion permanente : la production devient un flux continu de données qui engendrent une hyper connexion entre information-action-boucle de rétroaction ; cette masse de données est nécessaire pour réagir de manière flexible et rapide, mais elle implique également la disparition de tout espace privé entre le travailleur et son travail.
Le programmateur et artiste Lev Manovich (2002) décrit à son tour les technologies numériques selon quatre principes – représentation, modularité, automatisation et variabilité.
Le code ayant une nature mathématique, il en résulte que le contenu et les instructions des médias numériques pourront toujours être décrits en termes mathématiques ; ils pourront être sujets à des manipulations d’algorithmes et seront reprogrammables à volonté. Appliqué au monde de la production matérielle, le travail assisté par le numérique aura donc des caractéristiques d’ouverture et de reconfiguration permanente, mais également de fermeture sur l’algorithme qui structure la relation entre l’acte de travail et le résultat de l’action.
C’est cette composante qui peut être considérée comme l’une des formes d’aliénation de l’usine du futur : l’équilibre entre ouverture et fermeture des processus, entre la possibilité pour le travailleur de les contrôler grâce à son intelligence et l’automatisation engendrée par les algorithmes qui expulsent du processus l’élément humain, constitue le point caractéristique et différenciant de l’usine digitale par rapport à son ancêtre automatisée.
En définitive, un processus automatisé évacue en tout ou partie l’intentionnalité humaine ; l’algorithme à la différence de l’automatisation mécanique ne dépossède pas l’homme de sa capacité à agir, mais il déplace la responsabilité du processus décisionnel sur les utilisateurs de la technologie. Les processus digitaux attribuent aux utilisateurs la responsabilité de se représenter le monde et d’agir sur lui ; l’automatisation numérique se distingue donc de celle mécanique par le degré d’interaction et de variabilité offert à ses utilisateurs.
Toujours selon Manovich, un contenu numérique est modulaire : il représente les images, les formes, les sons et les comportements comme des briques discontinues (pixel, script, etc.) qui, même assemblées dans des structures de dimensions plus vastes, continuent d’avoir une identité séparée. Cette nature modulaire rend le contenu, c’est-àdire le travail, décomposable en parties réutilisables au sein de diverses configurations, et c’est de là que dérive son caractère reproductible, standardisable et économique. Une standardisation qui n’est pas statique puisqu’elle s’accompagne de variabilité : un contenu numérique ne reste jamais identique, il peut être décliné en versions très différentes les unes des autres.
Par honnêteté, il faut cependant reconnaître que ériques est souvent limitée à « variation sur le même thème », c’est-à-dire à des facultés de choix à l’intérieur d’un nombre limité d’options. De la consommation à la production, le « travail » qui utilise ces médias tend à s’éloigner des schémas intégralement routiniers ou standardisés; ils permettent de créer, au moins potentiellement, une routine «à géométrie variable».
Dans le monde des médias numériques, cela signifie partir des usages pour concevoir de nouvelles applications et rendre l’utilisateur co-producteur ; l’utilisateur passe d’un état passif au statut de prosumer (terme forgé par Alvin Toffler à partir de producer et consumer). Dans l’usine intelligente, la centralité du client se traduit par la personnalisation des produits et par l’intégration de la commercialisation au sein même de la conception : la production utilise le feed-back de la vente pour modifier les produits à la vitesse de l’éclair ; la production devient ainsi « consumer-responsive ».
On parle ainsi de « personnalisation de masse » à la fois dans le cas des médias numériques et de la production flexible, avec une gradation qui va d’une possibilité minimale à agir sur le processus jusqu’à une capacité maximale de l’usager-client à coproduire le contenu ou le bien. Par exemple, dans le secteur automobile, on trouvera à une extrémité la simple possibilité de choisir les options de son véhicule et à l’autre, la possibilité (théorique) de produire sa propre voiture en « do-it-yourself » comme dans le cas de Tabby.
Tabby est né de la collaboration entre le designer italien Ampelio Macchi et son homologue chinois Francisco Liu, qui ont conçu ensemble le premier modèle de véhicule open source. C’est un concept de mobilité ouvert, fondé sur l’idée que les biens matériels comme les logiciels peuvent intégrer l’éthique de l’open source. Ils ont donc mis à la disposition du public des plans techniques sur lesquels les usagers peuvent intervenir. Comme le montre l’exemple de Tabby, la culture digitale a ceci de particulier qu’elle permet de mettre l’usager au centre des processus, en créant des relations réticulaires fondées sur des mots-clés tels que collaboration, coproduction, partage. Un modèle qui est moins loin qu’on ne pourrait le croire du modèle de relations verticales entre base et sommet, travailleurs et direction. Car, même dans ce modèle classique d’organisation du travail, on ne cesse désormais d’invoquer la rhétorique de l’implication et de la participation des travailleurs aux processus opérationnels, voire décisionnels.
Le monde de l’automobile est, il est vrai, un laboratoire de l’hybridation entre industrie traditionnelle et industries numériques, et pas seulement parce que les véhicules encapsulent de plus en plus de dispositifs digitaux pour rendre nos transports plus plaisants et plus divertissants. Le cas le plus célèbre de cette hybridation des genres est Tesla, le constructeur automobile créé en 2003 dans la Silicon Valley pour développer des voitures électriques à partir d’un processus de conception et production hors du commun. Au cœur du système Tesla, il y a une logique collaborative conduisant à partager l’innovation technologique avec des centres de recherche, des fournisseurs et même des concurrents comme Lotus, Toyota et Daimler, afin de réussir à construire un véhicule sans détenir toutes les briques de ce qui demeure sans doute l’une des industries les plus complexes et diversifiées au monde. C’est ce qui a conduit Tesla à appliquer une philosophie open source à ses brevets, utilisables par chacun, témoignant ainsi d’une conception originale de la propriété industrielle. L’entreprise a ainsi ouvert la voie et a été suivie par d’autres, comme Toyota pour ses brevets sur les piles à hydrogène. L’objectif poursuivi par ce type de démarche est d’inciter les parties prenantes à proposer des améliorations et des innovations dans une logique de développement continu. En revanche, Tesla construit en propre certains éléments que les constructeurs sous-traitent habituellement, comme le volant, de façon à bénéficier d’une fertilisation croisée entre différents secteurs d’activité. Travaillant en incertitude radicale, Tesla mise avant tout sur l’innovation et la rapidité, y compris dans les modalités d’organisation du travail où la sélection est rude, les objectifs, autant de défis, et le personnel, essentiellement composé de « pionniers » et « talents ». En d’autres termes, un modèle organisationnel inspiré du numérique et appliqué désormais à l’industrie manufacturière.
Au caractère central de l’utilisateur-client répond la centralité du travailleur dans l’usine 4.0. Comme si, de l’extérieur vers l’intérieur, était mobilisée une même culture de la participation. Les pratiques de travail inclusives décelées dans les usines dépendent, en effet, beaucoup des outils de travail que l’on y trouve, et de la culture qui en dérive. La culture participative qui, selon le sociologue des médias Henry Jenkins (2007), caractérise les médias numériques entre en résonance avec le modèle toyotiste d’organisation du travail, qui trouve un prolongement dans l’usine 4.0.
L’archétype du travailleur dans l’usine du futur est un individu participatif et proactif, à l’opposé du travailleur traditionnel, « réactif » et faisant preuve de « résistance ». Ces deux dernières notions sont empruntées à Manuel Castells, dans son essai Le Pouvoir de l’identité20, qui distingue les « identitésrésistances », centrées sur des projets identitaires communautaires (nation, terroir, ethnie, religion, etc.), des « identités-projets », embryons de formes nouvelles d’organisation sociale (droits de l’homme, écologie, féminisme non fondamentaliste, etc.). En transposant cette grille de lecture à l’usine, on peut considérer que le travailleur de l’usine tayloriste construisait sa propre identité à travers un processus basé sur la résistance aux logiques de domination, dont il était à la fois victime et exclu, jusqu’à ce qu’il parvienne à se construire une « identité-projet », en adhérant aux mouvements ouvriers. Mais dans une organisation qui met au centre la participation du travailleur (sur le modèle de la participation des usagers aux médias numériques), celui-ci doit devenir pro-actif et résilient, c’est-à-dire affronter de manière positive des événements traumatiques, en réorganisant sa propre vie face aux difficultés ; on pourrait dire que l’industrie 4.0 met le travailleur devant un choix « tragique » (au sens du dilemme de la tragédie classique) : il ne peut plus se contenter de résister, il doit ré-agir pour survivre.
Enfin, on peut dire que position pro-active et rôle participatif correspondent à un processus de subjectivation du travailleur (sur lequel nous reviendrons plus loin p. 100) par lequel la responsabilité devient partagée. Car participer signifie aussi être co-responsable, ce qui se traduit par une nouvelle approche du rapport coût-bénéfice des actions et des attentes. Cette tendance, qui se répand dans toutes les sphères de travail, est considérée comme critique (Armano, Murgia, 2012 ; Morini, 2010) dans la mesure où la plus grande responsabilité accordée aux individus s’accompagne d’une plus grande vulnérabilité en termes de pouvoir et de perspectives.
Entre la dimension collective qui caractérise le couple « identité-résistance, identitéprojet », et l’individualisme de la société contemporaine, le travail 4.0 propose une troisième voie : celle de l’équipe. Fonctionnelle, flexible mais aussi éphémère, l’équipe opère dans un espace et un temps limités, liés aux impératifs d’une production rapide et reconfigurable (ici encore comme les communautés sur les médias numériques). Ce modèle se répand rapidement sous nos yeux, et bouscule des rôles, des pratiques et des cultures sédimentées.
L’ouvrier-artisan et l’ouvrier digital
Certaines des usines visitées permettent de mieux comprendre les notions précédemment développées. Le col bleu augmenté présente toutes les caractéristiques de l’utilisateur de médias numériques, non seulement parce qu’il est équipé de dispositifs digitaux qui s’interposent entre lui et son travail, mais surtout parce qu’il lui est prescrit d’agir selon le modèle participatif. À l’autre bout du spectre hiérarchique, l’ingénieur de nouvelle conception ou le technologue qui donne de l’intelligence aux machines agissent et sont reconnus comme des « talents » et des pionniers. D’un côté, donc, la figure ordinaire de celui qui, grâce à l’usage intelligent d’outils digitaux très communs (smartphone ou tablette), peut s’insérer rapidement dans la ligne de production, même avec un niveau de connaissances spécifiques peu élevé ; de l’autre, des figures plus rares, caractérisées par des formes « d’exceptionnalité », capables de gérer la complexité dans les territoires de l’innovation. Dans la réalité de l’usine 4.0, bien entendu, ces profils s’estompent et se mélangent, car ils dépendent en grande partie des caractéristiques particulières de chaque environnement de travail.
C’est sans doute chez Alstom à Savigliano qu’on voit le mieux à quoi pourrait ressembler l’usine du futur : extrême complexité du processus et petits lots ; temps de production qui se sont significativement raccourcis ces dernières années ; importante variabilité de la charge de production. Ce qui fondamentalement a conduit Alstom à se réorganiser, ce sont les exigences du marché : le processus de production y était auparavant pratiquement artisanal. Il y a 20 ans, la construction de trains était fondée sur un nombre limité de plans qui s’adressaient à des travailleurs « experts » capables de les interpréter, en vertu d’une expérience personnelle qui venait suppléer aux carences de la conception. C’est sur un modèle d’accumulation et de transmission des compétences que résidait la valeur ajoutée des ateliers, mais simultanément celle-ci reposait entièrement sur les capacités individuelles, et donc sur leurs limites. À partir de 2012, avec le projet 3D Master, Alstom devient capable de produire un avatar visuel du train, flexible, ouvert, partageable, une modélisation à partir de laquelle il devient possible de diriger et contrôler l’ensemble du processus productif, tout en y introduisant des variations. C’est le chaînon manquant qui permet enfin d’intégrer la production à la conception, l’objectif étant de concentrer les modifications en phase de simulation virtuelle « quand le train n’est encore qu’un algorithme et que les modifications se font presque à coût zéro » (Alstom) et d’accélérer le time-to-market. L’effectif du bureau d’études croît en nombre et en compétences, avec un impact non négligeable sur la composition globale des ressources humaines de l’entreprise : à Savigliano, l’âge moyen des ingénieurs est de 43 ans, et c’est toute la moyenne d’âge de l’entreprise qui s’abaisse. Les connaissances deviennent hyper-codifiées et rendues utilisables pour la ligne de production. La gestion de la complexité, qui était auparavant partagée entre la conception et la production, devient l’apanage de l’ingénierie de conception.
L’ouvrier-artisan, détenteur de connaissances tacites et transmissibles par l’apprentissage imitatif sur le terrain, perd progressivement sa place dans cette nouvelle usine smart. Quand il faut envoyer le train en production et intégrer à la ligne des centaines de contrats courts et d’intérimaires, il devient indispensable que le stock de connaissances nécessaires à la production soit standardisé et véhiculé par le langage multimédia. En conséquence, les informations vitales pour la chaîne de production nécessitent une « traduction » et une pédagogie de la transmission très différentes de celles qui prévalaient auparavant, puisqu’elles s’adressent à des ouvriers tendanciellement moins compétents.
Quel travailleur reste-t-il alors sur la ligne ? L’ouvrier-artisan est en grande partie remplacé par l’utilisateur natif de médias numériques qui importe dans son travail les pratiques digitales acquises dans sa vie quotidienne. Ce qu’on demande à ce travailleur, c’est donc une familiarité avec les outils de communication numériques qui assurent une grande vitesse d’apprentissage. Ces instruments parlent une langue universelle, constituée de symboles standardisés ; leurs interfaces sont toujours plus naturelles, adaptatives et responsive, permettant une relation homme-machine facilitée. Chez Alstom, cette langue universelle est mise au service de processus de formation simplifiés et rapidement valorisables, qui font de l’ouvrier un opérateur « augmenté » par les outils digitaux, mais « diminué » sur le plan de l’expérience.
Mais une fois encore, cela n’est pas si simple. L’École des projets spéciaux d’Alstom forme au contraire des opérateurs spécialisés qui œuvrent sur des parties du processus difficiles et capitales pour la construction du train. Outre le fait que l’école permet d’assurer le maintien des compétences, elle représente également le lieu d’où provient l’innovation issue du terrain et de l’expérience des opérateurs. C’est là qu’on expérimente des solutions nouvelles sur les produits, mais aussi des outils d’innovation pédagogique, comme l’entraînement des soudeurs grâce à la réalité virtuelle et immersive.
« Tous les six mois, nous rencontrons individuellement les personnes. Ici, nous recevons en entretien individuel 850 salariés deux fois par an. C’est un travail monstrueux mais très utile, parce que nous réussissons à les détacher quelque peu de la production quotidienne, ils sont libres de nous faire part de leurs préoccupations et de leurs critiques ; nous utilisons l’entretien comme une sorte de formation complémentaire. Nous voulons qu’ils puissent venir partager avec nous les problèmes qu’ils rencontrent en production, et les experts de l’école sont aussi sur la ligne, donc il y a d’authentiques échanges. » (Alstom)
Passer du modèle artisanal à l’usine 4.0 implique de transformer la carte des rôles, des compétences et des relations au sein de l’usine. À Savigliano, l’organisation est basée sur les équipes au sein desquelles des salariés experts, les team leaders (qu’il s’agisse d’ingénieurs ou d’opérateurs), jouent le rôle de tuteurs à l’égard de leurs collègues moins expérimentés. La direction des ressources humaines d’Alstom a voulu organiser une responsabilisation réciproque entre générations, et l’a associée à un système qui favorise l’implication des travailleurs dans les démarches porteuses d’innovation. L’entreprise devait, en effet, parvenir à transformer l’ancien modèle de fonctionnement, en recherchant un équilibre entre neuf et ancien et en favorisant l’acceptabilité du nouveau modèle au sein d’une structure aux pratiques professionnelles très enracinées. Les équipes et les tuteurs ont représenté la clé pour construire les fondations de cette nouvelle communauté. C’est un cas d’école pour tous les établissements qui ne naissent pas d’une page blanche mais doivent affronter une transformation culturelle profonde.
« Nous avons créé et développé la fonction de team leader qui, de notre point de vue, est névralgique. Les team leaders coordonnent les opérateurs de lignes, les font participer à la conception du processus en tenant compte de leurs observations, les impliquent et les motivent comme un coach sportif. Ce sont des éléments qui ont une grande valeur et qui sont susceptibles de transformer la manière de travailler de toute l’entreprise. Nous avons mis en œuvre un changement culturel qui a nécessité de l’abnégation de la part de toute l’entreprise. Mais après quelques années de travail, cela marche et ça en valait la peine. » (FCA Maserati)
« Il fallait renouer les liens entre l’usine et la société contemporaine. Parce que si les individus se trouvent dans un environnement vieillot, ils n’ont pas la motivation et le ressort, même si les machines sont très modernes et nécessitent une mise à jour importante des compétences. Mais si les jeunes apprécient une usine qui s’ouvre vers l’extérieur, il y a quand même des habitudes consolidées qui font de la résistance et sont difficiles à modifier. » (Ansaldo Energia)
Ce qui permet de faire le lien entre les générations, ce sont les tuteurs auxquels sont confiés les nouveaux entrants, dans les ateliers comme dans les bureaux d’études. L’objectif est aussi de parvenir à dépasser les mécanismes de protection des connaissances individuelles, qui constituent un réel problème dans les modèles de production reposant sur l’expérience personnelle. Jeunes ingénieurs diplômés aux côtés d’ingénieurs experts plus âgés, ouvriers non qualifiés avec des chefs de ligne… Le tuteur devient le chaînon entre l’usine d’hier qui avait le temps de laisser advenir l’expérience, et l’usine d’aujourd’hui qui ne peut plus se payer le luxe d’attendre.
Talents, pionniers et personnel d’exécution
Les formes de travail constatées chez Alstom ne sont pas encore généralisables ; elles permettent cependant d’entrevoir ce que pourrait être le travail 4.0 dans la pratique. Chez Avio Aero à Cameri, la vision est différente mais tout aussi intéressante.
Cameri est le plus grand site européen pour la fabrication additive appliquée à l’aéronautique. Peu de machines sur une surface assez réduite ; c’est dans ce décor épuré qu’Avio Aero, depuis son rachat par General Electric, prévoit de lancer une production industrielle pouvant atteindre jusqu’à 10 000 pièces par mois. À Cameri, contrairement à Alstom, il n’y a pas de racines à préserver, de routines à modifier ou de compétences à élever. Tout peut être inventé. Quelques caractéristiques de cette « usine-qui-n’est-pas-une-usine » sautent aux yeux : peu de personnes dans les ateliers, haut niveau de diplôme, âge moyen bas.
« Nous avons besoin de gens qui sachent raisonner. Si un jeune diplômé arrive sans rien savoir du travail, c’est pour nous un avantage. En revanche, nous recherchons des individus qui soient orientés vers l’amélioration continue dans les méthodes de travail. Nous avons embauché des personnes qui arrivaient avec l’ambition de résoudre un problème, mais nous avons écarté celles qui connaissaient déjà la solution parce qu’elles se rappelaient l’avoir lue dans un livre. Avoir de bonnes capacités de raisonnement est une caractéristique importante pour travailler en fabrication additive. » (Avio Aero Cameri)
On constate ici une rupture complète avec l’approche fondée sur l’expérience accumulée. Ce nouveau modèle repose entièrement sur la détection des talents, au point que l’expérience non seulement n’est pas nécessaire, mais est même considérée comme nuisible. Celui qui travaille sur l’innovation disruptive est un pionnier qui doit faire preuve de capacités d’exploration et d’orientation en contexte inconnu. C’est la différence entre un processus de transformation (Alstom) et un processus de création (Avio Aero Cameri) dans lequel les salariés participent activement à la construction de quelque chose qui ne peut pas encore être enseigné : « Ces garçons sont devenus des pionniers à travers l’expérience qu’ils ont vécue chez nous ».
Dans les usines de « l’innovation absolue » comme à Cameri ou chez Tesla, le diplôme est largement insuffisant comme le rappelle Elon Musk : « Nous examinons à fond les réalisations mises en avant dans le CV. Le succès est enfant de beaucoup de parents et nous essayons de savoir qui l’a vraiment engendré. Pour nous, le diplôme importe peu. »
Mais dans la pratique, la transformation cohabite avec la création, de la même manière que la gestion du personnel doit composer avec les exigences du renouvellement des générations autant qu’avec la nécessité de maintenir les compétences et l’expérience accumulées avec le temps.
C’est ce qui se passe chez CSM (Centre de développement des matériaux de la Métallurgie). On y trouve des chercheurs seniors qui disposent d’une forte spécialisation acquise à travers leur collaboration prolongée avec l’industrie et qui sont devenus des références dans leur domaine. Leur savoir n’est pas facile à transmettre. Aujourd’hui, des organisations comme le CSM doivent à la fois renouveler les talents sans perdre l’expérience accumulée, qui est peu standardisable et difficile à transférer.
Chez Avio Aero à Cameri, on trouve trois types de profils « pionniers » : l’opérateur machine, l’ingénieur de production et le spécialiste des processus. Leur point commun est d’exercer un contrôle : leur fonction consiste à surveiller un processus réalisé par des machines qui n’ont pas besoin d’une intervention permanente et qui fonctionnent de façon autonome, en continu.
Le rôle de l’opérateur est de mettre en route le processus qui est standardisé mais variable, au sens où ces machines peuvent produire une grande variété de produits ; le travailleur de Cameri est un contrôleur qui sait gérer la complexité, conformément à l’approche 4.0. Il ne se contente pas d’exécuter comme on l’entend traditionnellement, il n’est pas un banal surveillant de machines ; dans le monde de la fabrication additive, il a la responsabilité de réunir toutes les conditions pour que les machines fonctionnent selon l’infinie variété des produits à réaliser.
L’ingénieur de production effectue un travail créatif, car la technologie additive permet d’imaginer un design radicalement nouveau des produits ; il doit donc apprendre à penser en additif et pas seulement à réaliser des produits avec les technologies additives.
« L’ingénieur de production transpose le modèle 3D du concepteur. Ce modèle ne résulte pas seulement de l’idée du concepteur, d’autant que ce dernier ne sait pas forcément comment fonctionne la technologie additive et quelles sont ses limites. La conception finale est le résultat de la contribution de plusieurs métiers qui savent répondre aux deux exigences fondamentales d’un produit industriel : fonctionnalité et faisabilité. » (Avio Aero Cameri)
Au sommet de la pyramide sociale de cette nouvelle usine, se trouve le spécialiste des processus : un talent qui sait programmer les 300 paramètres gouvernant ce type de fabrication. Stabiliser les paramètres qui permettent d’obtenir la meilleure qualité et d’utiliser le moins de matériau fait partie du cœur de valeur ajoutée d’un établissement comme celui de Cameri.
Mais on peut aussi trouver ce type de précieux talents dans d’autres usines qui « deviennent intelligentes » ; ils sont souvent dépositaires d’une compétence produit ou processus déterminante pour l’organisation, et qu’importe s’il s’agit d’un jeune ingénieur ou d’un ouvrier expert !
« Nous avons embauché une personne avec une expertise de tourneur-fraiseur et une capacité à travailler au centième de millimètre près ; quelqu’un qui connaît la valeur de la précision. Il s’est initié aux procédures, puis il a mis à niveau toutes les machines. C’est quelque chose que tu ne peux pas demander à un ingénieur et que tu ne sais faire que si tu disposes d’une expérience en atelier. » (Avio Aero Cameri)
Le storytelling encore partiel portant sur l’univers de travail proposé par l’industrie 4.0 donne le sentiment qu’un fossé se creuse entre les typologies de travailleurs, classés désormais selon leur capacité à entrer en résonance avec le langage numérique et la production de connaissances. Au sein de l’entreprise, la classification du personnel basée sur les compétences ne coïncide plus forcément avec des critères tels que le diplôme ou l’ancienneté. Mais chaque entreprise a ses particularités. Chez Alstom, la richesse provient aussi bien du savoir-faire des ouvriers spécialisés dans des métiers experts (le soudage, par exemple) que de la formalisation globale du processus de fabrication en un modèle pouvant être ensuite subdivisé en autant de procédures simples, tandis qu’à Cameri, il s’agit de construire à partir d’une page blanche un référentiel « métiers » qui n’a pas de précédent historique.
Si les pionniers ouvrent la voie, ils sont aussi les premiers expérimentateurs des standards qui seront ensuite appliqués en aval par du personnel d’exécution dont la tâche est de suivre strictement la procédure avec méthode et précision. Celui-ci n’effectue pas un travail créatif, mais prédéterminé, standardisé et fixé dans des modèles et dispositifs numériques qui assurent à l’ensemble du processus une stabilité de résultat. Ce personnel d’exécution vit un aplatissement de ses compétences, qui pourrait bien représenter la porte d’entrée vers un « fordisme numérique », revers de la médaille du travail 4.0.
Mais tout le monde n’est pas d’accord avec cette interprétation.
« Les compétences demandées à un opérateur sont différentes. Par le passé, les interventions de l’opérateur sur un mode visuel et manuel étaient beaucoup plus fréquentes. Il connaissait très bien le produit. Aujourd’hui, il a moins de compétences techniques, mais il connaît beaucoup mieux le processus d’ensemble et cela demande un changement considérable de profil. Il sait gérer des machines complexes qui réalisent des processus complexes. » (STMicroelectronics)
Selon ce point de vue, le changement des missions implique un enrichissement des compétences pour le travailleur et une orientation de la demande des entreprises vers des profils à caractère polyvalent. La polyvalence valorise le rôle du travailleur, ne serait-ce que par son étymologie : « avoir de la valeur », mais aussi avoir un pouvoir d’action sur la création de valeur de l’entreprise.
Clairement, le débat sur cette question est loin d’être tranché. Les tâches d’exécution assistées par le numérique peuvent avoir une utilité sociale, en permettant la reconversion de travailleurs faiblement qualifiés ou âgés : les dispositifs numériques utilisés dans la vie personnelle créent une familiarité avec ces objets, pouvant jouer un rôle positif dans la réinsertion professionnelle des travailleurs. Sur le plan syndical, en revanche, ces catégories de personnes fragiles mais capables d’apprendre ne sont pas parfaitement représentées dans les schémas habituels. Si l’on imagine les compétences comme une monnaie d’échange entre entreprise et représentants des travailleurs, alors il faudra construire un grand « entrepôt » des compétences encapsulées dans l’entreprise.
Dans une récente étude, Daron Acemoglu et David Autor du MIT (2010) ont catégorisé le processus d’obsolescence du travail humain selon les axes cognitif/manuel et répétitif/non répétitif. Ils indiquent qu’aussi bien les tâches cognitives que manuelles seront frappées d’obsolescence si elles sont répétitives. Ces principes sont empiriquement vérifiés dans bien des cas de restructurations qui voient les hommes remplacés par des machines. Dans ce contexte, les syndicats pourraient se donner comme objectif d’établir une cartographie des risques d’obsolescence ou d’appauvrissement des compétences, afin d’orienter leurs revendications vers la rotation des personnes sur les postes, y compris en allant, s’il le faut, à l’encontre de la volonté des travailleurs. Il est en effet reconnu que, surtout dans les tâches manuelles et répétitives, il peut exister une préférence du travailleur pour l’autonomie que lui procure sa relation d’exclusivité avec « sa » machine, plutôt que pour la diversité des postes et des activités. Mais cette niche de confort risque fort de se transformer en voie de sortie, surtout avec l’avènement des technologies d’automatisation numériques.
La « subjectivation » de la force de travail
Nous avons vu que l’un des thèmes saillants du travail 4.0 est le rôle central donné à la participation et à la pro-activité des travailleurs. Les témoignages rejoignent les analyses pour souligner l’importance – qui n’est certes pas neuve mais semble prendre un relief particulier – de l’implication, non seulement fonctionnelle mais aussi émotionnelle, des salariés dans leur travail. On pourrait dire que l’usine intelligente ne réclame pas que des compétences « froides », habileté technique et connaissances, elle exige aussi des ressources « chaudes » : valeurs, comportements, passion, en un mot « subjectivité ». Simultanément, l’entreprise cherche à générer, dans les pratiques quotidiennes, l’identification et l’adhésion à des valeurs, donc à produire de la « subjectivité » ou encore à « subjectiver » le travail.
Participation et subjectivation sont les deux faces d’une même médaille, l’ombre et la lumière de mécanismes qui attribuent une responsabilité croissante à l’individu au sein de configurations économiques et sociales toujours plus déstructurées. En ce sens, les processus de subjectivation au travail apparaissent comme le miroir de conditions de travail caractérisées par l’incertitude et la précarité, en lien avec l’accroissement de la flexibilité des entreprises. Pour certains auteurs, cette dernière tendance s’est accentuée à partir des années 2000, conduisant les entreprises à déplacer sur les individus une partie de leur risque économique, financier et social (Armano, Murgia, 2014). On assiste ainsi à l’émergence d’une sorte « d’entrepreneurisation » de la vie, dont une composante essentielle devient la participation active des travailleurs.
Pour plusieurs raisons parmi lesquelles, d’une part, la logique propre aux technologies digitales (participer activement à la construction du contenu des réseaux) et, de l’autre, le tournant « subjectiviste » du travail, il est demandé au travailleur « une adhésion affective » au projet de l’entreprise. La tendance du nouveau capitalisme à introduire une subjectivation ambivalente chez le producteur, le consommateur et le travailleur fait depuis longtemps partie des thèmes centraux de la réflexion sur la société contemporaine : dans l’une des plus célèbres d’entre elles, Michel Foucault (2004) identifiait la transformation de l’individu en « unité-entreprise » et « capital humain » comme l’un des moments fondateurs du projet néolibéral.
Cette transformation peut donc être vue soit comme une opportunité de développement personnel pour l’individu (cf. le point de vue des militants de l’innovation p. 72), soit comme une réduction substantielle de sa liberté et de sa vie sociale, « là où justement on en célèbre le triomphe » (Magatti, 2013). L’analyse du travail contemporain, y compris dans la nouvelle usine, prend place entre ces deux points de vue extrêmes.
L’implication active des travailleurs à tous les niveaux du cycle de production est considérée par les managers interviewés comme un pilier de la production intelligente. En résumé, l’usine intelligente est obligée de donner au travail une place qui soit cohérente avec les objectifs de la production smart.
Rien de vraiment inédit dans cette approche. Depuis l’aube ou presque de l’industrie, les chefs d’entreprise ont cherché par différentes voies à obtenir l’approbation et la collaboration des salariés pour neutraliser les conflits intrinsèquement liés à la relation de subordination dans le salariat et à l’existence de la hiérarchie dans l’usine. La collaboration et la participation des travailleurs ont toujours été mises en avant par toutes les voies alternatives au taylorisme qui entendaient répondre au fait que la position du travailleur est consubstantiellement « étrangère » au projet de l’entreprise. Dépasser l’indifférence dont témoignaient les opérateurs à l’égard de la qualité du produit industriel fut le grand sujet du début des années 1990, lorsqu’on envoyait les managers au Japon étudier le Kaizen toyotiste et les 5S, fondés sur l’amélioration des processus par les opérateurs eux-mêmes.
Dans l’usine digitale, les impératifs d’attention, participation et implication semblent encore renforcés. Si les machines numériques peuvent engendrer une routine « à géométrie variable », elles requièrent cependant d’être mises en route et surveillées par les opérateurs. Obtenir des travailleurs un niveau d’implication suffisant pour qu’ils soient en mesure d’identifier les dysfonctionnements et les non conformités prend une valeur déterminante dans des cycles de production fortement intégrés. Car incorporer en temps réel les contrôles qualité dans les flux, en sachant identifier les gaspillages, les anomalies et les imperfections, afin de gagner en efficience dans les interstices du cycle, représente un des enjeux majeurs de la nouvelle usine.
« Grâce à l’implication des personnes, nous visons l’objectif que nos salariés soient capables de nous signaler toutes les non conformités ou tout ce qui n’est pas optimal. Nous demandons aux personnes de nous indiquer même de manière anonyme les points critiques qui nécessitent d’être “tracés” et de recevoir une réponse adaptée. Les yeux de 700 personnes valent mieux que ceux du seul ingénieur de production. » (Avio Aero)
À ce premier niveau d’implication fonctionnelle se superpose un second de nature plus idéologique. L’usine intelligente, et l’entreprise en général, se présentent comme un espace « commun » capable de valoriser et d’unifier la diversité au nom d’une mission partagée. Ce qui est demandé ici au travailleur, c’est plus qu’une participation consciente, mais quelque chose qui relève de son identité sociale : l’inciter à transférer dans son travail non seulement son attention et ses compétences, mais aussi de la passion – qui pour divers responsables RH devient ainsi un critère de recrutement lié à la création de valeur.
« Le travailleur que nous décrivons tient entre ses mains une valeur plus élevée que par le passé ; donc, sa motivation et la qualité de son travail sont fondamentales. Je pense qu’une grande part des individus, s’ils sont correctement stimulés, peuvent faire preuve de passion dans leur travail. Dans cette quête de valeur, nous devons extraire la passion ; la passion fait la différence entre le figurant et l’acteur. Chacun doit apporter sa contribution et cette contribution doit être valorisée : dans le cadre d’une organisation ouverte, passion et contribution doivent être cultivées, soignées et stimulées. » (ST Microelectronics)
Il y a donc une convergence entre le récit futuriste de la production intelligente et l’insistance mise sur l’adhésion aux valeurs. Il est difficile de dire si cette vision trouve son origine dans les nouveaux impératifs d’organisation ou si elle dérive de l’hégémonie acquise par l’« entrepreneurisation » de tous les aspects de la vie sociale. Ce qui est sûr, c’est que le fonctionnement de l’usine intelligente présuppose de porter une égale attention aux objectifs de l’entreprise et à la workplace within, selon le titre de l’ouvrage de Hirschhorn (1988), composée d’une force de travail plus instruite et donc plus exigeante. La rapidité de conception et d’exécution, la compression du time-to-market, l’intégration des processus et l’exigence de renouveler le stock de connaissances rendent, d’une certaine manière, l’usine intelligente plus vulnérable au risque provenant d’une faible implication des salariés ou de leur refus de collaborer. Le tournant « subjectiviste » ne dérive donc pas seulement d’un impératif technique, mais aussi du caractère central donné aux valeurs par l’entreprise elle-même. Sur le plan du travail, cela impliquera certainement une pression majeure sur les salariés, afin qu’ils adhèrent à ce modèle.
Transformation des compétences et nouveaux modes de valorisation
Comment la subjectivation de la main d’ œ uvre, avec ses conséquences en clairobscur, agit-elle sur l’organisation du travail (rémunération, primes, incitations et autres bénéfices sociaux) et sur les formes contractuelles ? En raison de la nécessité qu’elle a de susciter l’implication des col laborateurs, l’usine intelligente recourrat-elle de façon croissante à des formules d’incitation, individuelle ou collective, liées aux résultats et à la performance de l’entreprise ?
« Notre contexte implique que nous fassions appel, de façon assez importante, à des contrats nous permettant de gérer l’organisation du travail sur la base d’accords ad hoc, comme ceux conclus à Savigliano qui nous permettent de moduler les horaires de travail et les pauses, avec des temps de réaction beaucoup plus rapides par rapport aux accords nationaux. » (Alstom)
Traditionnellement, les syndicats abordaient les questions de reconnaissance et de valorisation des compétences à travers des systèmes de règles comme les conventions collectives et les nomenclatures métiers. Mais le passage vers l’usine intelligente rend cette approche partiellement obsolète et requiert des systèmes de certification des compétences beaucoup plus imbriqués avec la réalité du travail dans chaque entreprise. D’ailleurs, si les entreprises font prévaloir l’idée d’une amélioration continue des produits et services, qui découlerait des compétences professionnelles propres aux travailleurs, alors il paraît juste de mettre en place un modèle de reconnaissance et de certification des compétences qui puissent favoriser l’innovation et correspondre aux priorités de chaque entreprise.
« L’usine optimisée est comme une photographie prise à un instant t, dont la configuration n’est pas destinée à durer parce que les produits et les innovations technologiques évoluent rapidement. Mais dans cette usine en évolution constante, le rôle de l’homme est central, car il a la capacité de prévoir et d’anticiper. L’usine devient donc toujours plus un lieu où les personnes acquièrent la capacité à s’adapter au changement permanent et à une flexibilité beaucoup plus grande que par le passé. D’où, la question de la formation et de comment valoriser les idées dans la mesure où beaucoup d’entre elles naissent justement au sein de l’usine. » (Cluster Fabbrica Intelligente)
L’industrie 4.0 accélère le processus de création et d’évolution des compétences requises au sein d’un monde du travail toujours moins stable, ce qui met en cause le principe même de référentiel « métier ». D’où la nécessité, déjà largement repérée, de revoir la manière dont sont formellement décrites ces compétences, y compris dans les profils de poste et les contrats de travail.
Quelles sont ces nouvelles compétences nécessaires ? Celles qui sont le plus souvent évoquées par les entreprises sont l’entraînement à l’analyse et au diagnostic, la capacité d’abstraction et la capacité à savoir relier entre eux des éléments qui se présentent comme séparés. C’est seulement au sein de ce cadre élargi (même difficile à appréhender) qu’on pourra voir émerger des profils capables de circuler au-delà d’une seule entreprise, ouvrant ainsi des débouchés au sein d’un marché du travail trop changeant pour être efficacement codifié.
« Jusqu’à il y a cinq ans, les personnes accomplissaient des opérations limitées. Aujourd’hui, nous sollicitons leurs compétences en matière d’outillage, contrôle qualité, maintenance et gestion des processus. La capacité à assumer une diversité des tâches et la polyvalence prennent une grande valeur dans le cycle productif ; elles sont donc reconnues et récompensées, y compris sur le plan économique. » (Ducati Motor)
Prenons un exemple concret lié à l’écosystème de la mobilité, longtemps subdivisé entre constructeurs automobiles et fournisseurs de services. Cet écosystème se transforme sous l’effet de plusieurs tendances de consommation : attention portée à la durabilité environnementale ; coexistence entre moyens de transport individuels et solutions collectives de mobilité, modèles standardisés ou fortement personnalisés. Un monde en définitive où cohabitent transports publics et voitures partagées, achat d’automobiles et services financiers, problèmes de parking et logistique intelligente. L’intrication entre TIC et automobile est aussi inattendue que profonde : par exemple, BMW, Audi et Mercedes achètent Nokia Maps dans le domaine de la navigation satellitaire, brique essentielle pour le développement de la voiture sans conducteur ; Microsoft entre au capital d’Uber dans une logique de plateforme et services logistiques.
Dans l’automobile, les changements sont très profonds. Voici un exemple pris dans le monde de la carrosserie. Traditionnellement, la caisse en blanc est le résultat de procédés d’emboutissage et d’assemblage. Dans les procédés de moulage à froid des métaux, le travail manuel et tactile de l’opérateur reste encore aujourd’hui un élément indispensable à la qualité du produit fini, comme on le voit dans l’établissement FCA de Cassino. Le processus mêle des capteurs 4.0 et la compétence de l’opérateur issue de l’expérience. Pendant longtemps, l’entreprise s’est appuyée sur une forme de « diagnostic sensoriel » de l’opérateur, fruit de la relation intime entre l’homme et la matière : un tel diagnostic ne peut, encore aujourd’hui, être fait par une machine. Pourtant, dans cet établissement, le rôle de l’homme a changé. Sa tâche spécifique consiste à « identifier l’erreur », en intervenant si nécessaire sur la production du lot et en remontant le processus jusqu’à la source du problème. En outre, l’opérateur chargé de la programmation de la presse doit aussi « interpréter le matériau », car aucun lot n’est tout à fait semblable à un autre.
Les procédés de moulage traditionnels sont fortement concurrencés par l’introduction de la fabrication additive, dont le potentiel va bien au-delà de l’activité de prototypage. Les systèmes additifs sont déjà capables de produire des composants du véhicule à coûts compétitifs pour certaines gammes de produits. Leur extension à l’ensemble du monde automobile pourrait avoir un impact sur tous les corps de métiers liés à la carrosserie. Dans ce scénario, des métiers qui appartiennent à l’âge d’or du moulage risquent de disparaître au profit de profils multifacettes, plus analytiques mais dépourvus de compétences artisanales. Cette rapide obsolescence des métiers risque de mettre en crise les systèmes de formation traditionnels aussi bien que les politiques d’accompagnement pour qui a perdu son emploi.
L’industrie 4.0 a donc des conséquences profondes sur le système d’éducation et de formation, qui vont bien au-delà d’une simple révision des nomenclatures et référentiels métiers ou de l’alphabétisation numérique ou de l’apprentissage de base d’une langue étrangère. Le changement à l’œuvre rend dérisoire le fait de n’envisager qu’un ajustement technique ou une mise à jour des connaissances : à l’horizon qui se dessine, c’est toute la façon de concevoir et d’administrer les formations qui devra être profondément reconfigurée, avec des solutions toujours moins standardisées et des propositions d’adaptation des cursus quasiment personnalisées pour chaque entreprise ou groupe de travailleurs.
On considère souvent que les réformes de l’enseignement supérieur italien ont manqué de vision de long terme et ont été incapables de créer les compétences adaptées aux exigences de la production contemporaines. Toutefois, notons que les entreprises italiennes investissent avec parcimonie dans la formation et privilégie l’emploi d’une force de travail déjà formée. Le tissu des PME ne s’est pas vraiment intéressé aux vicissitudes du système éducatif national, privilégiant la formation continue (vue plutôt comme un « dressage » que comme une formation) et l’apprentissage (souvent considéré comme voie d’insertion professionnelle flexible plus que comme source d’expérience formative réelle). Le haut niveau de savoir-faire de la main-d’œuvre italienne employée dans certaines niches de production provient essentiellement de l’expérience acquise en ateliers ; dans les dernières années, les PME engagées dans des processus de reconversion de leur propre modèle d’affaires ont certes commencé à recruter des diplômés de l’université ou des techniciens avec des spécialisations post-diplômes, mais cela ne concerne que la minorité la plus dynamique et innovante.
Nous avons vu que la demande de formation pour les usines intelligentes s’orientait vers des niveaux supérieurs de diplômes (au moins bac technologique ou professionnel pour les opérateurs et différents niveaux de diplôme pour les fonctions supérieures). Pourtant, les questions de formation ne semblent guère préoccuper les auteurs qui s’intéressent à l’usine smart ; ils se contentent le plus souvent de porter des diagnostics très généraux, comme la nécessité d’une meilleure qualification de la main-d’œuvre ou d’un continuum plus efficace entre école et travail. Il y a heureusement des exceptions. Dans nos exemples, les entreprises qui sont justement les plus avancées dans les méthodes inspirées du modèle de l’industrie 4.0 prêtent une attention stratégique au recrutement et à l’intégration des nouveaux entrants, y compris à travers des partenariats avec les structures éducatives.
« Dans mon périmètre, nous avons complètement transformé le mix de population, en intégrant 150 diplômés en mécanique et électronique. Nous avons travaillé avec les instituts techniques, en faisant appel à leurs intervenants dans nos formations et en leur faisant visiter nos sites. La sélection des candidats se fait à travers un parcours qui commence par un examen dans la salle de classe, est suivi par une semaine de stage en atelier où les candidats sont évalués par nos tuteurs. » (Avio Aero)
Les liens développés entre les entreprises et l’enseignement supérieur, en particulier avec les pôles que représentent les grandes écoles polytechniques du Nord-Ouest italien sont intenses mais, dans l’ensemble, ni le débat national en cours ni nos témoins ne laissent entrevoir une vision forte de ce à quoi devrait ressembler un système éducatif adapté aux exigences du nouveau modèle productif. Or sans des investissements lourds dans ce domaine, difficile d’imaginer comment la production italienne pourrait globalement monter en gamme. Du point de vue des entreprises, de nouveaux modèles de formation sont un pré-requis pour rendre les travailleurs capables d’innover et de transférer les innovations en cascade, dans une logique continue et inter-agissante d’innovation-formation. Pour mettre en œuvre ce cercle vertueux, la salle de cours est très insuffisante, il faut imaginer des ateliers-écoles, des chantiers participatifs de création, codification, systématisation et transmission des savoirs avec une vaste participation à la vie de l’entreprise.
Le thème de la formation est revenu de façon constante dans nos entretiens, même si celui-ci est décliné différemment selon la nature de la production et le niveau de développement technologique de chaque entreprise. Dans certains cas, c’est la transmission des savoir-faire entre ancienne et nouvelle génération, le « tutorat » et l’apprentissage, qui sont mis en avant ; dans d’autres, l’attention est portée sur l’institutionnalisation de lieux de formation internes, comme les Factory Academy
L’opinion pense que l’industrie 4.0 conduira à vider les lieux de production de leur composante humaine, remplacée par des technologies qui effectueront tout le travail. Ce n’est pas une situation complètement inédite pour tous ceux qui ont piloté de grands processus de restructuration sectoriels ou territoriaux, mais c’est justement pour cette raison que les transformations en cours doivent s’accompagner d’une grande vigilance sur les conséquences organisationnelles et sociales de ces technologies : si l’innovation crée plus facilement et plus fréquemment du chômage à différentes phases de la vie d’un travailleur, il faudra concevoir des politiques publiques qui sachent à la fois cueillir le potentiel de l’innovation technologique comme source d’intérêt général, mais aussi prendre en charge ses effets sur les sujets les plus vulnérables et les plus exposés à ces changements. Autrement dit, il faudra tenir ensemble des politiques industrielles efficaces et des politiques du travail inclusives. Et il faudra également réfléchir au rôle des organisations représentatives dans le processus.
Car préparer les travailleurs à affronter cette mutation n’est pas que l’affaire de l’entreprise, mais aussi des syndicats. Mais il importe de reconnaître avec honnêteté qu’il s’agit d’un processus de longue haleine à l’issue incertaine. Toutefois, c’est dans ce but que sont nés en 2000 les Fonds paritaires interprofessionnels, alimentés par une part minime des cotisations sociales des entreprises (0,3 % au titre de « contribution obligatoire contre le chômage involontaire ») et destinés à financer des plans de formation que des entreprises, seules ou en association, décident de mettre en place pour leurs salariés. La mission de ces fonds repose sur quatre piliers : analyse des besoins, identification des compétences, formation, développement personnel des travailleurs. C’est surtout le premier pilier qui exigera un alignement entre les besoins de l’industrie 4.0 et la vision qu’en ont les instances représentatives.
Une autre question qui se pose fréquemment est : comment valoriser les savoirs créés par les travailleurs et leur contribution à l’amélioration continue réclamée par les entreprises ? Il y a deux façons de considérer la contribution personnelle et originale d’un salarié : a) récompenser le bénéfice que procure à l’entreprise ladite amélioration, une fois que celle-ci aura été passée au tamis de l’équipe, puis transformée en opération codifiée dans le « manuel » et enfin aura été rendue reproductible ; b) considérer que la capacité d’un travailleur à engendrer de l’amélioration continue constitue en soi une compétence distinctive, nécessitant d’être développée, évaluée et rémunérée.
Or, de tels processus sont souvent considérés comme « naturels » et évidents, y compris par les travailleurs eux-mêmes. En Italie, il reste donc à construire un système qui permette de « saisir » et de récompenser de tels résultats, sachant que dans d’autres pays comme l’Allemagne ces pratiques engendrent des primes de salaires non négligeables. Un système efficace de reconnaissance des compétences devrait donc récompenser les comportements vertueux selon une échelle d’évaluation que nous pourrions imaginer comme suit : un premier critère d’évaluation pourrait être la capacité à engendrer une innovation, qu’il s’agisse d’un geste manuel ou d’une idée industrialisable ; le deuxième critère, la capacité à interagir avec l’organisation et les processus ; le troisième, la capacité à créer une implication autour d’une activité ou d’un projet, à susciter la motivation ou l’enthousiasme ; le quatrième, la capacité à activer des boucles de communication, c’est-à-dire à trouver des solutions utiles pour stocker ou transférer les savoirs et processus innovants de façon standardisée, y compris en utilisant des dispositifs digitaux ; le cinquième concernerait la capacité à assumer un rôle de tuteur ou de formateur ; enfin, le dernier porterait sur la capacité à coordonner et animer une équipe.
Représentation et participation
Un sondage conduit par La Stampa (i. e. quotidien national de Turin) demandait au public en juillet 2015 si le pays irait mieux sans les syndicats. Les réponses se sont réparties en trois blocs : 27 % a indiqué que le pays se porterait « mieux », 40 % a répondu « pareil » et 33 %, « pire ». Si l’on sélectionne dans l’échantillon uniquement les réponses des salariés, le taux passe à 41 % pour cette dernière réponse. Les syndicats protègent-ils les travailleurs ? 18 % a répondu « oui », 54 %, « non » en soulignant que les syndicats « ne comprennent pas les changements du monde du travail » (40 %) et « défendent seulement ceux qui ont déjà un travail » (14 %).
Cette perception plutôt négative qu’a l’opinion publique des syndicats résulte-t-elle d’un formidable déficit de communication de leur part ? Ce qui est sûr, c’est que la tendance à les considérer [les syndicats] comme une force « conservatrice » de défense des droits acquis devient de plus en plus marquée. Les médias tendent à les présenter comme des vecteurs de conflictualité, porteurs d’obstacles au progrès. L’opinion les voit comme des instruments de conflits plutôt que de négociation.
Pourtant, le cœur de l’activité syndicale consiste à définir des règles issues de la négociation et qui résultent d’un consensus. Un accord est toujours le résultat d’une triangulation qui part de la représentation, se poursuit par le dialogue social et s’achève par la signature d’un accord.
L’industrie 4.0 est susceptible de créer une tension inédite dans ce fonctionnement, car les mécanismes de la représentation sont lents, alors que le nouveau paradigme favorise le temps réel. Les syndicats devront parvenir à concilier le temps long de la « fabrication du consensus » avec le rythme de plus en plus rapide des choix industriels. La fabrique du consensus devra en outre intégrer de plus en plus une dimension de responsabilité : la responsabilité de prendre en compte non seulement les intérêts des travailleurs, mais aussi les besoins de l’entreprise, pour parvenir à dépasser l’idée que le destin de l’entreprise ne concerne que le patron ou les actionnaires.
Durant tout le XXe siècle, les syndicats se sont focalisés sur la revendication de protections générales, collectives et automatiques, reposant sur l’égalité et l’équité, et n’ont pas fait grand cas de la force de proposition que représentaient les salariés eux-mêmes. Il n’était pas demandé au travailleur représenté par le syndicat de participer à la définition de ses propres conditions de travail, ni de contribuer à la construction du système de protection sociale.
Entre les années 1950 et 1960, les syndicats ont réussi à construire pour les travailleurs une longue série de droits et protections ; ils ont joué un rôle majeur entre la fin de la Seconde Guerre mondiale et le crépuscule du Boom économique (i.e. l’équivalent en France des Trente Glorieuses), permettant au pays de passer d’une société agricole à une société industrielle. En une vingtaine d’années, les organisations syndicales ont accompagné les travailleurs dans la conquête de leur dignité au travail et de leur citoyenneté sociale. Du fait de leur rôle dans la modernisation sociale du pays, elles ont joui d’une grande popularité jusqu’à la première crise pétrolière des années 1970 ; puis celle-ci s’est beaucoup érodée au cours des grandes restructurations des années 1980. C’est dans ces années-là que le climat social et les besoins des travailleurs se sont profondément modifiés.
Aujourd’hui, l’individualisation qui accompagne l’émergence de la société 4.0, avec ses limites et contradictions, pose un défi important au mouvement syndical. L’idée d’adhésion à une représentation repose sur un nouvel équilibre entre nécessités collectives et liberté individuelle, et se présente plutôt comme un « self-service » dans lequel chacun choisit des options sur la base de son style de vie, de son travail et de ses revenus.
L’exemple le plus emblématique de cette situation est sans doute la question des horaires de travail modulables. Si l’on présuppose que le juste équilibre entre vie professionnelle et vie privée relève de la subjectivité de chaque individu, le rôle d’un syndicat en la matière n’est plus que de deux ordres : assurer une réponse adaptée aux besoins de l’entreprise et offrir aux travailleurs des marges de manœuvre au sein de ce cadre. C’est sur cette base qu’a été conçu en Italie l’accord sur les horaires modulables, imaginé pour la première fois chez Luxottica21, leader mondial de la lunetterie de luxe et de mode à Sedico près de Belluno en Vénétie. L’objectif de cet accord est de satisfaire les besoins de l’entreprise en matière d’heures de présence journalières, tout en proposant aux salariés un éventail flexible de modalités devant respecter trois critères : présence sur le lieu de travail ; articulation avec les horaires des collègues ; engagement à garantir le bon fonctionnement de la production. L’accord Luxottica est un exemple à la fois de créativité et de responsabilité à l’égard de l’entreprise, d’action régulatrice et de garantie de liberté pour les travailleurs, au sein d’un dialogue social de qualité entre syndicats, salariés et direction.
En tant qu’expression de la politique industrielle européenne, la finalité du programme Factory of the Future est de renforcer l’industrie de l’Union européenne, en lui donnant les moyens de conserver le contrôle sur des parts significatives des chaînes de valeur au sein du territoire européen. Mais les perspectives qui s’ouvrent à l’industrie représentent aussi des possibilités de scénarios inédits pour le monde du travail comme pour les organisations syndicales. Ceci est particulièrement vrai dans un pays comme l’Italie. L’un des points critiques est que la Factory of the Future, en mettant l’accent sur la compétitivité des entreprises comme support d’une société plus active et plus libre, allégée des régulations générales au profit d’options plus individualisées, déplace le curseur sur la question des mécanismes qui seront aptes à réguler ces nouvelles usines.
Les syndicats devront abandonner le modèle passif qui intervient essentiellement sur les questions d’emploi et se réfère le plus souvent à la grande entreprise, et adopter une ligne davantage orientée sur l’anticipation et la création de nouvelles opportunités. L’enjeu de l’implication des collaborateurs, qui a été souligné par les entreprises les plus avancées, y compris celles de notre échantillon, constitue un signal évident du fait qu’un nouveau modèle d’entreprise est à l’œuvre, qui influencera inévitablement la nature de la représentation, la délégation donnée par le travailleur au syndicat, et l’efficacité des stratégies et des actions de protection à mettre en place.
Les années de crise ont d’ailleurs permis de mesurer à quel point les entreprises constituaient une ressource sociale d’importance majeure pour un territoire. Face à ce besoin de renforcer l’entreprise, y compris sur le plan de la communication, la fonction des syndicats peut apparaître ambiguë. Pourtant, elle consiste essentiellement à agir sur la question de la participation des travailleurs aux choix organisationnels qui engagent l’avenir. Le terrain des revendications syndicales doit donc évoluer pour épouser les changements qui affectent l’industrie.
Le syndicat de la mécanique au sein de la CISL22 a conduit une étude pour mesurer la participation des travailleurs dans certains établissements de Fiat Chrysler, où a été déployé le World Class Manufacturing. Il en ressort que la volonté de faire participer activement les travailleurs à l’amélioration continue entraîne un mouvement progressif de partage des choix sur d’autres aspects de la vie des entreprises. Ce que différentes études semblent montrer, c’est que la volonté de faire participer activement les travailleurs à l’amélioration continue entraîne un mouvement progressif de partage des choix sur d’autres aspects de la vie des entreprises. Position qui peut sembler extrême et qui pourtant semble reconnue par le management de plusieurs entreprises, dont celles de notre étude.
Nous avons vu que l’industrie 4.0 a besoin de l’implication des travailleurs dans la vie de l’entreprise en raison du rôle central joué par la connaissance, par la densité des interrelations et par la nécessité d’articuler entre eux les divers niveaux de formation, depuis l’instruction de base (plus élevée que par le passé) jusqu’à la formation tout au long de la vie (permanente), en passant par la formation professionnelle (spécialisée et approfondie) et la formation supérieure (nécessaire à l’excellence). C’est pourquoi, rendre plus efficace le droit à la formation pourrait représenter pour les syndicats un nouveau terrain de négociation, à condition de ne pas cibler l’ensemble des travailleurs, mais de les segmenter par âge, niveau d’instruction, potentiel sur le marché du travail, etc.
Tout aussi important semble être le fait de déterminer le niveau minimum d’éducation nécessaire au fonctionnement de l’usine intelligente, ce qui pourrait conduire de futures négociations à revisiter l’instrument historique du « droit aux études »23 : né dans les années 1960, ce droit pourrait redevenir utile pour combattre un nouvel analphabétisme numérique.
Enfin, un autre enjeu ouvert par l’usine numérique concerne les primes sur objectifs, puisqu’il oblige les parties à aller au-delà du quantitatif (heures ou jours travaillés) pour aborder le qualitatif et le mérite.
- 18. Capacité d’un objet à suggérer sa propre utilisation.
- 19. En philosophie, l’agency est la faculté d’action d’un être ; sa capacité à agir sur le monde, les choses, les êtres, à les transformer ou les influencer. C’est-à-dire la perception de soi comme acteur du monde qui fait arriver des choses, et pas seulement comme quelqu’un à qui il arrive des choses. L’originalité de la pensée de Bruno Latour est de considérer que les techniques et les objets aussi ont une agency .
- 20. Fayard, 1999. Il s’agit du volume 2 de la trilogie intituléeL’Ère de l’information .
- 21. En 2018, la fusion entre l’italien Luxottica et le français Essilor a donné lieu à la naissance d’un groupe d’envergure mondiale.
- 22. Confédération italienne des syndicats de travailleurs.
- 23. 150 heures maximum par an pour 3 % des salariés en contrat à durée indéterminée qui en font la demande.
Interprétations et ouverture
Un nouvel intérêt pour l’usine
Hasarder des hypothèses sur le devenir du travail dans les usines du futur comporte inévitablement des risques. Même si une littérature managériale assez considérable s’accorde sur le fait que nous nous trouvons devant un tournant intelligent de la production industrielle et malgré la large diffusion des concepts liés à l’industrie 4.0, il est en réalité assez difficile de repérer les traits caractéristiques d’un modèle stabilisé, comme le fut le taylorisme pour l’ère de la production de masse. Comme nous l’avons vu, les nombreuses définitions qui en sont données se rapportent souvent à des objets différents et peuvent véhiculer des significations variées, qui vont d’une tendance générale à la numérisation (ce qui n’est en rien spécifique à l’industrie) jusqu’à la description détaillée de concepts technologiques et organisationnels.
L’une des manifestations concrète de la smart factory réside dans la prolifération de solutions organisationnelles, car celles qui sont déployées dans certaines catégories d’entreprises ne sont pas forcément généralisables à l’ensemble du secteur manufacturier. Deux variables influencent significativement les modèles technico-organisationnels : le secteur d’activité, puisqu’à chaque secteur répondent des problèmes de production particuliers ; la géographie de la division internationale du travail, devenue plus mobile et articulée. Ces deux variables prennent dans le cas de l’Italie une importance singulière, compte tenu de la grande diversité de ses produits, et donc de son positionnement sur les marchés mondiaux et les chaînes de valeur.
Même si la question du travail, au cœur de notre étude, concerne avant tout le travail au sein de l’entreprise, il devient en réalité toujours plus difficile – aujourd’hui et plus encore demain – de délimiter les frontières spatiales et organisationnelles des usines. Le travail industriel se confond de moins en moins avec la figure de l’ouvrier ou du technicien d’atelier, exactement comme les frontières entre industrie et services tendent à s’estomper. Ce n’est pas un hasard si les créations de postes dans l’industrie se concentrent surtout sur l’amont et l’aval du processus de production, qui lui-même intègre toujours davantage la conception et la logistique.
Les mutations culturelles et des modes de consommation tendent à accroître la part de valeur « immatérielle » incorporée dans les produits : recherche, conception et design, formation, marketing, communication, distribution et après-vente constituent, pour une grande partie des biens, les principales composantes de la valeur, et ce sont elles qui permettent d’obtenir une prime de valeur et d’occuper une niche enviée sur le marché considéré. Le produit devient donc le résultat de différentes opérations amalgamées, prises en charge par une diversité d’acteurs coordonnés, et dont certains n’appartiennent pas formellement à la sphère des relations professionnelles (par exemple, les consommateurs).
Le déversement des salariés de l’industrie vers les services durant les dernières décennies s’est traduit par une recomposition de la main-d’œuvre au sein des organisations industrielles. Par exemple, dans les années 1950, il y avait chez Fiat cinq ouvriers pour un employé ; dans les années 1990, ce rapport était tombé à deux pour un. Aujourd’hui, dans l’ensemble du secteur manufacturier italien, y compris au sein du vaste segment des micro et petites entreprises qui emploient 55 % de la main-d’œuvre occupée dans l’industrie, les salariés avec des qualifications d’ouvriers en représentent les 2/3, mais avec de profondes différences sectorielles : dans la chimie ou l’électronique, les ouvriers représentent déjà moins de la moitié des salariés, alors que leur part reste élevée dans des secteurs à plus faible intensité capitalistique comme l’alimentaire, le textile, l’ameublement. En moyenne, dans de nombreuses entreprises, les cols bleus et cols blancs sont au mieux à parité, tandis qu’augmente dans toutes les organisations la présence de profils professionnels qui ne concourent pas directement à la production, mais gèrent la certification, la sécurité, les relations institutionnelles, les pratiques administratives, la communication, la responsabilité sociale et environnementale, etc.
Enfin, une part du travail n’est plus directement contrôlée par les entreprises têtes de filière. Une part croissante des activités en amont et en aval du processus productif, variable selon les secteurs, le degré de complexité, les caractéristiques du marché et les choix managériaux, est prise en charge par des organisations tierces, reliées par des relations contractuelles. La réalisation de certains produits implique un très grand nombre d’entreprises : des centaines d’acteurs situés dans différents pays du monde concourent à la fabrication d’un iPhone ou d’une voiture. Depuis quelques années, le recours systématique à l’outsourcing, qui avait caractérisé les décennies précédentes, semble contrebalancé par un retour à l’insourcing, et les technologies intelligentes pourraient renforcer cette tendance. Reste cependant le fait qu’une part considérable du travail s’effectue aujourd’hui hors des murs de l’entreprise donneuse d’ordre ; c’est pourquoi, observer les usines des grandes entreprises ou regarder la seule phase du cycle de production qu’elles contrôlent ne fournit qu’une idée très partielle de la transformation du travail.
Ces tendances à l’œuvre précèdent de beaucoup l’avènement du paradigme 4.0. Le problème d’un pays comme l’Italie, qui veut maintenir une matrice industrielle, réside dans la cohabitation entre des entreprises innovantes, bien insérées dans le jeu mondial, et d’autres qui restent prisonnières de modèles d’affaires très simplifiés : ces entreprises à forte innovation et celles faiblement qualifiées ou spécialisées coopèrent souvent au sein d’une même filière.
Bien que de façon non linéaire, les solutions technologiques et d’organisation de l’usine intelligente devraient pour le moins renforcer ces tendances et sans doute en faire émerger de nouvelles, inédites, voire révolutionnaires. La raréfaction de la composante humaine dans les ateliers, la concentration dans des activités qui, en amont, donnent de l’intelligence aux machines et, en aval, s’occupent d’attirer, profiler et suivre les clients-consommateurs sont des phénomènes qui devraient s’accentuer sous l’effet des technologies 4.0. Pour toutes ces raisons, l’évaluation et la prospective des changements dans le travail devront reposer sur des observations recueillies aussi hors des usines, et même hors des entreprises manufacturières.
Les débats sur l’usine du futur doivent également s’intéresser à la place que nous voulons donner à la production industrielle dans nos sociétés. Les documents stratégiques, les nombreuses études et les propos de nos témoins s’accordent sur l’importance retrouvée de la production industrielle pour les économies européennes – « On a redécouvert dans l’industrie ce qui nous lie étroitement aux dynamiques de l’économie internationale, là où les services nous ancrent dans un marché intérieur asphyxié et déclinant » (Berta, 2014). Cette redécouverte reflète le désir de relancer des secteurs qui, depuis des décennies, ont subi un deficit d’image et d’attractivité auprès des jeunes, par rapport à d’autres univers productifs ou sociaux. Dans l’immédiat, on voit l’urgence pour l’Europe de retrouver une place dans l’économie mondiale, prise qu’elle est dans un étau constitué, d’une part, par les États-Unis sur le plan des fonctions créatives et financières (localisées respectivement sur la Côte Ouest et Est), et d’autre part par la Chine sur les fonctions de fabrication, même dans les secteurs high tech, l’Europe ne représentant plus qu’un vaste marché final. Il y a aussi l’exigence de construire un nouveau rapport entre industrie et finance, après trente ans d’affaiblissement du lien entre capital financier et base industrielle. Enfin, c’est l’occasion de donner du contenu au concept d’économie de la connaissance, en articulant ce concept à la réalité de la structure économico-sociale de l’Europe.
Plus encore que sur l’industrie, les documents et les entretiens mettent l’accent sur l’usine comme lieu de la production. Si depuis la fin des années 1960, l’usine était devenue invisible, elle revient au premier plan dans sa matérialité. D’où l’intérêt porté à l’architecture et au design des édifices, des produits et des machines : l’usine devient un lieu à montrer, à exhiber, et sa forme esthétique, un enjeu de compétition pour laquelle se mobilisent des cabinets d’architectes de notoriété mondiale. Mais ce désir de redonner à l’industrie un caractère central dans l’économie, impliquant une montée en gamme des productions, des processus et des savoirs, n’est pas forcément synonyme d’un retour des usines dans la conscience sociale. Les usines du futur sont imaginées comme des espaces à forte intensité capitalistique, traversés par des flux de données provenant du marché et pour le marché, de taille réduite et harmonieusement insérés dans les territoires. Mais ce ne seront plus de grands bassins d’emploi, et leur intérêt résidera surtout dans le fait d’être des catalyseurs de processus engendrant de la connaissance, dans le cadre d’une chaîne raccourcie entre science, recherche appliquée, conception, production, distribution et consommation.
Des termes comme « révolution » et « usine » prennent à l’ère digitale une connotation positive. Le mot « révolution » a dissipé ses relents de menace et devient un contre-point à « évolution », au sens où le tournant digital de l’usine permet désormais le changement continu. Le terme « usine » devient smart, renvoyant à un passé lointain les jugements de valeur portant sur son caractère dégradant, aliénant et synonyme de mauvaise qualité de vie (Butera, 2014). Dans l’usine du futur, il n’y a plus de bleu de travail, taché d’huile et de graisse ; les opérateurs interagissent avec de l’information « propre », et non avec des machines crasseuses, et ils disposent d’un bon niveau de formation.
Image réelle ou idéalisée ? L’usine intelligente fera-t-elle disparaître l’aliénation au travail ?
Un post-fordisme augmenté
L’industrie 4.0 est présentée comme un tournant d’une portée telle qu’il mériterait le nom de « révolution industrielle » ; cette révolution aurait pour caractéristique l’intégration de l’univers physique et des technologies numériques. Il n’est cependant pas sûr que ladite révolution soit en train de donner naissance à un modèle d’organisation, à des concepts communs, à des plateformes technologiques et cognitives partagées et à des nouveaux profils convergents de travailleurs. Tout au contraire, le devenir intelligent de la production pourrait suivre une multitude de chemins, en continuité ou en discontinuité avec le passé.
Discontinuité par rapport au taylorisme, longtemps hégémonique, et qui continue en partie à modeler notre imaginaire, vu l’effort qu’il faut consentir pour s’en détacher lorsqu’on observe l’usine intelligente. Le crépuscule du taylorisme n’est cependant pas un fait nouveau : dès les années 1970, cette forme d’organisation était entrée en crise pour un ensemble de causes sur lesquelles le débat n’est pas clos. Et même si le taylorisme n’est pas tout à fait mort, son hégémonie dans la pensée managériale a cessé avec la fin de l’ère de la production de masse.
Plutôt que comme une alternance de cycles, le dernier se substituant au précédent, l’histoire des modèles d’organisation peut être vue comme des vagues qui s’interpénètrent et au sein desquelles coexistent des modèles concurrents. De ce point de vue, on peut affirmer qu’à aucune époque il n’y a eu un seul modèle d’organisation de la production : il y a eu à côté du taylorisme des modèles mettant l’accent sur l’autonomie et la responsabilisation, sur la participation et la valorisation du facteur humain, sur l’importance des équipes, et sur des conceptions systémiques et ouvertes. Le toyotisme, par exemple, maintenait des éléments du taylorisme, comme la parcellisation des tâches, mais valorisait la participation active de l’opérateur, la résolution de problèmes, le dépassement de l’indifférence face à la qualité du produit, en plus d’introduire des concepts alors révolutionnaires comme le juste-àtemps, le lean et l’organisation aplatie. L’Italie plus qu’aucun autre pays devrait avoir conscience de cette polyphonie : notre territoire (ou plutôt certaines de ses régions) a, en effet, donné naissance à un modèle industriel alternatif à la production de masse, fondé sur des formes de division du travail horizontale entre petites entreprises concentrées dans des districts, spécialisées sur des niches et s’appuyant sur des savoir-faire artisanaux enracinés dans les cultures productives locales.
À partir des années 1970, et plus encore dans les décennies suivantes, s’affirment des modèles d’organisation qui partagent déjà certaines caractéristiques que l’on retrouvera dans l’usine intelligente : par exemple, la tendance à la « recomposition des débris du travail », selon l’expression du sociologue Federico Butera (1972), auteur d’un essai important de ces années-là, comme réponse à l’appauvrissement des compétences des travailleurs, ou encore le passage d’une conception « mécaniciste » à une conception « organique » des organisations. En réalité, à cette époque, la conception mécaniciste ou tayloriste de la production ne disparaît pas, elle se relocalise dans les pays émergents ou se déplace vers le tertiaire, comme dans la distribution, la logistique, la restauration, les services de santé ou, plus généralement, le travail de bureau.
Dans les nouvelles usines disparaissent les modèles strictement organisés en mode hiérarchique : la chaîne de commandement amont est partiellement déstructurée pour distribuer de l’autonomie aux équipes, et recomposée en aval pour permettre à l’information et à l’innovation de donner leur pleine mesure. Selon les grands cabinets conseil, les technologies de l’industrie 4.0 sont supposées conduire à une rupture dans les modèles d’organisation. Pourtant, les concepts, les références culturelles et les motsclés recueillis au cours de nos entretiens (mais repérables aussi dans de nombreux documents) mettent en lumière une continuité avec les modèles « post-fordistes » : à son niveau le plus général, l’usine intelligente apparaît davantage comme un développement raffiné du post-fordisme, ou de l’« automatisation flexible » ou encore du « toyotisme », que comme un nouveau modèle d’organisation. Ou pour le résumer par un slogan, l’usine 4.0 est un « post-fordisme augmenté ».
Par exemple, plusieurs interviewés insistent sur les avantages logistiques de l’usine intelligente : elle permet de réduire les risques du juste-à-temps pour lequel la synchronisation est fondamentale et où tout retard en un point critique du processus fragilise la chaîne entière ; et conséquemment, elle permet de réduire les stocks et la taille des entrepôts.
Nous avions souvent des machines à demi-montées ; s’il manquait une pièce, on était arrêté pendant deux jours. Aujourd’hui, les fournisseurs remplissent automatiquement nos boîtes au fur et à mesure qu’elles se vident. On réduit ainsi l’encombrement, ce qui fait qu’on peut utiliser l’espace pour d’autres activités. Nous gérons beaucoup mieux les espaces de montage. (Giletta)
Plus généralement, on constate que, dans l’usine intelligente, « les chaînes fournisseurs sont significativement raccourcies, produisant une augmentation du nombre de transactions commerciales pour une valeur plus faible » (Veronesi, 2014).
L’orientation client est un autre des thèmes récurrents de l’usine intelligente. Il s’agit d’inverser le flux d’information qui alimente la production, en partant de la commande, selon une logique consumer to business. Ce concept était déjà au cœur du système toyotiste, ainsi que des innovations market driven du Made in Italy. La flexibilité des volumes et du mix productif, c’est-à-dire la possibilité de réaliser avec les mêmes installations une gamme de produits plus large avec des séries plus courtes, se trouvait déjà au fondement des organisations du travail de type « systémique » qui accompagnèrent dans les années 1980 le virage vers l’automatisation flexible. Les nouvelles technologies permettent de mettre en œuvre ces principes avec un coût inférieur et une accélération des délais : aujourd’hui, on peut produire un train en 13 mois plutôt qu’en 4 ans.
L’accent mis sur les équipes comme élément crucial de l’organisation était déjà au centre de toutes les expérimentations qui visaient à dépasser les limites du taylorisme. Même la polyvalence du nouvel ouvrier a une longue histoire et trouve son origine dans le job design des années 1970 et 1980, avec des concepts tels que rotation des postes, enrichissement et élargissement des tâches. L’image du nouveau col-bleu (à « rayures blanches » selon l’expression ironique du sociologue Luciano Gallino), contrôleur et expert en flux, rappelle la figure du « conducteur systèmes » ou « conducteur de travaux » de l’époque de l’automatisation flexible.
Les concepts-clés de l’usine intelligente apparaissent donc comme un prolongement ou une rénovation de principes qui avaient cours bien avant que la crise ne ramène au premier plan l’usine, reconfigurée par une nouvelle génération de technologies. S’interrogeant sur les facteurs de compétitivité des plus grandes entreprises mondiales, Suzanne Berger (2005) identifiait, entre autres, la qualité, l’amélioration continue, l’efficacité dans la gestion de la chaîne d’approvisionnement, le design, l’orientation client et la qualité de vie au travail. L’agenda 4.0 n’est pas très différent.
Mettre en évidence ces éléments n’a pas pour objectif de réduire ce que l’usine intelligente porte de novateur. En effet, si nous passons de la vue d’ensemble au détail, de l’organisation générale à la réalisation des processus de travail, les changements prennent davantage de consistance. C’est à ce niveau que se situent les questions d’élaboration, traitement et circulation de l’information et de la connaissance entre les machines et entre les personnes ; ici encore que se trouvent les dispositifs qui transforment la manière de concevoir et de fabriquer. Les nouvelles technologies permettent d’étendre et d’amplifier les innovations qui sont ainsi mises à la portée d’un beaucoup plus grand nombre d’acteurs que par le passé. Par certains aspects, l’usine intelligente réalise la promesse faite par le toyotisme et l’automatisation flexible, en levant les obstacles techniques qui en empêchaient le complet avènement.
Les entreprises appliquent cependant de façon encore limitée et discontinue les solutions technologiques capables de révolutionner leur modèle d’affaires. C’est pourquoi, nous préférons parler de virage intelligent de la production industrielle plutôt que d’industrie 4.0, ce qui permet d’attirer l’attention sur un processus en cours, plutôt que sur un « avant-après ». C’est ce qu’affirment d’ailleurs les fournisseurs de solutions euxmêmes. Selon certains experts, en Europe, nous ne sommes pas encore dans une phase opérationnelle, nous sommes plutôt en phase d’exploration. Les États-Unis et le Canada sont plus avancés, mais nous parlons de toute façon de quelque chose qui ne va pas arriver tout de suite, parce que les processus sont graduels, les avancées incrémentales, et parce que nous apprenons aussi des erreurs et des expérimentations. La mise en œuvre sera sûrement progressive. Les plateformes technologiques existent déjà, mais le problème porte sur le management du changement qu’il faudra réussir à intégrer de manière efficace.
Il est d’ailleurs possible que la mise en œuvre de solutions pionnières et expérimentales favorise l’éclosion de principes d’organisation vraiment novateurs, qui restent encore difficiles à saisir pour des yeux tournés vers le passé.
La possibilité de revêtir des dispositifs connectés, de doter d’interfaces les objets de la vie quotidienne (automobile, produits électroménagers) ou les biens de consommation courants (aliments, médicaments) renouvelle le sens de notions communes comme le marketing, l’orientation client, la proximité ou la traçabilité. Le consommateur pourra ainsi être mis à contribution et pleinement intégré au processus productif, en générant des informations qui seront transmises aux créateurs, concepteurs et développeurs de produits, bien plus qu’il ne l’est aujourd’hui sur les plateformes de partage ou les médias numériques.
C’est d’ailleurs de ces expérimentations que s’inspire le secteur manufacturier. Il est tout à fait imaginable de répliquer le profilage des utilisateurs de médias numériques dans l’univers industriel pour recueillir les pratiques et les usages du client. Le fait de pouvoir mesurer l’usage qui est fait des produits pourrait conduire à des déplacements de business model chez beaucoup d’entreprises qui passeraient ainsi de la vente à la location ou encore factureraient des heures d’utilisation comme dans le cas des moteurs de Rolls Royce. Des modèles d’affaires qui s’organiseront toujours plus autour de l’assistance, du service après-vente, de la collecte et de la transformation des données comme sources d’innovation. De tels changements auraient un impact profond sur la structure de l’emploi et sur les profils de compétences demandés.
Il n’y a pas de modèle de production sans structures de marché correspondantes. Toutes les innovations développées par le monde industriel depuis les années 1980 jusqu’à aujourd’hui ont essentiellement visé à combiner grande série et personnalisation. L’usine intelligente se propose d’aller encore plus loin dans le concept de personnalisation de masse requis par les marchés matures. La possibilité technique d’obtenir des hauts niveaux d’efficacité via des établissements flexibles et multifonctionnels, d’une part, et de dialoguer directement avec les clients, d’autre part, permettrait, au moins sur le papier, d’atteindre une intégration inédite entre entreprise et consommateurs, usine et société (vue dans cette optique surtout comme un vaste marché), production et circulation des biens.
C’est bien là l’un des thèmes cruciaux de l’industrie du futur : en transférant des facultés cognitives et de communication à des moyens de production flexibles, il devient possible de casser les rigidités des séquences qui réduisaient les niveaux de capacité et d’utilisation des usines, et d’ouvrir de nouvelles voies pour faire varier le processus en fonction des produits. De cette manière, les mêmes établissements et les mêmes machines pourraient, à partir d’instructions différentes, engendrer une multitude de produits, des gammes plus larges ou des combinaisons plus variées d’options sur des lots plus limités en volumes. Le nouvel établissement Pirelli de Settimo Torinese permet de produire 30 à 32 types de pneumatiques différents, là où l’ancien n’en fabriquait que 18 (Berta, 2014).
Mais les visions futuristes doivent cependant toujours tenir compte non seulement de la variété des secteurs et des marchés, mais encore des interdépendances qui forment la toile de fond de l’économie contemporaine, traversée par l’interpénétration de multiples formes de spécialisation territoriale. Cette diversité prend un relief particulier dès lors que l’on s’intéresse à l’industrie italienne : en effet, pour de larges pans du tissu industriel italien, le problème n’est pas tant d’apporter de la flexibilité à des productions à haute intensité capitalistique, que de produire davantage de volumes et d’acquérir une culture industrielle, sans sacrifier pour autant le caractère artisanal des productions, ni la capacité à occuper des niches aux volumes limités mais à haute valeur ajoutée. Soit un problème exactement inverse à celui que l’industrie du futur se propose de résoudre. Pour beaucoup de PME italiennes le virage intelligent consiste avant tout à réaliser des investissements et de la recherche orientés vers la montée en gamme, objectif qui ne peut plus être atteint par les seuls moyens traditionnels que représentaient auparavant la créativité de conception et un savoir-faire artisanal sophistiqué combinés à un usage flexible de la main-d’œuvre.
« Nous avons redessiné notre gamme de produits pour pouvoir la fabriquer sur une ligne de montage, puis nous avons introduit les robots de soudage qui, avec les méthodes lean, ont été clés dans notre succès de ces dernières années, sur un marché qui exige beaucoup de flexibilité en raison de sa saisonnalité et de l’imprévisibilité des conditions météorologiques. » (Giletta)
Enfin, aucun modèle ou paradigme ne se limite au processus de production, mais englobe également les mécanismes de reproduction sociale, la réglementation et les modèles de consommation. Si le taylorisme est devenu un paradigme, c’est qu’à un instant t, tout le monde – entreprises, pouvoirs publics, syndicats et institutions éducatives – « savait à quel jeu il jouait » (Butera, 2014). Ce n’était donc pas seulement un modèle d’organisation de la production et du travail, mais aussi un système institutionnel de régulation de l’économie, régissant les modèles de reproduction sociale et, en définitive, les rapports sociaux. Les hausses de salaires, l’institutionnalisation du conflit de classes au sein du dialogue social et les obstacles à la libre circulation monétaire furent des « tuteurs » non négligeables de l’organisation scientifique du travail.
L’industrie du futur, qui remet au premier plan l’un des lieux les plus emblématiques du siècle dernier, est un programme d’« industrialisation sociale » : une usine ancrée dans le territoire comme espace de relations, de coopérations et de consommation. L’usine se fond dans la cité au point d’abattre les murs entre elle et son environnement, exploitant les liens entre intérieur et extérieur, entre savoir collectif et valorisation privée. Et en tant que programme (encore loin d’être implémenté), l’industrie 4.0 est amenée à orienter selon ses exigences les institutions et les règles qui structurent le marché du travail, les flux financiers et logistiques, les relations industrielles, etc. En outre, elle présuppose un modèle de société orienté vers l’expansion de la consommation ou vers la substitution d’anciens modèles de consommation par de nouveaux. Qui va acheter les biens et services « intelligents » ou en louer l’usage ? Les technologies numériques favoriseront-elles le renouveau du capitalisme industriel, en créant des biens et services nouveaux que nous pouvons, à l’heure actuelle, à peine imaginer ? Ou ferontelles naître une société « post-capitaliste » (Mason, 2015), dont l’avènement ne serait que retardé (mais pas pour longtemps) par les limitations volontaires apportées au déploiement de leur potentiel collaboratif et de partage ?
Au-delà des frontières de l’entreprise
Les entretiens et les cas étudiés nous ont fourni une base pour formuler des hypothèses concernant les transformations au sein de l’usine qui, selon des rythmes variés, devient intelligente. Toutefois, l’espace de la production intelligente s’étend bien au-delà des murs de l’usine. C’est donc au sein de ce réseau traversé de flux de données et d’informations par et pour le marché que la question du travail devrait être examinée pour pouvoir en cerner toute la complexité.
Les changements identifiés dans la composition professionnelle des salariés, dans les articulations hiérarchiques entre détenteurs de la connaissance, dans les niveaux d’intégration hommes-machines traduisent en réalité de nouvelles formes dans la division du travail (associant fournisseurs de composants et de technologies, services avancés, entreprises partenaires et autres acteurs de référence) qui ne se limitent plus aux ateliers ou aux bureaux d’une seule entreprise. L’usine contemporaine incorpore de plus en en plus de services : conception, marketing, logistique, service client et distribution deviennent indissociables de la création de valeur liée à l’acte de production. Les usines sont multi-localisées et connectées. Les entreprises deviennent des réseaux, plus ou moins hiérarchisés, dépassant les frontières non seulement de leur activité mais de leur entité juridique.
Le secteur de la logistique en fournit un très bon exemple. Dans l’économie globalisée, les fonctions logistiques constituent souvent un laboratoire d’expérimentations technologiques et organisationnelles. Les intégrateurs logistiques qui, en Italie, sont presque tous des acteurs de dimension internationale, sont aujourd’hui les partenaires indispensables des secteurs d’activité qui ont adopté la production agile. Leur degré d’intégration avec les lignes de production des clients révèle à quel point ils ont dépassé depuis longtemps la position de simples fournisseurs de services à l’industrie. Rappelonsnous le rôle de Kuehne+Nagel, opérateur du pôle logistique de Ferrari à Maranello. Mais ces changements posent aussi des défis aux logisticiens qui doivent adapter leur recrutement, leur organisation et l’articulation hommes-technologies.
« Nous avons deux entrepôts, un pour la carrosserie, l’autre pour les composants du moteur. Ils sont organisés de façon à minimiser le parcours pour alimenter la destination finale des pièces. Toutes les 15 minutes, une motrice part pour aller chez Ferrari : nous faisons 4 navettes par heure, 10 heures par jour. » (Kuehne+Nagel Maranello)
« Le dialogue avec les fournisseurs change. Plus rapide et agile grâce à l’utilisation de portails fournisseurs. On peut comparer les propositions et surveiller l’approvisionnement. La production intégrée influe sur les stocks et la vitesse d’approvisionnement. Nous gérons l’entrepôt de façon intégrée avec un système de gestion très sophistiqué. » (Avio Aero)
Les grandes entreprises logistiques internationales ont un temps d’avance sur les industriels. C’est souvent l’entreprise logistique qui implante au sein de l’entreprise manufacturière des solutions opérationnelles plus efficientes ; c’est pourquoi, en Italie, s’intéresser à la logistique constitue un bon point d’observation pour évaluer l’adoption des innovations. Le système logistique et de transports italien a longtemps reposé (et repose en grande partie encore) bien plus sur la contraction des coûts de personnel que sur l’innovation : nous en voulons pour preuve la large présence dans ce secteur de coopératives de chauffeurs routiers (Bologna, 2013), ainsi que la grande utilisation qui est faite de camionneurs indépendants qui ont pour principal avantage concurrentiel de conduire bien au-delà des règles et des limites imposées au secteur.
Ce qu’on a appelé le « modèle logistique italien » n’a longtemps été rien d’autre que la réponse à la demande parcellisée de transports émanant des districts industriels italiens, qui exigeaient des petites ou moyennes expéditions à un rythme frénétique (Appetecchia, 2014) : le succès du premier Made in Italy s’est donc fondé sur la commercialisation de produits de bonne qualité à prix compétitifs grâce à la contribution notable de services logistiques à coûts comprimés dont le prix était en outre transféré au client (prix franco départ usine).
Ces dernières années en revanche, un certain nombre d’entreprises récupèrent des points de marge à travers le recours à l’outsourcing de leur logistique, un processus qui favorise plutôt les grands opérateurs du secteur qui seuls disposent des ressources permettant de larges économies d’échelle. Sont apparus alors de grands entrepôts à haute intensité technologique et à l’avant-garde dans l’application des dispositifs smart, dont les conséquences les plus visibles sont, d’une part, un rééquilibrage entre capital et travail (comparé aux entrepôts semi manuels qui couvrent encore une bonne partie du territoire) et, d’autre part, des niveaux élevés de néotaylorisme numérique pour le personnel. Peu de secteurs autant que la logistique intégrée ont ainsi parcouru par anticipation le chemin de l’innovation numérique.
« La logistique moderne est née quand nous avons pu « lire » les informations contenues dans un code-barres de plusieurs manières différentes, avec un scanner sans fil ou par reconnaissance vocale (i. e. voice picking). Aujourd’hui, nous évoluons vers le voice scan, qui combine la reconnaissance vocale et la lecture par scanner et qui réduit considérablement les erreurs : on change très souvent les codes sur les articles pour éviter que les gens ne prennent des habitudes et s’installent dans la routine. » (Kuehne+ Nagel Iveco)
Dans l’usine interconnectée, l’innovation peut également provenir des marges de l’entreprise, de la capacité de celle-ci à « cueillir » des signaux faibles, des informations et des connaissances produites en dehors d’elle. Pour cela, elle doit déployer des antennes. Dans le modèle traditionnel du Made in Italy, ces antennes coïncidaient souvent avec le « cool hunting », une sorte de marketing amont reposant essentiellement sur l’intuition aigüe de l’entrepreneur ajoutée à quelques études de marché. La numérisation en cours modifie aussi ces modalités traditionnelles d’exploration des marchés, des tendances et des pratiques sociales.
On notera également, dans l’écosystème de l’innovation numérique, la flexibilité des start-up, vaisseaux légers qui naviguent en mode agile dans les flux du marché et sont capables de faire émerger des compétences distinctives d’avant-garde. À ce champ s’apparentent également le mouvement des makers, mais aussi le recours aux innovations venues « d’en bas » que les grandes entreprises favorisent par le développement d’instruments participatifs comme les hackathons. Ces innovateurs par le bas font office d’explorateurs pour défricher des terres vierges ou relancer des productions traditionnelles revisitées par la technologie (Micelli, 2014). En toile de fond, on trouve toujours l’idée que ces nouvelles manières de travailler pourront pénétrer le fonctionnement des grandes entreprises pour raccourcir les délais de décision et de réalisation, rendre plus flexible les processus, en articulant toujours mieux la production à l’usage du consommateur.
Selon les zélateurs de l’industrie 4.0, la frontière technologique se déplace pour permettre une « externalisation » de la production bien au-delà des frontières de l’entreprise, dans un espace social complet. Le concept de prosumer a été souvent analysé comme un déplacement de la fonction de production vers la fonction de consommation, mais peu d’attention a été portée à l’interprétation inverse qui se révèle bien plus décisive : la transformation de la consommation en « travail ». Le web 2.0 montre de façon éclairante comment, à travers les nouvelles technologies, on extrait de la valeur de ce qui auparavant relevait de l’espace privé, du jeu, du loisir ou de la simple relation humaine. Les machines numériques transforment les formes de vie en plateformes permanentes d’innovations. Dans cette perspective, et même s’il apparaît très prématuré d’en imaginer toutes les conséquences, le travail industriel est destiné à changer en profondeur et peut-être verra-t-on apparaître des « cols blancs striés de bleu » aux côtés des « cols bleus striés de blanc ».
Nouvelle industrie et artisanat
La notion « d’artisanat digitalisé » revient souvent en Italie dans le débat sur le devenir intelligent de la production industrielle. Née au sein de la grande industrie allemande ou comme aux USA dans le contexte d’un primat donné au numérique, l’industrie du futur se cherche une déclinaison « à la mode italienne », cohérente avec le profil national de son tissu productif. Par « artisanat », on entend ici non l’entreprise strictement artisanale, mais un ensemble d’avantages compétitifs caractéristiques des moyennes entreprises, capables de diffuser l’esprit et les valeurs du Made in Italy : qualité d’exécution, spécialisation de niche, orientation vers le client.
La production intelligente pourrait avantager les productions italiennes, dans la mesure où celles-ci sont depuis toujours orientées vers la personnalisation. Nous aurions ainsi une sorte de retour au caractère artisanal de la production, qui ne serait plus une niche de résistance par défaut, mais bien une déclinaison de l’innovation et du développement industriel 4.0 ; les nouveaux « artisans » deviendraient ainsi les principaux bénéficiaires de la numérisation industrielle. D’ailleurs, on constate que ce trait « néo-artisanal » est explicitement revendiqué comme un marqueur d’italianité par des dirigeants industriels italiens, leaders mondiaux de leur marché.
Cette « artisanalité » qui contamine la production industrielle se manifeste pleinement à travers la technologie de la fabrication additive, qui est encore aujourd’hui principalement utilisée pour produire des petites séries à petite échelle (si l’on excepte le cas d’Avio Aero à Cameri) que ce soit dans un cadre strictement artisanal ou dans la limite des activités de prototypage au sein d’entreprises de plus grandes dimensions. Comme l’a indiqué Stefano Micelli, l’un des chercheurs qui s’est le plus intéressé à la fabrication additive, les promesses contenues dans le développement et les applications de cette technologie restent encore à vérifier : « Les progrès technologiques, qui ont coïncidé avec la fin de nombreux brevets et la diffusion de protocoles open source, ont permis de produire des machines plus petites et plus économiques, pouvant même être achetées par un particulier. Les imprimantes 3D sont aujourd’hui accessibles aux consommateurs finaux. De façon analogue à ce qui s’est produit lors du passage des gros ordinateurs-systèmes aux PC, ce changement d’échelle peut ouvrir des formes d’usage de cette technologie et des marchés qui restent à découvrir. » Mais le même auteur avance aussi que l’introduction de cette technologie remet effectivement en question les échelles qui gouvernaient auparavant la production industrielle : « Le monde analogique exigeait des économies d’échelle significatives pour compenser les rigidités technologiques et de gestion des processus de production. Aujourd’hui, la flexibilité de ces nouvelles technologies et leur coût relativement abordable permettent de contourner cet obstacle et d’imaginer imprimer de très petits volumes, sans compromettre la saturation et l’efficience de l’outil de production. »
La spécialisation de niche, qui est le positionnement stratégique souvent recherché par les PME italiennes, est donc parfaitement compatible avec les technologies de l’industrie 4.0 qui visent la personnalisation de la production. On peut citer en exemple des applications déjà opérationnelles dans la haute couture ou les chaussures sur-mesure : un scanner 3D prend les mesures du client qui peuvent ensuite donner lieu à des productions correspondant au style et à la morphologie de chaque individu, comme des chaussures haut de gamme dont la forme et la semelle correspondent parfaitement aux caractéristiques du pied. En fait, tous les secteurs du Made in Italy sont potentiellement concernés : de la couleur personnalisée des carrelages à la conception sur-mesure des canapés et des lits, des revêtements muraux en marbre ou en bois à la personnalisation des lunettes et autres accessoires.
Cependant, il ressort de nos entretiens que la fabrication additive est regardée par les industriels de façon plus précautionneuse qu’elle n’est habituellement présentée dans la littérature et les médias, qui tendent à en faire un symbole de la conversion numérique de l’industrie. Parmi les technologies propres à l’industrie 4.0, les imprimantes 3D sont souvent présentées comme un fait technologique engageant une promesse importante de changement. Certains considèrent même la fabrication additive comme la technologie pouvant assurer la bascule vers un « prosumérisme » enfin soustrait aux lois du marché, permettant de se réapproprier des techniques, des connaissances et une maîtrise de sa propre vie : c’est l’utopie des makers.
« Les imprimantes 3D ne vont probablement pas révolutionner le destin de l’industrie, comme le fit l’électricité. Cette technologie pourra être d’un grand apport, si elle est introduite dans l’industrie de manière appropriée et intelligente, cette dernière pouvant soutenir les programmes pluriannuels qui seront nécessaires à son développement. Comme l’a fait Airbus qui va l’utiliser pour produire des composants toujours plus sophistiqués. » (CSM Centro Sviluppo Materiali)
« On imagine que c’est la panacée, mais ce n’est pas le cas, au sens où nous ne devons pas l’utiliser pour dupliquer des choses déjà existantes. Si le coût est moindre, l’utiliser a un sens. L’effort consiste à redessiner des composants pour les réaliser en additif, mais il ne faut le faire que si cela a un sens du point de vue fonctionnel ou économique. » (Avio Aero Cameri)
Les entreprises que nous avons rencontrées au cours de notre recherche présentent encore bien des caractéristiques de production artisanale, souvent nichée dans les interstices de cycles complexes et flexibles, par exemple en maintenance, en prototypage, ou encore là où l’on produit des pièces uniques ou gigantesques (les navires de croisière). Artisanales aussi, les procédures de contrôle des pneumatiques Pirelli, pourtant produits dans un établissement parmi les plus modernes d’Italie (Berta, 2014) ou celles du moulage chez Fiat Chrysler où les mesures optiques sont complétées par le contrôle visuel et tactile des opérateurs. En somme, il existe bien une complémentarité entre les capteurs et la compétence de l’opérateur acquise par l’expérience.
Certains ne sont pas d’accord avec cette présentation : « La smart factory produit des données si riches à étudier que l’entrepreneur devient bien plus ingénieur qu’il ne demeure artisan ». Les nouvelles technologies et la robotique intelligente pousseraient à industrialiser l’artisanat bien davantage qu’à « artisanaliser » l’industrie. Du reste, la coexistence de plusieurs modèles au sein d’une même orientation générale ne seraitelle pas justement le signe de cette transformation intelligente de l’industrie ?
En définitive, la voie italienne vers l’industrie du futur consiste à adapter au contexte local les innovations et les organisations créées ailleurs. Les nouvelles technologies peuvent permettre d’unir la productivité aux qualités propres à l’industrie artisanale, à condition de tenir compte des caractéristiques du système productif italien : leadership de niche, petite taille des structures et capitalisme familial qui limite les ressources financières disponibles.
Les limites de la petite taille pourraient être en partie surmontées par le recours à des dispositifs comme les réseaux d’entreprises ou Contrats de Réseau, ou encore à travers le « prêt de filière » qui consiste à réduire pour un petit fournisseur le risque bancaire de l’emprunt, en lui appliquant le même taux d’intérêt qu’à l’entreprise « tête de district ou de filière ». Il y a des cas connus comme les taux appliqués à Gucci ou Diesel, et certaines banques ont aussi accordé des taux préférentiels à des entreprises associées au sein de clusters locaux. Ce sont là quelques exemples d’instruments disponibles pour favoriser le rapprochement d’entreprises au sein des districts et leur permettre ainsi d’accéder aux technologies de l’industrie 4.0.
La logique lancée par les Allemands est cohérente avec le profil de leurs entreprises ; elle n’est pas forcément applicable telle quelle au contexte italien. Le pronostic est plutôt que l’Italie en développera une formule adaptée, fondée sur la flexibilité des solutions d’organisation. Dans notre scénario national, la difficulté provient du fait que des technologies nées pour être appliquées dans de grandes unités ne sont pas facilement adaptables à notre petite réalité. Comme l’a déclaré Tullio Tolio au cours d’une interview, les efforts actuels consentis dans le champ de l’industrie du futur doivent être ciblés sur les petites entreprises « qui n’investissent pas dans les technologies non par ignorance, mais par manque d’une offre qui leur corresponde ». Il faut cependant noter que la simple adaptation des standards technologiques à notre système économique exigera déjà un remarquable effort, au niveau global comme pour chaque entreprise.
En conclusion
Comme cela a été indiqué dès les premières pages de ce livre, la recherche qui a justifié ce voyage n’avait pas pour objectif de fournir une description analytique ou prédictive du travail dans l’usine du futur. Il s’agissait plus modestement d’attirer l’attention sur quelques cas d’application de la transformation intelligente des processus de production, et plus particulièrement sur d’éventuelles contradictions entre les discours tenus sur l’industrie 4.0 et sa réalité du moment, et sur des observations contreintuitives. La consigne était de ne céder ni à l’utopie d’une usine qui aurait totalement échappé aux contradictions à l’œuvre pendant tout le XXe siècle, ni à la crainte de voir les technologies intelligentes « manger » le travail des hommes.
« La robotique, c’est du métal et des logiciels » nous a dit un dirigeant de Comau à Turin. Il utilisait ainsi sans le savoir la métaphore qui a guidé notre travail : mettre en évidence non seulement les points d’inflexion mais également les lignes de continuité par rapport au passé. Car les technologies font toujours partie d’un système social de production ; elles en constituent l’un des aspects fondamentaux, mais elles ne le déterminent jamais complètement, de façon directe et linéaire.
Le développement industriel lui-même n’est pas linéaire. La séquence historique qui, partant de la manufacture, conduit à la grande entreprise et donc au taylorisme, bascule vers le toyotisme et l’automatisation flexible pour aborder enfin les rivages de la production intelligente, est une pure construction intellectuelle. Une construction certes utile pour mesurer les discontinuités, mais soumise à l’idée (fausse) que l’industrie évoluerait selon une direction unique. Dans la réalité, plusieurs modèles de production ont cohabité au sein des différents paradigmes et le passage de l’un à l’autre s’est toujours révélé un nœud de contradictions.
Enfin, il importe de préciser que toute réflexion relative au travail dans l’industrie doit être replacée dans le contexte de chaque territoire et de la place qu’il occupe dans la division internationale du travail. Cette place définit en grande partie les modèles d’affaires et les formes d’industrie que l’on va trouver dans chaque pays. En Italie, de nombreuses terres d’industrie n’ont jamais connu la production de masse ; en conséquence, les débats sur l’industrie du futur ne s’y inscrivent pas dans la séquence historique classique décrite ci-dessus. La problématique de nombreuses entreprises du Made in Italy n’est pas de flexibiliser l’organisation du travail, mais bien d’industrialiser des processus de production de nature artisanale ou passablement déstructurés.
Le travail industriel est aujourd’hui visiblement moins segmenté que par le passé. La traditionnelle division entre ouvriers, employés, techniciens, cadres et management ne suffit plus à rendre compte de certains organigrammes ou est carrément inopérante dans d’autres cas. Ce qui reste du travail « vivant » dans les processus de production pourrait exiger des compétences plus complexes qu’autrefois, en particulier des capacités de diagnostic, de résolution de problèmes et d’adaptation à la variabilité du cycle de production. Mais une telle évolution dépend de plusieurs facteurs : maturité du produit, environnement concurrentiel, positionnement dans la chaîne de valeur, etc.
Parmi les objectifs explicites de l’usine intelligente, nous avons relevé celui de créer une chaîne de langage, dans laquelle les informations seraient traduites non plus seulement par les travailleurs mais par les machines. Les robots qui assemblent devraient à l’avenir être également capables d’élaborer des instructions, tandis que serait attribuée aux hommes la mission de contrôler le fonctionnement du système et d’intervenir en cas de problème. Dans une étape ultérieure, le produit lui-même collectera des données et des informations qui seront transmises à la production pour l’améliorer – cette étape étant aujourd’hui plus une vision qu’une réalité. Nous avons parlé ici simultanément d’une orientation vers la production intelligente et de post-fordisme augmenté, en raison du fait que, même dans les entreprises de notre échantillon les plus engagées sur la voie de la transformation, les dirigeants interrogés nous ont parlé davantage avec des concepts issus du passé qu’avec les mots du futur. L’accent est donc mis sur l’approfondissement et l’accélération de certaines tendances, plutôt que sur un changement radical de paradigme.
En Italie, la difficulté de procéder à des investissements technologiques à grande échelle est évidente. Pour l’expliquer, quelques interviewés ont souligné l’absence d’une politique industrielle apte à fixer une direction et à hiérarchiser les priorités24. Ceux qui soutiennent que l’Italie doit faire fleurir les innovations devront tenir compte des indicateurs qui semblent pointer vers une tout autre direction : l’investissement orienté vers la R & D est faible et l’habitude consiste toujours à faire reposer l’avantage concurrentiel sur un mix de créativité et de contrôle des coûts de la main-d’œuvre (parce que le coût de la main-d’œuvre est peut-être devenu un sujet secondaire dans les usines intelligentes, mais il reste une priorité dans l’agenda de la majorité des industriels). Tout ceci met l’industrie italienne au mieux au milieu du gué, avec le risque de ne parvenir à être compétitive sur aucune des deux rives, ni sur l’innovation, ni sur le coût du travail.
Plus généralement, la place de l’Italie dans la division internationale du travail empêche toute grille de lecture monolithique de son système productif. Tout se passe comme si l’Italie était engagée dans un processus de redimensionnement de sa capacité productive, qui puisse néanmoins préserver ou sélectionner des champions nationaux capables de conquérir les marchés internationaux pour compenser le rétrécissement du marché intérieur. C’est une forme de globalisation « en mode mineur », avec peu de vrais joueurs mondiaux et un nombre croissant d’entreprises orientées vers l’export, qui ont du mal à s’imposer sur les marchés les plus dynamiques mais maintiennent leurs positions sur les marchés matures et visent à se développer dans des marchés de moyenne portée (Europe de l’Est, Afrique du Nord, Moyen-Orient). D’ailleurs, l’internationalisation, bien plus que la recherche et l’innovation, a longtemps représenté la stratégie gagnante aux yeux de la minorité d’entreprises qui a su rebondir après la crise. On peut supposer que l’insertion des entreprises les plus en avance technologiquement dans les chaînes de valeur mondiales, ainsi que leur filialisation au sein de groupes transnationaux, favoriseront les exceptions high tech au sein d’un panorama national où l’avantage concurrentiel se caractérise toujours essentiellement par le style, l’image, la qualité artisanale et les coûts contenus de la main-d’œuvre. Le dynamisme des exportations, comme l’ont montré les dernières années, ne suffira pas à assurer la croissance, l’inclusion et la redistribution sociale des bénéfices.
Quant aux développements de type 4.0, ils apparaissent pour le moins embryonnaires et incertains. Les robots ne communiquent qu’à des niveaux assez faibles et l’intelligence des machines est encore passive. De ce point de vue, font remarquer certains observateurs, le robot, c’est encore l’homme. Mais qu’implique tout cela pour les travailleurs ?
Tout au long de ce livre, nous avons insisté sur le fait que l’usine intelligente ne correspondait pas à un aplatissement des lignes hiérarchiques. C’est dans les usines les plus intelligentes qu’on voit se renforcer une couche de collaborateurs qui donnent de l’intelligence aux machines ou qui maîtrisent les routines organisationnelles et les connaissances sédimentées dans la mémoire de l’entreprise. Dans les organisations les plus avancées, on trouve, d’une part, une main-d’œuvre plus instruite et, de l’autre, une relative sous-utilisation des compétences issues de l’expérience ou une demande pour des compétences simplifiées. Les entretiens laissent entrevoir une recomposition des missions, que ce soit au niveau des opérateurs ou des activités de conception. Il faut cependant se défier de la tentation de définir de nouveaux profils de travailleurs : les ouvriers « augmentés » ou « diminués » de même que les ingénieurs de nouvelle conception sont des archétypes et non des professions réelles. L’évolution vers des nouveaux métiers de gestion et transmission de l’information, de services ou d’analyse des données demeure opaque. Mais c’est peut-être du virage numérique des activités de bureau que pourraient provenir les plus grands changements, même dans le secteur industriel.
Grande absente de la littérature relative à l’usine du futur : la réflexion sur le temps de travail et les salaires. Pour répondre à ces interrogations, il faudra approfondir les observations sur la réalité de cette nouvelle phase industrielle, en acceptant sa complexité. Il faudra aussi continuer à se demander si l’aliénation n’est plus qu’un souvenir du passé ou si elle est susceptible de revêtir de nouveaux atours, si dans les nouvelles usines l’emploi sera gratifiant sur les plans du sens et du salaire, s’il y aura adéquation entre le travail proposé et les compétences et attentes de celles et ceux qui l’effectuent. Il faudra pour cela écouter de nouvelles voix : celles des travailleurs 4.0.
- 24. Le présent ouvrage a été écrit avant la présentation du Plan national Entreprise 4.0 (Piano Nazionale Impresa 4.0), dit Plan Calenda (du nom du ministre de l’Économie), en septembre 2016.
Bibliographie
AA.VV. (2014), Sociologia del lavoro , n. 133.
Accenture Strategy (2014), « La trasformazione digitale », in Harvard Business Review , supplemento al n. 12.
Acemoglu D., Autor D. (2010), The Polarization of Job Opportunities in the U.S. Labor Market, Brookings Institution.
Alma Laurea (2011, 2012, 2013, 2014), Condizione occupazionale dei laureati , Rapporto annuale.
Anderson C. (2013), Makers. Il ritorno dei produttori , Rizzoli Etas, Milano.
Anie (2014), Osservatorio dell’industria italiana dell’automazione , Milano.
Appetecchia A. (2014), La logistica in Italia , Isfort.
Armano E., Murgia A. (sous la dir. de) (2014), Generazione precaria. Nuovi lavori e processi di soggettivazione , Emil Bologna.
Armano E., Murgia A. (2012), Mappe della Precarietà vol. I. Spazi, rappresentazioni, esperienze e critica delle politiche del lavoro che cambia , Odoya, Bologna.
Autor D., Dorn D. (2013), « The growth of low skill service jobs and the polarization of the US labor market », American Economic Review , n. 103.
Autorità Agcm (2015), Indagine conoscitiva concernente i servizi di comunicazione Machine to Machine (M2M) , Rapporto finale, Milano.
BCG Boston Consulting Group (2015), Industry 4.0. The future of productivity and growth in manufacturing industry , Milano.
Beaudry P., Green D.A, Sand B. (2013), The great reversal in the demand for skill and cognitive tasks , National Bureau Economic Research.
Bell D. (1973), The coming of post-industrial society. A Venture of Social Forecasting , Basic Books, New York.
Benedini A. (2015), Prospettive del manifatturiero italiano e impatto delle tecnologie digitali , XV Giornata « Ripensare la politica industriale oggi », GEI-Gruppo Economisti d’Impresa, 5 marzo, Milano.
Berger S. (2005), How We Compete : What Companies Around the World Are Doing to Make it in Today’s Global Economy , Doubleday, New York.
Berta G. (2014), Produzione intelligente , Einaudi, Torino.
Bologna S. (2013), Banche e crisi. dal petrolio al container , Derive Approdi, Roma.
Bower J.L., Christensen C.M. (1995), « Disruptive Technologies : Catching the Wave », Harvard Business Review , vol. 73, n. 1.
Braverman H. (1978), Lavoro e capitale monopolistico. La degradazione del lavoro nel XX secolo , Einaudi, Torino.
Brynjolfsson E., McAfee A. (2014), Second Machine Age , WW Norton & Co., New York.
Butera F. (1972), I frantumi ricomposti : struttura e ideologia nel declino del taylorismo in America , Marsilio, Venezia.
Butera F. (2014), « Futuro professionale : dal taylor-fordismo ai nuovi modi di produzione. I frantumi ricomposti, 1971-2015 », Studi organizzativi , Franco Angeli, n. 2.
Cancellato F. (2015a), « Basta Italia-Germania : è l’ora del Made in Europe », 17/3/2015, Linkiesta , http://www.linkiesta.it/it/article/2015/03/17/basta-italia-germania-e-lora-del- made-in-europe/25075/
Cancellato F. (2015b), « Con industria 4.0, la Germania può aiutare l’Italia a ripartire », 11/9/2015, Linkiesta , http://www.linkiesta.it/it/article/2015/09/11/con-industria-40-la-germania- puo-aiutare-litalia-aripartire/27353/
Castells M. (2003), Il potere delle identità , Università Bocconi, Milano.
Centro Studi Federmeccanica (2013), Indagine sul lavoro nell’industria metalmeccanica .
Cipolletta I. De Nardis S. (2012), « L’Italia negli anni duemila : poca crescita, molta ristrutturazione », Economia Italiana , n. 1.
Cohen D. (2001), I nostri tempi moderni. Dal capitale finanziario al capital umano , Einaudi, Torino.
Commissione Europea (2014), Comunicazione della Commissione al Parlamento Europeo, al Consiglio, al Comitato Economico e Sociale Europeo e al Comitato delle Regioni : Per una rinascita industriale europea , Bruxelles, 22/01. http://eur-lex.europa.eu/legal-content/IT/TXT/?uri=CELEX%3A52014DC0014
Commissione Europea (2012), Un’industria europea più forte per la crescita e la ripresa economica , http://eurlex.europa.eu/LexUriServ/LexUriServ.do?uri=COM:2012:0582:FIN:it:PDF
Confindustria Servizi Innovativi e Tecnologici (2015), « Industria 4.0 », Il Sole 24 Ore , Milano.
Confindustria Veneto (2015), Il manifesto del nuovo manifatturiero , Mestre.
Coriat B. (1991), Penser à l’envers, Christian Bourgois, Paris.
Crapelli R. (2015), Industry 4.0 : high impact transformation , XV Giornata « Ripensare la politica industriale oggi », GEI-Gruppo Economisti d’Impresa, 5 marzo, Milano.
CSC Confindustria e Prometeia (2014), Esportare la dolce vita , SIPI, Roma.
Deutsche Bank Research (2014), Industry 4.0 : Upgrading of Germany’s industrial capabilities on the horizon , Frankfurt am Main.
Dijk J. Van (2005), The Deepening Divide : Inequality in the Information Society , California, Sage.
Dore R. (1990), Bisogna prendere il Giappone sul serio , Il Mulino, Bologna.
Dyer J. e Bryce D., « Tesla’s High End Disruption Gamble », Forbes , 20/8/2015 www.forbes.com/sites/innovatorsdna/2015/08/20/teslas-high-end-disruption-gamble/#6c75e82c4e2f
Dyer J., Gregersen H., Furr N. (2015), « Decoding Tesla’s Secret Formula », Forbes , 19/08.
European Commission (2013a), Factories of the future. Multi-annual roadmap for the con tractual PPP under Horizon 2020 , Luxembourg.
European Commission (2013b), Digcomp : A Framework for Developing and Understanding Digital Competence in Europe , Luxembourg.
European Commission (2010), Factories Of The Future PPP. Strategic Multi-Annual Roadmap , Luxembourg.
FIM-CISL (2014), Le persone e la fabbrica. Una ricerca Fim-Cisl sulla condizione dei lavoratori negli stabilimenti Fiat , www.fim-cisl.it
Florida R. (2003), L’ascesa della nuova classe creativa. Stile di vita, valori e professioni , Mondadori, Milano.
Foucault M. (2005), Nascita della biopolitica . Corso al Collège de France (1978-1979), Feltrinelli, Milano.
Frey C.B., Osborne M.A. (2013), « The future of employment : how susceptible are jobs to computerization ? », The Leadership Quarterly , vol. 21.
Fuchs C. (2014), Social media : a critical introduction , Sage Publications, New York.
Frullone M. (2015), Comunicazione Machine-to-Machine : Le necessarie sinergie istituzionali , seminario LUISS-Fondazione Ugo Bordoni, 25 marzo, Roma.
Gauntlett D. (2013), La società dei maker , Marsilio, Venezia.
Gimélec (2014), Industrie 4.0 : L’usine connectée, Paris.
German Ministry of Research and Education e Acathec (2015), Recommendations for implementing the strategic initiative Industrie 4.0. Final report of the Industrie 4.0 Working Group , Berlin.
Germany’s Federal Government (2014), The new High-Tech Strategy. Innovations for Germany , BMBF, Berlin.
Germany’s Federal Ministry of Education and Research (2010), Ideas. Innovation. Prosperity. High-Tech Strategy 2020 for Germany , BMBF, Berlin.
Gouvernement Française, Industrie du futur. Réussir la Nouvelle France Industrielle, 2015
Head S. (2014), Mindless : Why Smarter Machines Are Making Dumber Humans, Basic Books, New York.
Hirschhorn L. (1988), The Workplace Within : the psychodynamics of organizational life , MIT Press.
Huws U. (2010), « Expression and expropriation : the dialectics of autonomy and control in creative labour », ephemera , vol. 10 (3/4).
Industry-Science Research Alliance e Acatech – National Academy of Science and Engineering (edited by) (2013), Securing the future of German manufacturing industry. Recommendations for implementing the strategic initiative Industrie 4.0.
James O., « Le CV est kitsch », L’Usine digitale , 27 août 2015.
Jenkins H. (2007), Cultura convergente , Apogeo, Milano.
Lanza A. (2015), L’industria italiana di fronte alle nuove frontiere tecnologiche : sfide e opportunità , XV Giornata « Ripensare la politica industriale oggi », GEI-Gruppo Economisti d’Impresa, 5 marzo, Milano.
Latour B. (2005), Reassembling the Social. An Introduction to Actor-Network- Theory , Oxford University Press, New York.
Lopez Research LLC (2014), Building smarter manufacturing with the Internet of Thing , San Francisco, USA.
Magatti M. (2013), La grande contrazione. I fallimenti della libertà e le vie del suo riscatto , Feltrinelli, Milano.
Manovich L. (2002), Il Linguaggio dei nuovi media , Olivares, Milano.
Mason P. (2015), Postcapitalism , Allen Lane.
McKinsey Quarterly (2010), The Internet of Things , n. 2, New York.
McKinsey (2013), Disruptive technologies : Advances that will transform life, business, and the global economy , New York.
Micelli S. (2014), Futuro artigiano , Marsilio, Venezia.
Micelli S. (2014), « La rivoluzione del digital manufacturing e la sfida per l’Italia », Imprese & Città , n. 3.
Moretti E. (2013), La nuova geografia del lavoro , Mondadori, Milano.
Morin E. (1999), La testa ben fatta. Riforma dell’insegnamento e riforma del pensiero , Raffaello Cortina, Milano.
Morini C. (2010), Per amore o per forza, femminilizzazione del lavoro e biopolitiche del corpo , Ombre corte, Verona.
Moscati R., Vaira M. (a cura di) (2008), L’università di fronte al cambiamento , Il Mulino, Bologna.
Norman D. (2013), The Design of Everyday Things , Basic Books.
Oxford Economics (2012), The Digital Transformation of People Management.
Paolazzi L. (sous la dir. de) (2014), People first : il capitale umano, la forza del paese , Centro studi Confindustria, Roma.
Pellegrino G. (2004), Il cantiere e la bussola : le reti intranet fra innovazione e routine , Rubbettino, Catanzaro.
Petrick, Irene J., Timothy W. Simpson (2013), « 3D Printing Disrupts Manufacturing : How Economies of One Create New Rules of Competition », Research Technology Management , 56, pp. 12-16.
Piaac-OCSE (2013), Rapporto nazionale sulle competenze degli adulti , Isfol.
Politecnico di Milano (2007), RFID : Alla ricerca del valore , Rapporto 2007 dell’Osservatorio RFID, Milano.
PwC PricewaterhouseCooper (2015), Digital manufacturing : cogliere le opportunità del rinascimento digitale , Milano.
Roland Berger (2015), The digital transformation of the industry , München.
Rullani E. (2004), Economia della conoscenza. Creatività e valore nel capitalism delle reti, Carocci, Roma.
Sacchetto D., Gambino F. (2015), prefazione edizione italiana di Pun Ngai, Han Yuchen, Guo Yuhua, Lu Huilin, Nella fabbrica globale , Ombre Corte, Verona.
Seghezzi F. (2015), « Come cambia il lavoro nell’Industry 4.0 », working paper, Adapt , n. 172, 25 marzo, Modena.
Technology Strategy Board (2012), High Value Manufacturing Strategy , Swindon https://www.gov.uk/government/uploads/system/uploads/attachment_data/file/362294/High_Value_Manufacturing_Strategy_2012-15.pdf
Toffler A. (1980), The Third Wave , William Morrow & Company.
Veronesi L. (2014), Il Futuro dell’Industria Manifatturiera , Infor.
WEF-World Economic Forum (2015), Industrial Internet of Things : Unleashing the Potential of Connected Products and Services , Geneva.
Wilensky H.L. (1964), « The Professionalization of Everyone ? », American Journal of Sociology , vol. 70, n. 2.
Womack J.P., Jones D.T., Roos D. (1993), La macchina che ha cambiato il mondo , Rizzoli, Milano.
Zanardini M. (2014), « La rivoluzione digitale nella manifattura », Impresa & Città , n. 4.
Annalisa Magone est journaliste, spécialisée dans les entreprises, la recherche et l’innovation. Depuis 2010, elle est présidente et directrice générale de Torino Nord Ovest.
Tatiana Mazali est sociologue des médias, spécialiste des cultures digitales. Depuis 2005, elle enseigne l’ingénierie du cinéma et des moyens de communication à l’École polytechnique de Turin.
Sous la direction d’Annalisa Magone et Tatiana Mazali
Avec la collaboration de Salvatore Cominu, Antonio Sansone, Giampaolo Vitali
Traduction : Marie-Laure Cahier
L’édition originale de cet ouvrage a été publiée en langue italienne par Edizioni Guerini e Associati Srl sous le titre Industria 4.0. Uomini e macchine nella fabbrica digitale. © 2016 Edizioni Angelo Guerini e Associati Srl
ISBN : 978-2-35671-538-8
ISSN : 2495-1706
© La Fabrique de l’industrie, Presses des Mines, 2018, pour l’édition en langue française. Tous droits réservés.